by Kyle Molyneux | Wed 10 Apr 2024
10 Years of Komatsu’s intelligent Machine Control
Since launching its first intelligent Machine Control (iMC) dozer 10 years ago, Komatsu was inspired by the innovation to launch a brand new digital construction portfolio. Now its own entity, Smart Construction's Deputy General Manager Richard Clement, discussed why iMC was such an important innovation and how it has inspired the next generation of digital construction solutions.
Q: How has iMC impacted Smart Construction’s approach to innovating for the sector? What did the rollout of iMC highlight for the industry?
Richard Clement: The invention of iMC has been instrumental in innovating further solutions for the sector. Intelligent Machine Control made us look closely at machine performance and the parameters we set - it opened our eyes to look at how customers really use our machines and further, how we can help them use them more effectively.
Because of the innovation of iMC, we managed to refine our offering to design a process to better suit the technology that was at our fingertips. We began to look wider than the machines that we had on site and recognise the power of thinking more creatively about how technology can be used to completely rethink the way we approach construction projects.
Our 3D Machine Guidance is a fantastic example of a solution that can be used with any excavator. It can be fitted to older machines so they can continue to be used at job sites, and the solution ensures that the latest plans from the planning team are uploaded and displayed to avoid costly reworks. Payload metering offers insight as to the material moved and distributed throughout the dig phase, and as-built data taken directly from the machine can be pulled through to create a digital twin of the jobsite.
An accurate and up-to-date digital twin allows site management to review progress and make decisions based on precise measurements without needing to make excessive visits to the site to view physical changes. We’ve so far implemented 3D Machine Guidance for a number of clients, including National Highways which has mandated 3D Machine Guidance for all plant machinery working on UK roads.
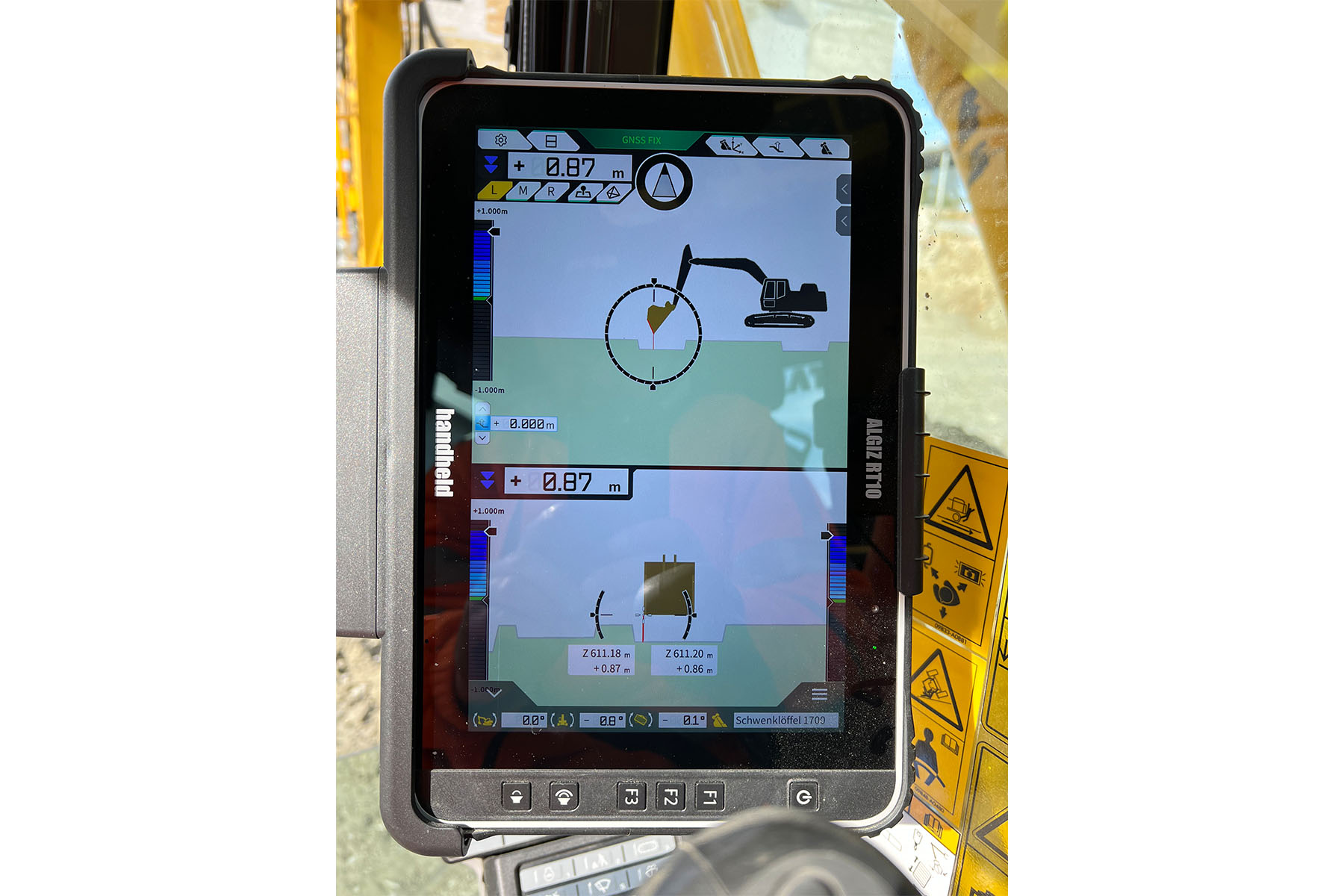
Q: What does the future of machine control look like?
RC: The future of machine control is about connectivity. We now need to integrate the entire job site so our machines become part of a comprehensive network. The challenge comes from being in a market where technology is beginning to mature, and different companies handle data in different ways. Interconnectivity is the next step. At Smart Construction, we’ve endeavoured to create agnostic tools that benefit the workforce no matter which OEM designed their fleet.
Achieving interconnection between different brands and OEMs is of utmost importance to the industry, ensuring a streamlined approach to data harvesting and handling across the sector. Once we achieve this, we’ll be able to enjoy continued growth as an industry, working together towards a common goal of a fully digitally optimised future.
Q: Do you see as-built data continuing to play a huge role in the digitalisation of the sector?
RC: As we move towards a digital future, technology is only going to play a bigger role in the planning and implementation of construction projects. In just a few years’ time, we’ll be revisiting sites that were built with the aid of tech like 3D Machine Guidance when we’re contracted for new projects - and all the data from the initial groundworks will be accessible.
In construction and especially earthworks, one of the only things we can be certain of is the uncertainty of the subsurface - in the majority of cases, you’ll find something unexpected when you begin to break ground. Having access to previous files and visuals of the site is invaluable when it comes to ensuring an efficient delivery of a contract.
Ultimately, data collection should be easy – it shouldn’t be an extra task for the driver or site manager. The data is there for the taking, and we’ve simply enabled the workforce to capitalise on it.
Got a news story? Email news@earthmoversmagazine.co.uk.