
MARKET GUIDE: Crushers & Screeners
Eoghan Daly reports from the Hillhead show on the latest developments in crushing, screening and associated processing equipment
Over the four years since the last Hillhead show, material processing machinery manufacturers have launched a raft of new and updated products. This sector of the industry was therefore extremely keen to get back to Buxton, taking full advantage of the unique opportunity to showcase their products at work in a live quarry environment.
A growing trend is the provision of diesel-electric drivelines in tracked crushers and screeners. In itself, this will be more fuel efficient than a traditional powerpack, but also opens up the possibility of powering the machines from an external electrical supply. This is likely to become more common, part of a raft of developments to reduce diesel consumption and therefore carbon emissions across the industry.
Northern Ireland-based manufacturers have dominated this market for years, developing a strong nationwide after-sales support network for their products. A number of new entrants to the UK market were exhibiting and demonstrating at Hillhead, not only from continental Europe, but also from the USA. These products may be relatively unknown, but have a well-proven reputation and provide the industry with an even greater choice in how to meet their material processing needs. These new offerings also provide dealers with the opportunity to expand their portfolio of products, the establishment of a service network being critical to the success of these new players in the UK market.
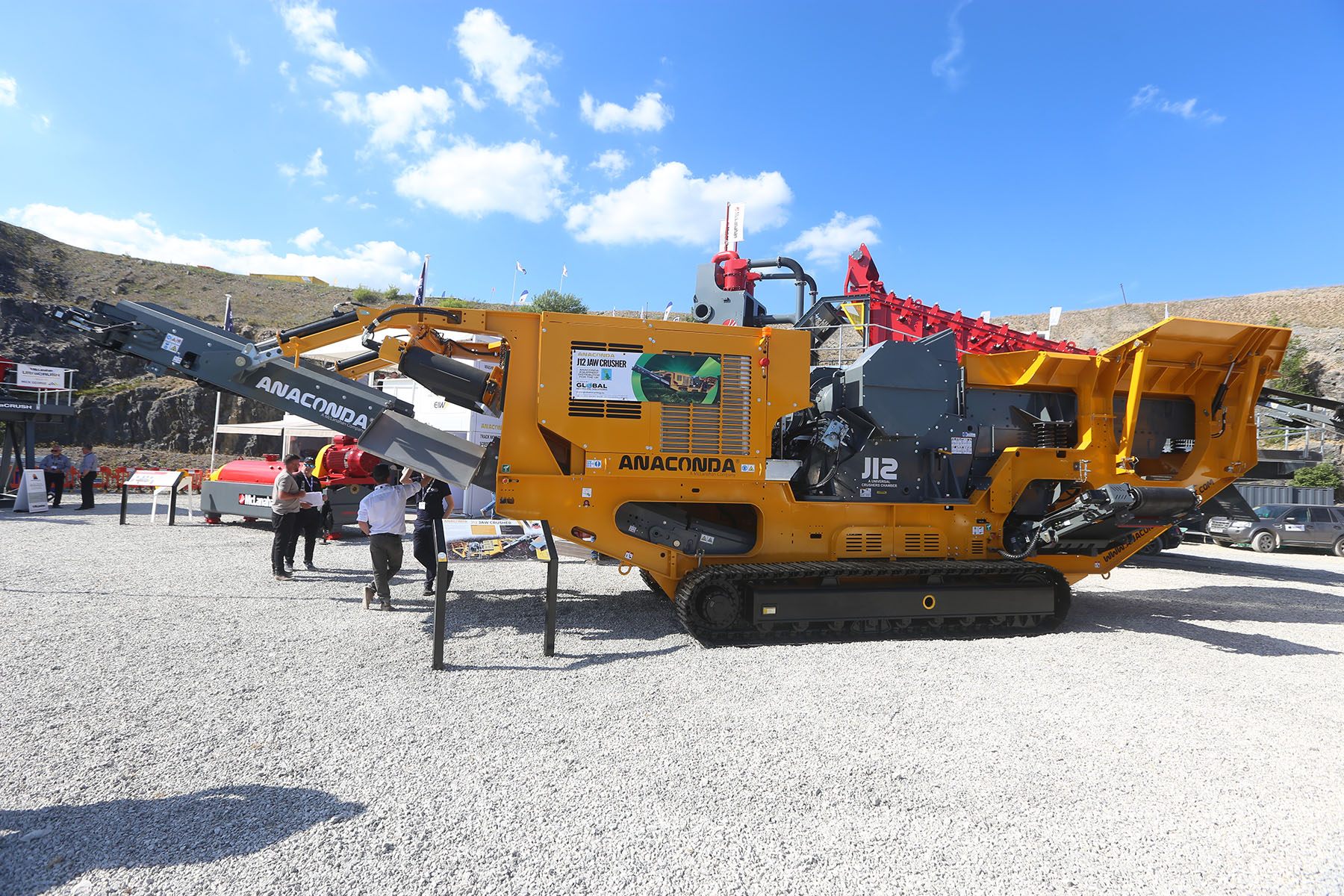
ANACONDA
Among the exhibits from Anaconda was their J12 tracked jaw crusher, which offers a 6.5cu.m in-feed hopper capacity. Weighing 45.2 tonnes, the tracked machine features a Universal Crushers jaw chamber measuring 1100 x 700mm. As a Cummins-powered, direct hydraulic drive machine, the J12 offers fully hydraulic jaw adjustment and reverse feed capabilities in the event of a blockage.
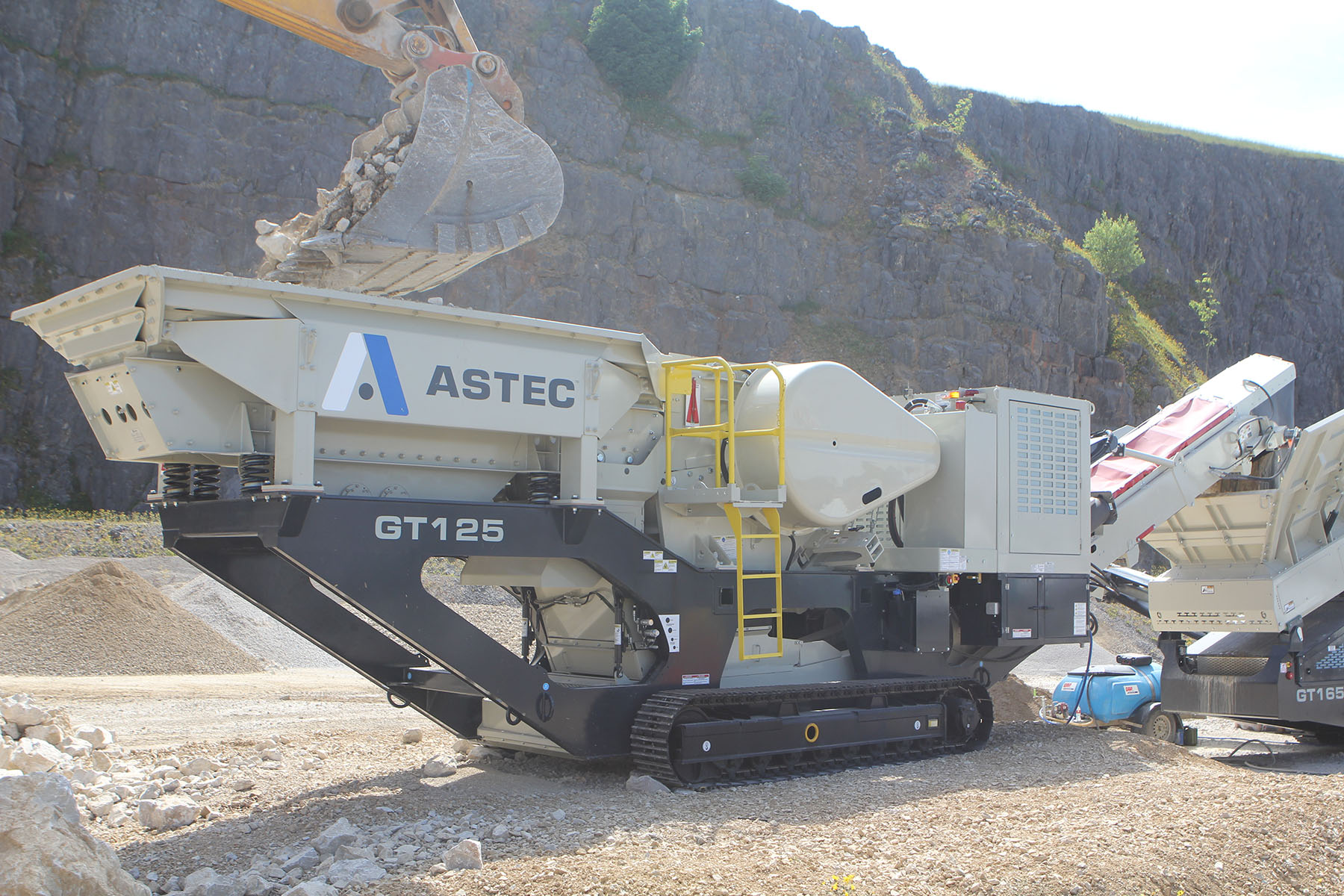
ASTEC
There are 16 brands of machinery under the American-based Astec Group corporate umbrella, providing machinery to work in every part of the chain from the rock face to the road surface. For example, their Roadtec Shuttle Buggy paver feeder machines are already well known to UK and Irish users.
At Hillhead 2022, Astec presented a selection of their mobile crushers and screeners. On static display was the GT205S three-deck inclined screener, which offers immense potential in high-end aggregate production operations. As an aside, Astec claims its screeners offer an industry-leading conveyor discharge height, reducing the demand on the site’s wheel loaders.
On the demonstration plot, Astec showcased its smallest jaw crusher, the 36-tonne GN125, which offers a 1 x 4.2m feeder, and a 686 x 1067mm crusher opening. Astec also claims a class-leading stroke for this jaw crusher, leading to a 25% increase in output, while the large flywheel reduces the machine’s overall power requirements. This jaw crusher was discharging directly into an Astec GT165DF scalp screener, a twin-deck machine offering a screen area of 1.5 x 4.8m.
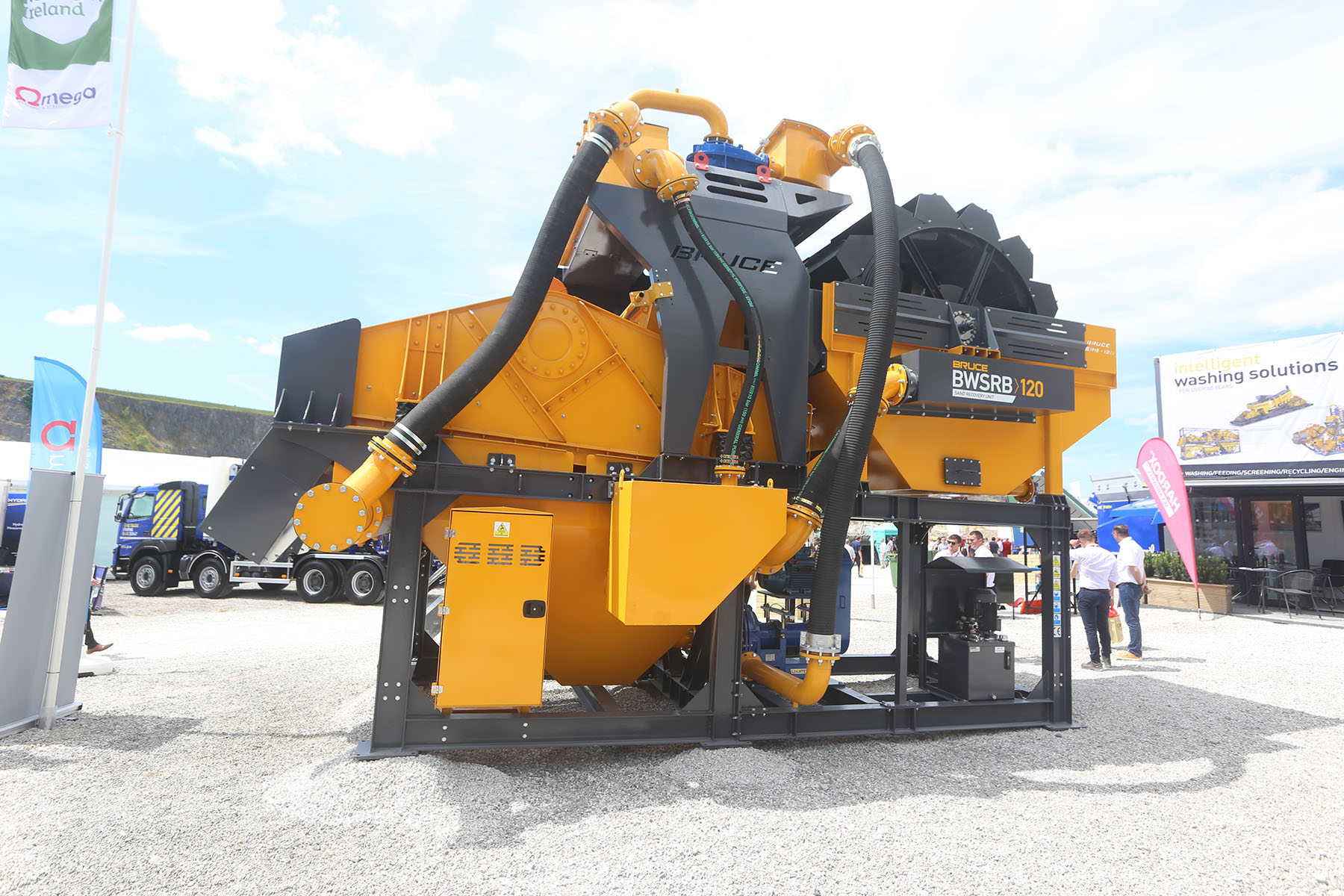
BRUCE ENGINEERING
Among its exhibits, Bruce Engineering presented the BWSRB120 sand recovery unit, the display unit having been pre-sold to Irish customer Hilltop Quarries. This machine features a double wheel design with a centrifugal slurry pump, two hydro cyclones, a collection tank and dewatering screens, all combined into the same chassis unit. It is able to recover 96% to 98% of all materials above 75microns, while silt and clays below this size are largely removed by the process. The BWSRB120E also dewaters the material, the end result typically having 12% to 15% residual water content.
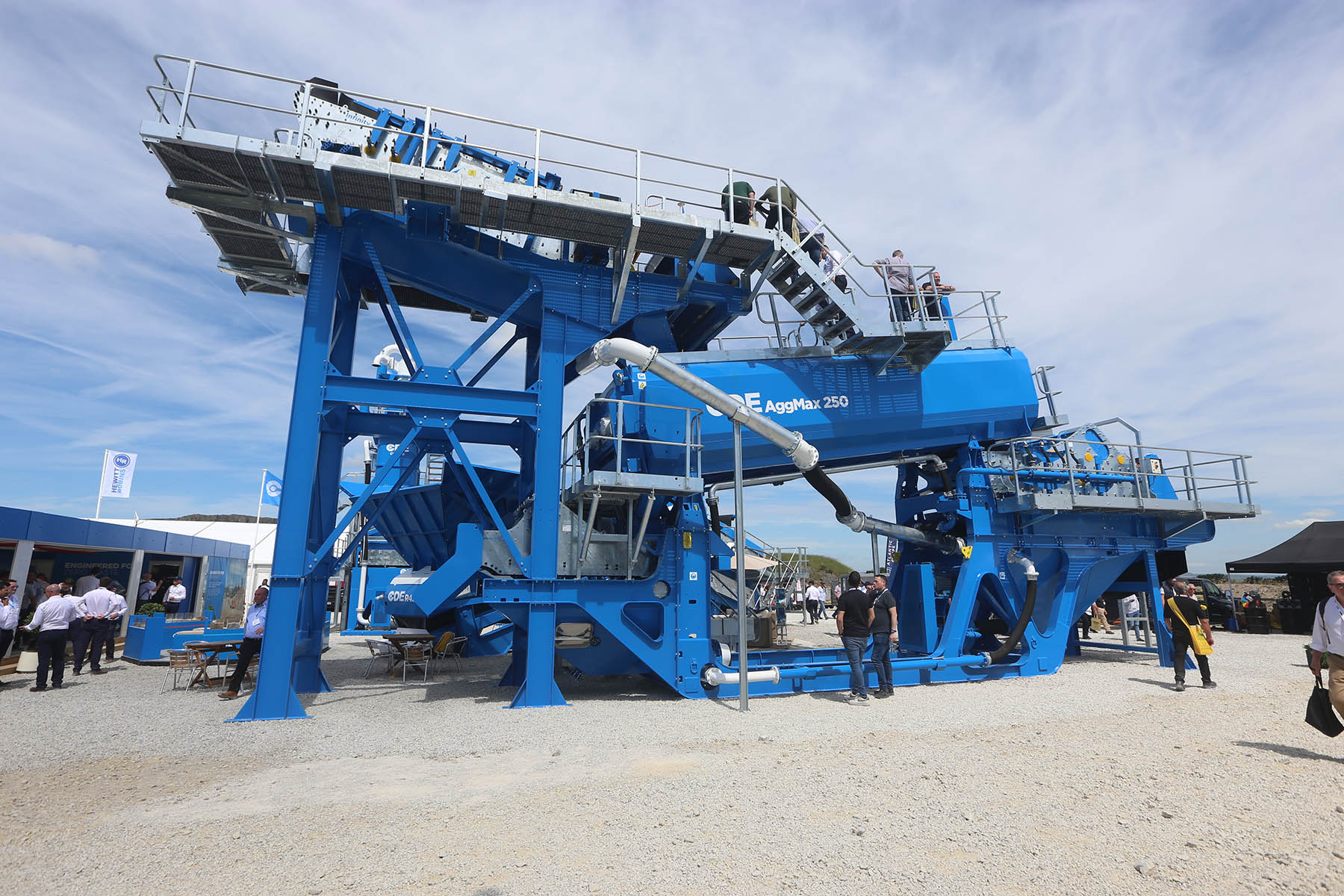
CDE
CDE, a leading provider of screening, washing and recovery plant, showcased its Evoscreen, Aggmax 250 and R4500 screeners. These modular units can be commissioned as part of a bespoke installation for sand and aggregate production, including recycling some classifications of construction waste.
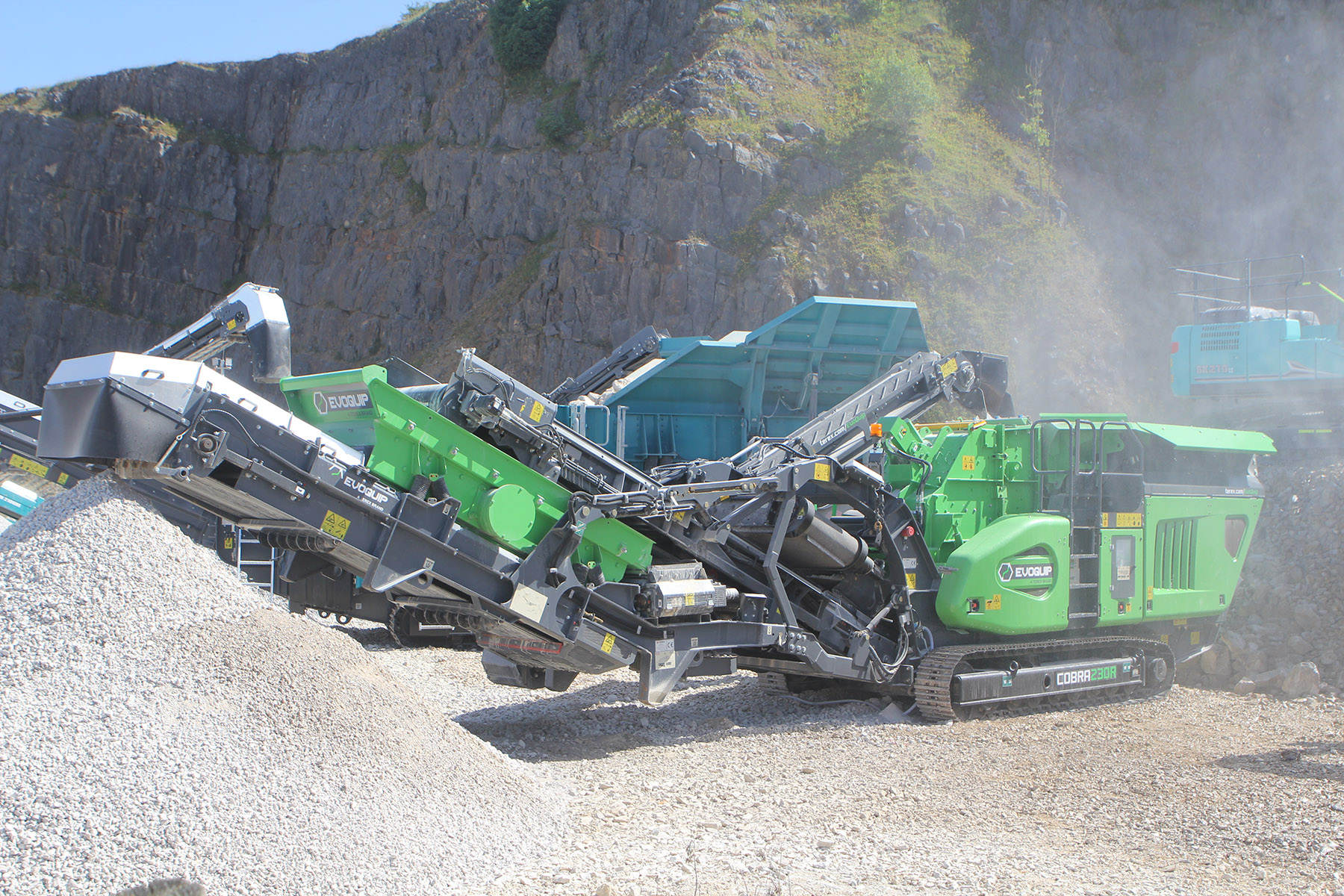
EVOQUIP
On the Hillhead site, Evoquip’s machines fitted in to the more compact end of the market. On the demo plot, a Cobra 230R impact crusher showed its capabilities over the three-day event. It features a hanging post screen and oversize recirculating/stockpiling conveyor. Like all others in the Evoquip range, this compact crusher offers a telematics system for remote monitoring of its operation and condition.
On the Evoquip stand, the highlight was the all-new Falcon 820 two-deck finishing screen. As the smallest of the company’s three-model range, the Falcon 820 features an 8 x 4ft screen box, while its overall dimensions remain reasonably compact for ease of transport.
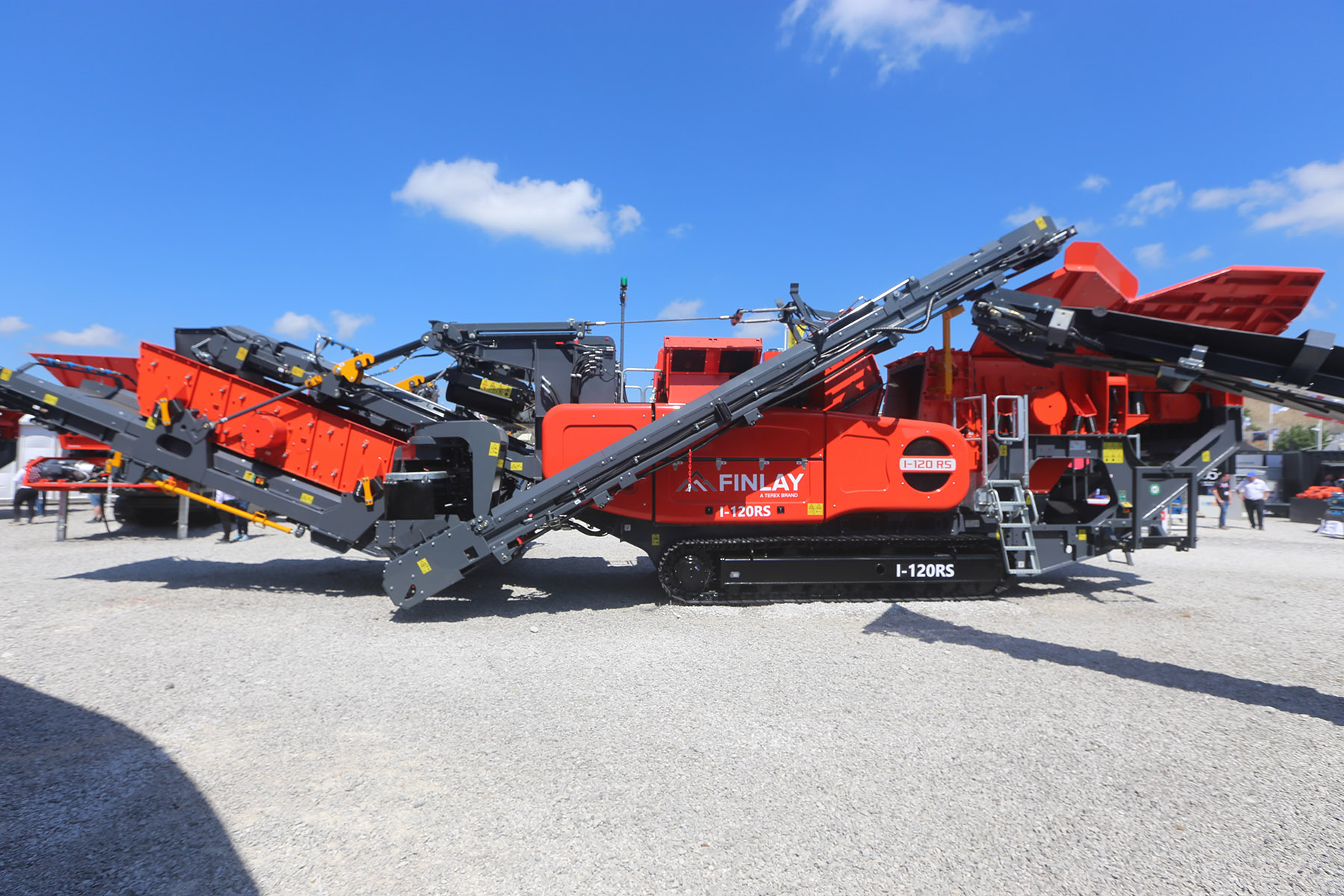
FINLAY
Coinciding with the rebranding of the Finlay marque, but still part of the Terex Group, the firm showed a large selection of machinery both on its stand and working on the demonstration area. A highlight of its static exhibition was the Finlay I-120RS impact crusher with a pre-screen and quick detach two-deck hanging screen, together with a recirculation conveyor that directs oversize material back through the direct drive crusher unit.
On the demonstration area, a diesel-electric Finlay J-1175 single toggle jaw crusher was at work, which is also capable of powering screeners and conveyors in the processing chain, further adding to the operating efficiency of such a drivetrain. On the Hillhead demo area, the jaw crusher was allied to a Finlay C1550 cone crusher, which discharged into the firm’s range-topping 696 three-deck screener.
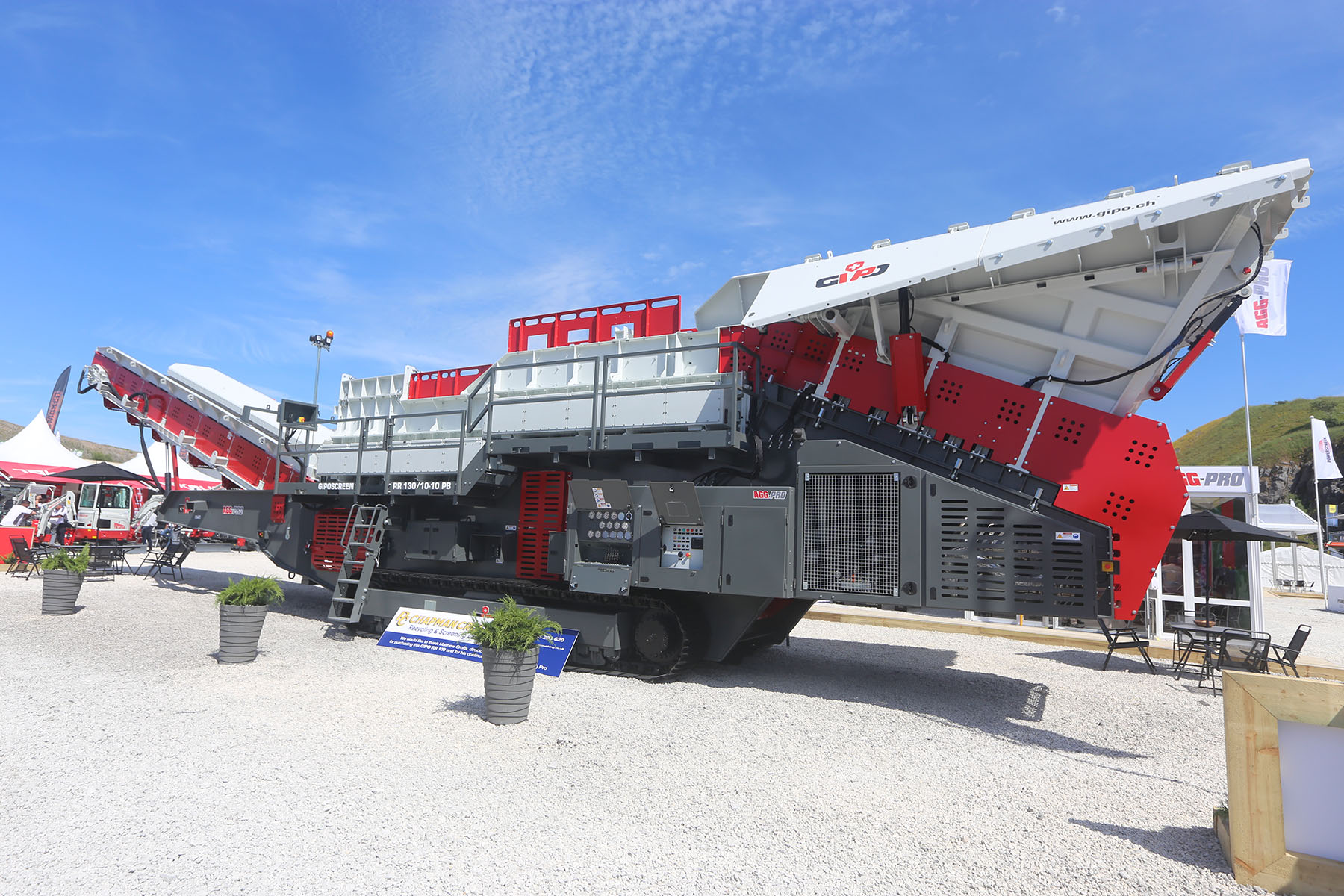
GIPO
Swiss manufacturer Gipo, represented at the show by Pro-Agg, displayed the Giposcreen RR130 10-10 tracked roll screen. It is a proven alternative for screening highly contaminated materials rather than a conventional trommel screen. Capable of an output of up to 600tph, the machine has a 1.3m grizzly width and features 10 grizzly shafts. The screened fines exit the machine via a side conveyor, while the useable product is discharged via the main conveyor. Power is from a 224kW Volvo engine driving the fully hydraulically driven machine.
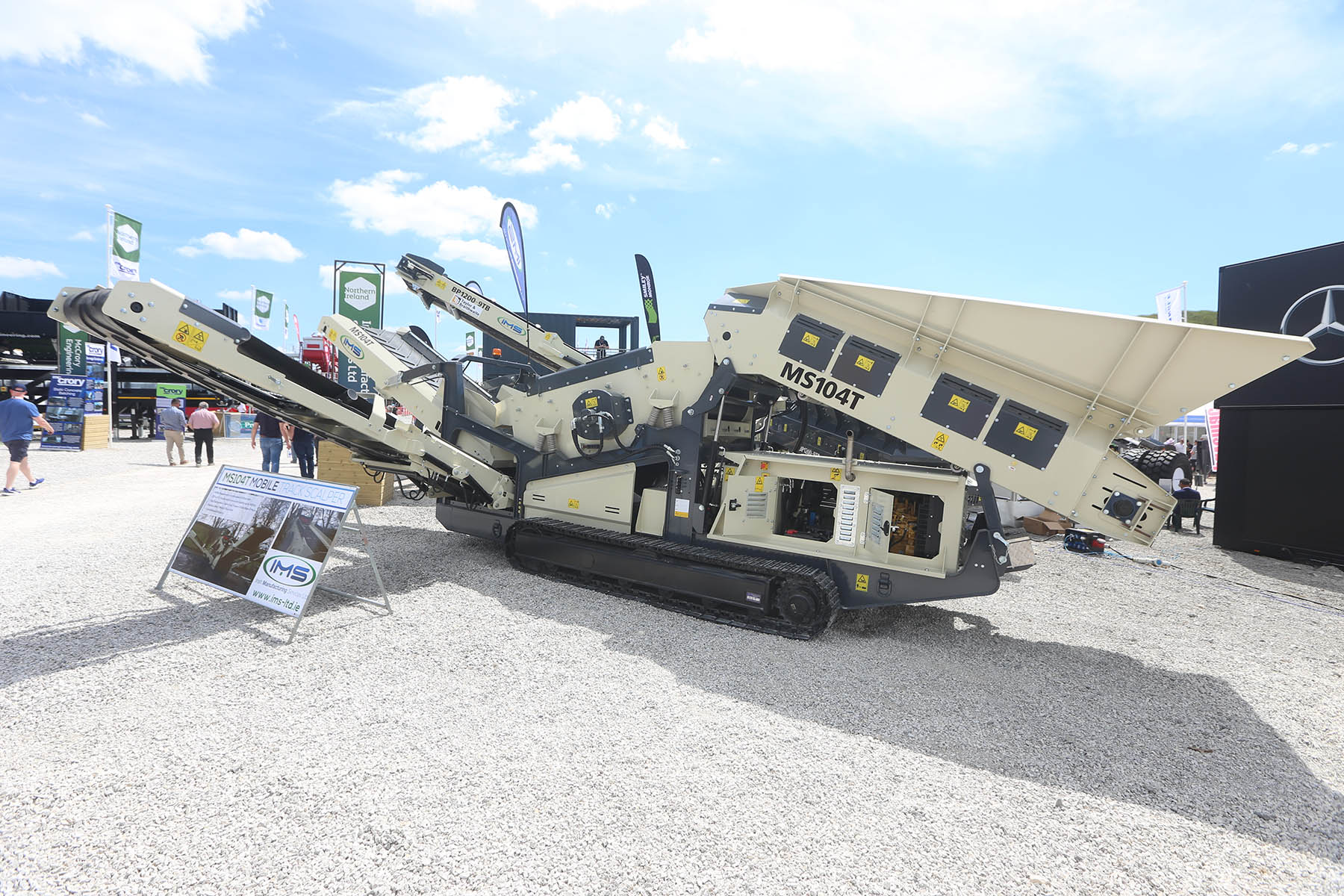
IRISH MANUFACTURING SERVICES
IMS, the abbreviated form of Irish Manufacturing Services, presented its 104T scalp screen at the show. Established in 2010, the County Tyrone-based company designs and builds a wide range of specialist equipment including tracked conveyors, silos and blending plants. The IMS 104T scalp screen features a 55kW Cat engine and Sauer Danfoss hydraulic motors. It has a hopper capacity of 4.6cu.m and the double deck screen measures 3050 x 1250mm. Fast set-up is ensured by the hydraulic activation and folding of the side wing conveyors.
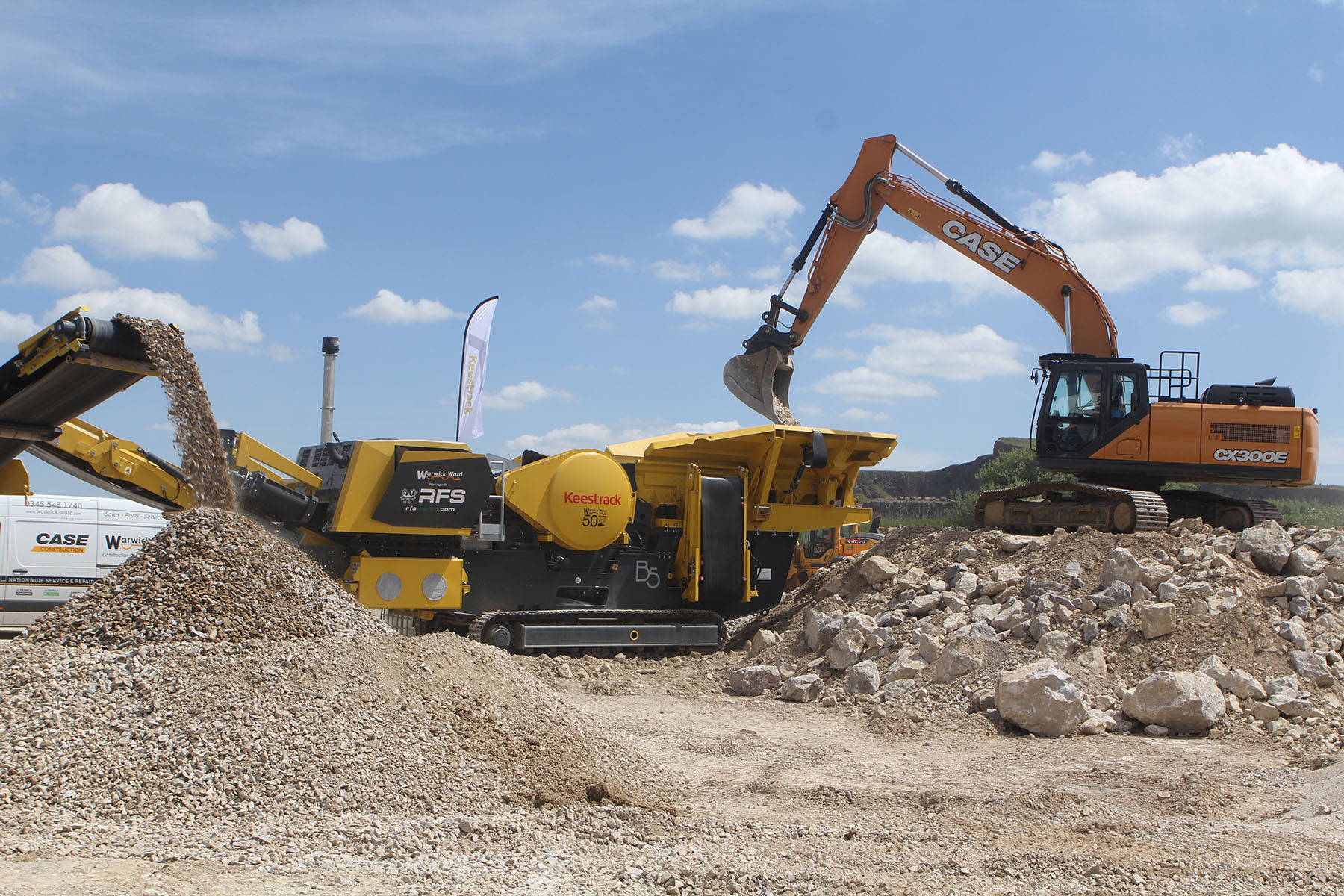
KEESTRACK
Keestrack and Case dealer Warwick Ward had an impressive working demonstration throughout the show, where the latest generation Case CX300E excavator fed a Keestrack B5 jaw crusher, which in turn fed a Keestrack K4 tracked scalp screener. The B5 jaw crusher can be factory ordered as a diesel-electric machine. With a generous in-feed capacity via an 1100 x 750mm opening, the B5 also offers good pre-screening capabilities. The working range of the pre-screen conveyor is said to be more generous than the norm, allowing the fines to be delivered well clear of the crusher.
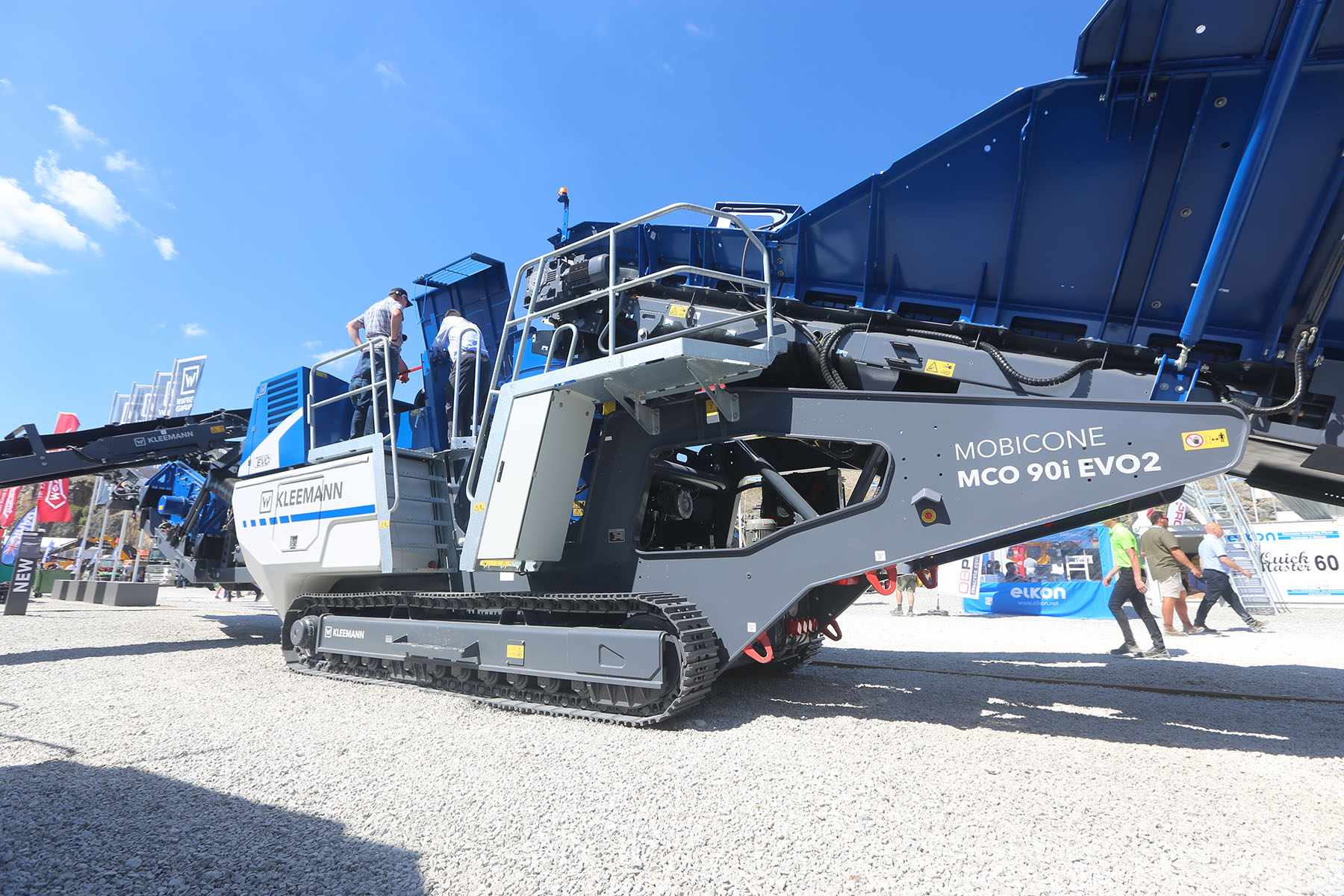
KLEEMANN
German manufacturer Kleemann presented a comprehensive range of crushers and screeners, with primary crushing represented by the Mobicat MC110i Evo2 jaw crusher, while the new Mobiscreen MSS802i Evo three-way split scalp screen was on static display.
However, they did not detract from the other exhibits, among which the Mobicone MCO90i Evo2 secondary cone crusher attracted much attention. Fitted with a generous feed intake, the machine’s cone crusher features a range of elements that are said to ensure the optimum level of productivity and quality. Included is a continuous feed system that is said to improve quality and consistency. The machine on show benefited from the incorporation of a suspended screen, which enables the segregation of oversize for recirculation, via the side conveyor, back to the cone.
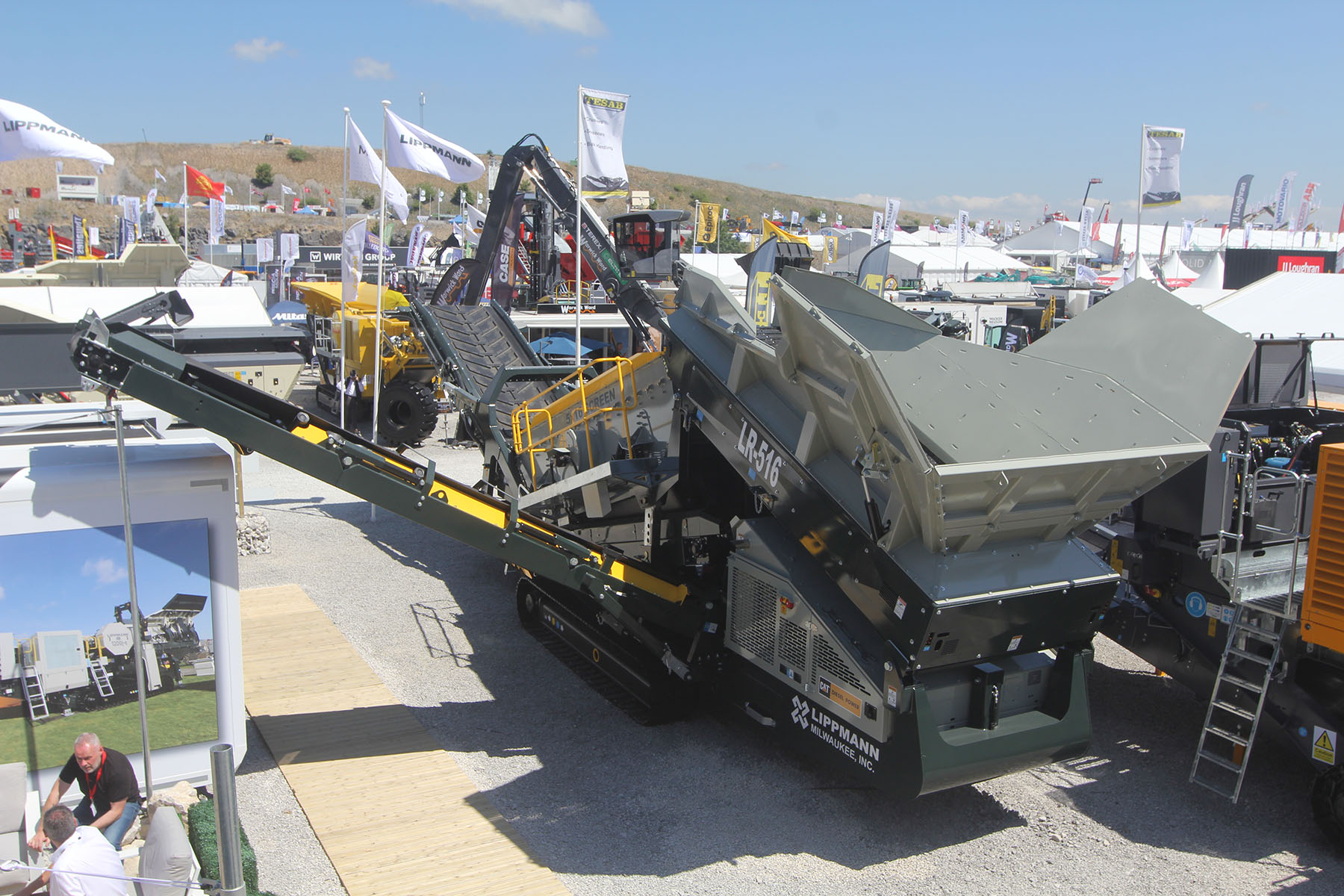
LIPPMANN
Another American brand to enter the UK market is Lippmann, established in 1923 and now producing a comprehensive range of crushers, screens and stackers. The firm was taken over by McCloskey in 2018, both firms then becoming part of the Metso Outotec Group the following year. However, Lippmann’s unique product designs continue to be very much in evidence, and among the Hillhead exhibits was the heavy-duty Lippmann LR516 two-deck scalp screen.
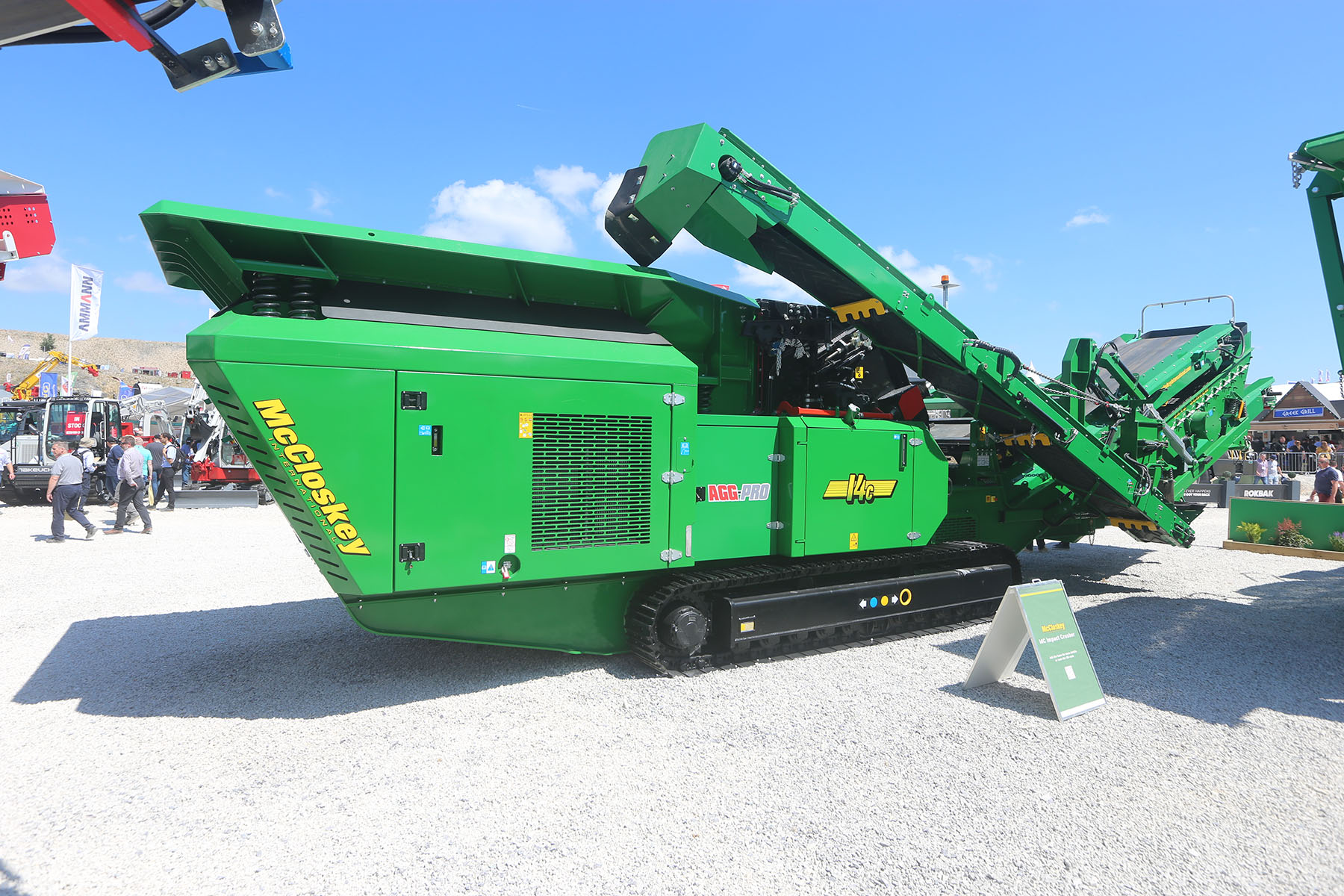
MCCLOSKEY
Among a large display of its machines, McCloskey showcased two brand new models, the C2C cone crusher and the I4C impact crusher. Capable of an output of up to 300tph, the C2C is designed to work in a range of applications, including in production trains typically comprising a J40 jaw crusher and 5130 screener to produce value added chippings of a range of different size classes. Using the MC200 cone, the C2C employs continuous load and material metering, it also offers a generous discharge conveyor height of 3.14m.
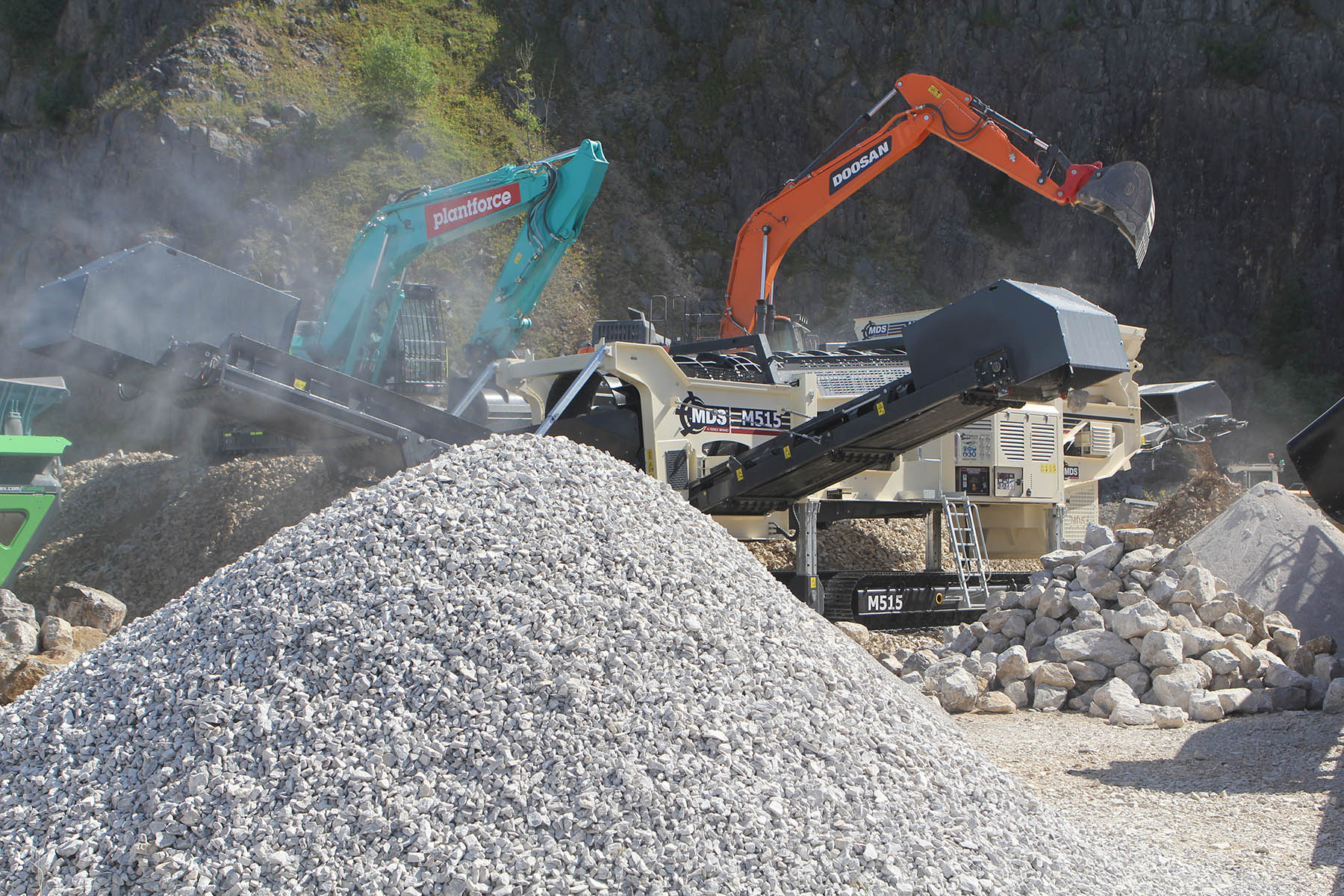
MDS
Now part of the Terex group, MDS showcased its 48-tonne, Cat-powered M515 trommel screen in the demonstration area. The M515 can handle material up to 800mm in size in its 1.5m-diameter drum, which extends to 5.5m in length. Capable of achieving three material fractions, the MD515 incorporates a hydraulic push feed from its intake. Following passage through the screening drum, material exits via one of three discharge conveyors, the height of which is maximised by the machine’s ability to elevate above its standard transport height, in the interests of increasing stockpiling capacity beneath the conveyors.
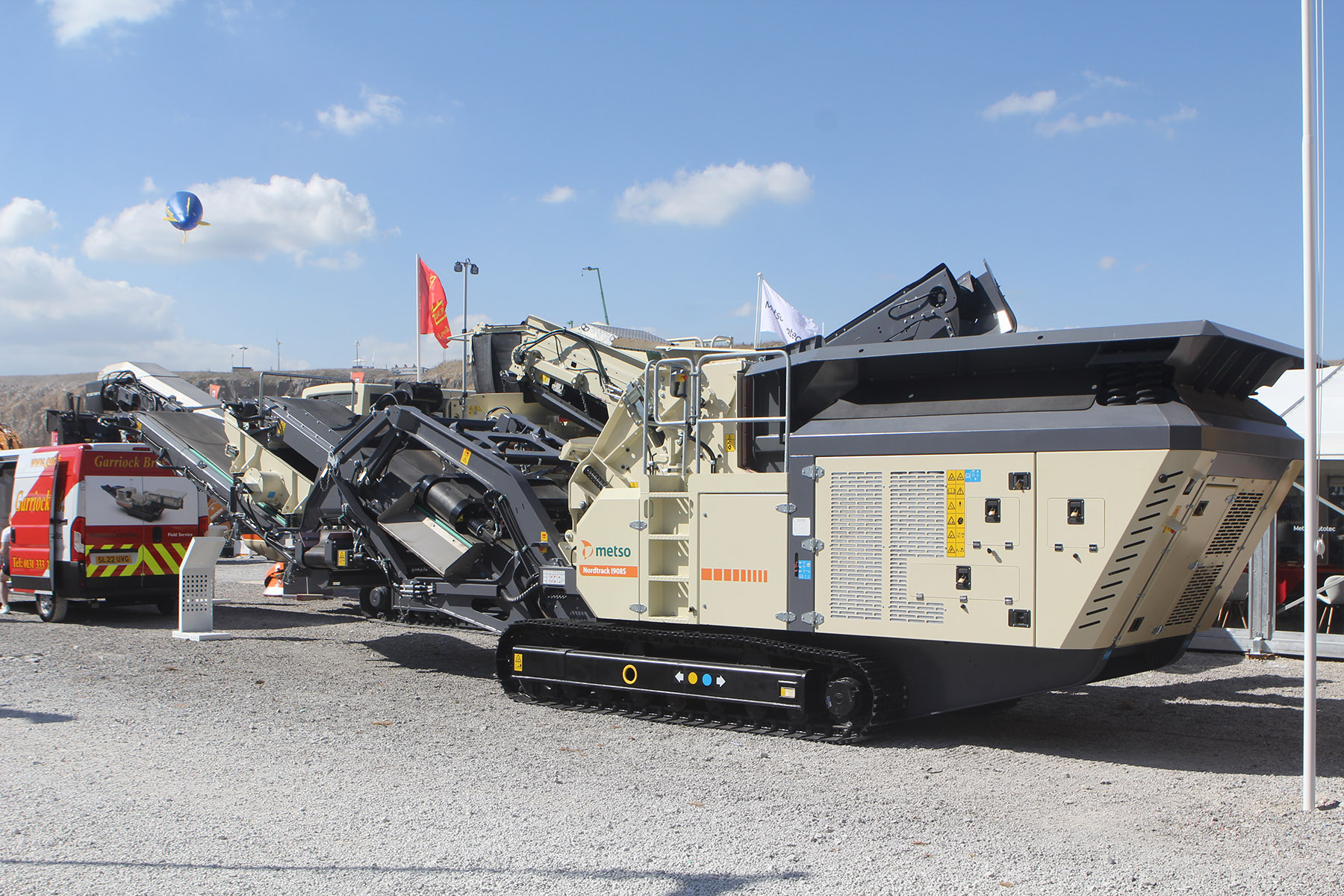
METSO OUTOTEC
With Metso Outotec represented by exhibitors the Duo Group and Garriock Brothers, there was a particularly comprehensive range of machines on display throughout the show, including a Lokotrack LT300HP tracked cone crusher working in the demonstration area.
Some lesser-known models were in the static exhibits, including the compact and versatile 27.5-tonne Nordtrack I908S, part of a range of equipment aimed at the smaller end of the market. Launched in 2019, the I908S is a vertical shaft impact-type crusher that features a hanging screen. Its 180-degree radial conveyor can be used for oversize recirculation, or to stockpile oversize away from the crusher.
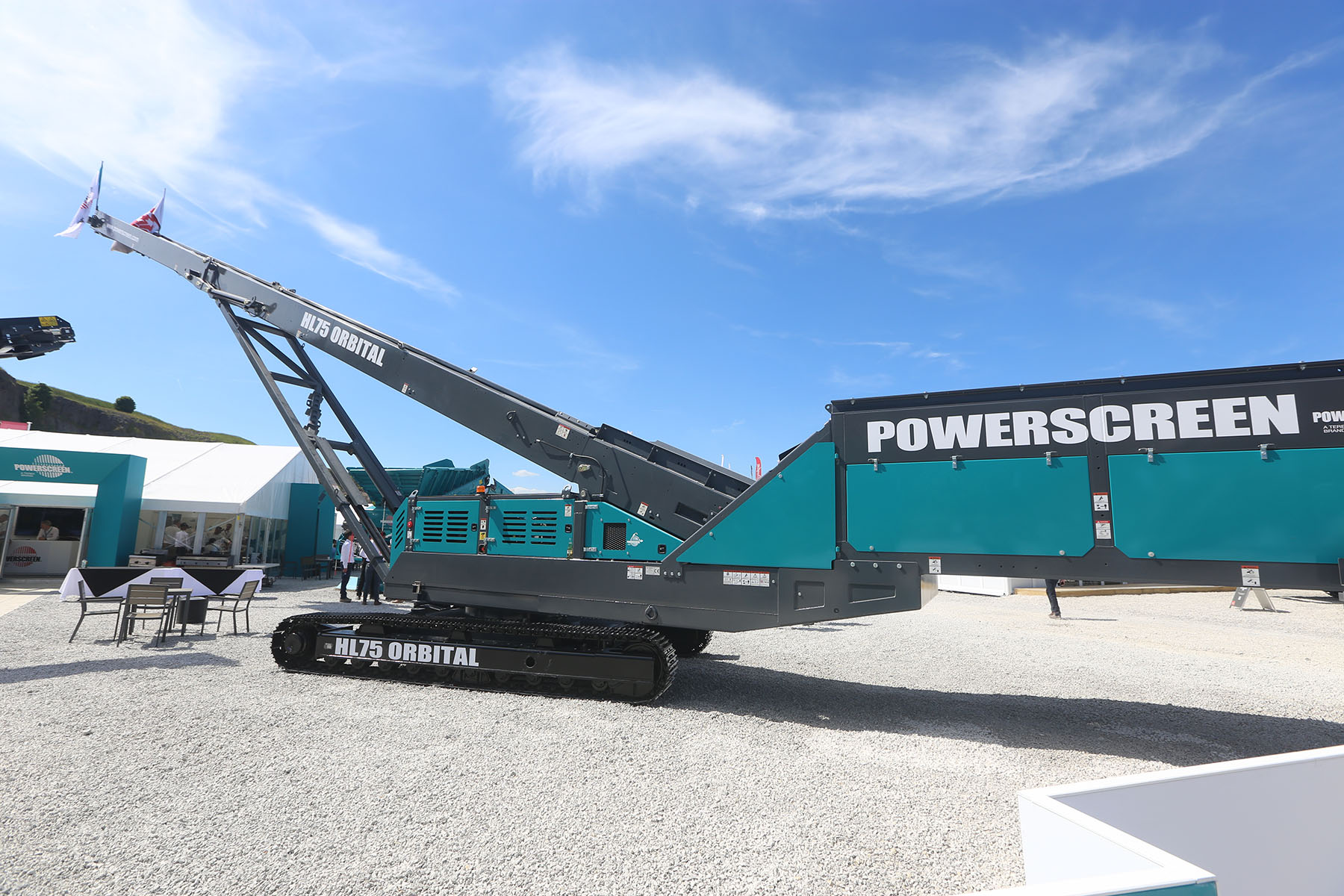
POWERSCREEN
As always, Powerscreen had one of the more impressive displays, both on the demo area and the stand. Among them was the Chieftain 1700X, one of the most recent additions to the screener range. Featuring a four bearing screen box, the 1700X is a three-deck type machine and is said to be particularly user-friendly when it comes to changing between different screen media. Other screeners of interest included the Chieftain 2100XE working in the demo area, which featured a new diesel-electric drive system, as well as the recently introduced Titan 2300 scalp screener.
Another interesting exhibit was the Powerscreen HL75 tracked orbital conveyor, which is a further manifestation of the firm’s wish to become a full-line manufacturer, not just crushers and screeners.
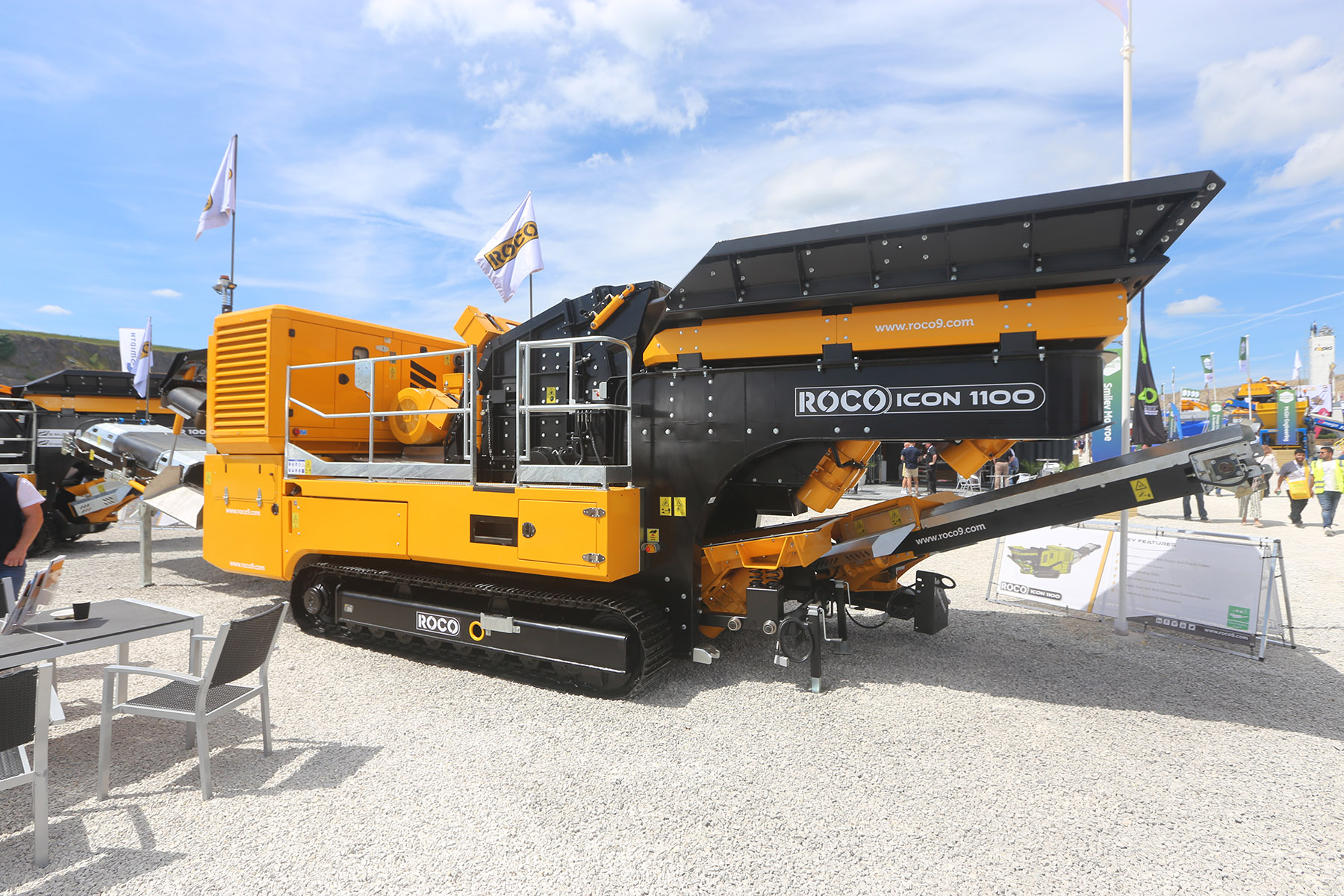
ROCO
The exhibits of County Tyrone-based Roco included the existing Ryder 1000 jaw crusher and the all-new Icon 1100 impactor. As a diesel-electric drive machine featuring a pre-screen, the Icon 1100 represents an important addition to the Roco range and is a crucial step forward for the manufacturer in offering a complete line of crushing and screening equipment.
The Ryder 1000 was introduced at the end of 2020 and has been well received by the market. It is a diesel-electric machine powered from the on-board Cat engine, or through an external 400v power source. This machine highlights Roco-specific design features, including greater clearance beneath the crushing chamber and the metal deflector plate, for improved belt protection, ideal for demolition and recycling applications.

RUBBLEMASTER
Rubblemaster presented a range of equipment, including the RM120X crusher and MSC8500E screen on static display, while their RM100GO! diesel-electric impact crusher worked in the demonstration area. Sold to Tony Brown by dealer Taylor & Braithwaite, the RM100GO! is the latest diesel electric drive version of this versatile crusher and can also be directly connected to an electric supply. Employing a four-hammer design with three operating speeds, the crusher was fitted with a suspended conveyor for segregation of oversize, which was recirculated by the side-mounted conveyor.
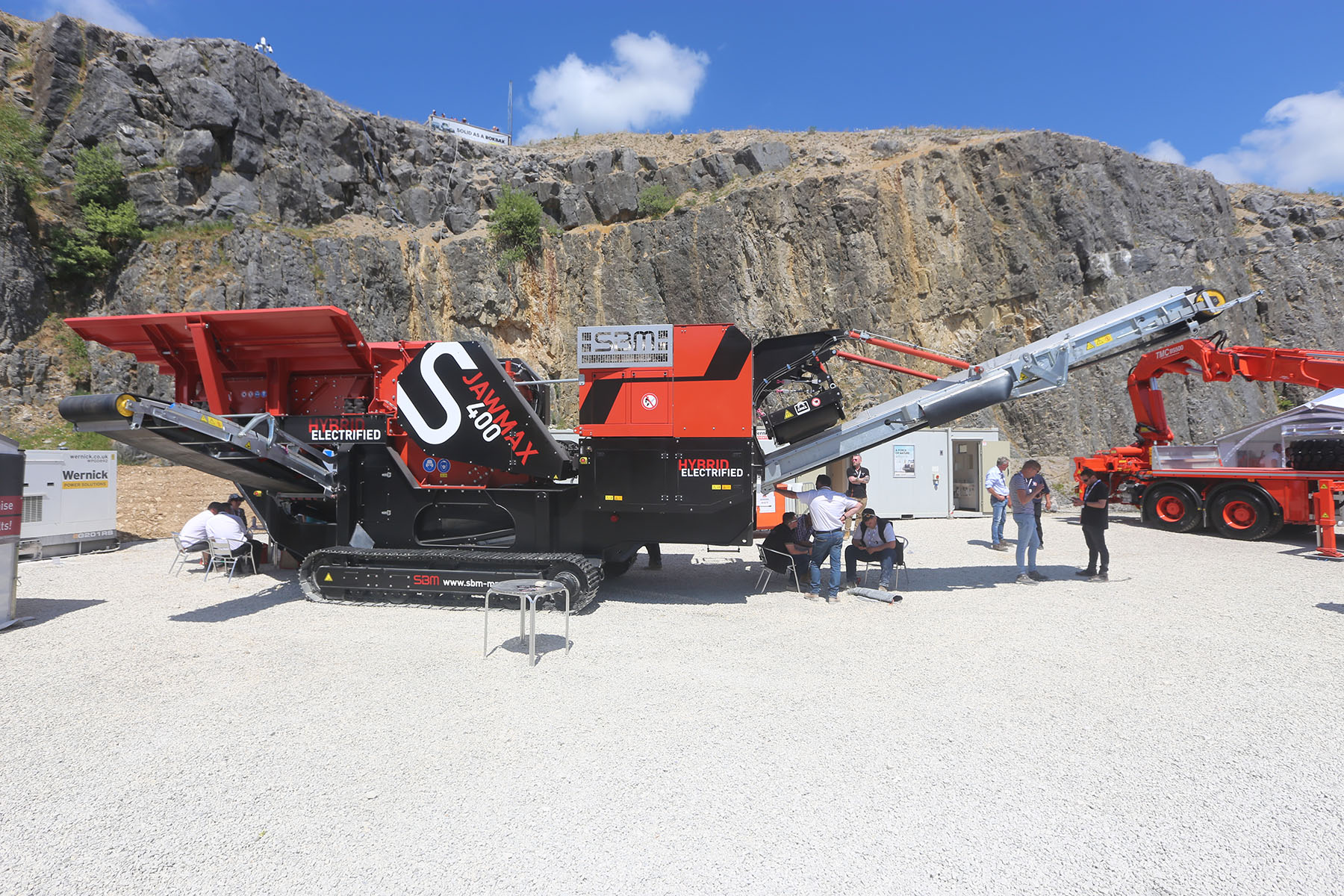
SBM
Austria-based SBM is a new entrant to the UK crusher scene, and Scottish-based dealer Hodge Plant presented two models from the extensive range from this established manufacturer. On the demonstration area, a 47-tonne SBM Remax 400 impact crusher was working, configured with a pre-screen with side discharge recirculation conveyor. The material from the in-feed is then directed to the 1200 x 800mm impactor crusher, which features 120kW crusher drive. The machine draws power from a 300kvA diesel generator and is quoted as having production ratings of up to 400tph.
On static display was a 36.5-tonne SBM Jawmax 400 diesel-electric tracked crusher, which offers inlet dimensions of 1100 x 700mm.
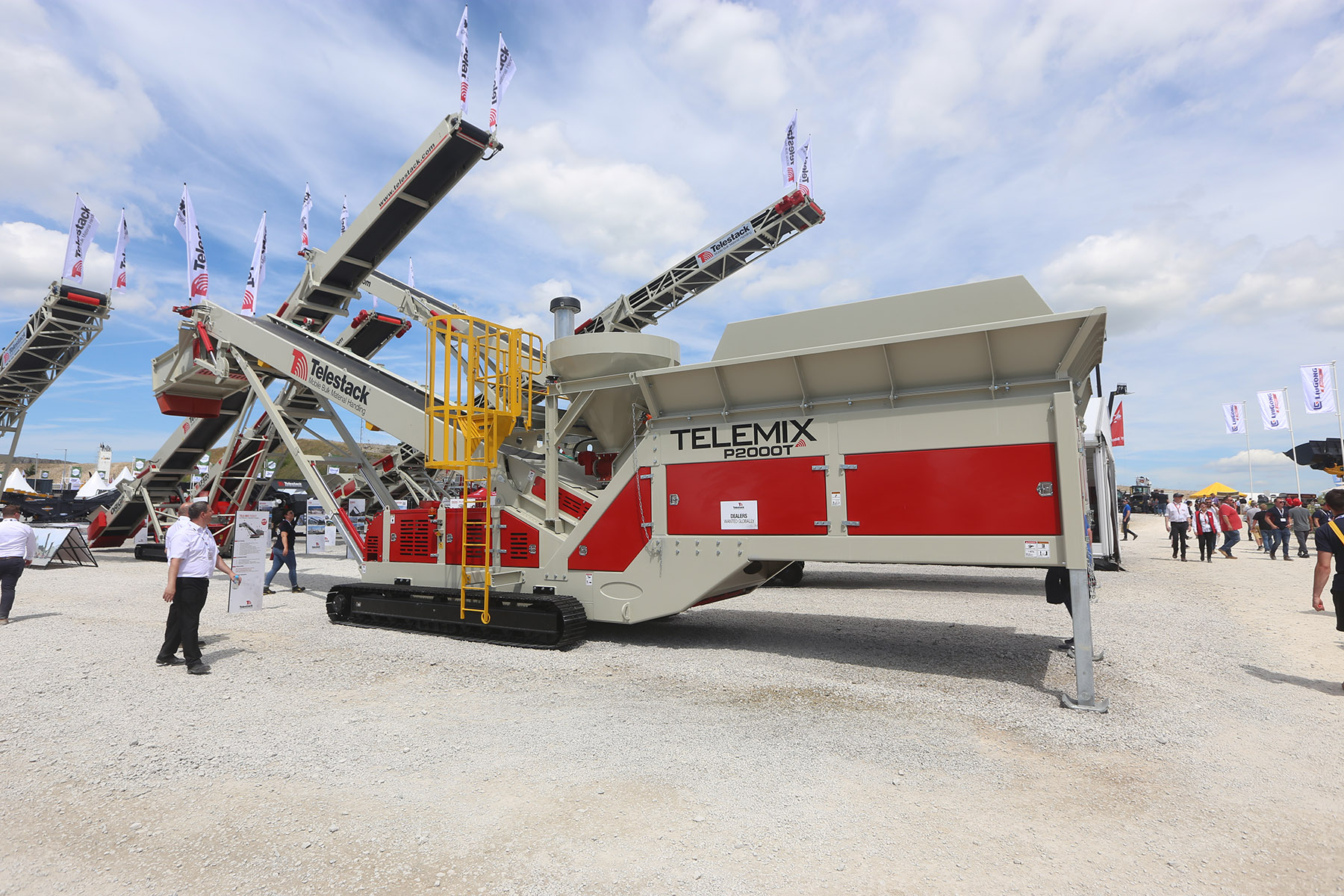
TELESTACK
As always, Telestack had one of the more comprehensive displays at Hillhead, focusing on its range of stockpiling and loading conveyors. The standard range of conveyors, radial units and telescopic variants can be custom-tailored to match a specific application. But what really caught the eye was the Telemix P200T pugmill, which is used in applications that blend material, or for the addition of lime, in addition to many specialist activities.
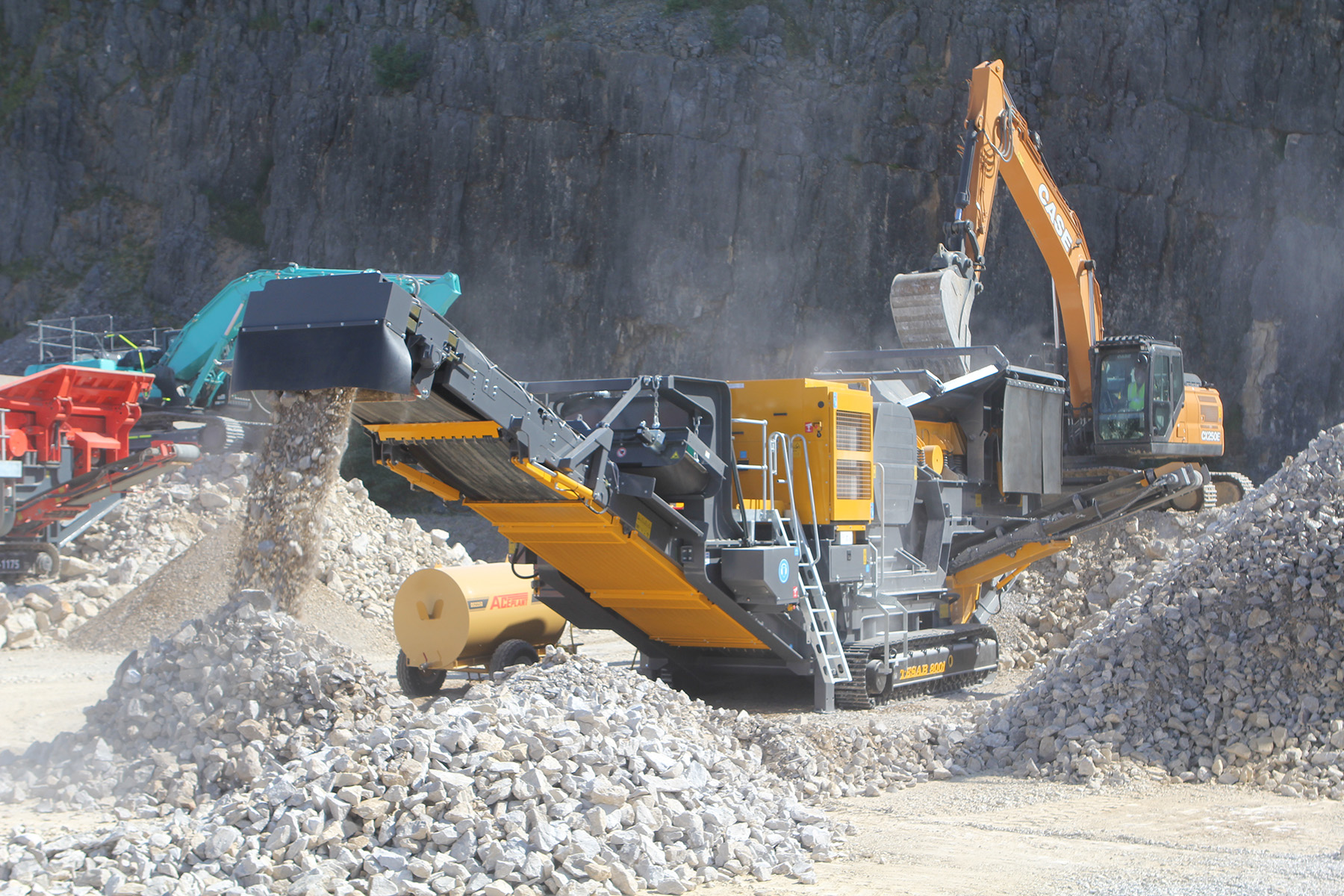
TESAB
Tesab presented its latest 700ie model on static display while the 800i worked in the rock processing area. Both jaw type machines, the 700ie signals the firm’s entry into the diesel-electric drive market. Based on the existing 700i model, the 700ie features an on-board generator based on a Cat 225kW engine, or can be powered from an external electrical source. Capable of an output of up to 350tph, this new variant could reduce the fuel bill by a third, compared to the standard diesel engine driven machine.
To aid access, the discharge conveyor offers a hydraulic raise and lower facility. In addition, the machine, like the rest of the Tesab range, is technology rich, featuring the latest control systems that can be accessed remotely via a mobile app.
This article featured in the September 2022 issue of Earthmovers.
Subscribe to Earthmovers!
Subscribe to the industry-leading construction machinery publication here.
- Earthmovers is packed with all the latest construction machinery news and information to keep you up-to-date with industry developments.
- Impartial in-depth reviews will ensure you buy the best whatever your budget
- First-hand experiences of genuine owners and operators
- On-site analysis of the latest products by industry experts
- Save on the newsstand price of 12/24 issues and receive your magazines direct to your address, usually before it’s in the shops!