by Nick Drew | Wed 05 Feb 2020
Dibynnedd: Welsh for Reliability
Taking another look back at one of my previously published Earthmovers Magazine articles and bringing it to life on the internet with alternative photos and video.
Like many a Welsh plant man before him, Mark Griffiths spent a lot of his early working life in the open cast mining industry. Mark spent 10 years working at the Ffos Las Open Cast Coal mine in Trimsaran, in the Gwendraeth Valley in Carmarthenshire, which at one time was the largest operating open cast mine in Europe. During his time at Ffos Las Mark got to operate a vast range of machinery gaining invaluable experience that would put him in good stead for the future.
When the work there eventually came to an end in 1999 Mark decided to fulfil a long-term ambition to have a go on his own as an owner/operator, with the formation of MRG Plant. The business that bares Mark’s initials initially started out doing general plant hire, performing such tasks as excavating footings, drainage works, site clearance and excavation works for small builders.
Following a busy and largely successful 2 years Mark took the decision to branch out further into the groundworks side of things, pricing for jobs and undertaking them as a contractor, to cut a long story short he hasn’t stopped since, Talking about his business Mark said, “We are always busy and that’s really good, I run a tight knit operation, its mainly just me and my cousin who is a subbie bricklayer and as and when I need them, I can call on some other excellent subbies to help us out. As a side-line I also run two concrete mixer wagons and employ two full time drivers for those, so it keeps us on our toes at times!”
His first ever machine came from the JCB stable, Mark takes up the story, “My first purchase was 3 tonne JCB 803 model and I also invested in a 7.5 tonne lorry to move it around on, the truck of course could also be used for moving materials too so it was a good investment and made me independent. I sold that machine and bought a larger 804, then a while later did the same going up in weight with the purchase of a brand new JCB 806, that machine was totally bomb proof, in fact the chap I sold that too locally is still running it today with over 7,000 hours on it!”
Mark continued, “After I’d sold the 6-tonner I purchased a 6.5 tonne JCB which if I’m honest, I have to say gave me some issues. After that experience I turned to Japanese manufacturer Takeuchi for my mini excavator requirements through our local dealer JDS Machinery at Pencader.
My first dabble with the red and grey was a TB285 which I have to say was a phenomenal machine, I had her for over 4 years and never put a spanner to it except for routine servicing. I then had 2 x 1.5 tonne class TB216’s and in 2016 I purchased a 15-tonne TB2150 which was like a mini excavator on steroids! You need a lot of work for that size machine though, so I didn’t keep it long and downsized back to a 4-tonne TB240. This was later replaced by my first TB290 which has recently been traded in for this my current TB290-2 model which I’m told was the first of its kind to be sold in Wales”.
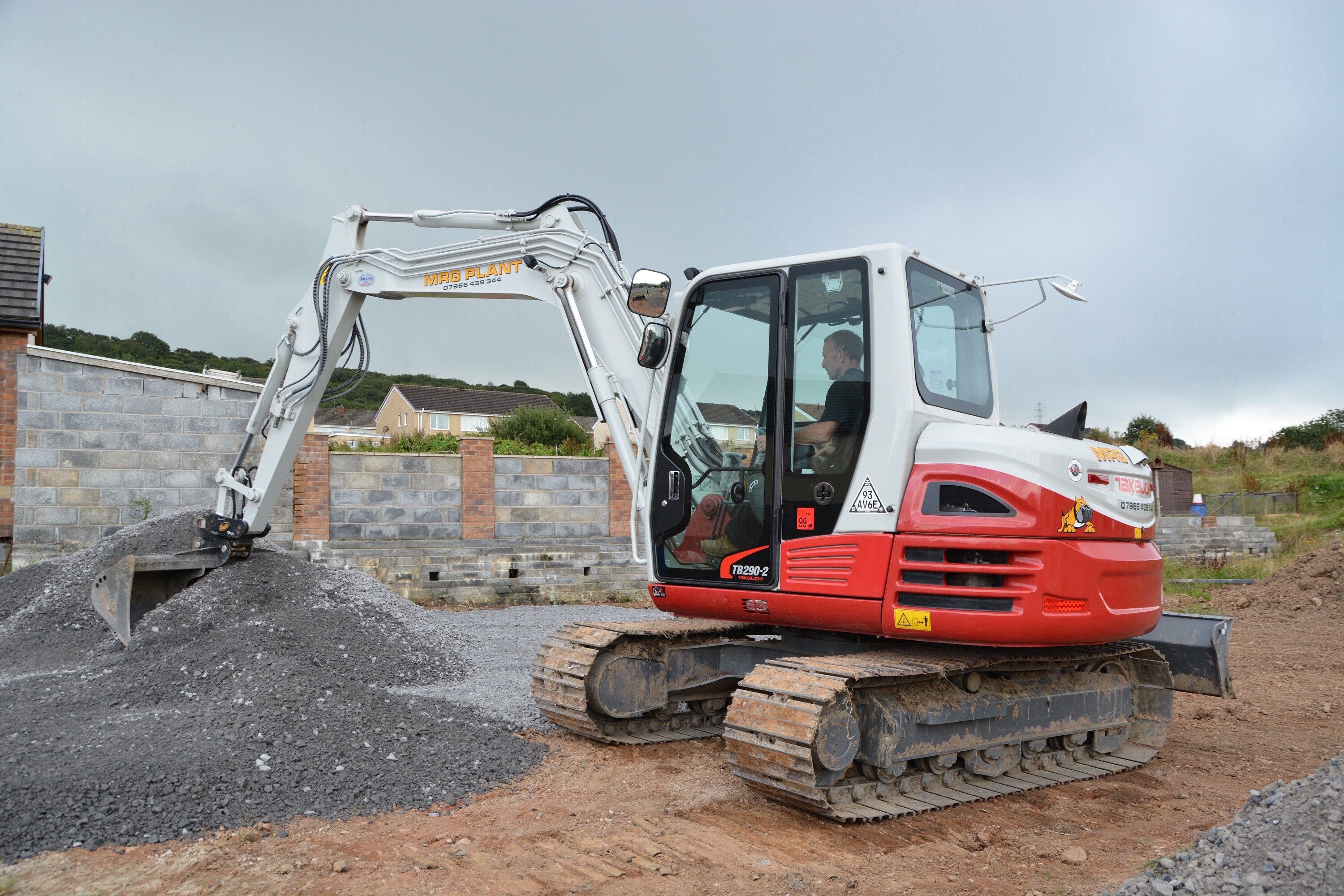
Mark was clearly delighted with the machine which had just passed 205 hours on the clock on the day of our visit, “I’m very happy with the Takeuchi product, I really cannot fault them in anyway, shape or form, they are just so reliable and never let me down”.
We caught up with man and machine on the first phase of a 10-phase private housing development in Trimsaran, Carmarthenshire, where Mark is doing all the groundwork and infrastructure works for 78 houses.
WALKAROUND
First thing you notice as you approach the TB290-2 and what sets it apart from other Takeuchi’s at the moment is the cosmetic splash of red paint around the back end and sides which is higher than on previous models. Another eye catcher on Mark’s machine is the very original “Digger Dog” logo which was designed for Mark by Marie at Eagle Signs, based on a bulldog with a mouth like a digger bucket it really is a cracking piece of artwork!
On this machine Mark has specified the optional 550mm wider steel tracks on the TB290-2 (standard fitment is 450mm) apparently, he specifies steels on all his machines as he prefers the durability and finds them better all round for his type of work. Two track guards are fitted on either side, one at the idler and one midway along the undercarriage.
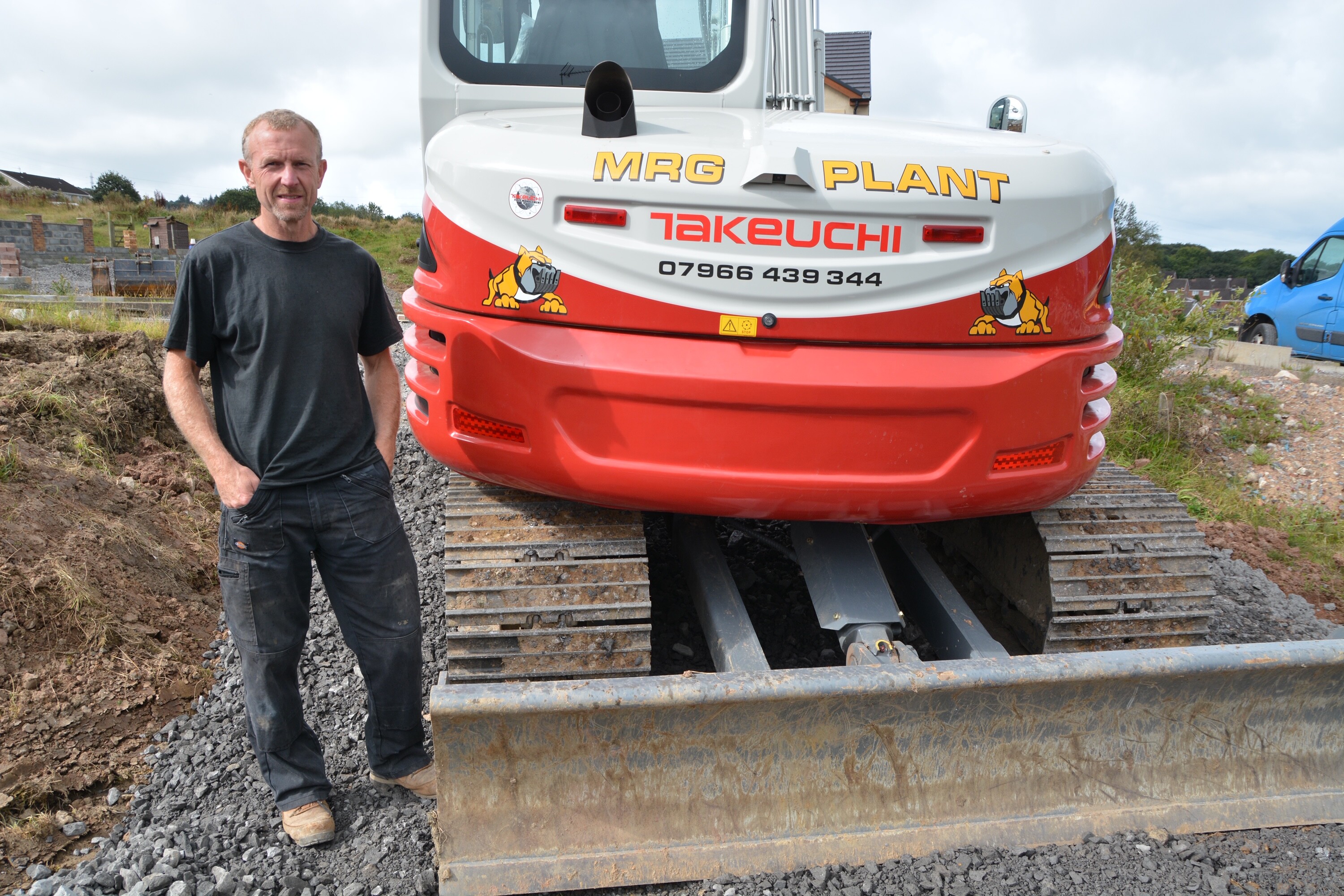
Same as on the earlier TB285 and TB290 models the gas strut assisted gull wing bonnet cover on the offside of the machine raises up to reveal a host of tightly packed in components including the main valve block, hydraulic oil tank, expansion bottle and screen wash bottle are located side by side and the 128 litre fuel tank. An electric refuelling pump is fitted as standard in this area and a handy sight tube is located down the side of the tank so you can easily gauge when refuelling is complete. The diesel tank filler point can also be accessed by a smaller lockable opening side panel too, rather than lifting the whole canopy.
To the rear Mark pops the bonnet to reveal the new heart of the TB290-2, the 4-cylinder turbocharged Yanmar 4TNV98CT-WTB which is Stage V emissions compliant and uses a DPF to achieve these standards and has a power output rating of 51.6kw @2000rpm. This unit replaces the Isuzu power pack in the previous model which was rated at 52.0kw producing a maximum torque of just 255 N/m while the new Yanmar motor produces significantly more at 308 N/m at the same rpm.
The engine bay is also home to the new larger hydraulic pump, the blue-chip component from leading Japanese manufacturer Kawasaki offers vastly improved oil flow delivery ensuring enhanced performance. Working in unison with the engine and other hydraulic components this enables the machine to perform better and more smoothly when using multiple functions, like when slewing and tracking with a manhole section for instance, you don’t get that feeling of one circuit slowing down another, making such operations a lot safer and less jerky in the movements.
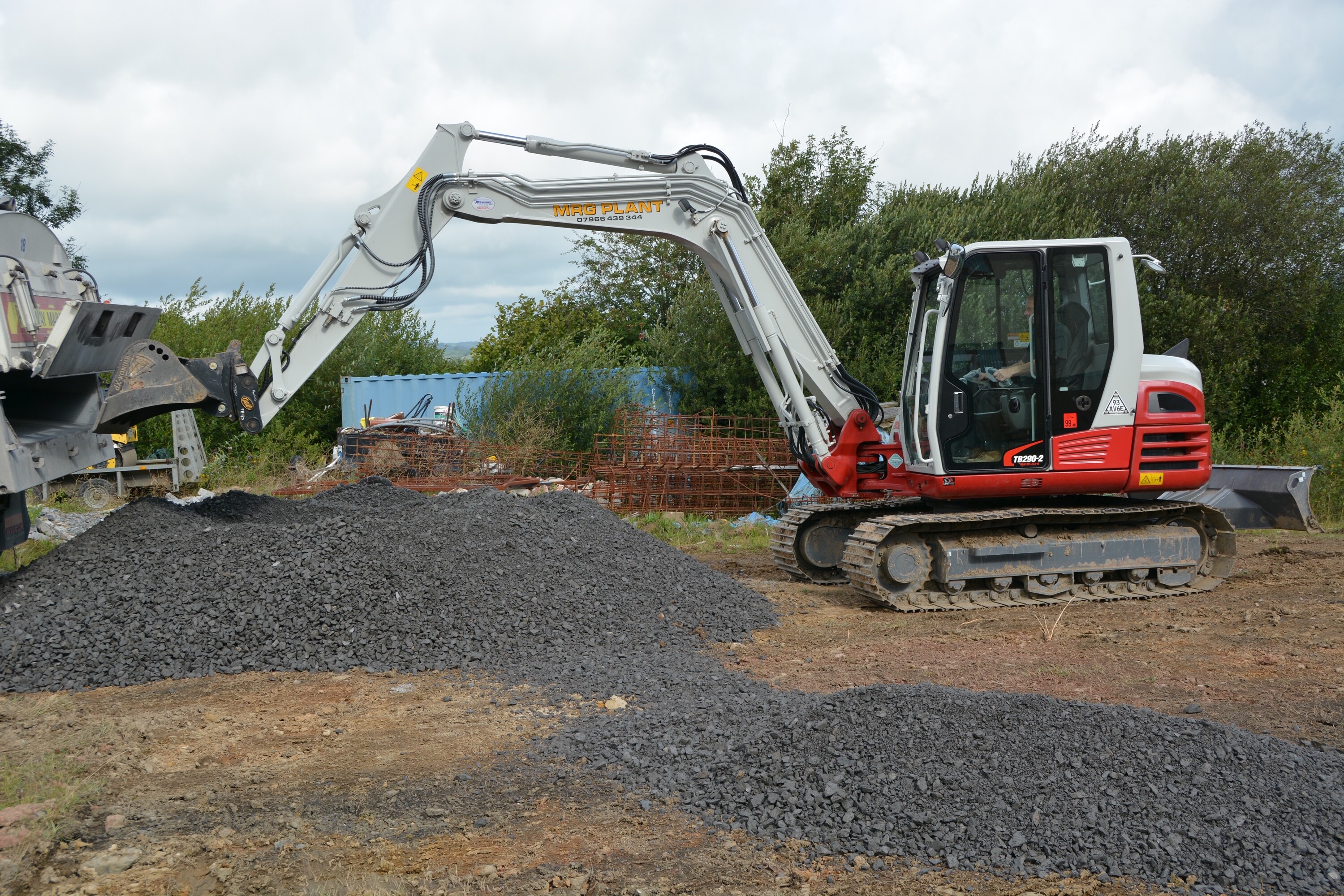
An all new LED work light package is now standard consisting of 2 x forward facing on the cab roof, 1 x boom mounted and 1 x forward facing on the offside canopy. Extra light options are available on request to meet specific customers requirements.
Mark’s machine is fitted with the standard boom and long arm combination which offers a maximum reach at ground level of 7,290mm and a maximum dig depth of 4,580mm. Also, as standard boom and dipper check valves are factory fitted and the machine pre-piped for 3rd auxiliary lines. Boom off-set is 700 to the right and 600 to the left.
At the business end of the dipper Mark specified a Geith fully automatic hydraulic quick coupler and a full set of buckets from Rhinox, at first Mark felt that the buckets lacked capacity, in terms of not being deep enough, but dealer JDS Machinery arranged for Rhinox re-engineer the buckets to make them larger.
Climbing into the cab and it’s all that we have become accustomed to with the Takeuchi machines, a nice spacious interior and as Mark said, “It’s got everything as standard, what more could I possibly need in there” standard fitments include full climate control air conditioning and Bluetooth mobile phone connectivity.

The full colour monitor offers a whole host of information back to the operator in a clear cut easy to use and read layout. In this model the operator can also select to see the rear-view camera view, but according to Takeuchi from next year this will become an automatic feature once reverse tracking is selected. Operators can pre-set auxiliary modes on the VDU to match individual attachments flow requirements. The machine also features TFM, Takeuchi’s new Telematics system. This monitoring system keeps an eye on the overall health of the machine remotely and effectively can minimize any potential downtime.
Features include remote diagnostics that reduce service trips by capturing run hours and equipment data. Utilization tracking allows the operator to make decisions based on actual equipment use, and schedules maintenance. This saves time, parts and money by avoiding unnecessary maintenance. In addition, TFM minimizes cost using the precision to identify the problem as soon as it starts.
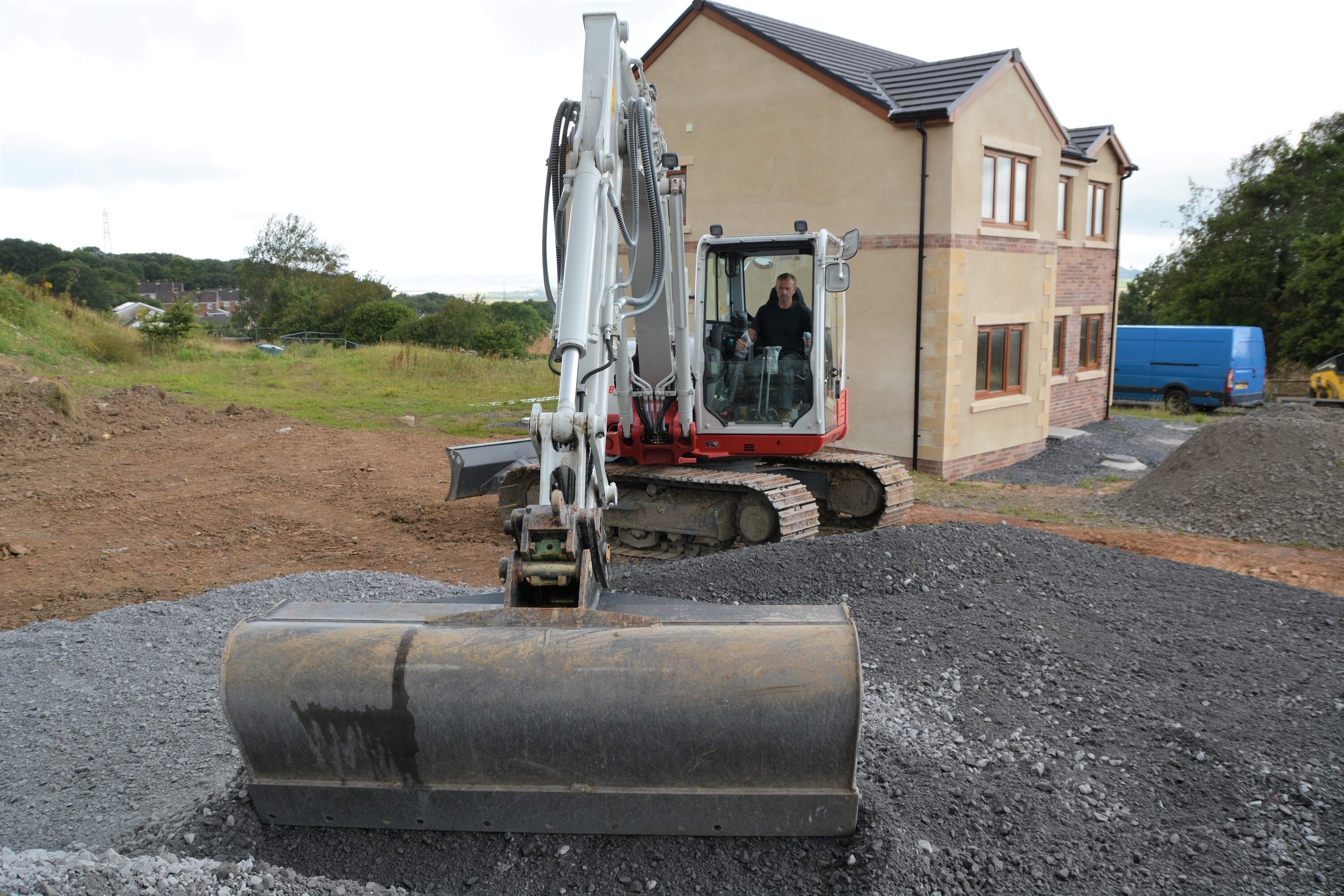
Mark invited me to try out the new Takeuchi for which I needed no encouragement! What can I say that hasn’t already been written about these Japanese excavators? The Takeuchi’s have always been smooth, but this example is even better, no matter how many services you choose to use there never seems to be any drag of power at all, just incredible and a real credit to the design team behind these machines, my opinion was echoed by Mark who said, “It’s just an incredible piece of kit and a real dream to operate”.
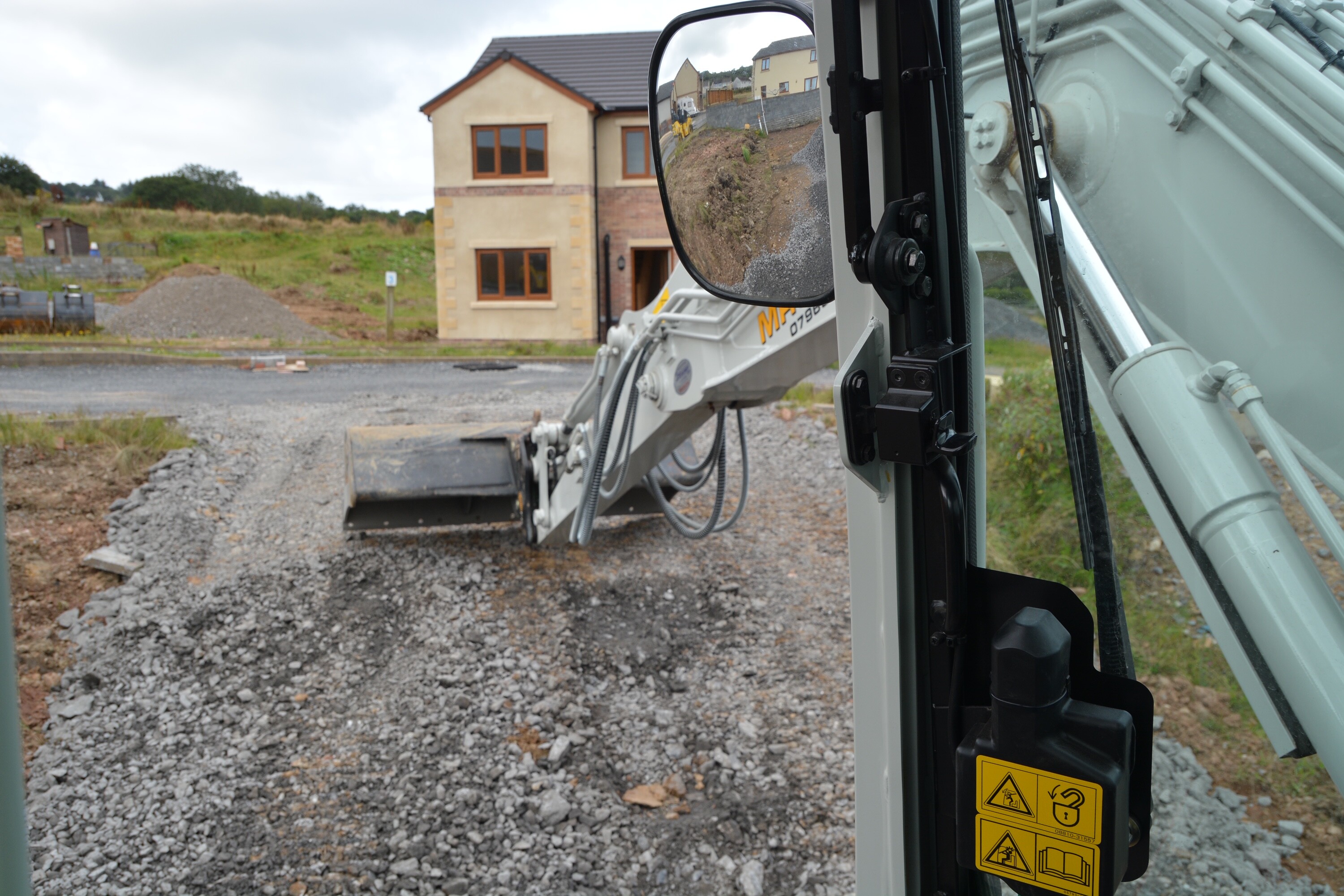
But its not just the machine that Mark was impressed with the dealer is very important too, “JDS Machinery are just so helpful in everyway I cannot fault them, I think it’s the fact that they are a family run business and know what its like for us as customers, they are always willing to go the extra mile for us, whereas some dealers who are just franchisee’s don’t really care about the small man with one or two machines and that’s really what makes the difference” concluded Mark.