by Kyle Molyneux | Mon 21 Nov 2022
Cat MH3250 and MH3260 Material Handlers
The new Cat MH3250 and MH3260 material handlers replace the Cat 330D MH and 345 C MH models respectively, boasting longer maintenance intervals and improved fuel efficiency to decrease owning and operating costs up to 20%. An entirely new cab concept elevates operator comfort throughout the shift to increase productivity.
Both models feature new mechanical variable-gauge undercarriages that flexibly improve machine transportation without sacrificing lifting performance. Track gauge retracts to 3,220mm to lower transport costs and make moving the material handlers more efficient. When at the yard, gauge extends to 3,720mm-wide to increase stability and maximise lift capacities.
The MH3250 and MH3260 promise excellent capacities when working at their respective 16,010mm and 18,000mm maximum reaches, reducing the number of times the material handler has to be repositioned at the yard to increase productivity.
Power modes
Three different power modes – Power, Smart and Eco – fine-tune power requirements to the job, so the new MH3250 and MH3260 use less fuel than their predecessors without sacrificing machine performance. Smart Mode automatically matches engine and hydraulic power to working conditions to reduce fuel consumption, while Power Mode provides maximum power to optimise productivity. The machines’ new fuel-efficient engines meet stringent EU Stage 5 and US EPA Tier 4 Final emission standards, and can run up to B20 biodiesel.
These material handlers operate at up to 2,600mm above sea level without derating and offer standard high-ambient temperature capability of 52C and cold-start capability of -32C. New valve priority automatically places hydraulic pressure and flow where it’s required to increase material handling efficiency. Their advanced electrohydraulic system provides the optimum balance of power, efficiency and load control. Auto warm-up reduces the time it takes for hydraulic oil warming in cold temperatures and helps prolong the life of system components.
A range of attachments and reach options are available for varied applications to increase operating flexibility. Increasing the MH3250’s versatility, it can be equipped with the ex-factory 25kW generator for magnet operation. Customers can choose from a range of Cat work tool attachments in different sizes to meet the site’s material handling and production needs.
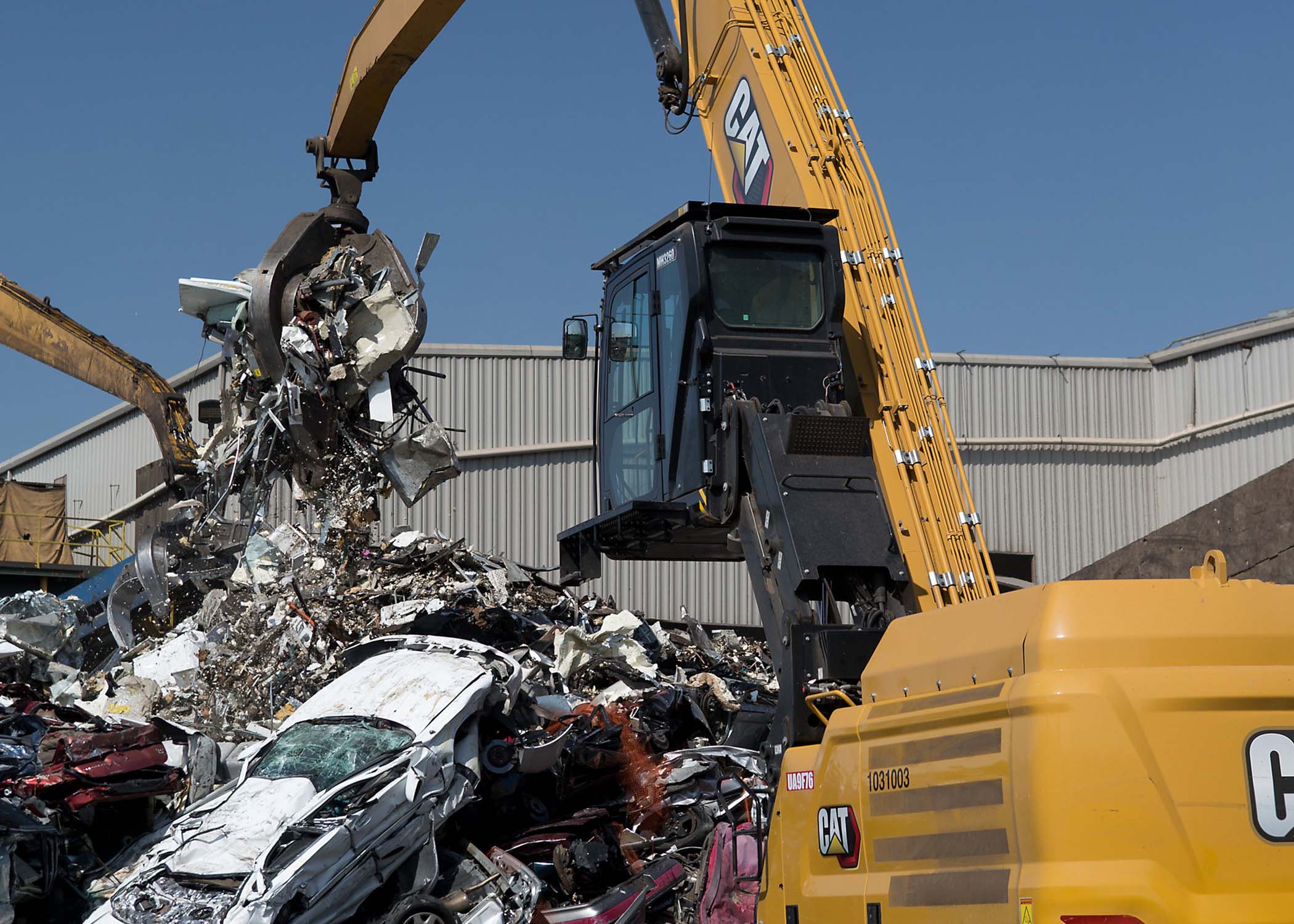
Cabin advancements
Featuring sound suppression for interior noise reduction and rubber cab mounts to reduce vibration feedback, the all-new next generation cab promises to improve operating comfort and productivity. A 10-inch touchscreen monitor with jog-dial offers easy navigation of the operator controls. Improving highwall trailer loading/unloading and shredder loading efficiency, the hydraulically controlled cab rises to a maximum elevation of 6,020mm.
Smaller cab pillars, combined with large tempered windows and a flat engine hood, deliver excellent all-around visibility for the operator, increasing safety. With video feed displayed on the large touchscreen monitor, standard rear-view and side-view cameras improve work area visibility. The cab design includes thick, impact-resistant safety laminated windshields that meet P5A standards, while operators are protected from falling and flying debris by the standard Falling Object Guard System (FOGS).
An upper-level service platform with access steps constructed of antiskid punch plate provides easy, safe and quick access to machine service items. In the event of a hydraulic service interruption, the cab can be safely lowered via one of two emergency cab lowering valves, located inside the cab as well as outside of the machine. Check valves on the boom and stick prevent reverse hydraulic oil flow, to maintain the position of the front linkage should the hydraulic system experience an unexpected loss in pressure.
Now standard technologies on the MH3250 and MH3260 material handlers elevate operating protection. New cab avoidance helps the operator by preventing contact between the attachment and cab. E-fence automatically stops machine motion using boundaries you set in the monitor for the entire working envelope. By requiring a PIN code to start the engine, the new Operator ID inhibits the machine from unauthorised operation.
Simplified servicing
Synchroniwed service intervals and extended filter replacement schedules reduce maintenance time and costs for the new Cat MH3250 and MH3260 material handlers. All fuel filters feature a coordinated 1,000-operating-hour change interval, and the new air intake filter with pre-cleaner lasts up to 1,000 hours to reduce maintenance requirements.
A new hydraulic oil filter improves filtration and increases change intervals to 3,000 operating hours, a 50% longer service life than previous filter designs. New anti-drain valves keep the hydraulic oil clean during filter replacement to improve system longevity.
Operators can track filter life and maintenance intervals on the in-cab monitor. Eliminating the need for operator interaction, the cooling fan features an automatic reverse function to keep the cores clean. Conveniently located ports allow for quick fluid sample extraction for analysis.
New remote services capabilities for the MH3250 and MH3260 increase service efficiency and potentially save trips to the jobsite. Remote Flash works around the production schedule to conveniently assure the machine operates with the most current version of on-board software, so it delivers high performance with minimum downtime. The Cat App conveniently helps to manage fleet location, hours, and maintenance schedules and provides alerts for required maintenance needs.
Got a news story? Email news@earthmoversmagazine.co.uk.
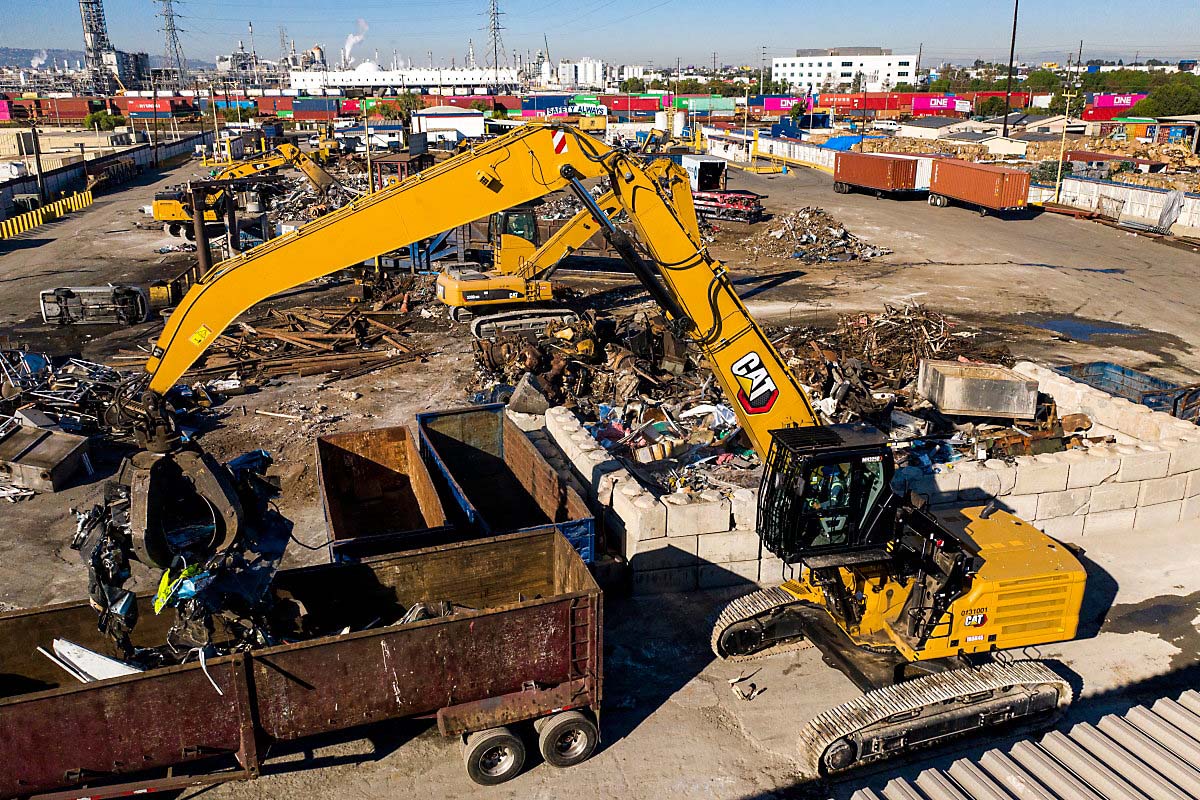