by Nick Drew | Tue 01 Jul 2025
Big Bell Fits the Bill for Brookland
I last visited Brookland Sand & Aggregates back in 2016, so it was with great delight that I headed back down to the Littlejohns pit near St Austell, Cornwall, recently to take another look around and to spend some time with their latest articulated hauler addition.
This family-owned business was formed in March 2010, after Barry Cleave and his son Marshall purchased the Gunheath Quarry operation from Aggregate Industries. The Cleave family has a long history in the earthmoving plant and machinery sector, with Marshall Cleave’s grandfather Norman Cleave having formed Norman Cleave Plant Hire as far back as 1972, the company had an extensive fleet of earthmoving equipment which worked on many of the large motorway projects up and down the country in what have always been considered to be, the golden years of road building in the UK.
The company started to diversify into aggregate processing and recycling around the mid-1990’s and it is this aspect that following the formation of Brookland Sand & Aggregates, the company is primarily focused on to this this day.
Based right in the middle of the white lunar type landscape that is Imerys China Clay works, the company takes in excess of 2 million tonnes of China Clay waste per year from the main Imerys operation, and recycle it into around 1.5 million tonnes of saleable product for use on a wide range of construction projects not only in the South West but more nationally too, with large volumes being sold into the London and surrounding areas.
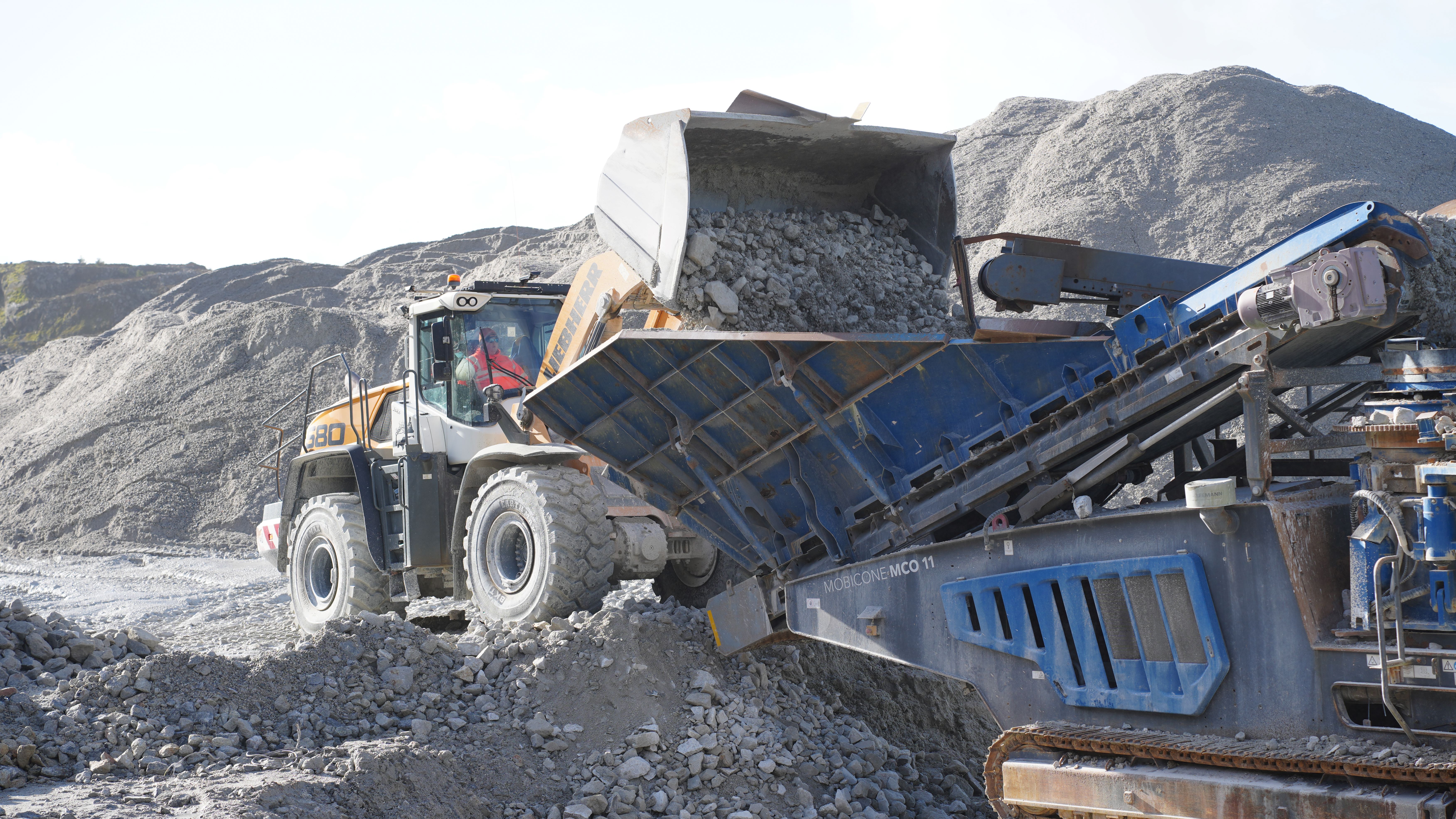
It’s a significant operation producing any thing and everything that is granite based from fine sand right up to armour rock. The material is notoriously abrasive and as such is hard going on the machines and associated equipment.
A significant amount of the material produced here is supplied to the concrete producing companies, and of course supplying sand and aggregates to groundwork contractors working on infrastructure sites.
On the machine front, Brooklands have most recently taken delivery of a Bell B45E 4x4 articulated dumptruck which is the first of its kind delivered to a customer in the South West of England. The unit had actually made an appearance on the Bell Equipment UK stand during the Hillhead show last year and was delivered to site sometime after the event.
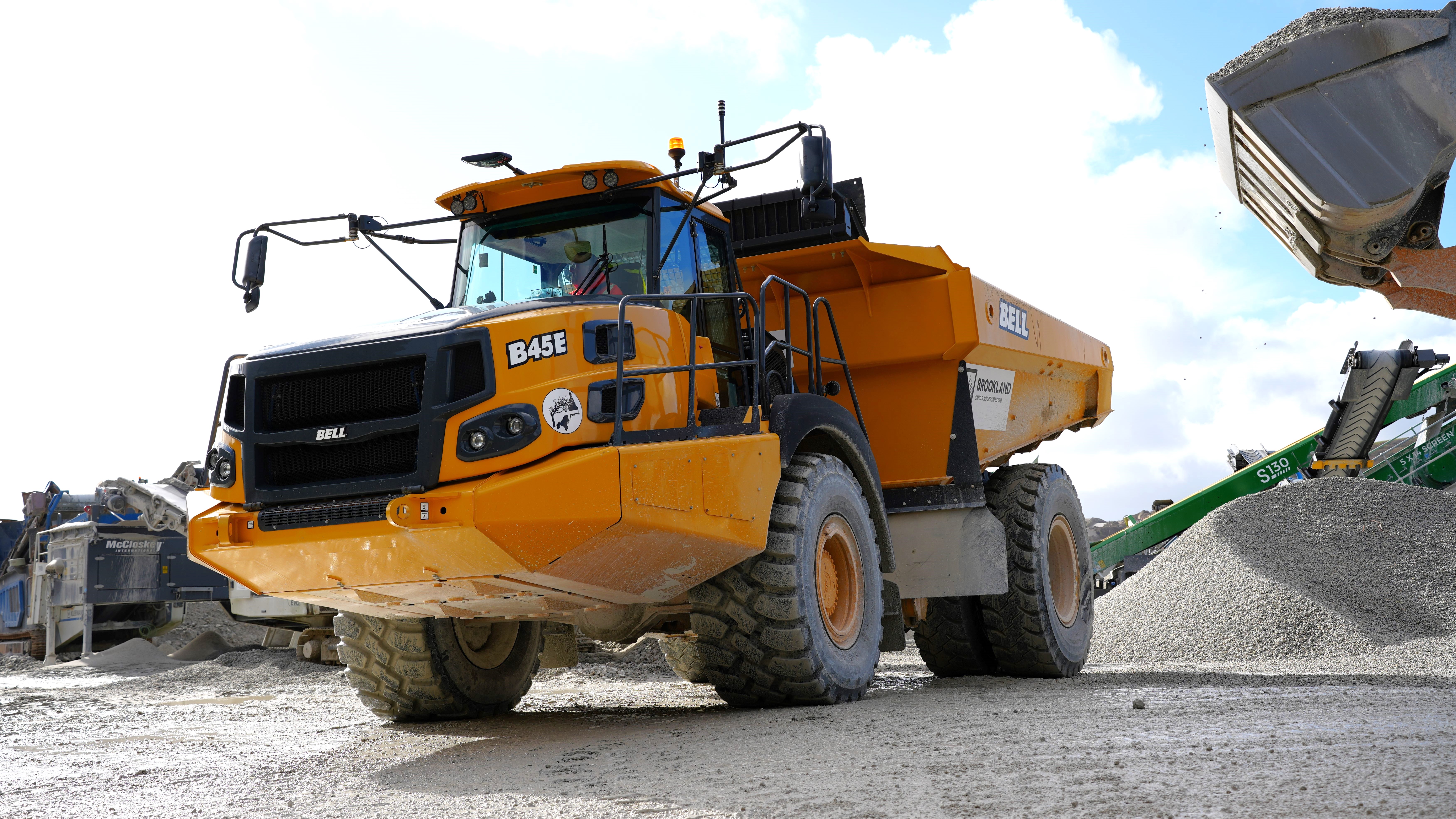
Asked about his decision to opt for the Bell Marshall said, “We have been running three Caterpillar 770 rigid dumptruck’s here for some time now, we have found that they work well on site here because we have good roads throughout the site. We had found from previous experience that when we ran 6 wheeled articulated hauler’s they had a tendency to tear the roads up, which can cause problems when road going lorries come into the pit, they just don’t work together, so that’s why we tend to stick with four wheeled dumptruck’s and now that the B45E 4x4 has come along, it certainly appears to offer the best of both worlds for us”.
Two of the Cat trucks have had Cat Certified Rebuilds by Finning, but the price to do the third was considered to be unviable and ultimately it made more economical sense to invest in the new Bell unit.
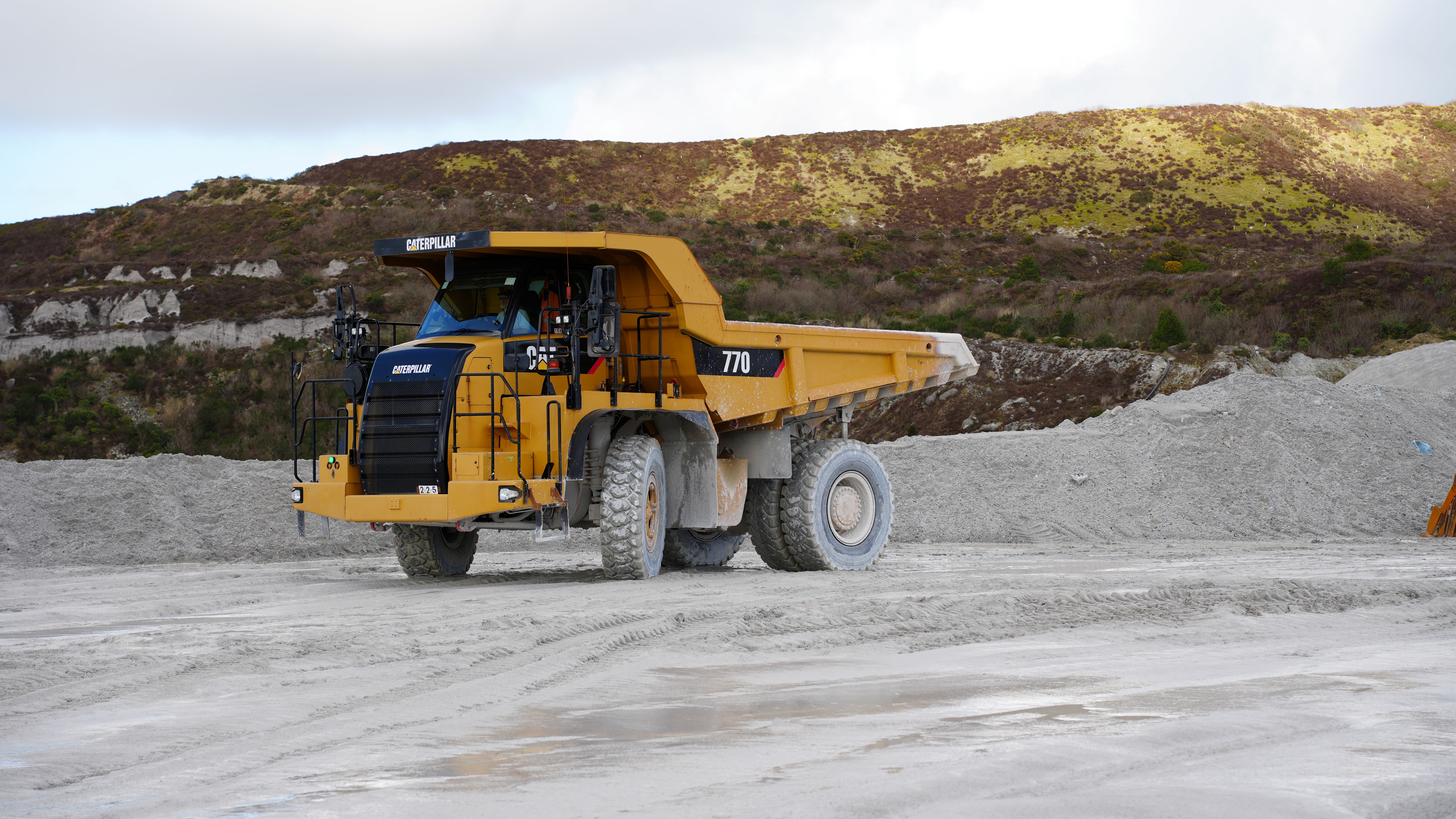
Marshall continued, “We had stayed with the old Cat’s because they were last generation units, with no AdBlue or DPF issues to worry about, and they were very cheap to run in many aspects, and as its very early days with the Bell B45E, I’m yet to find out what the running costs will be, we know already that the tyres will be more expensive to replace, but we will cross that bridge when the time comes, hopefully the fuel savings will help to fund the new tyres!”.
It’s still relatively early days running the Bell but asked how it’s been so far Marshall commented, “Yeah, it’s been pretty good, we had a few teething issues, as you do with any new machine, but the Bell guys have been right on it straight away, we are finding that the fuel economy is definitely there over the Cat’s and it’s been running absolutely fine.
My mistake was not ordering a tailgate with the build order, we had never needed to have tailgates on the Cat’s, but the Bell seems to have a short skip and with the general geometry of it, its clear we need a tailgate as it does tend to spill a bit of product when going up steep climbs”.
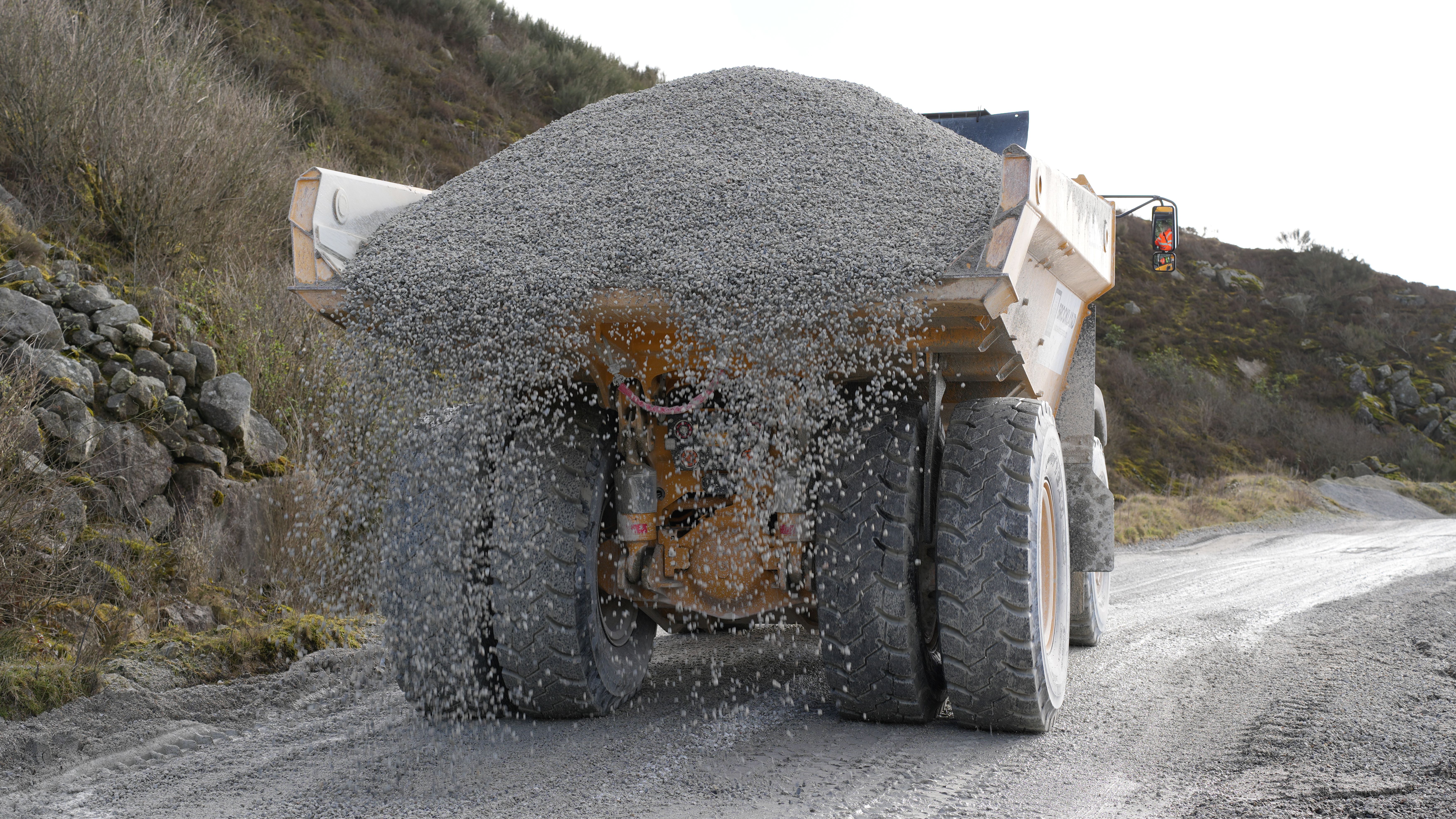
Adam Baker, Bell Equipment’s Regional Account Manager said, “A tailgate is now on order and in the build stage at our factory in South Africa, it will then be transported to our European hub in Eisenach-Kindel in Germany, then from there will be delivered to the UK”.
The Cleave’s are no strangers to the Bell brand having previously run a 40-tonne class B40 and two 25-tonne class B25’s, at the time they were undertaking more muckshifting work then, and eventually the B40 came into the pit to undertake longer hauls, but it was not involved in bringing the aggregates up out of the lower workings, due to the tearing up of the roads, especially on the corner turns. The B40 was actually taken back in part-exchange for the new B45E 4x4 model.
BELL B45E 4x4
The Bell B45E 4x4, which has a rated payload of 41,000kg (90,390lb), made its first public appearance at the Bauma Trade Fair in Munich in 2019, slotting into the manufacturers 4x4 range between the smaller B30E 4x4 and the larger B60E 4x4.
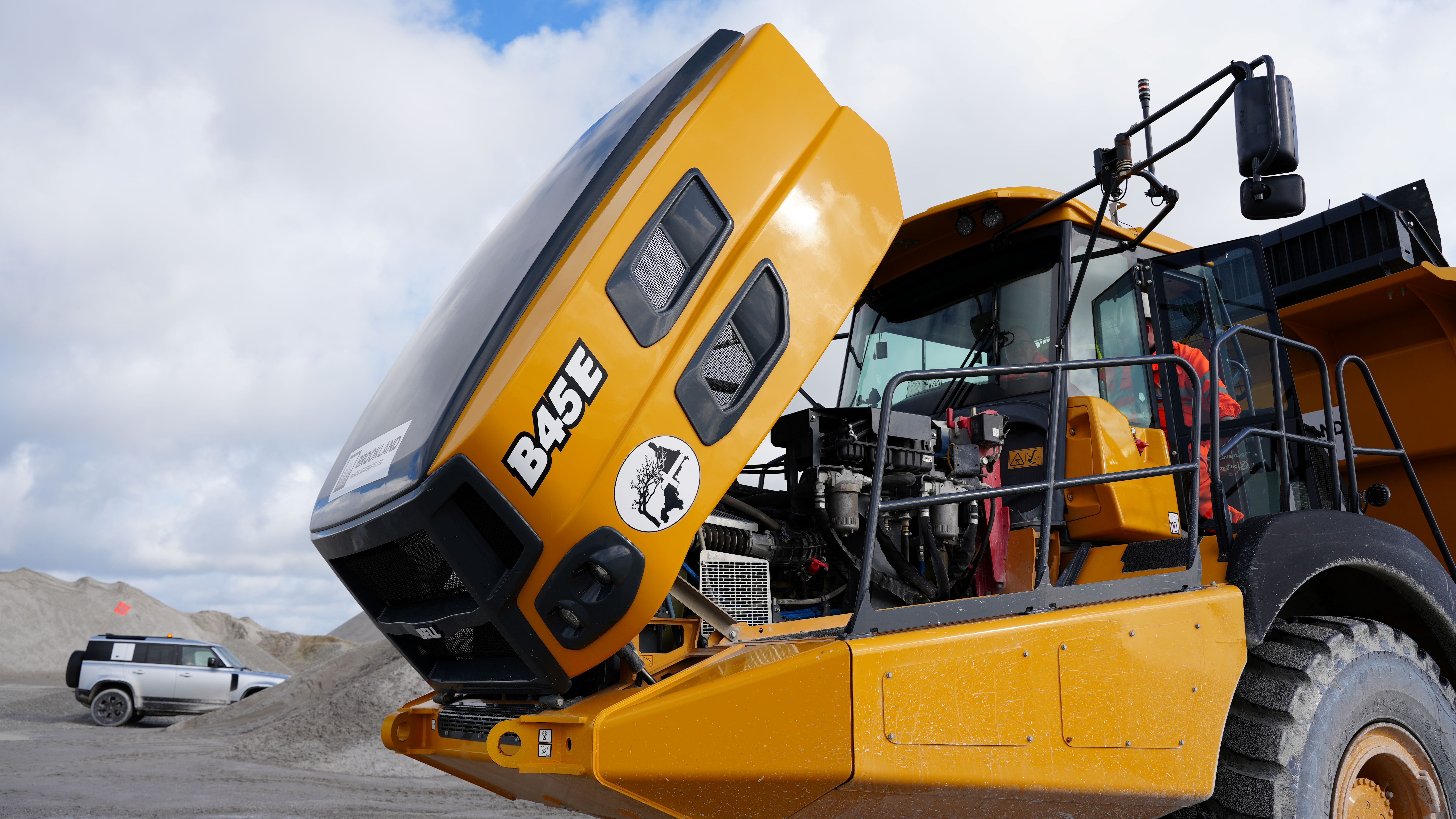
Power comes from the well-proven Stage V emissions compliant Mercedes Benz (MTU) six-cylinder turbocharged and intercooled diesel engine, which produces a maximum power output rating of 390 kW (523hp) @1600rpm and a gross torque of 1,917lbft (2,600 Nm).
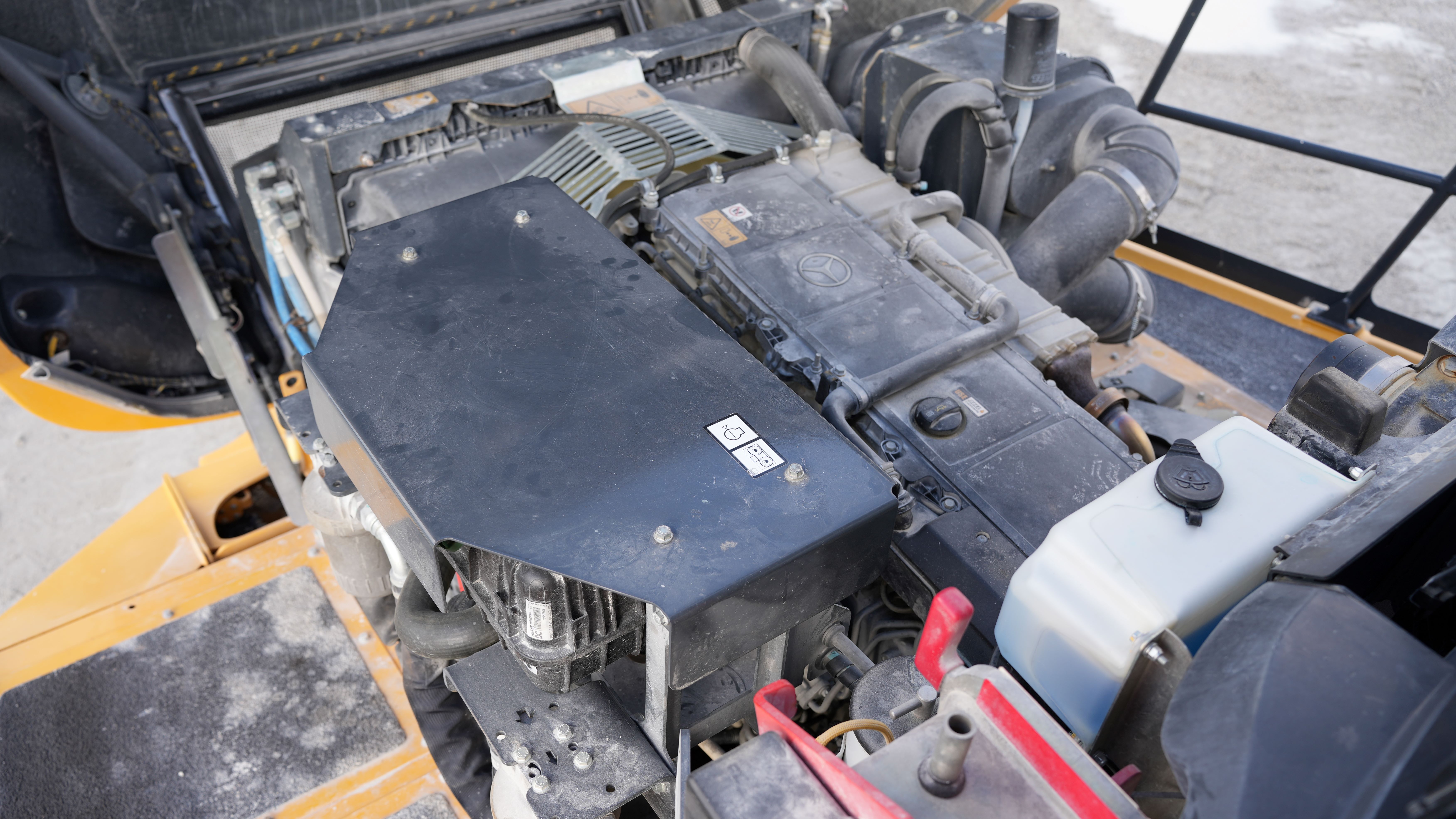
This drives an Allison 4700 ORS fully automatic planetary transmission, offering 7 forward gears and 1 reverse gear, speed ranges from 3.5 km/h (2.1 mph) in first gear and up to 48km/h (30mph) top speed in 7th gear, whilst reverse gear delivers 6km/h (3.7mph).
Wet brakes on both axles ensure safe and controlled deceleration working in conjunction with the Jacobs engine brake, which provides a multi-stage programmable automatic retardation.
The front section of the machine is effectively the same as the conventional B45E 6x6 offering in this weight class. Fitted with a Bell manufactured front axle the truck rolls on 775/65R29 tyres, in this application from Goodyear. The machine also features Bell’s ‘Comfort Ride’ adaptive front suspension system which although an option, is fitted as standard on all UK supplied Bell trucks.
The rear chassis and it’s 25 m3 skip is based on Bell’s original 4x4 offering the B60E with built in strength for the toughest of conditions.
It features a rigid mounted 55-tonne capacity axle which is supplied by blue-chip German manufacturer Kessler, this axle drives the twin rear wheels fitted with 21.00R35 tyres in this instance are once again supplied by Goodyear, this set up provides a steady platform for carrying a nominal payload of 41.0 tonnes.
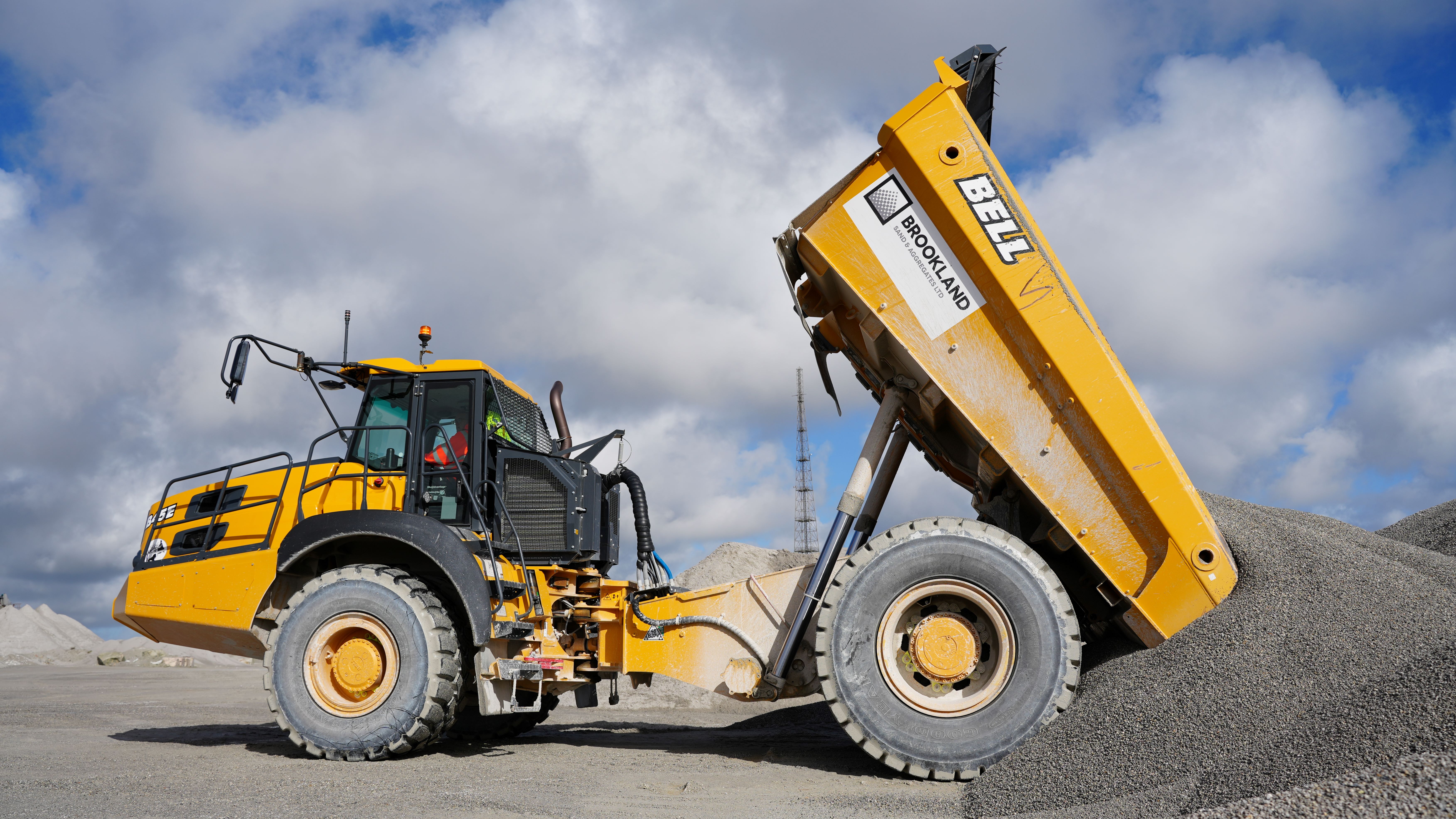
The truck cuts a dominating figure as it climbs out of the pit with its large rear skip, I liken it to a regular ADT on steroids with a combination of all the good aspects of a rigid truck, and the equally beneficial aspects of an articulated hauler, in this application with good haul roads it’s a superb piece of kit.
The wide rear end geometry and the flat-bottomed bin floor is well suited to such quarry applications, and enables easier loading from loading shovels and hydraulic excavators. On the day of our visit Marshall’s son Jake Cleave was loading the Bell B45E 4x4 with his Liebherr 580 XPower wheeled loader fitted with a 5.7m3 bucket in just 5 passes.
At the tip area the twin double acting two stage telescopic dump cylinders, fully hoist the body in just 18 seconds, and lowers the body in 16.5 seconds. Maximum tipping angle is 55o or can be programmed to a lower angle from the cabin. The short bin body reaches a tipping height of only 6394 mm, which can be an advantage when operating with overhead structures especially useful in this application working around hoppers and crushers.
The wide bed allows for clean tipping with hardly any return load material staying put in the skip, having said that this processed material seemed to flow very nicely out of the back end.
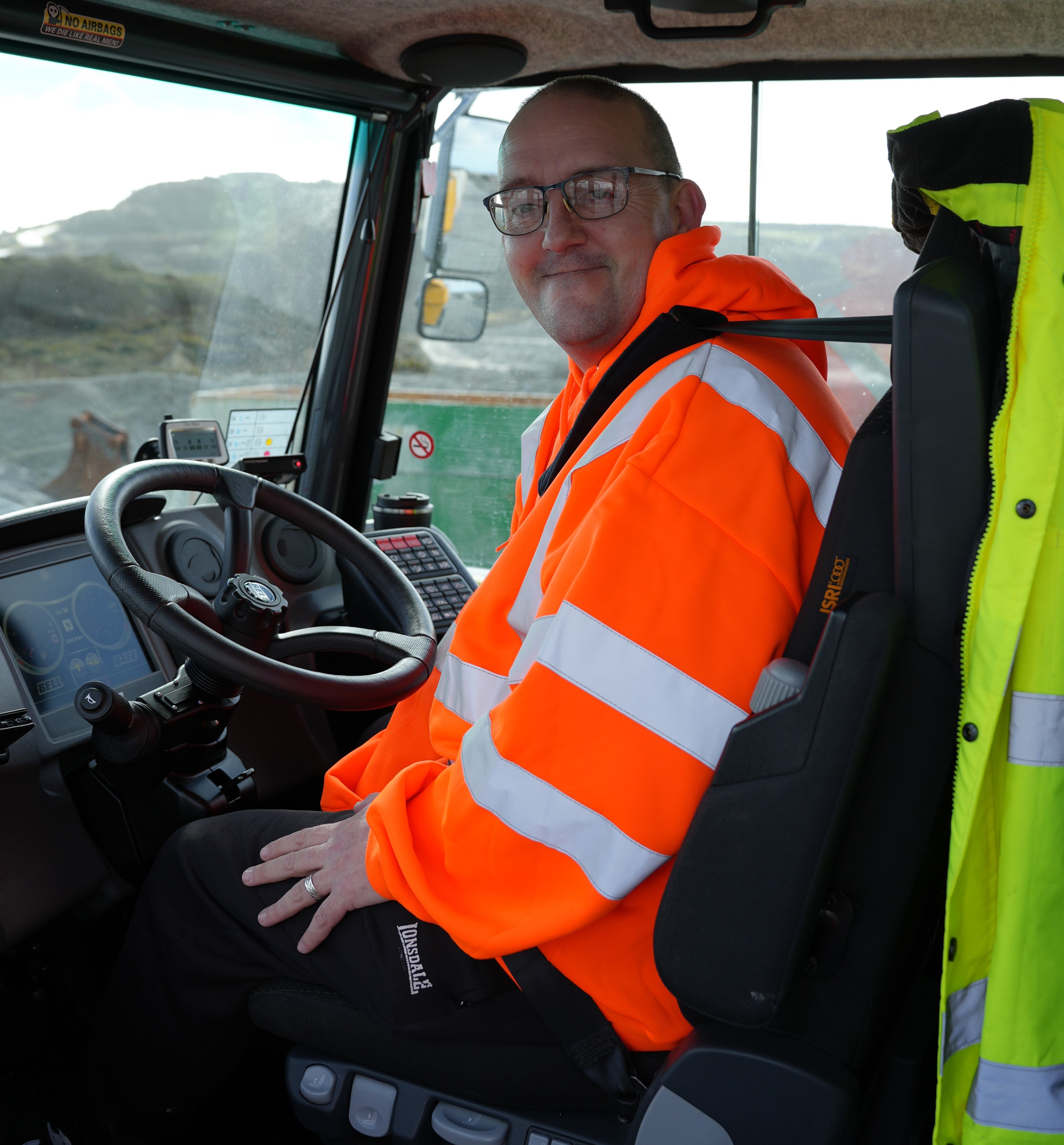
Pictured above: Operator Steve Bond.
I didn’t have the opportunity to drive the truck, but I did spend some time with regular driver Steve Bond in the spacious and well-appointed cab. Steve had previously been driving one of the Cat rigid trucks but was very clearly impressed with his new mount, “It’s a brilliant piece of kit, its really comfortable to run too, and I find the ride to be a lot smoother than anything else I have been on before, I’m very happy with it” commented Steve.
The cab interior is of the usual Bell standard, with the comfortable air suspension seat as standard, and the familiar control pad to the driver’s right-hand side, and simple to use direction and tipping levers also on the right-hand side of the cabin. There is also a comprehensive package of productivity, safety and ease-of-operation features, based on real-time data collection by the truck’s sensors (on-board weighing, pitch/roll sensor, and a rear-view camera screen which is crystal clear and, in my opinion, one of the best examples I have seen. All in all, it looks like a nice place to be spending a shift.
PROCESSING OPERATION
The company runs no less than 16 wheeled loading shovels of varying sizes, all from their preferred supplier Liebherr, which they say work very well for them as a business, and Marshall says he can’t fault them in terms of fuel economy and reliability, they range from the 566 model right up to the 586 all working at various locations around the Littlejohns site and at another location nearby.
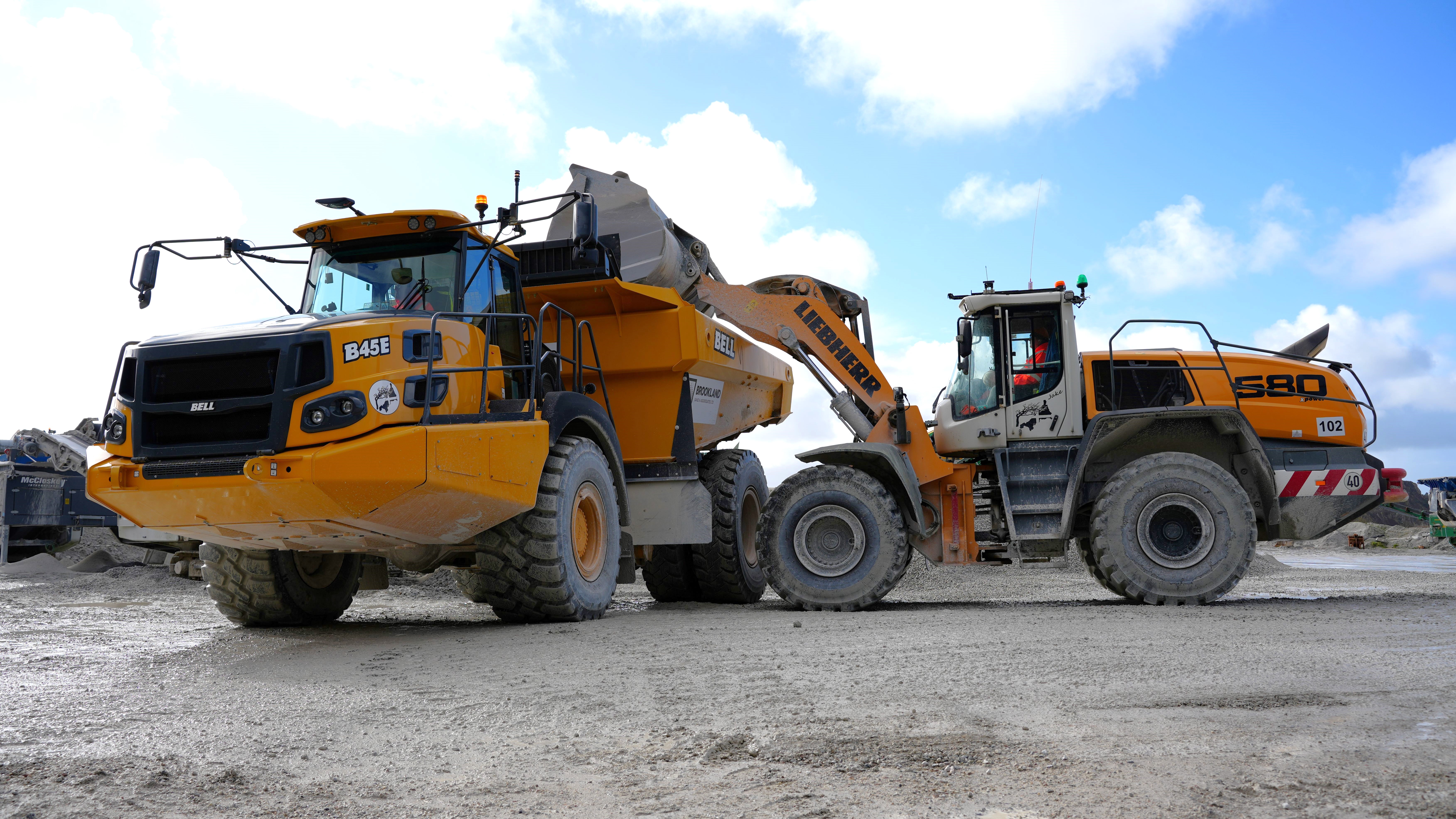
They also run a number of Liebherr hydraulic excavators which have not been as reliable as the shovels and have proven to be rather expensive to repair.
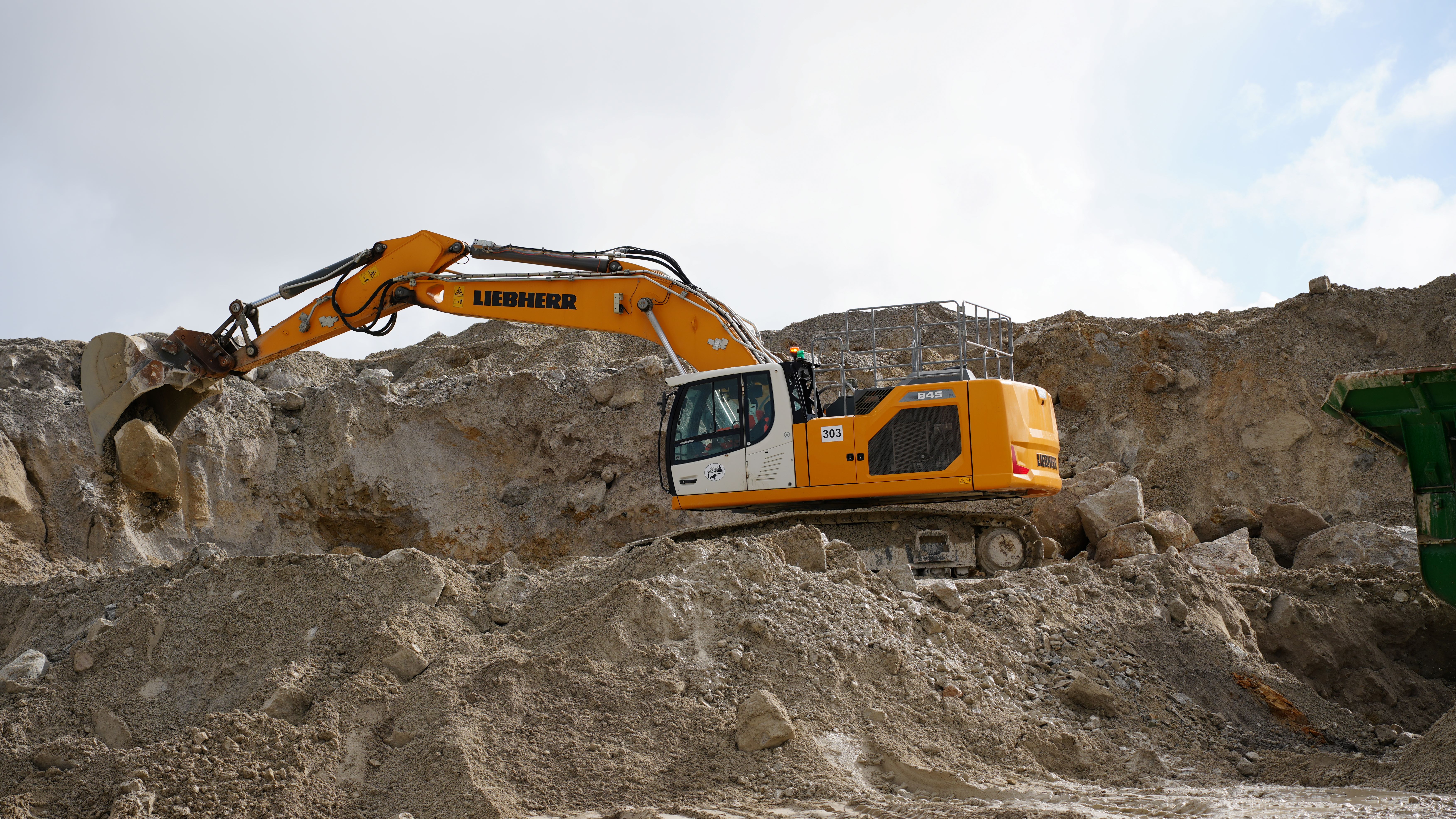
In terms of the processing equipment, there is a lot of it down in the pit and there needs to be as Marshall explained, “So we take Imerys’s waste, for every one tonne of kaolin (china clay) produced, there is nine tonnes of granite waste, rock and sand. So, Imery’s largely deliver the waste to us, or on the odd occasion we will go to a location of a blast and process there, but in the main it comes to us in Littlejohns where we undertake the processing at our more permanent set-up.
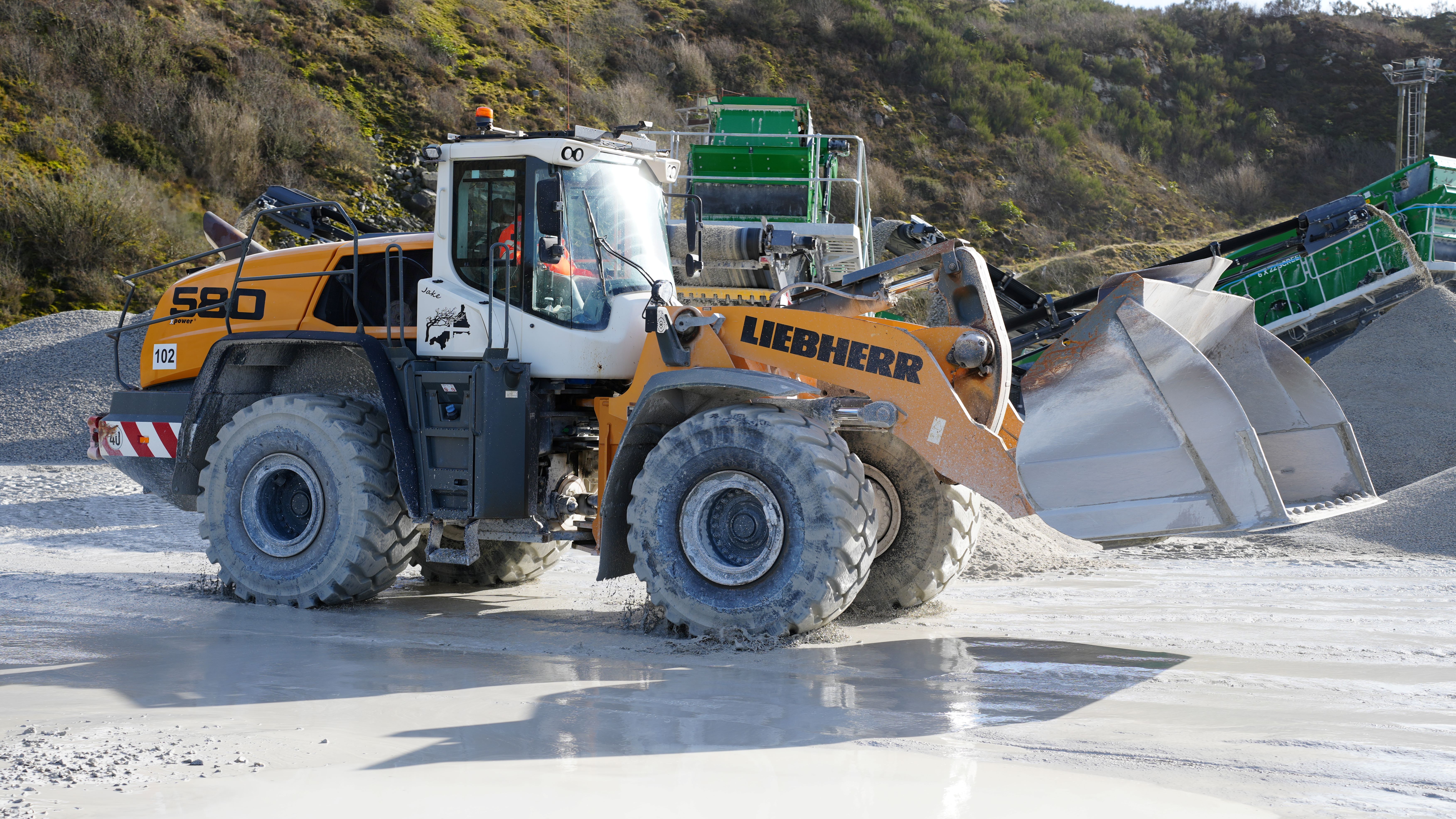
For the primary operation we have three of the Kleemann MC120i jaw crushers running here, and one Kleemann MC110 jaw crusher, and two McCloskey J50H’s. On secondary crushing side, we have four Kleemann MC11’s which will shortly be refreshed for Kleemann MCO110’s which are the newer version, and we have the smaller MCO9’s, so plenty going on to keep us busy down there!”.
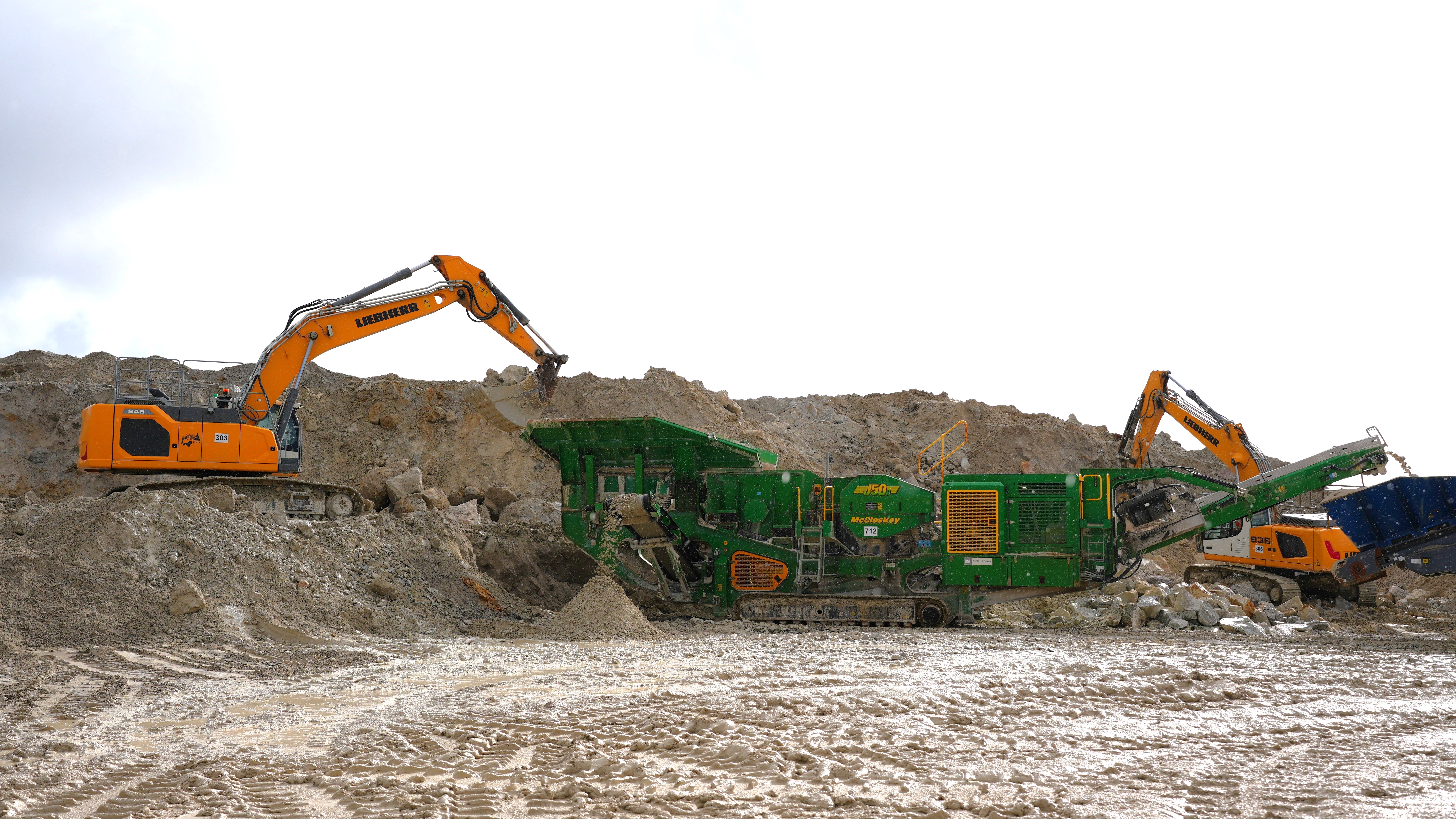
It’s always an interesting and insightful place to visit down in China clay country, the actual product itself is used in so many products that we take for granted on a daily basis, its used more obviously to make porcelain and ceramics, but also in paper production, cosmetics, fibreglass, adhesives, batteries and the obvious one in concrete, Marshall also pointed out that when you take a humble paracetamol tablet for a headache, it more than likely contains China clay too!
The fact that the waste product processed by the team at Brooklands goes on to be a useful commodity in the environment while ticking all the relevant green credentials, can only be a good thing for the local area and the world in general.