by Nick Drew | Fri 08 Mar 2024
Sunward On the Up
A #FlashbackFriday post with look back at one of my articles on Sunward Europe, which featured in Earthmovers towards the end of last year, unedited and with alternative photos and video footage.
In the wider scheme of things Chinese manufacturer Sunward is still a relatively young company, having been founded in Changsha, China in 1999 by professor HE Qinghua.
The company’s expansion has been rapid and sustained, and the wide range of products now include, construction and earthmoving machinery, mobile access equipment, foundation machinery and even aviation component manufacturing, as we discovered during a recent visit to the Sunward Europe Heavy Industry facility in Tessenderlo, Belgium which was established in 2015.
The statistics make for interesting reading, with the company producing in excess of 200 + different products, exporting to over 100 countries with an estimated turnover of USD 1.2 billion, and offering full time employment to around 5,000 employees globally.
Manufacturing takes place at the Sunward Industrial Park in Changsha, China, at a state-of-the-art facility covering 120 hectares, roughly the size of 168 football pitches, a workshop area covering over 100,000m2 features the very latest in robot welding technology.
With professor Quingha’s background as an engineer, the company has invested heavily in research and development facilities and has created 20 R&D test centres, these facilities employ 400 staff alone. The company states that it holds 800 patents and has won 7 awards for innovation and science.
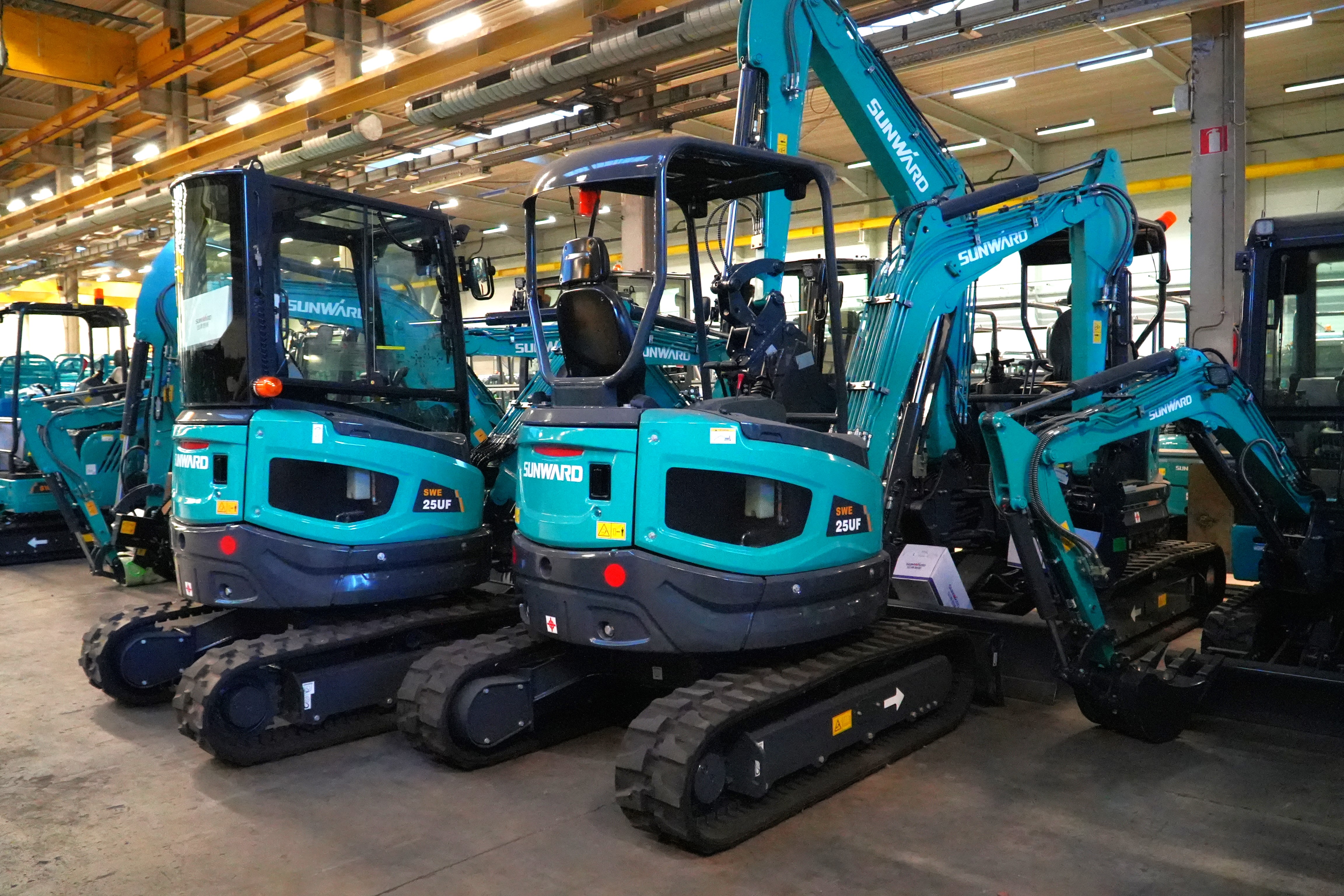
The European operation, which also covers Israel and North Africa, is headed by the highly experienced CEO Arnaud Berthier, who has worked previously with Yanmar Compact Equipment. Arnaud has been with Sunward now for nearly 4 years and his experience of the European market is invaluable. He has been instrumental in forming a team to push the brand forward in Europe.
It’s fair to say that the brand had a bit of a faltering start in the UK, but with the appointment of highly experienced construction machinery man Rick Still as Country Manager, new and enthusiastic dealers have been signed up and interest in the products and sales are going extremely well.
The European hub moved to the Tessenderlo facility around two years ago, and while not on the scale of Changsha, is an impressive size for a distribution centre, covering some 25,000m2 of which 15,000m2 is under cover. Breaking down the stats, 6,500m2 is dedicated to machine stock storage, 2,600m2 to spare parts stock, and 3,000m2 of attachment stock storage, while an outside machine demo area covers 2,000m2.
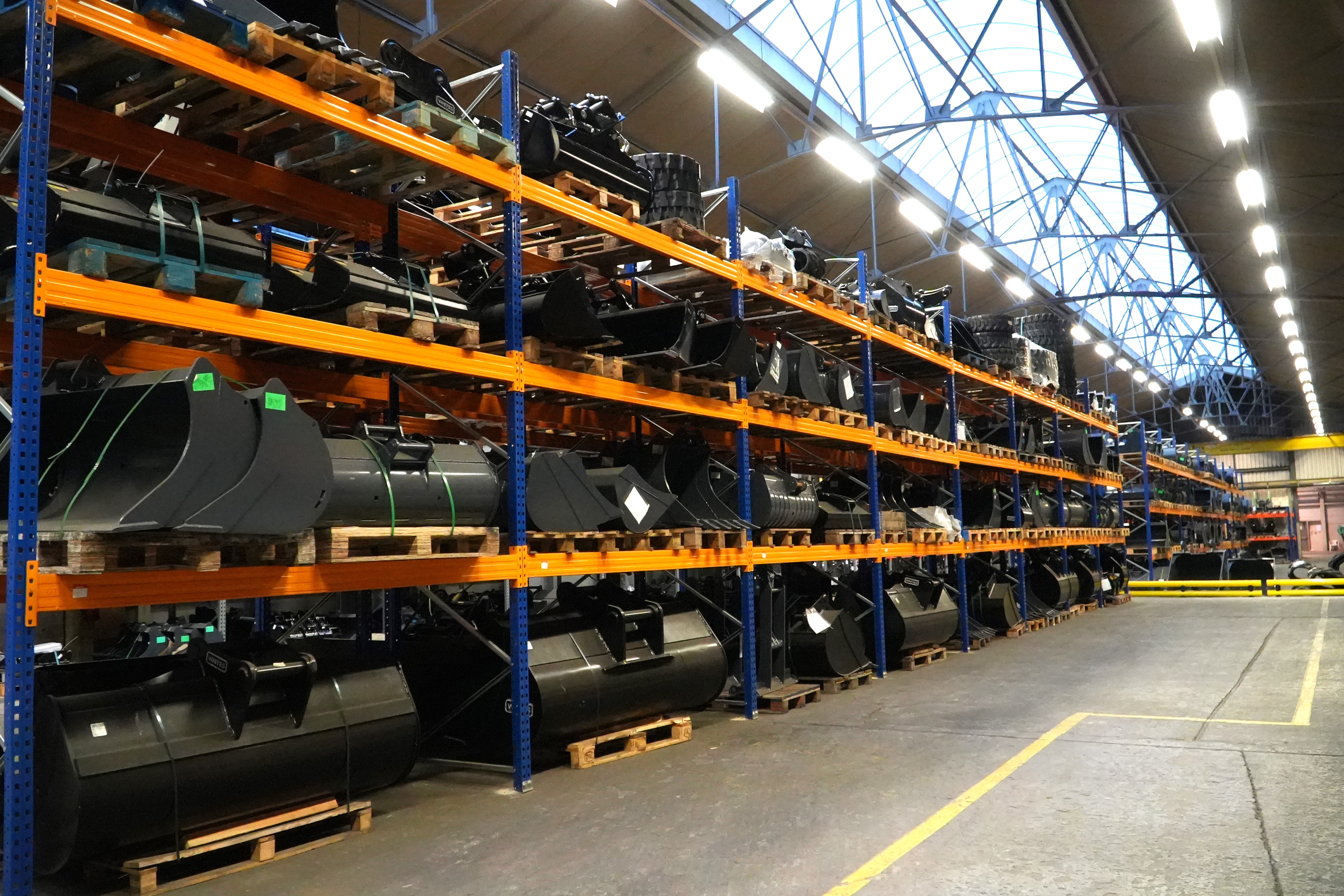
The company holds a massive stock of spares in Belgium and guarantees 95% of spare parts availability, with delivery to the customer within 24 hours of ordering. The machines arrive at Tessenderlo direct from China, and they are customised at this facility to meet the various regional requirements.
These customizations include, the fitment of safety check valves, fitting of hydraulic quick hitch pipe work (Europe and UK), installing lubrication systems, fitting premium seats, proportional joysticks, and various track set ups, including steel, steel with rubber pads, or full rubber tracks as specified by the receiving dealer’s customers. During our tour of the facility, we witnessed some of this customization being undertaken by Sunward’s own staff many of whom have come from China to work in the European hub.
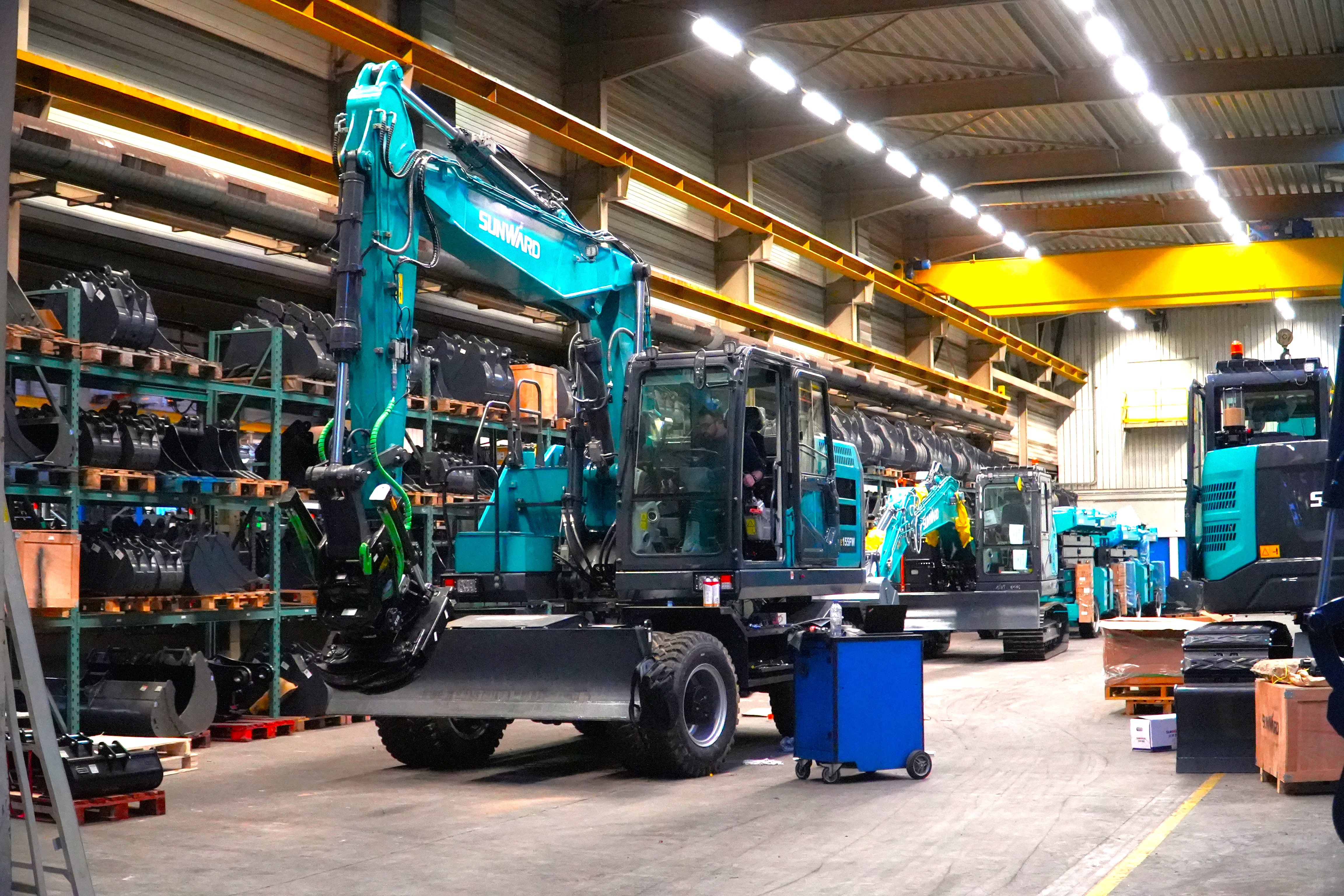
At the end of the quality control process, machines are cleaned and then thoroughly washed off in a purpose-built indoor wash bay in preparation for loading onto the transport. There was a constant stream of trucks at the loading bay area on the day of Earthmovers visit and we saw machines being loaded onto the transport via two loading ramps.
In the main indoor storage warehouse, we were greeted by a sea of blue mini excavators, both diesel powered, electric, and access platforms. However, there were some noticeable exceptions as we spotted a number of SWE 25UF 2.5-tonne zero tailswing models sporting orange paintwork, these machines are supplied to German brand Atlas, to be badged as AC 25UF models.
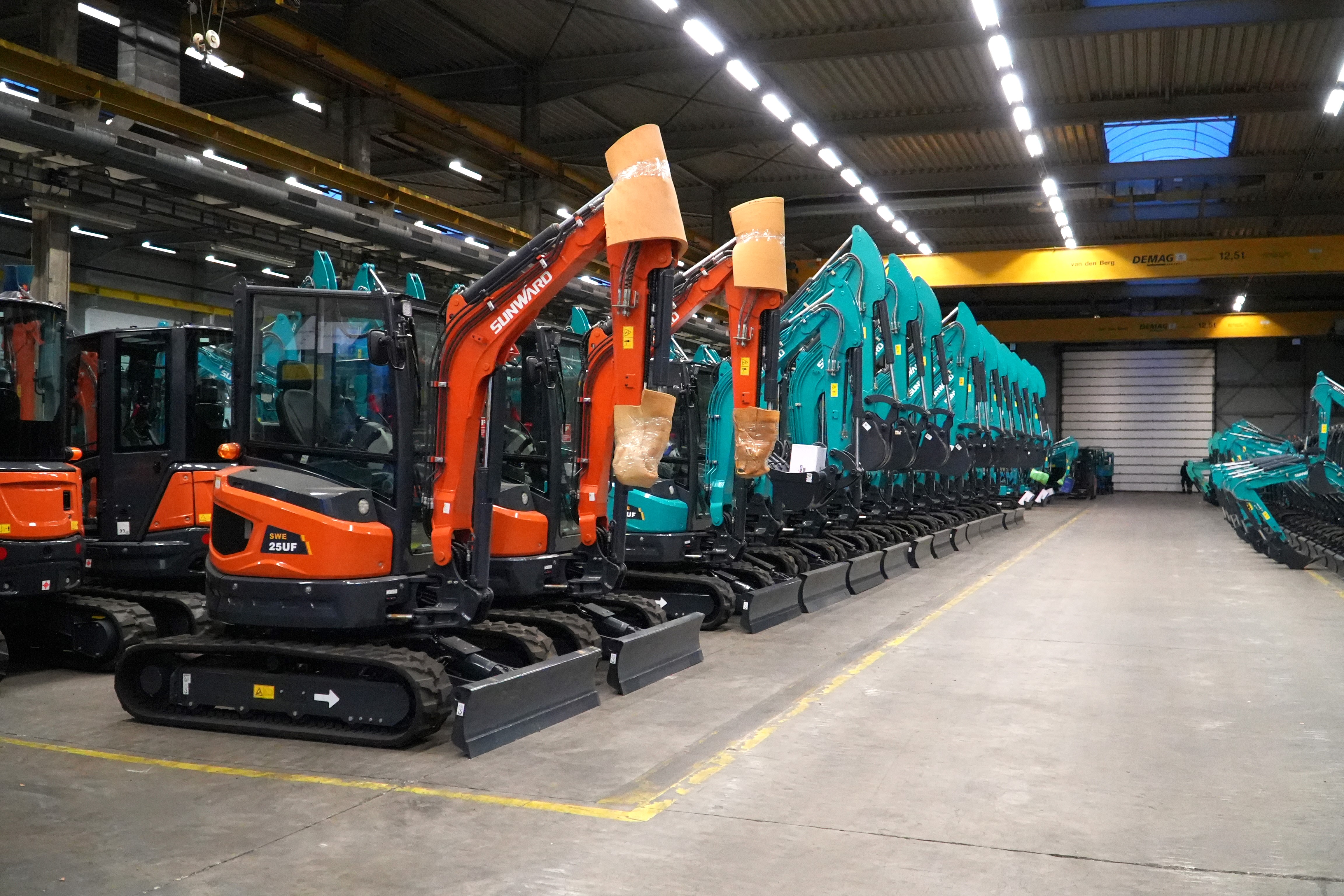
We were on a tight time schedule during this visit, so both myself and my German friend and industry colleague Dirk Bömer were keen to get out to the demo area for some much anticipated “stick time”.
A whole range of machines were set up to try out, but my primary goal was to spend time in the 16-17-tonne class SWE 155UF-2PB, which was shown for the first time in the UK during the Plantworx show last year, sporting a Steelwrist tiltrotator. This short tailswing machine with two-piece (TAB) boom really caught my eye at the show and I was keen to see how it performed.
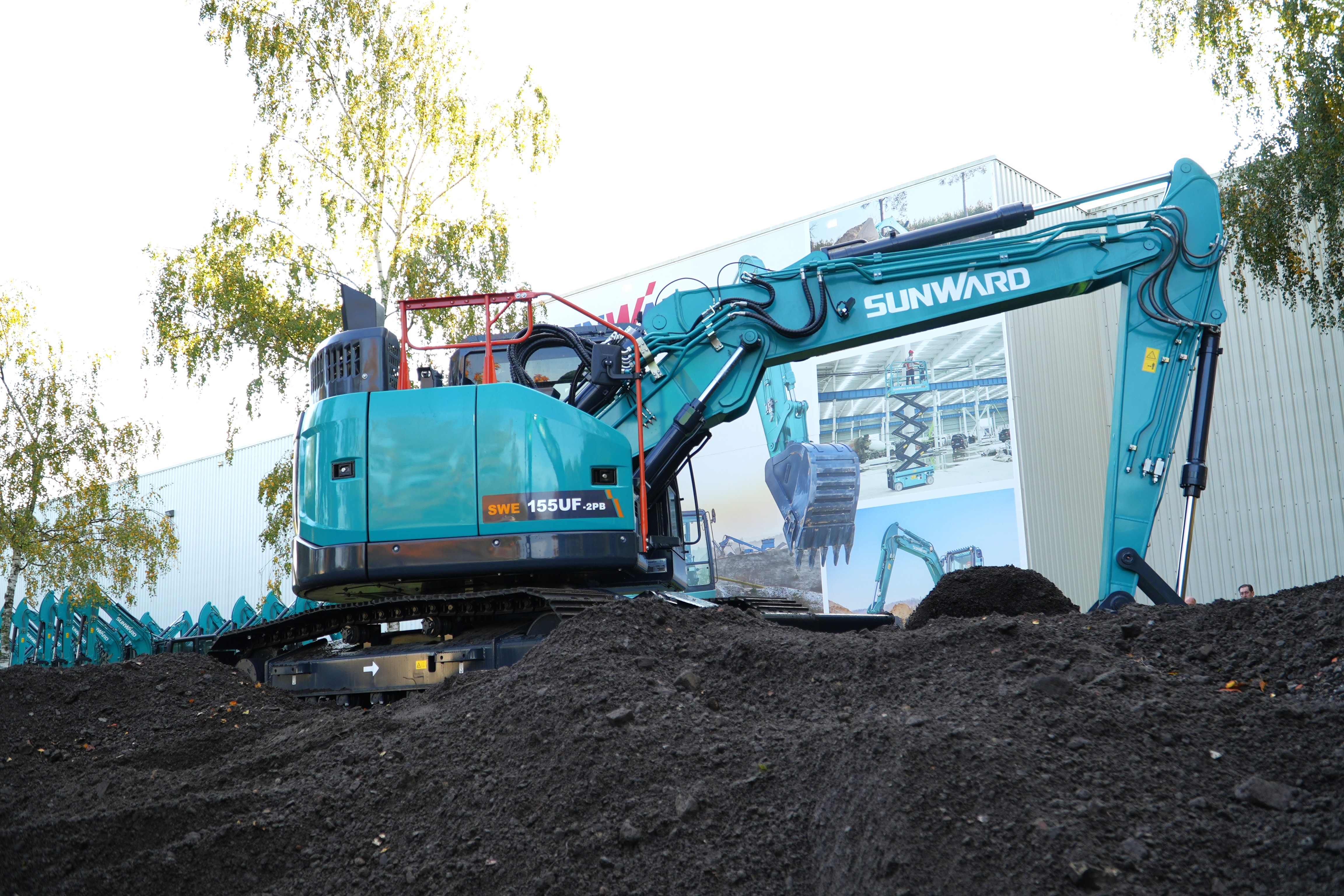
At first glance, its clear to see that this machine has been totally designed for the European market, with its compact design, dozer blade as standard and two-piece boom, making it an ideal choice for the urban jobsites we see across the European sector.
Popping the bonnet reveals the well-proven, ultra-low emission Stage V compliant, 4-cylinder, 4 stroke, turbo-charged, Cummins QSF3.8 diesel engine offering a power output rating of 90kw (124hp) @2200rpm.
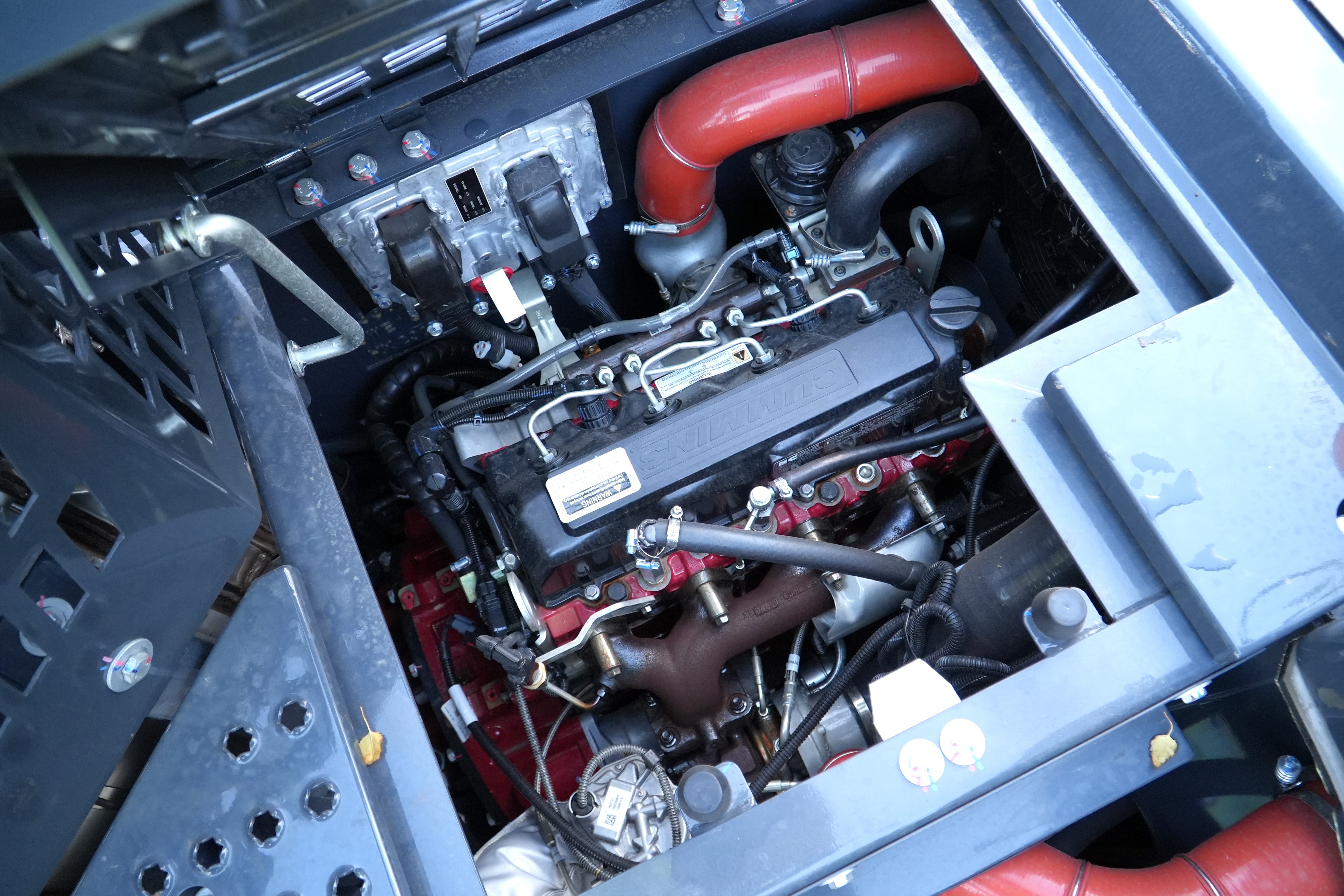
In common with other brands of compact radius machines, two curved rear corner panel doors are fitted, on the nearside we discover the cooling packs, air filter, windscreen washer bottle, batteries and the main battery isolation switch.
On the offside, it’s home to the variable piston hydraulic pump, in this instance from Hengli, regarded as the Chinese equivalent of Kawasaki. In front of that we have a nicely laid out array of fluid filters, which can be easily reached from ground level for routine servicing programmes.
To the front offside a large panel door opens up to reveal the main hydraulic control valve block, which is also manufactured by Hengli, this area is also home to the Add-Blue tank and the electric refuelling pump. I have to say I was very impressed with the quality of these panel doors, the retaining latches and the overall quality of the paintwork which looked very good.
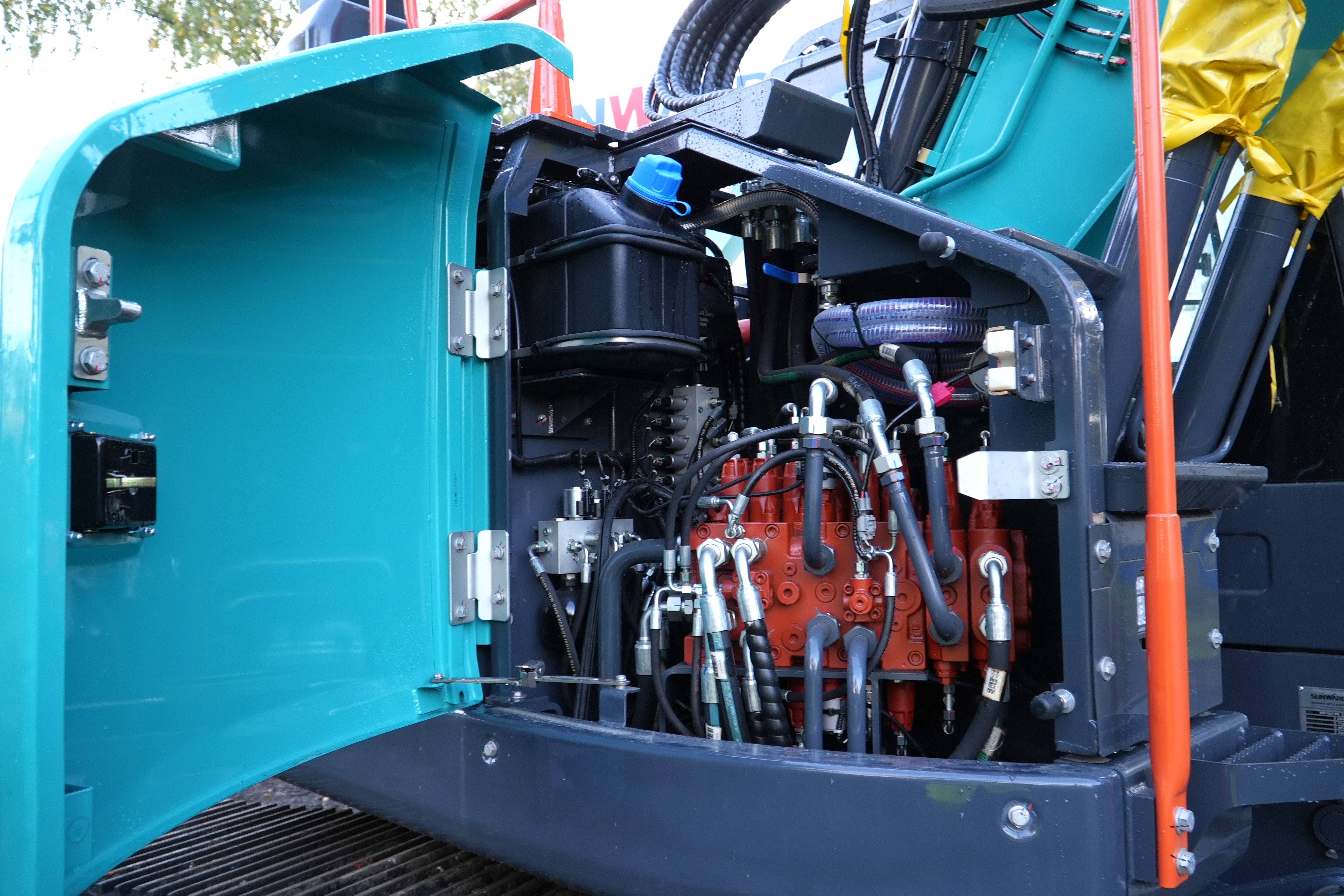
Sitting on the UK preferred 700mm wide track pads, the overall track length on the ground is 3,000mm, the undercarriage features seven lower rollers and two top carrier rollers, which I much prefer as it prevents upper track sag. Undercarriage width is 2,600mm and the full width dozer blade looks sturdy with good protection for the twin hydraulic rams to protect the rods from any overspill material. This example was sporting a 2.5m dipper arm and a direct mounted digging bucket.
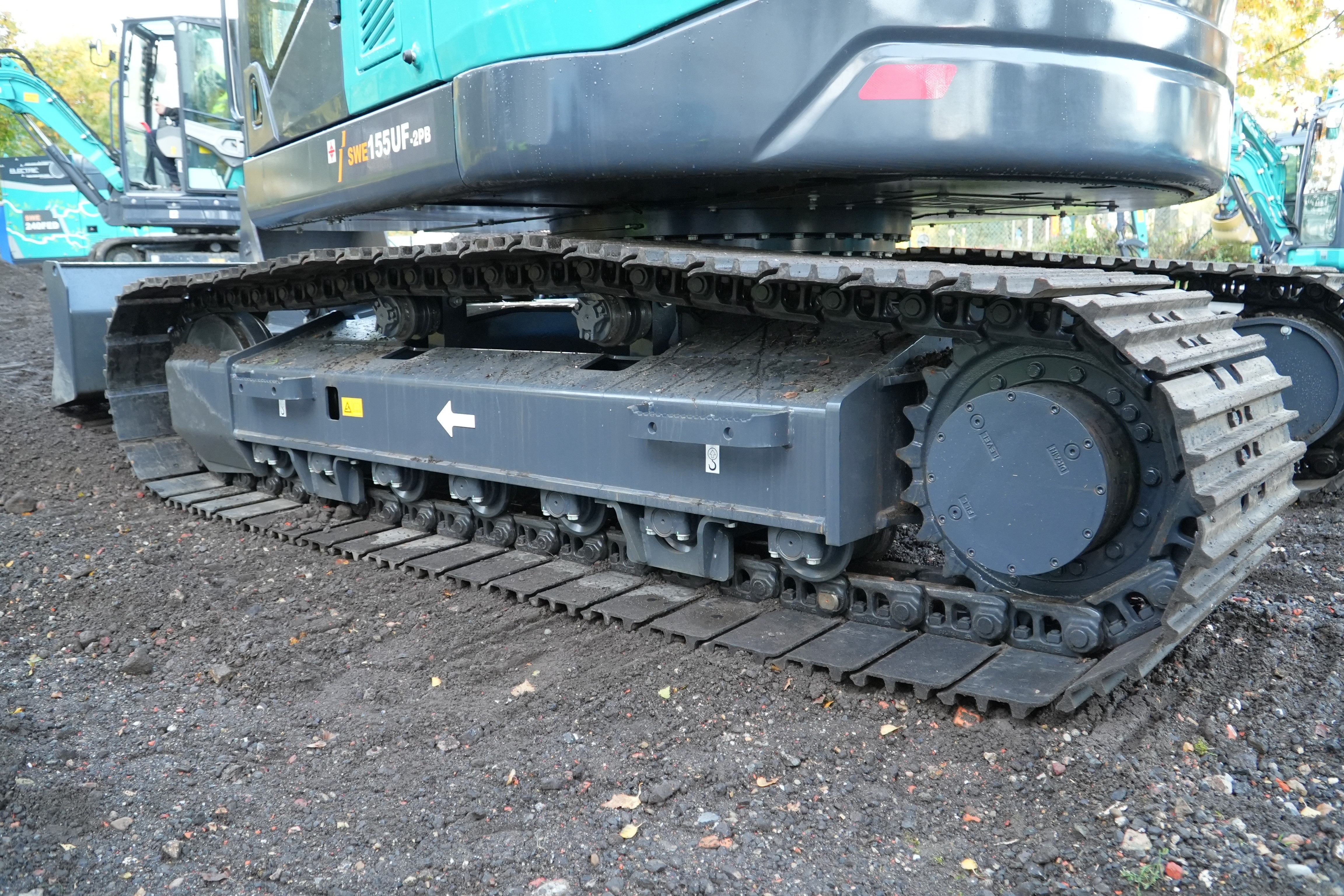
Up into the cab and I find the ever-popular Grammer manual suspension seat is provided, making it a comfy place to spend your days. Overall, the cabin is well appointed with all the standard features we have come to expect in a modern hydraulic excavator.
The light and dark grey plastic trim is of as good quality as you would find in the perceived premium brands, the only thing I found looked slightly cheap was a row of three warning lights consisting of red, amber and green below the main monitor on the front console.
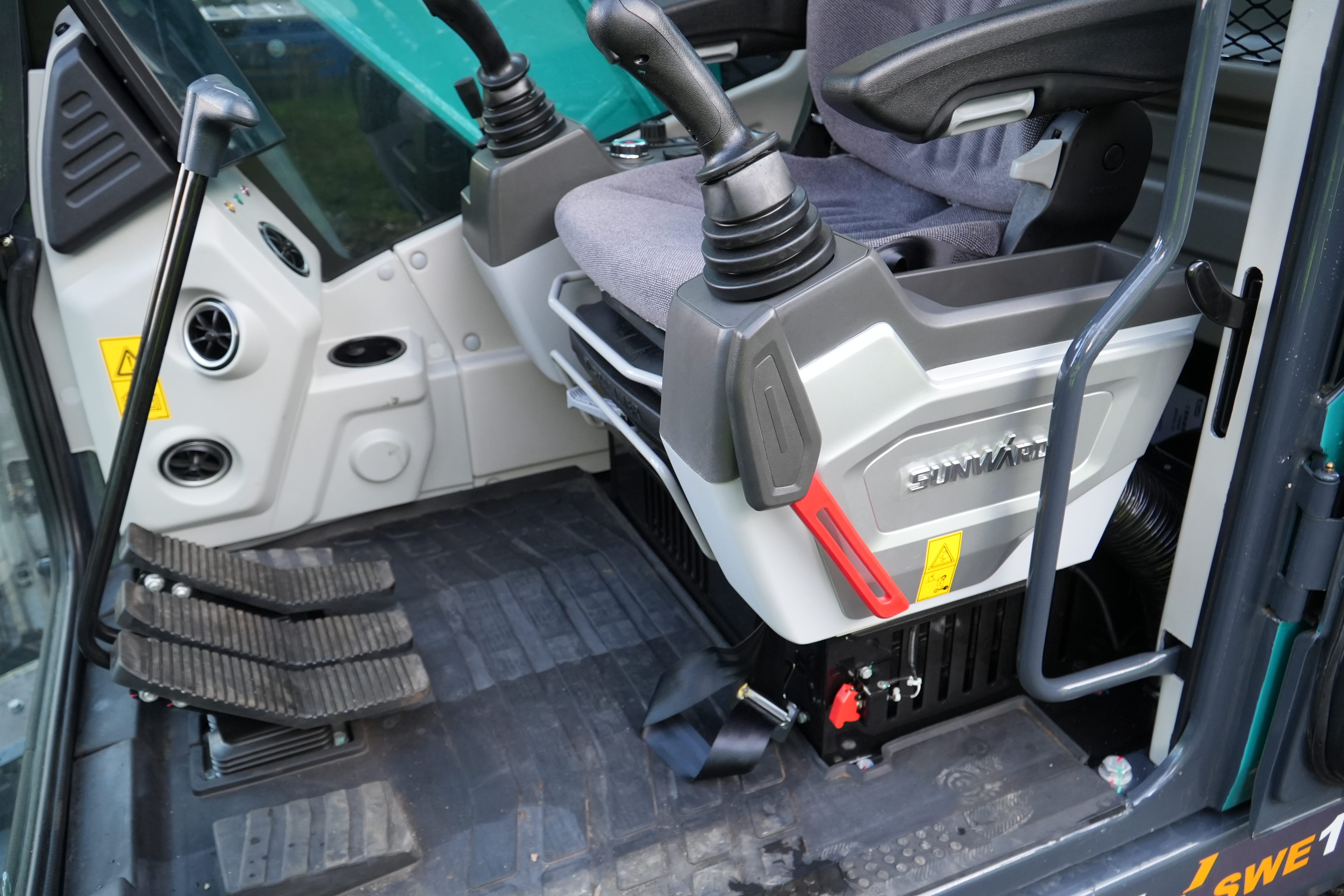
The large multi-functional touchscreen monitor/camera view screen, is as good as you will find in anything else, and can also be controlled by a jog dial on the right-hand side console.
Start-up is key-less via a rotary dial switch combined with a push button starter in the middle, with a rotary throttle dial situated to the right-hand side in front of a bank of 12 function switches, for such things as work lights, wiper and screen wash, auto idle, quick coupler and two speed tracking selection to name a few.
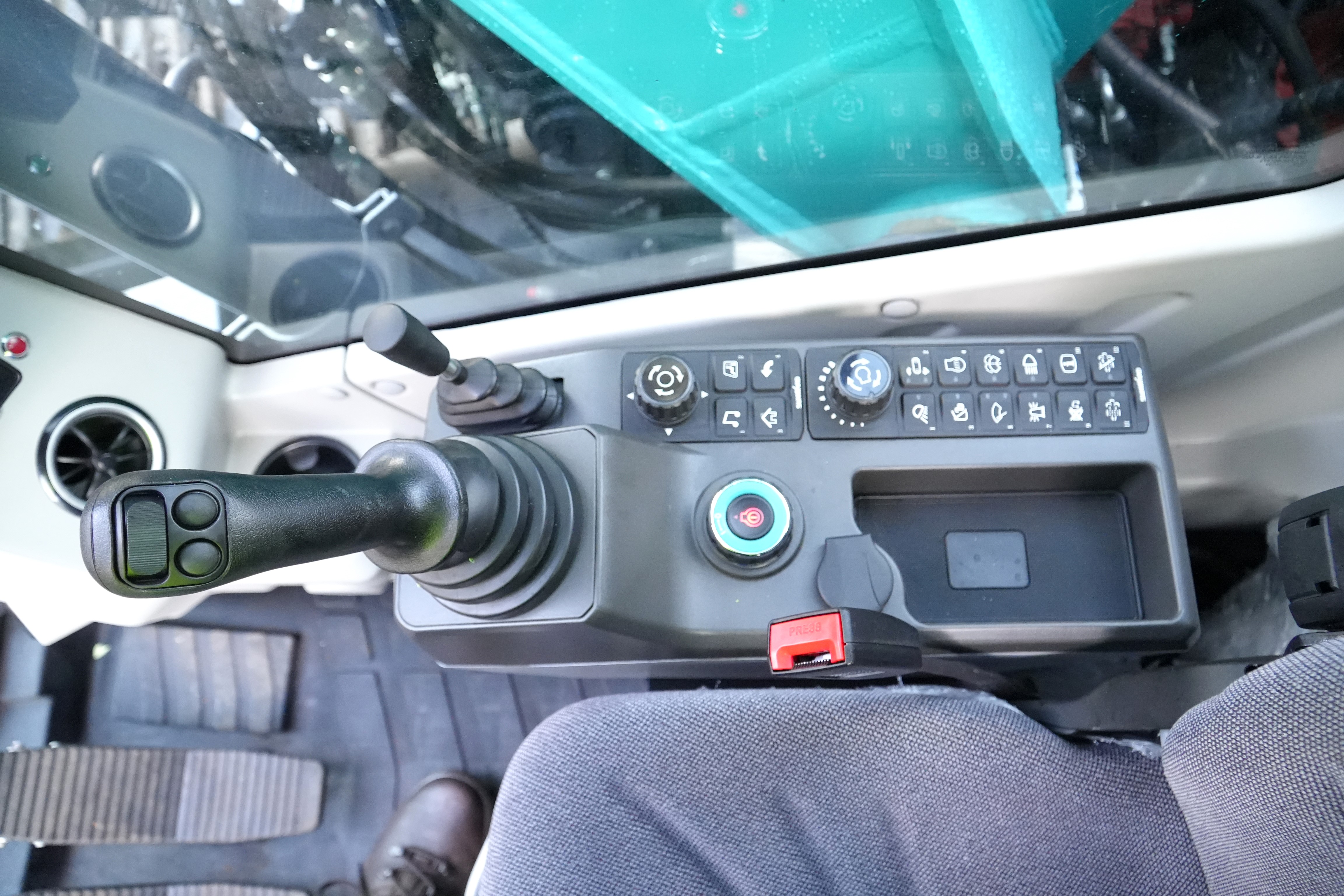
Nice T-Bar tracking levers are provided and some really decent sized track pedals are installed too. Just to the right of the track pedals is another equal sized pedal which is used to operate the extremely useful two-piece boom feature.
In the rear of the cab, there has been no compromise in space on this short radius model. A decent two-level parcel shelf is provided with some cargo netting on the front to retain items that are stored there during the working day, it’s the little things that count in an operator’s world, just like that other essential, the cup holder for that all-important morning brew, mounted to the front right-hand side.
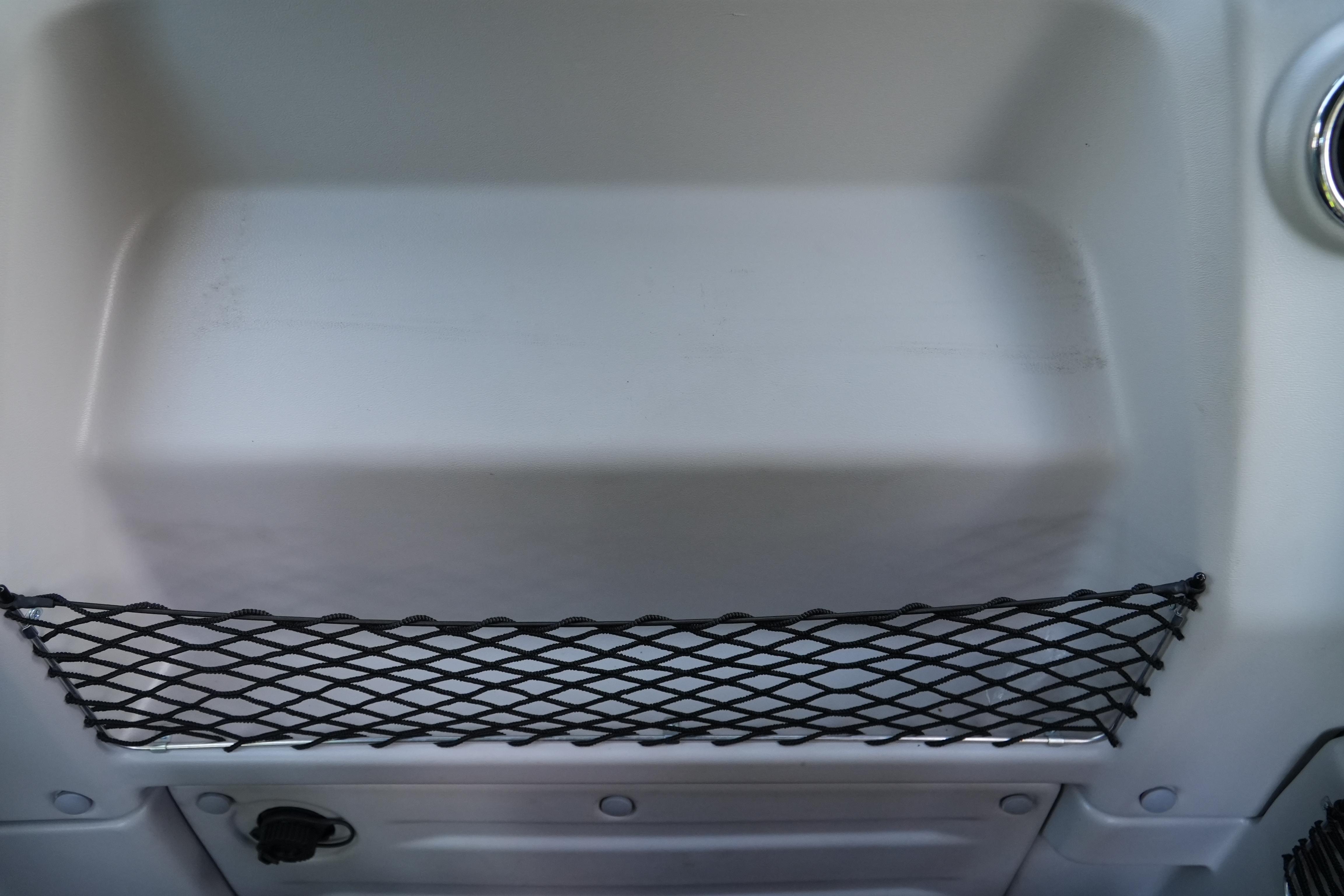
I had seen enough and with time ticking by, I was keen to get a feel for the machine. I fired up the Cummins engine, and giving it time to warm up, I explored the settings on the monitor discovering that there are three working modes to choose from, as we were only playing about on a heap of old tarmac planings, I decided to leave it in its default Eco mode.
A tug on the right-hand joystick and the SWE 155UF-2PB sprang into life, running the boom and dipper through the motions for a few times, I was quickly impressed with the machine’s performance and smoothness, and I remember thinking, wow, this Chinese kit is really coming on leaps and bounds now, compared to some of the earlier stuff I have tested for Earthmovers, this really felt up there with the best of them.
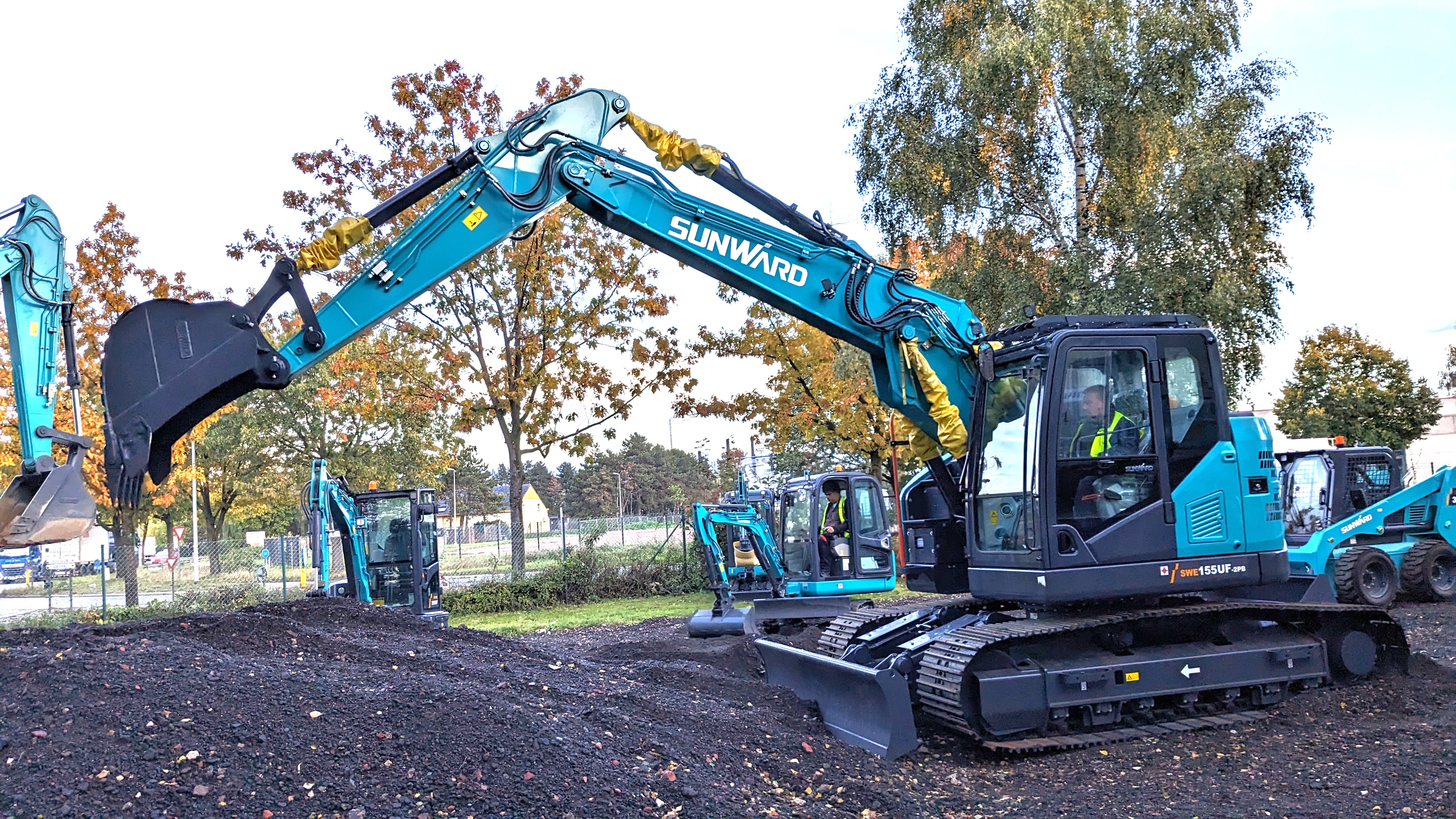
Of course, throwing some loose material around is no big test for a machine, but you could feel this had the power, speed and finesse to cope with the most demanding of jobsites. It was lively on the slew too, with a very quick take-off, the Hengli slew motor offers a speed rating of 11.2rpm so its no slouch in that department.
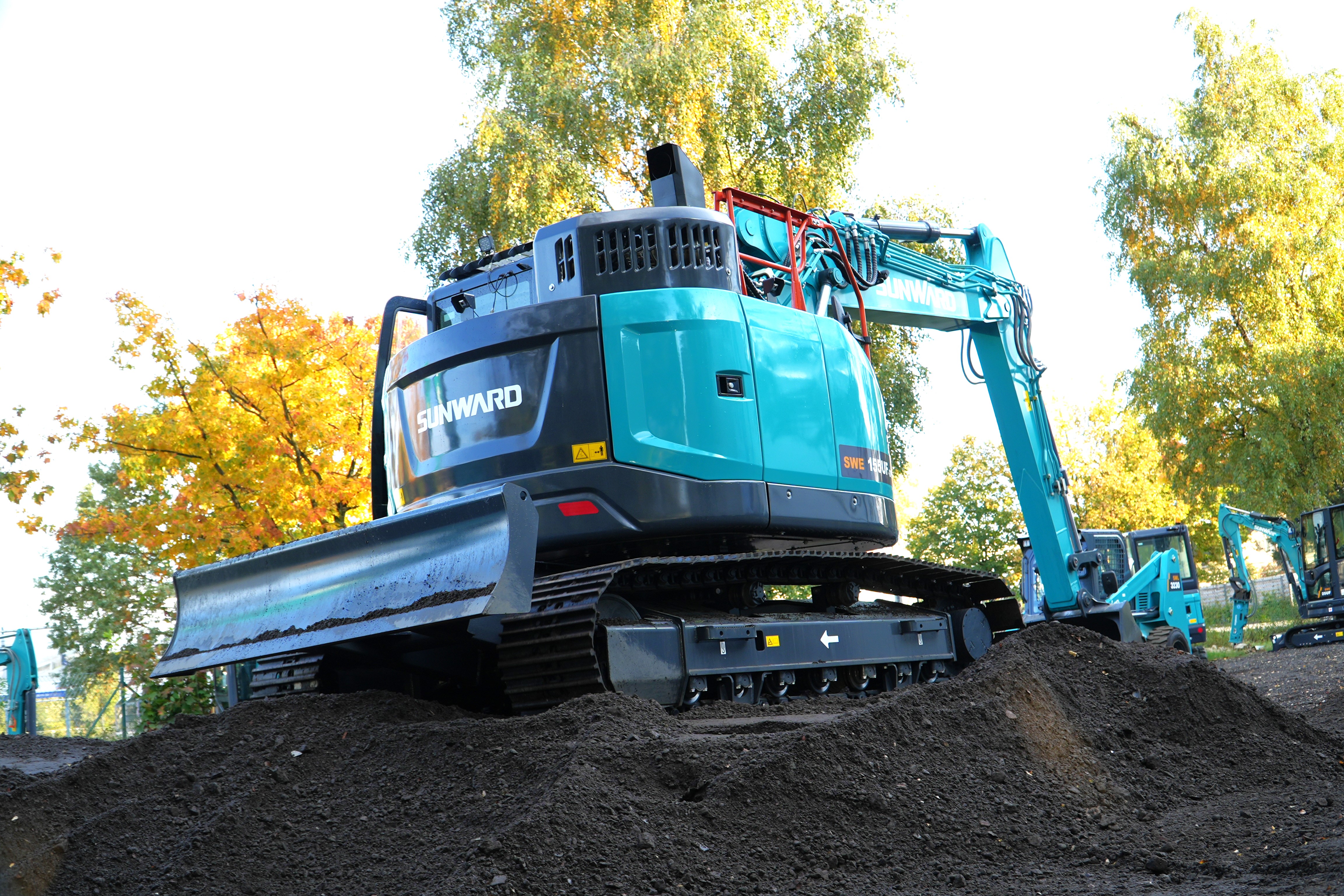
In the fine grading department, it was very proficient too, the Kawasaki inspired Chinese hydraulic system was proving its worth in that aspect without a doubt. All in all, I left the cab feeling well impressed with what I had just experienced, how durable these machines are in the long run remains to be seen, but in terms of basic economics and with the security of a 3-year warranty they are machines not to be overlooked.
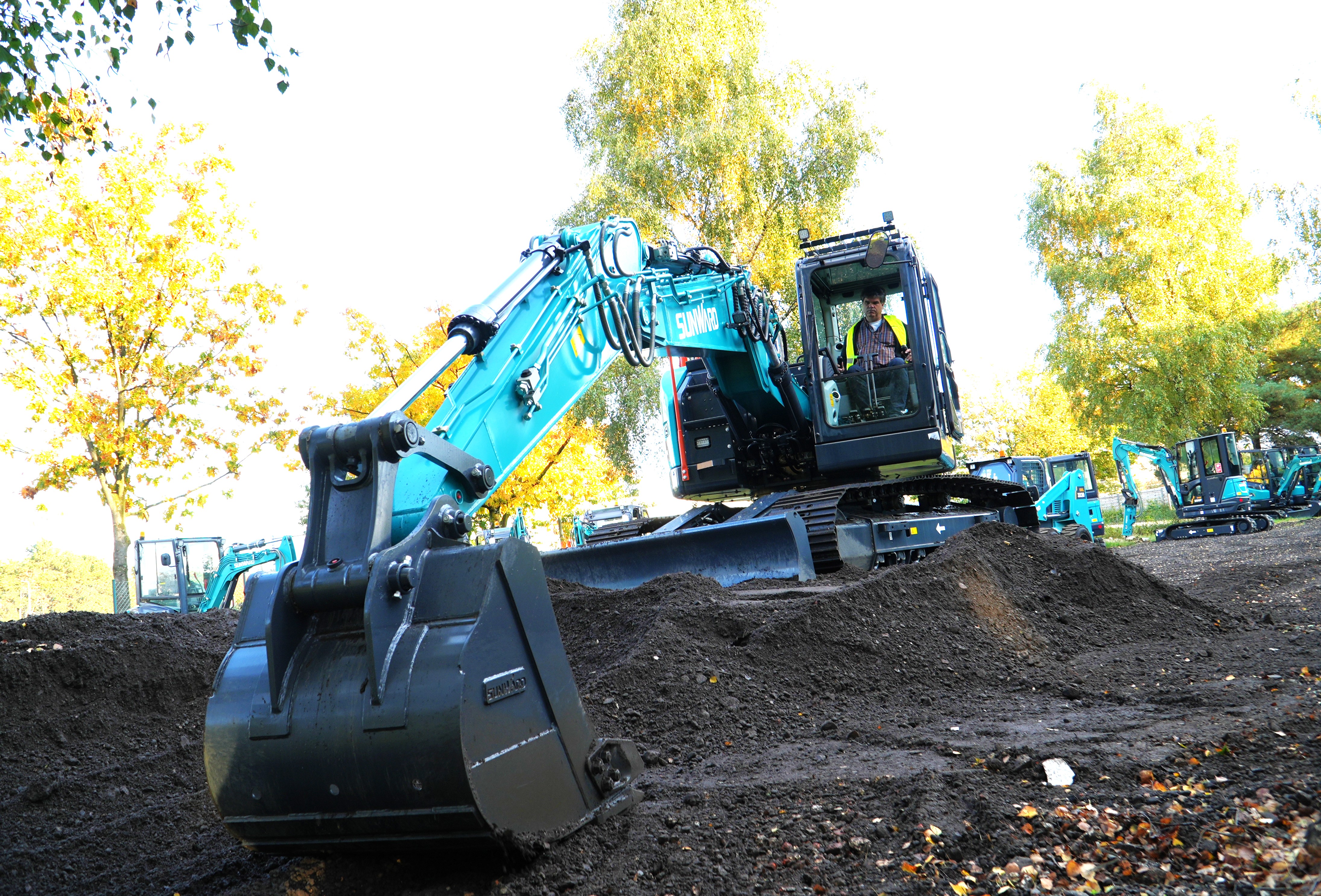
We had so many machines to look at in a short space of time, but I was extremely keen to try the big 24-tonne battery powered electric hydraulic excavator before I left.
Tipping the scales at 23,180kgs, and with a power output rating of 120Kw, we first caught sight of the SWE 240FED when it was on static display during Bauma 2022, where it cut a dominating figure in the centre of the stand. It’s probably fair to say that the machine is not going to win any beauty competitions with its box like shape at the rear end, however this is necessary to accommodate the 460KWh battery package, the biggest battery capacity in its class.
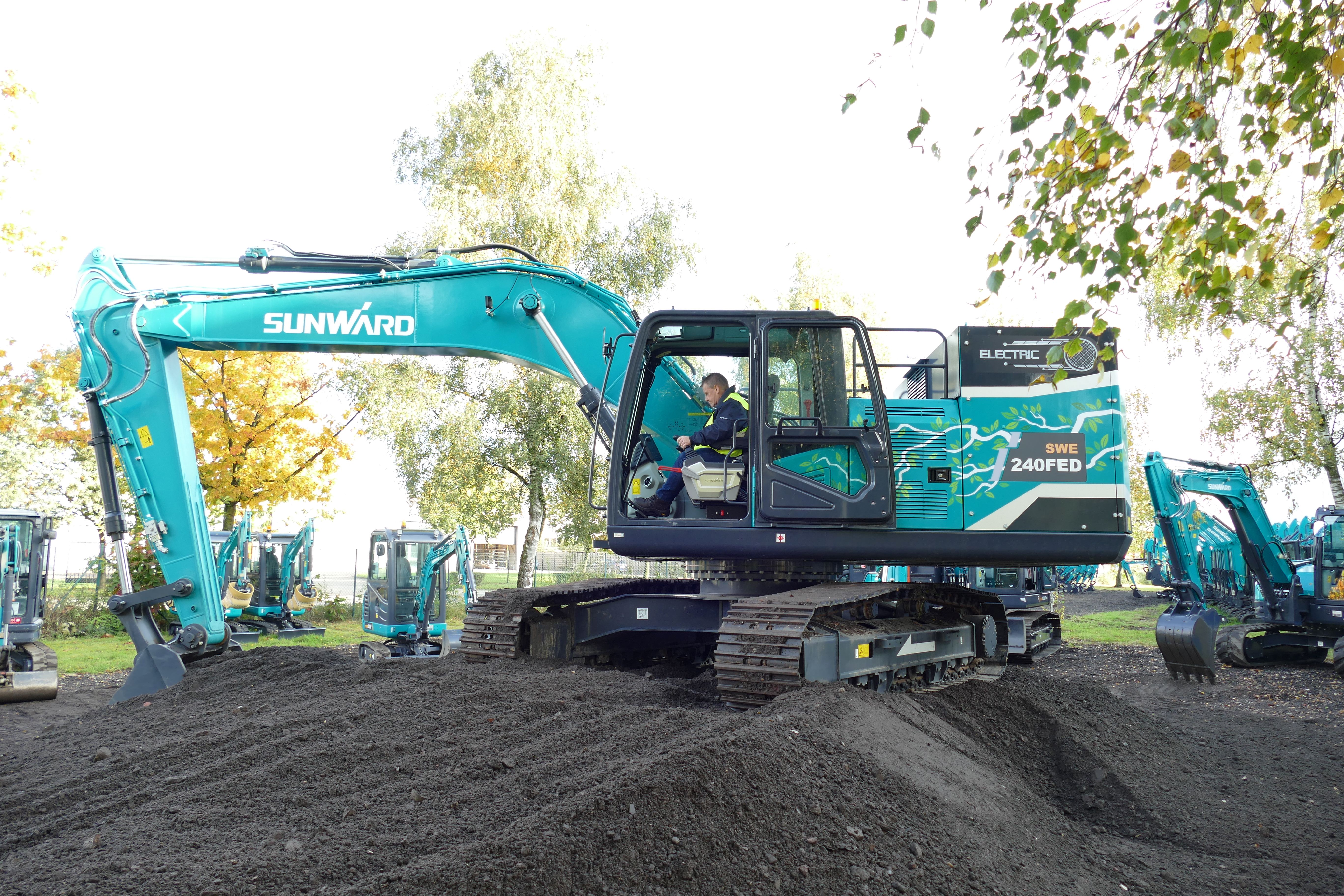
The battery which powers a 3-Phase asynchronous motor, is a premium product from leading battery technology company CATL, and is the Lithium Ferro Phosphate (LFP) type which offers the best protection against battery thermal runaway.
The big question with all these electric machines is always, how long can it work on a single charge, a question I posed to Hans Driesen, Sunwards Product Manager in Europe for earthmoving equipment.
Hans said, “We have already delivered at least four of these machines into the Netherlands that are working with a hydraulic shear in a scrap recycling application, those machines are actually achieving up to 10 hours of operation time, with zero emissions at point of use, which is impressive.
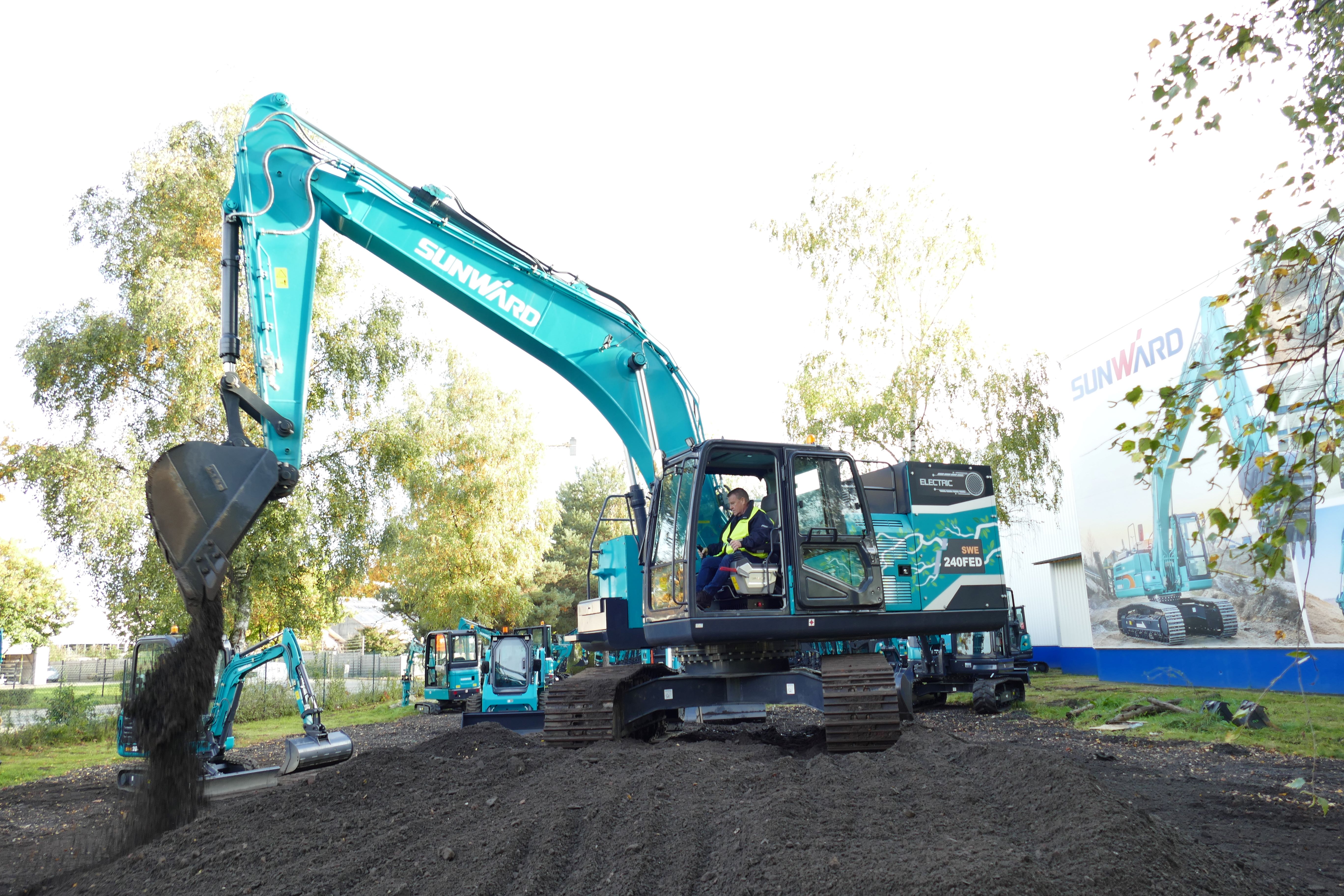
In heavy digging work it would be around 5 hours, and for truck loading operations around 6 hours, while in a demolition application, for instance running a hydraulic breaker up to 7 hours can be achieved.
In terms of battery recharging times, that all depends on the available electricity network i.e. (3 phase + neutral) The optional supercharger (dual gun, CCS2 plugs) offers the fastest recharge 600A/400V = 1.7 hours, 125A/400V = 7 hours while the 63A/400V = 12 hours overnight recharge”.
The machine comes supplied as standard with 7 hydraulic lines, including double acting aux 1/aux 2/ quick hitch and high flow return line.
I jumped in the machine for a very brief spin on the controls. Having spent time on a number of electric powered mini excavators, I wasn’t quite sure what to expect from a machine of this size. Flicking the switch to make the machine live, it just sounded very quiet, just like any other electric machine I had driven previously, but on actuation of the joysticks the machine came alive, I wouldn’t say it was overly loud, but it was making sounds that we are more used to from a modern excavator, personally I like to hear feedback from the machine operating, so I was delighted to hear it.
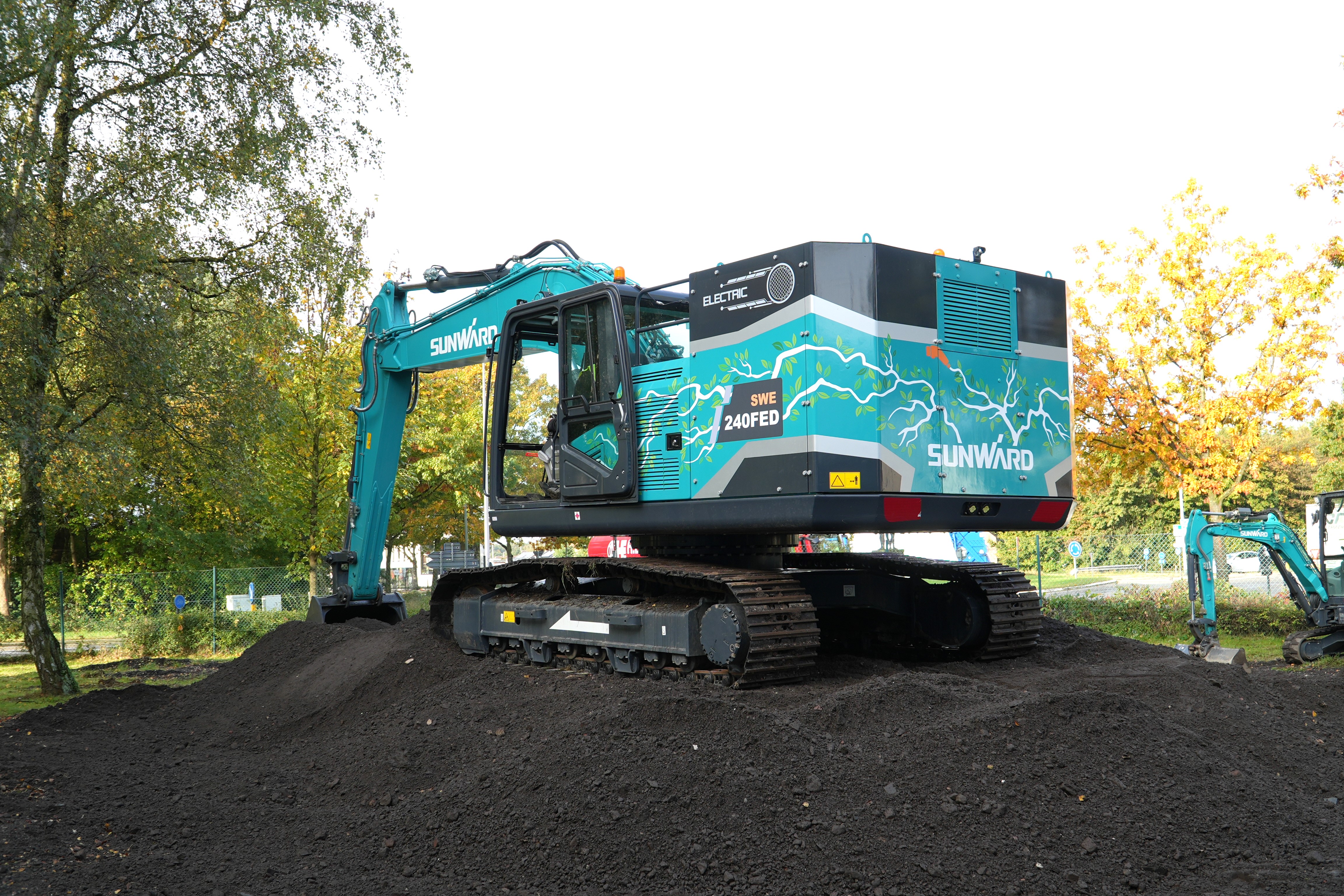
I have to say, performance wise, the SWE 240FED blew my mind, don’t let its ugly backend detract from its ability to do the job its designed for, this machine had so much power, speed and precision, that after a while, I had forgotten I was behind the controls of a battery powered hydraulic excavator, I left the cab with a beaming smile.
According to Hans, the company already has a smaller 21-tonne class SWE 215FED prototype going through the R&D department at the moment, so one to look out for in the future, I’m sure.
Having visited this facility, seen and felt the passion of those behind the European operation, I really had my eyes opened to the Sunward brand and I predict big things for them in 2024, especially in the UK with the quality of the newly selected dealers putting the brand well and truly on the map.
Checkout our video from the visit.