by Nick Drew | Wed 20 Nov 2019
SANY: A Red Dragon Rising
Taking a look back at another of my articles previously published in Earthmovers Magazine bringing it to life on the internet, unedited and with alternative photos and video footage.
There can be no doubting the ambitions of giant Chinese construction machinery manufacturer Sany Group. Some of the statistics behind this company are truly amazing and serve to show that they are serious contenders on the global stage.
Sany have established 25 what they call manufacturing bases globally, six of these factories are in some of the largest cities in China including Beijing, Changsha, Shanghai, Shenyang, Kunshan and Urumchi. Since 2006 the company has established research and development centres and manufacturing facilities in the USA, India, Brazil and also in Germany to serve the European market.
These facilities are not some post war converted warehouses as we might imagine, but state of the art factories that use Toyota style production principals and have only been built in the last 8 years, each facility being able to produce 20,000 + excavators per year.
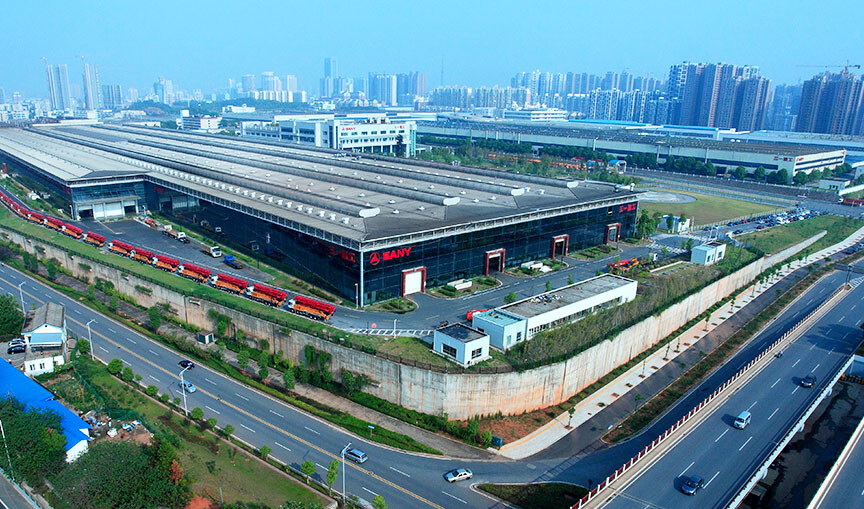
Incredibly in 2018 the company produced a record breaking 44,000 excavators of which 8% were exported and depending who you talk to so far this year, a new excavator is rolling of the production lines every 7 or 14 minutes in China only. It is predicted that this year 2019, Sany will exceed 50,000 units when including the output of their factories in the US and India.
The company is one of the top 2 exporters of construction equipment out of China, the other being Caterpillar. It may surprise many, but Sany have been the number one brand in China since 2011 ahead of the others in the top 5 including Caterpillar, Komatsu, Hitachi and Kobelco respectively.
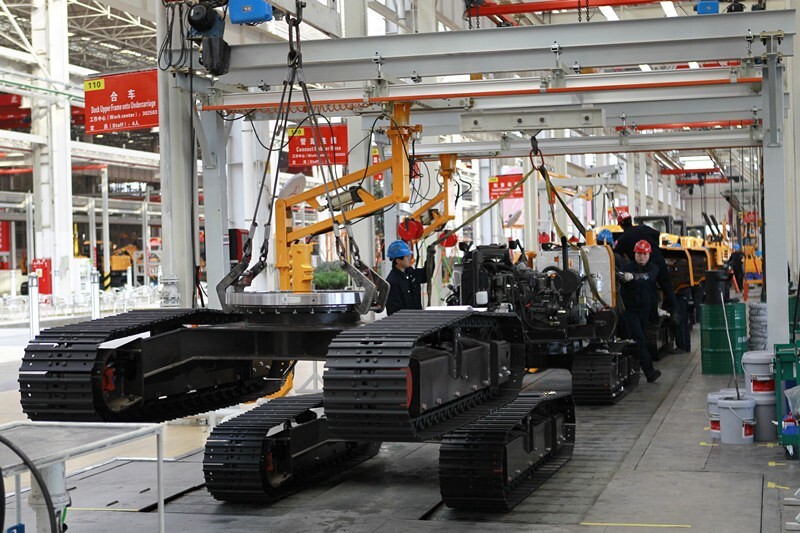
Exporting to over 150 countries Sany builds excavators from 1.6 tonnes up to 95 tonnes for its domestic market and currently in Europe 1.6 tonne to 50 tonne models are available. The company is aiming for 5% market share in Europe by 2025 which would equate to around 6,000 units.
Sany have been regular attendees at Bauma in Munich and China for many years now and at the 2019 event they had a number of new hydraulic excavators aimed at the European market to show off, among them was a new 8-tonne class compact radius model the SY80U and the larger SY155U which when fitted with the dozer blade tips the scales at 16-tonnes.
According to TDL Equipment Ltd’s Dealer Principal Andrew Taylor both these machines are not expected to be available in the UK until the first quarter of 2020, however TDL have had a pre-production field follow model of the SY155U doing the rounds with selected customers for an evaluation period, so they could offer their feedback for the Chinese design team and while the machine was back in TDL’s yard in Tankersley, South Yorkshire, Earthmovers were given exclusive access to this machine for a First Drive.
Walkaround
Its often said that the Sany kit does look a bit dated in styling, or at least similar in looks to some other manufacturers older models, but you would have to say that they are definitely listening to customers and are now working on putting together kit with a much more modern look to them, this 15-tonner is a prime example of that as from the outside it looks as current as most other machines on the market today.
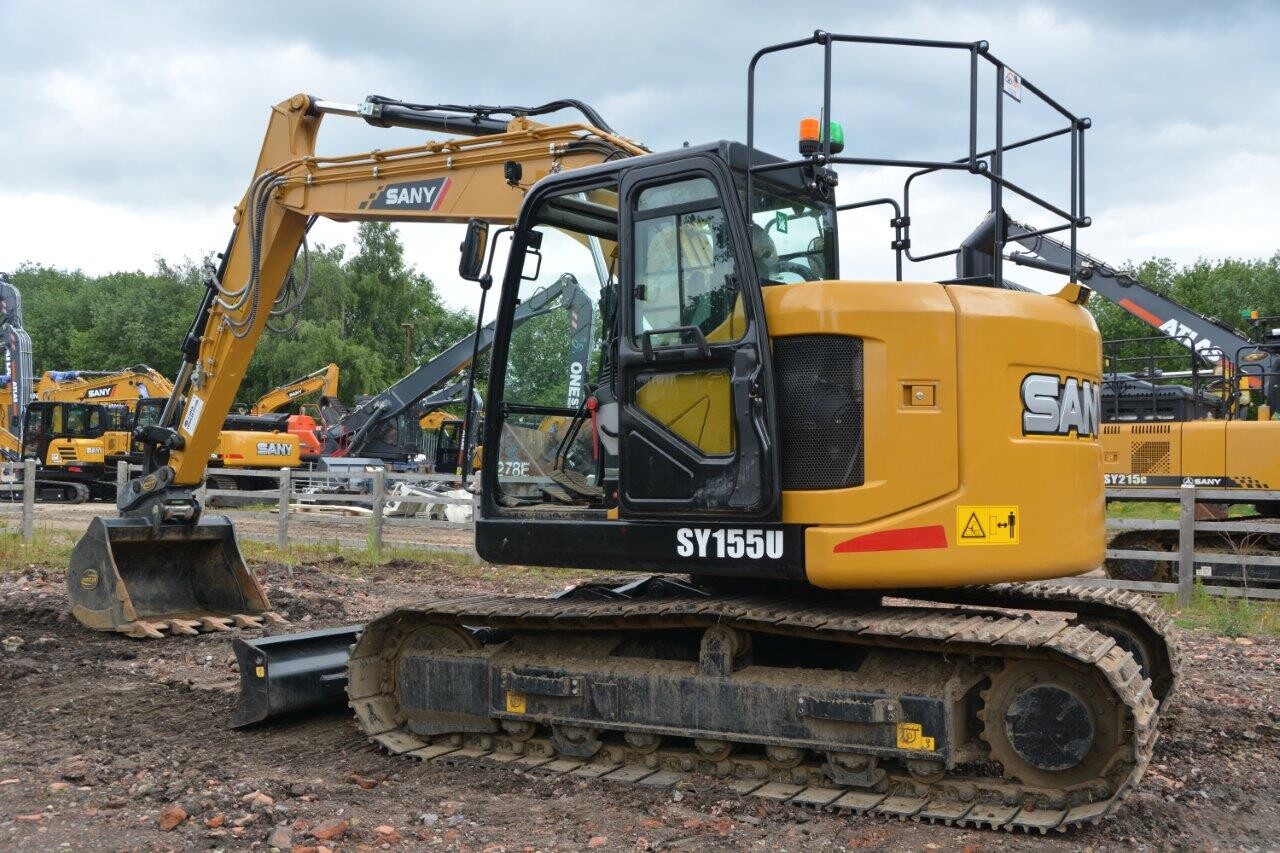
Walking around the machine I quickly discover that although this machine is built in China, it features a whole host of blue-chip components from major Japanese and Korean manufacturers. On either side of the sleek rounded counterweight there are curved panel doors. On the nearside it’s the usual fare of cooling packs, batteries, air filter and a small screen wash bottle. While on the offside we discover the latest KPM Kawasaki positive flow system hydraulic pumps, oil and fuel filters are also found here as is the suction pipe for the electric refuelling pump which is a standard fitment.
At the offside front another large panel door opens outwards to give access to the hydraulic valve block and this is also home to the AdBlue tank. Four steps are provided with a decent sized hand rail to give access up to the engine bay, as I passed by on my way up, I also spot that the slew motor and reduction gearing is another well-proven Japanese component from Kawasaki.
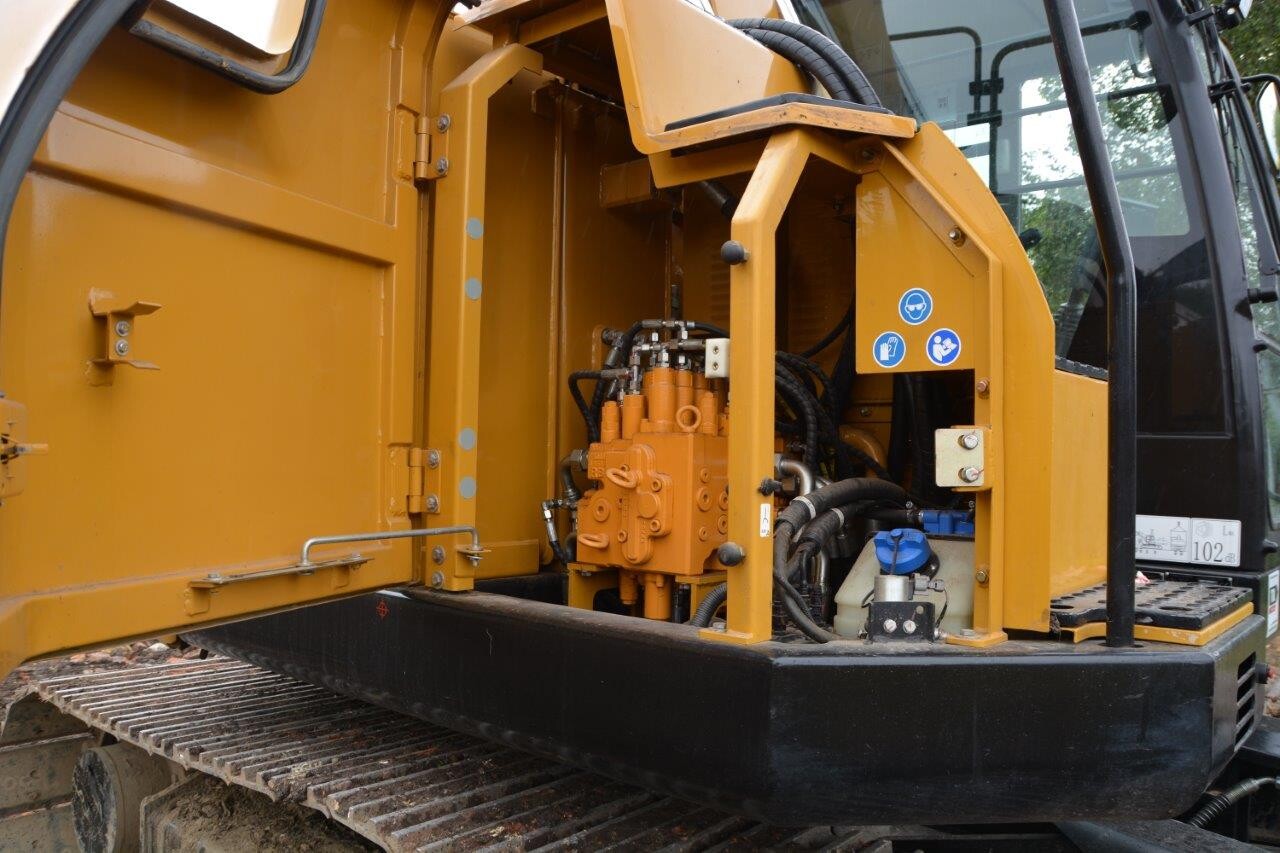
On ascending to the top of the machine I am surrounded by all-around boxing ring fall from height protection which has been retro-fitted by the dealer to meet UK requirements on sites. Raising the engine bay hood, we find more Japanese components in the form of the well-proven 4-cylinder Isuzu 4JJ-FT4 diesel engine which is Tier 4 Final/Stage IV emissions compliant and offers a power output rating of 78.5kw @2000rpm.
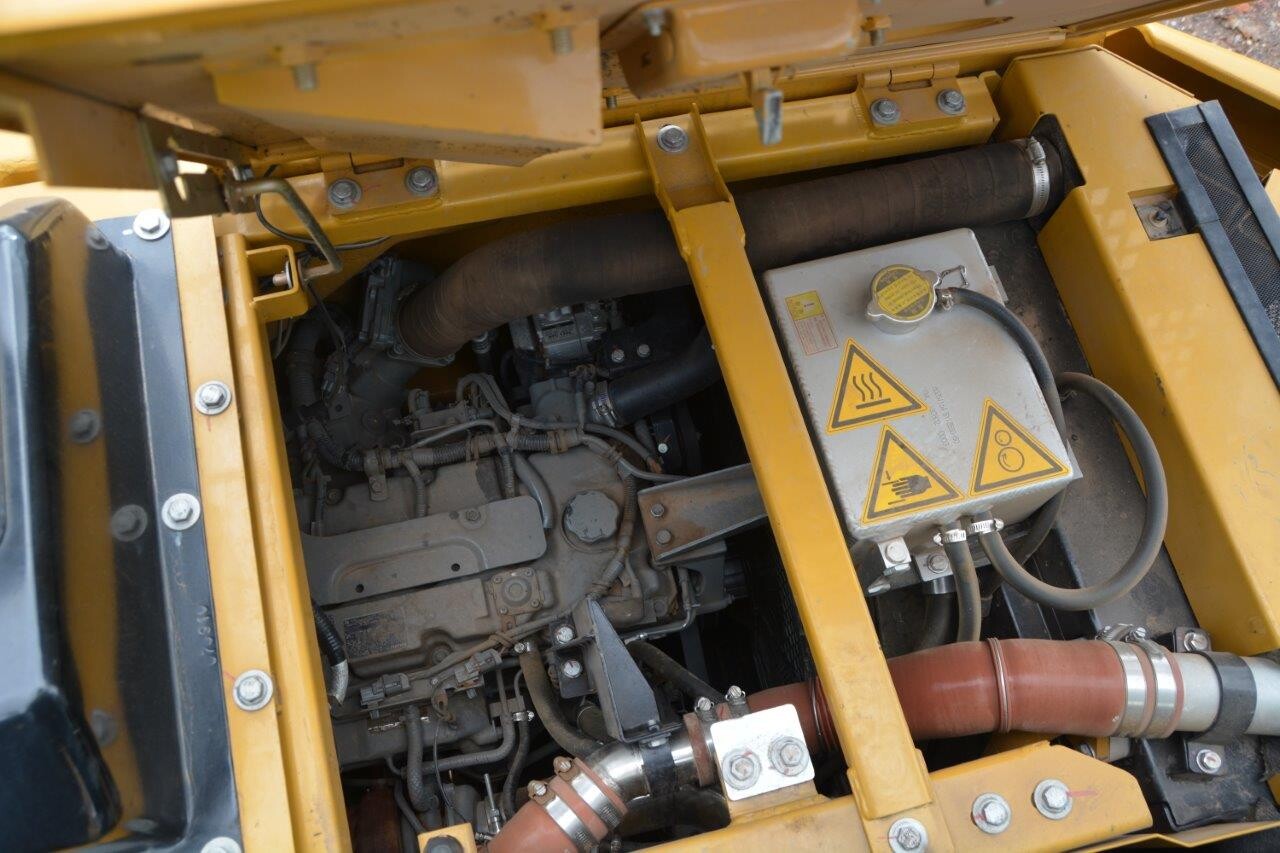
Back down at ground level and checking out the undercarriage which is a decent length at 3,665mm. This machine in UK spec was sitting on 700mm triple grouser pads and has 7 x bottom rollers and 1 x top roller, on that length of track I would prefer to see 2 top rollers personally, to help prevent track sag as it’s a lot of weight on a single roller, maybe that will be a change when the machine goes into full production. The track motors are South Korean in origin made by Doosan.
Climbing into the ROPS and FOPS approved cab and my first impressions were that it reminded me of a Dash-7 Komatsu interior, nothing wrong with that of course but it is clear to see where the Chinese have got their inspiration from. A plastic interior of two-tone grey is pleasant enough and its nice to see that they are moving away from the cheap looking fake wood trim style plastic that we saw on some of the early entrants into the UK market.
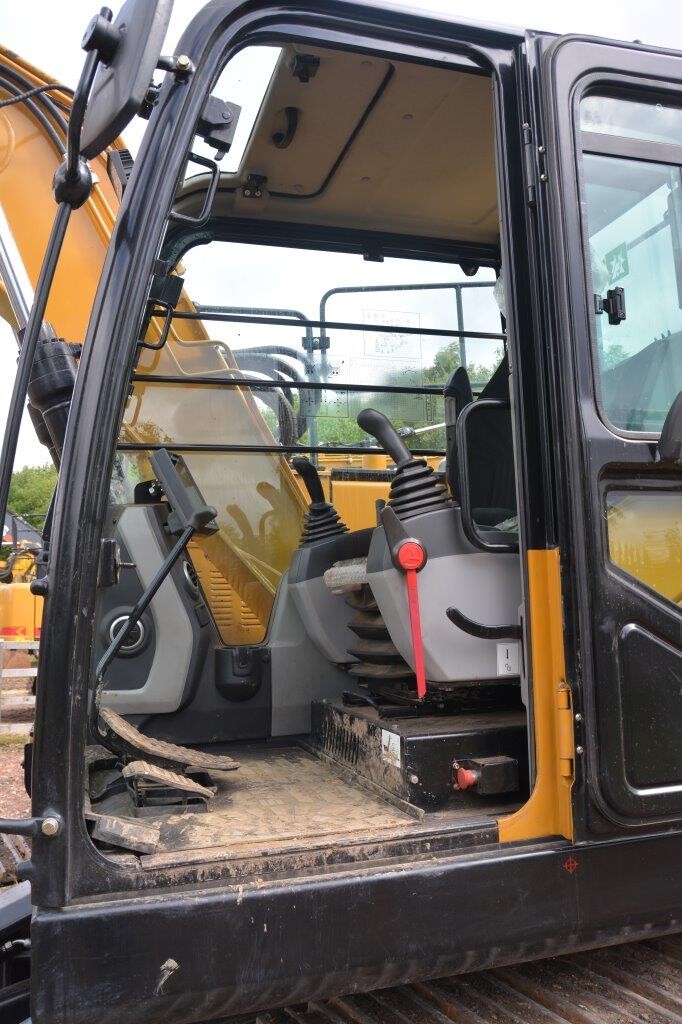
A fully adjustable heated air suspension seat is the standard fitment which I believe is made by Grammer and which I found to be very comfortable to spend time in. I would say no matter if you are tall, short or of medium size build you would be able to find a good operating position in this cab no problem, however, if you want to take your dinner bag with you into the cab, you might have to think again as there is next to no space at the rear of the cab to store such items, so often a compromise on compact radius machines. An extension to the top half of the cab out towards the back would cure this issue, but I’m yet to see a manufacturer do such a radical thing!
Sitting back in the seat and to the operators left on the joystick console we have the DENSO style heat and air conditioning control pad, this will be very familiar to any operator who has been operating excavators for at least the last two decades, as they have changed very little over the years.
To the operators right, just behind the 12v electrical socket, there is a cluster of no less than 16 push buttons for selecting various functions including start/stop, flashing beacon, working lights, auto idle, travel speeds and overload alarm, elsewhere and on the joystick console itself we have the ignition key, throttle dial, a pair of rocker switches for the wipers and screen wash, and the dozer blade control lever. A Sany
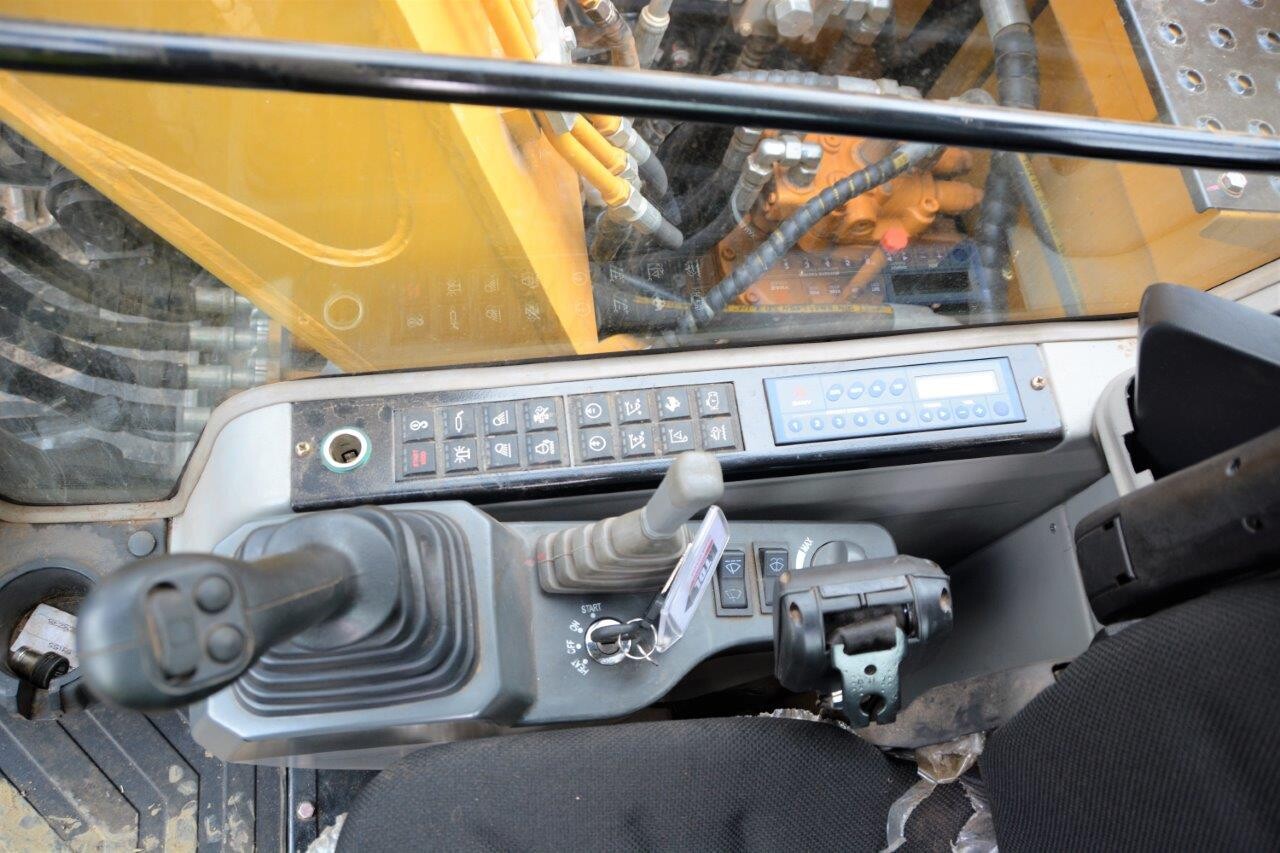
The front screen is a two way split affair with storage in the roof for the top half, talking of the roof, there is a sunroof which can be opened if needed, one thing I did not like about that is the small strip of glass that is fitted, there is no blind to cover it so on sunny mornings you would be battling to see, or reaching for the baseball cap, I cannot see any benefit from having that glass there, if you needed to see up that high it would just be logical to pop open the sunroof, hopefully that will be addressed in the full production model.
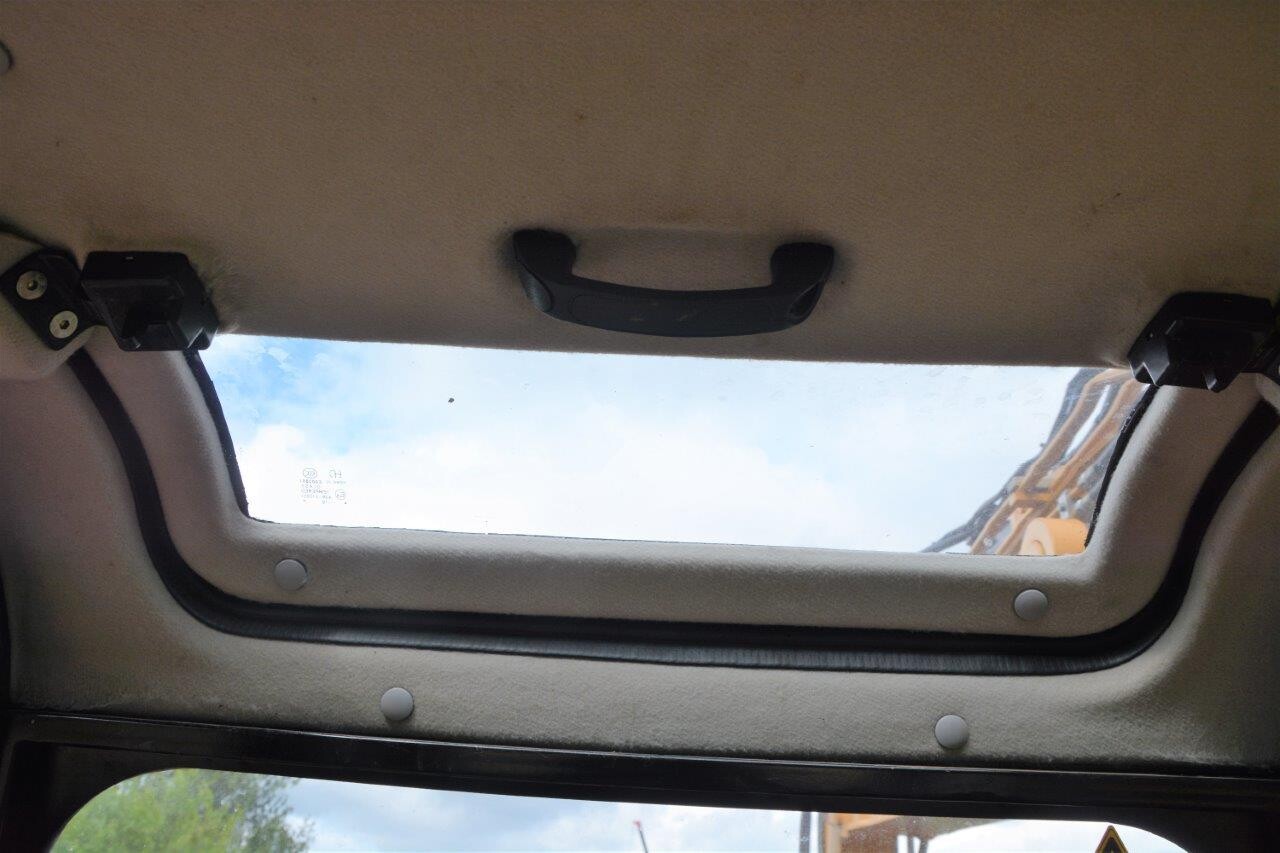
A full colour multi-language display screen provides the feedback to the operator on all the usual stuff, fluid levels and temperatures and doubles up as the rear-view camera. By accessing the menu’s, the operator can make adjustments to the hydraulic flows for when using specific attachments, various work modes are also available to suit the task in hand, or if you are old school like me, just crank it right up!
As for the controls track levers are provide with really decent sized track pedals and there are foot rests on either side of the pedals for operator comfort, the joysticks are according to TDL from KPM Kawasaki and feature multi-function control buttons for proportional operation of the hammer and shear lines and for the rotational line all of which comes as standard.
Standard boom size is 4,600mm while the options on the dipper arm are pretty standard of either 2.5m or the preferred UK spec 3.0m, however for those now opting to fit a tiltrotator experience has proven that the 2.5m option is best suited. This example was fitted with the standard 2.5m dipper and a Strickland fully automatic quick coupler and bucket.
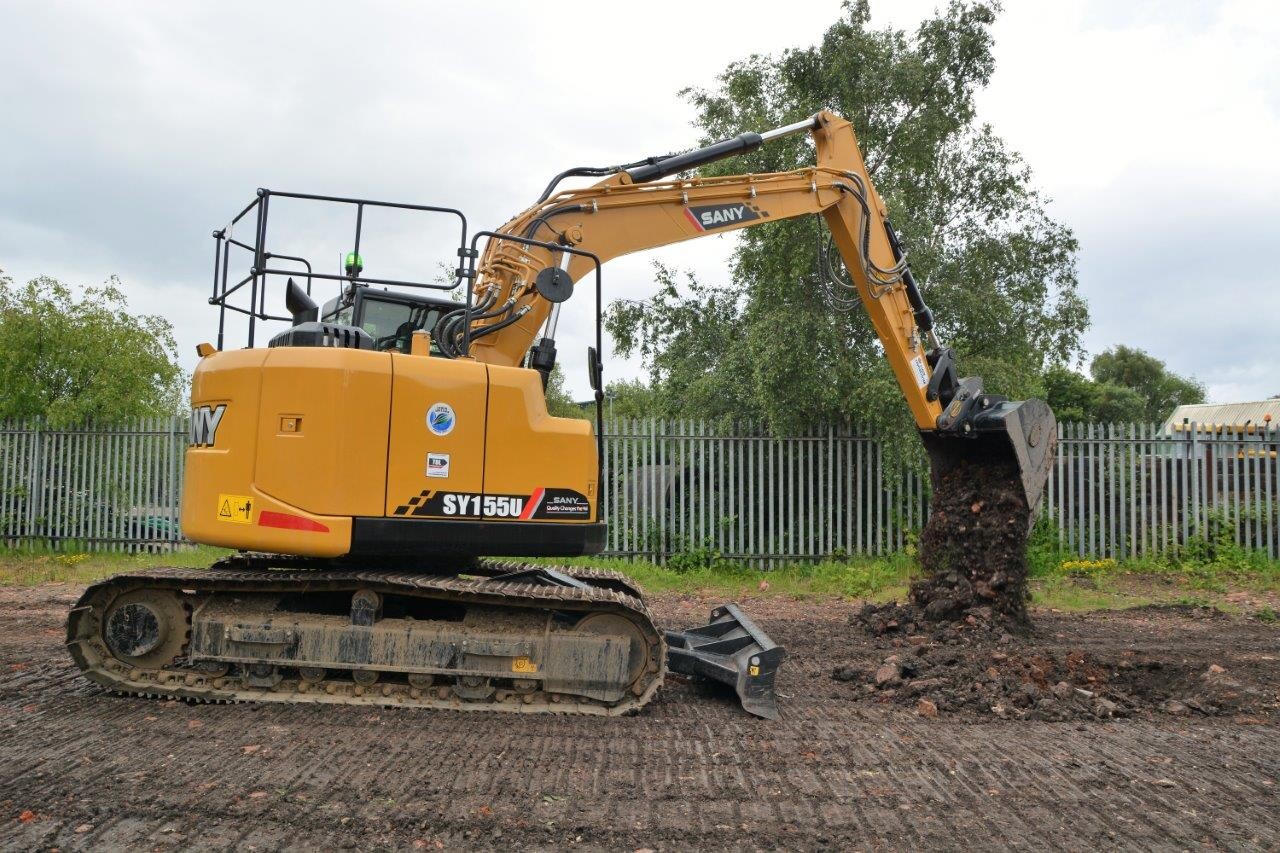
The machine looked pretty good and everything you could need from a modern-day excavator was in there, but how would it perform. Without further ado, I jumped back in the seat got comfy, turned the ignition and pressed the start button. I was warned this pre-production model was a bit noisy in the cab and I have to say they weren’t wrong, however, that is what field follow machines are for, finding out niggly faults in a real-life working scenario and I’m confident that will be addressed on the full production model.
This machine had previously been out with customers during which time it had amassed 192 hours on the meter and apart from the in-cab noise issue, feedback had been extremely positive. I was pleasantly surprised by the machine’s smoothness on the controls and feedback through the levers was good.
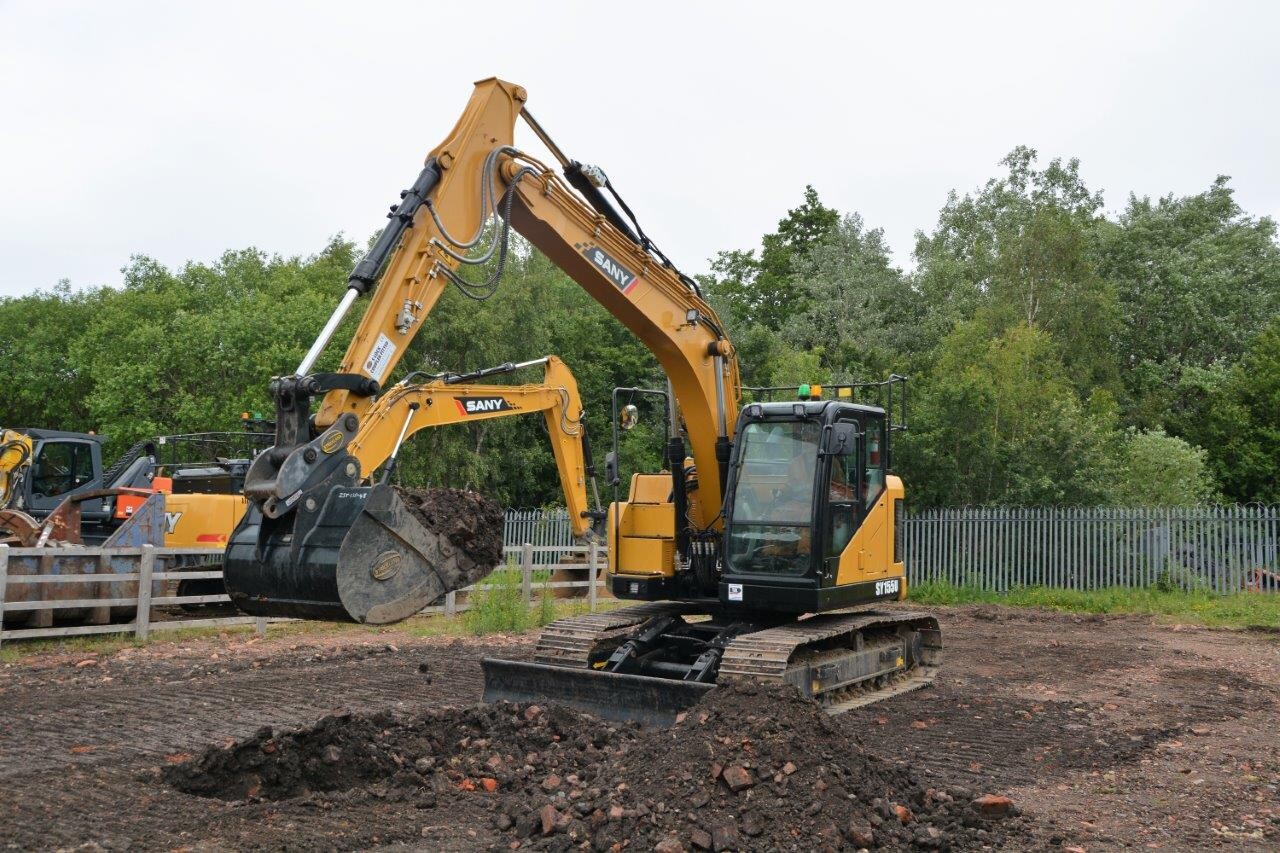
With a big 48” bulk digging bucket on the machine had plenty of grunt in the dig on the TDL demonstration plot which was largely made up of demolition rubble and soil which is never the easiest of combinations to dig in, to the front and rear the machine remains very well balanced, but over the side with a full bucket, as is often the case with compact radius machines, she could easily become unsettled, so a bit more weight on the back end could be beneficial on the finished product.
Grading ability is always the ultimate test for any machine and I was delighted to see that it was not a problem for the SY155U, even at full stretch there was no “dip” on the initial pulling in of the dipper arm while raising the boom a great advert for the use of top quality Japanese hydraulic components. It would be really good to spend a few days on site with one of these to get the full measure of it, but from the time I spent on the Sany, I have to say it impressed me and surprised me in equal measure, of course the old question remains what will the residual values be like when it’s time to trade in, but when we look back, the same used to be said of the Korean brands like Daewoo, (now Doosan) and Hyundai and look where they are now.
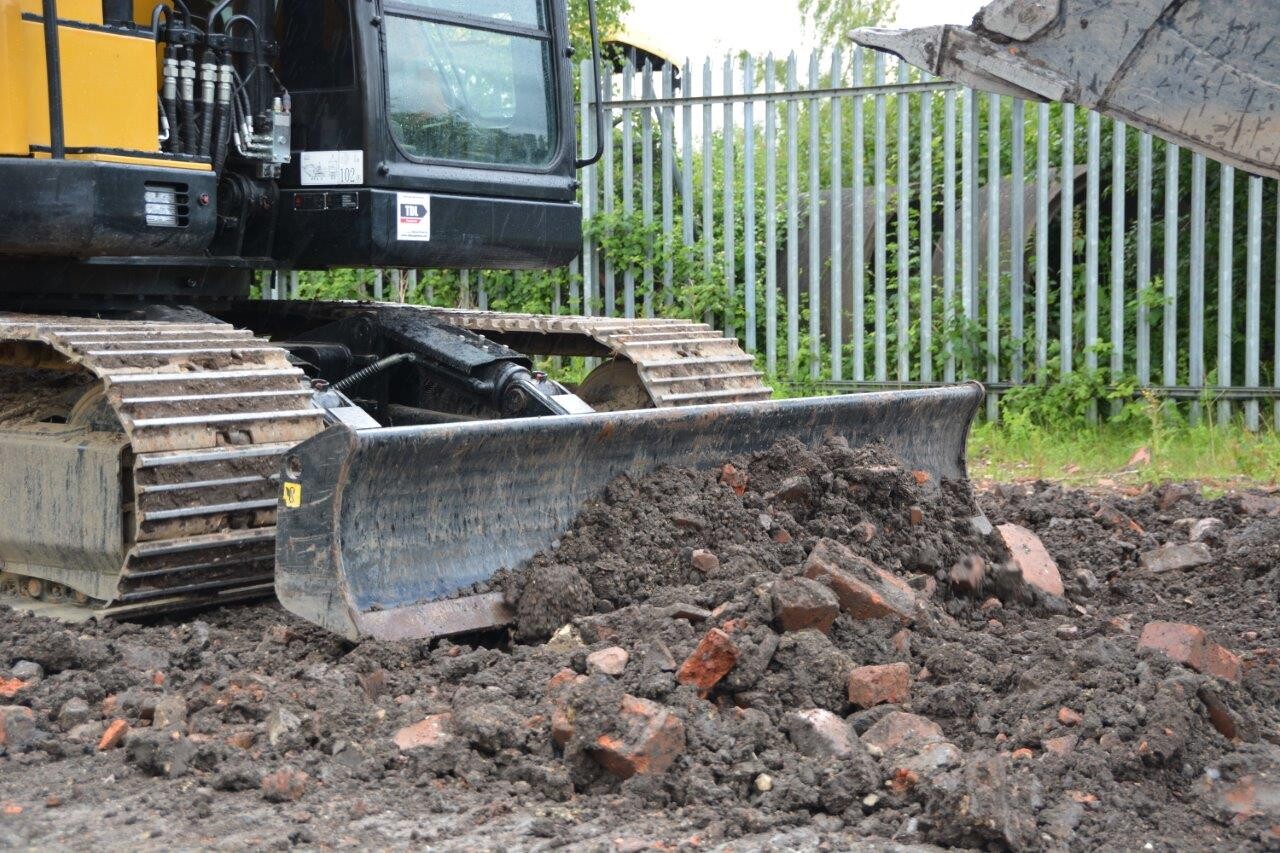
For big fleet users it makes perfect sense, buy a batch of these type of machines run them for 3 years, then chop them all in for a like for like order and away you go again. The hardest part is convincing operators who would prefer to be sat in a big brand named machine and that will always be the case.
With Sany offering a 10,000hr/5-year warranty on booms, stick and chassis as a mark of confidence in their products these machines are going to appeal to the owners, accountants and the hire desks, after all you’ll get the same rate for your excavator no matter what name is on the boom.
There is no doubt in my mind that these Chinese manufacturers are on the up in terms of design and quality and what we are seeing from them now is only the beginning.