by Nick Drew | Thu 12 Nov 2020
Big Cat’s on the Prowl at Torr
Taking a look back at one of my articles which previously published in Earthmovers, bringing it to life on the internet with alternative photos and video footage.
As an excavator operator working on sites across Hampshire and East Dorset back in the late 70’s to early 1990’s, I was often engaged in work that involved using the type 1 limestone that has been extracted from the famous Torr Works (formerly Merehead) quarry in Somerset from as far back as the mid 1930’s.
The stones distinctive colour, quality and even its smell has stuck with me to this day and although I had passed the quarry on numerous occasions in the past, I had never been inside. So, I was delighted to be invited to take a look around to find out more about the operation and to see their latest big Cat wheeled loader in operation.
From the late 1930’s the Merehead quarry was operated by another famous industry name Limmer & Trinidad, but in 1959 the site was purchased by Foster Yeoman, a company who were to become synonymous with limestone production in the area. The company invested heavily in the site establishing a railway branch right into the quarry.
In 1970 the quarry was officially re-named as “Torr Works”, apparently after the quarry’s chief engineer Ron Torr and the name has remained the same to this day. The current site owners are Aggregate Industries, who bought Foster Yeoman in 2006 and who continue to invest in the latest plant and machinery required to run such a large operation.
.JPG)
Employing over 150 people the Torr Works site covers an area of some 205 hectares and has an annual limestone aggregate production figure in the region of 5.5 million tonnes, which is primarily produced for the South and South East markets including London. The vast majority of the stone produced, around 70% is loaded straight onto rail wagons with the remaining 30% leaving the site on road going trucks. Rail is much preferred these days due to having a lot less impact on the environment.
Torr Works Mobile Plant & PPM Manager James Ashman explained a bit more about the operation, “This site is a bit unusual in the fact that it hasn’t got a load and haul process for stone delivery to the processing plant, the stone is dug direct from the face by our two primary movers the 992G and our new 992K wheeled loaders, who load it straight into the hopper of our giant walking crusher. The stone flows through our primary and secondary plants and makes its way up to the distribution hub via conveyor belts”.
There is a total of three rail lines for loading of the material, two are fed via a “tripper” which runs up and down the belt, loading the wagons from either side and one individual shuttle that loads wagons independently.
Road going vehicles are loaded via storage bin hoppers, or by one of the quarries two Cat 980M wheeled loaders from ground level. Making up Torr’s fleet of Cat loaders are 3 x 980K, 1 x 982M, 1 x 966M and a 962M. The M Series machines are all supplied as part of an FMS (Finning Managed Solutions) working arrangement, whereas the new 992K has been purchased outright by Aggregate Industries.
As mentioned previously, the 992’s are primarily dedicated to feeding the crusher, armed with a standard bucket capacity of 12.3m3; the guys are looking to achieve around 2,000 tonnes per hour with both machines feeding the hopper continuously one on each side. The O&K (Orenstein & Koppel) walking crusher is a huge structure, tipping the scales at around 1,300 tonnes and 7 storeys high it has been on site for over 30 years, since first entering daily use in 1985.
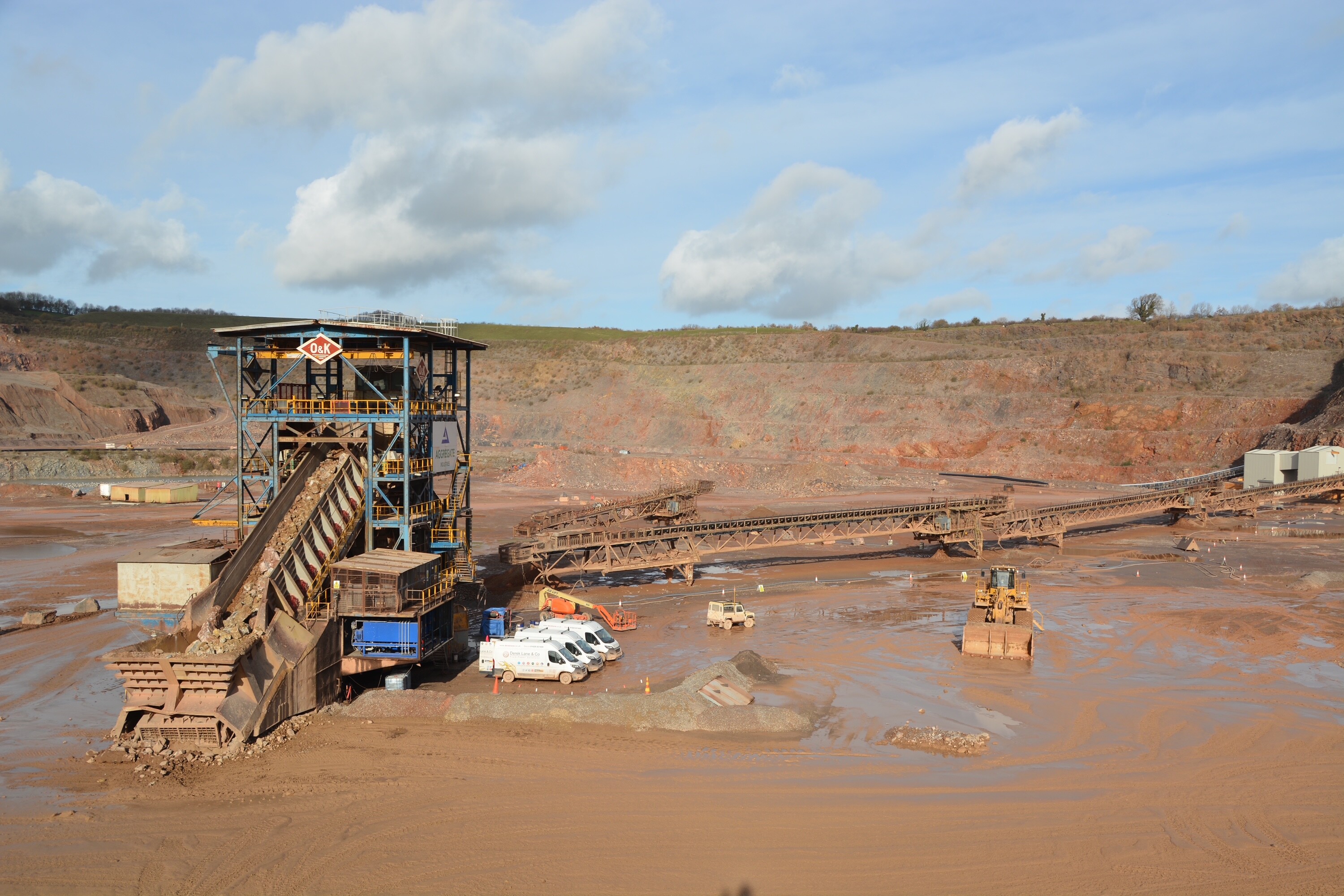
It is the only one of its kind in the UK and possibly even in Europe. The gyratory style crusher is capable of producing up to 3,000 tonnes per hour, but the secondary plant behind it can only cope with 2,000 tonnes per hour. It’s a hungry beast of a machine and the 992’s are usually kept very busy feeding it. A third 992G is kept in reserve as a back-up machine in case of any breakdowns as the quarry can simply not afford any downtime.
The two older 992G’s are both 2003 models, with one amassing 38,000 hours on the meter, while the other one is on slightly lower houred with 34,000 hours clocked up. During their time in service they have had Finning Certified Rebuilds on major components including engine, transmission and axles as part of the company’s preventative maintenance programme. Due to the fact that the quarry has an excellent workshop facility on site this work is carried out on site with the components being removed in the workshop and sent to the relevant Finning depot for the rebuilds.
The 992’s are fully operational from 05.30 in the morning up until 21.30 in the evening, covered by two shifts, with the operators changing in the middle of the day, so its long days for the operators and big hours for the machines as you would expect on such an investment.
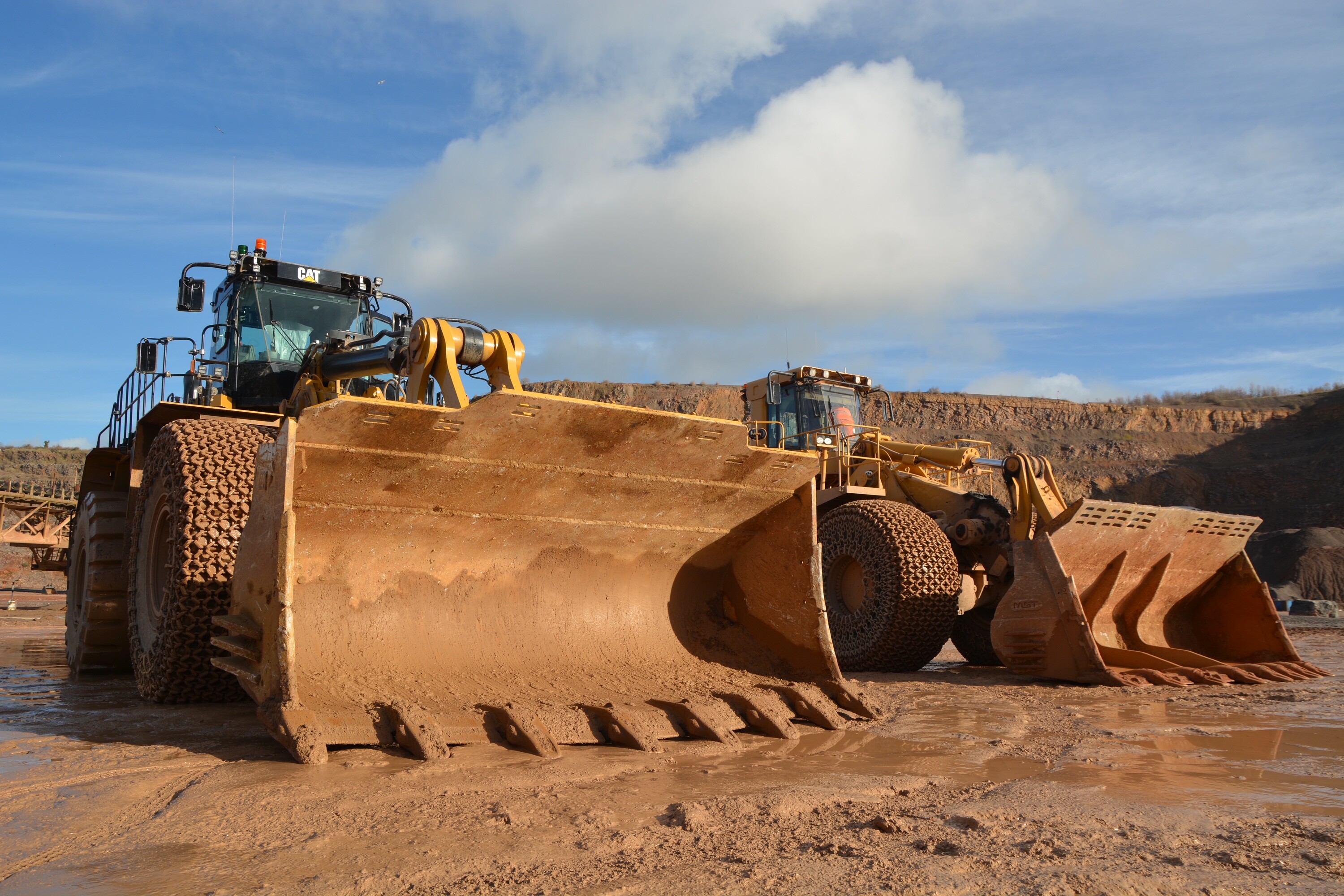
It was early days with the new K Series 992 at the time of our visit, but James Ashman has been delighted with it so far, he said, “Its been interesting being able to use the new technology, especially the Vision Link which is great! We can monitor the machines productivity and fuel burn straight away, something we have never been able to do before. We can monitor exactly what it’s doing per tonne in terms of fuel burnt and we are already expecting to see improvements compared to the old models, a 10% reduction has been talked about so we expect some significant savings to be made”.
James continued, “The early results have been impressive so it will be interesting to see how it goes over the coming months. Another great aspect for me personally as a plant manager, is that I can login to my laptop from anywhere, at anytime of day to monitor that machine if needs be which is incredible!”
As part of the deal the team at Torr have access to Cat’s Machine Control Software (Electronic Technician) which James explained further, “We have the electronic technician software here for our guys on site, which enables them to plug into the machine to see what’s going on if there is a problem, that in line assists me if I need to speak to the guys at Finning, I have all the detail and error codes so they would know what parts if any are required which further minimises any potential downtime for us, which as I mentioned before is crucial to keep to a minimum”.
.JPG)
It’s not every day that one gets up close and personal with what is the third largest wheeled loader in the Caterpillar range, so I was keen to take a look around the beast!
Starting at the business end, the 992K is fitted with the standard 12.3m3 (16yd3) bucket and has been supplied with Cat’s Advansys tip and adaptor system, which is a hammerless system making tooth tip changes easier and faster to complete, “bucket wings” are also fitted on the outer edges of the bucket. It came as a surprise to me that wear parts are not much of a problem in this quarry as according to James, the limestone is relatively low abrasion so bucket teeth will generally last up to a year with around, 9 months being a general rule, “We are lucky in the fact that we don’t really get through that much “GET” which is good for our business” said James.
The loader arm is of a single boom style structure for strength and durability but which also offers excellent visibility down to the bucket corners and the quarry floor.
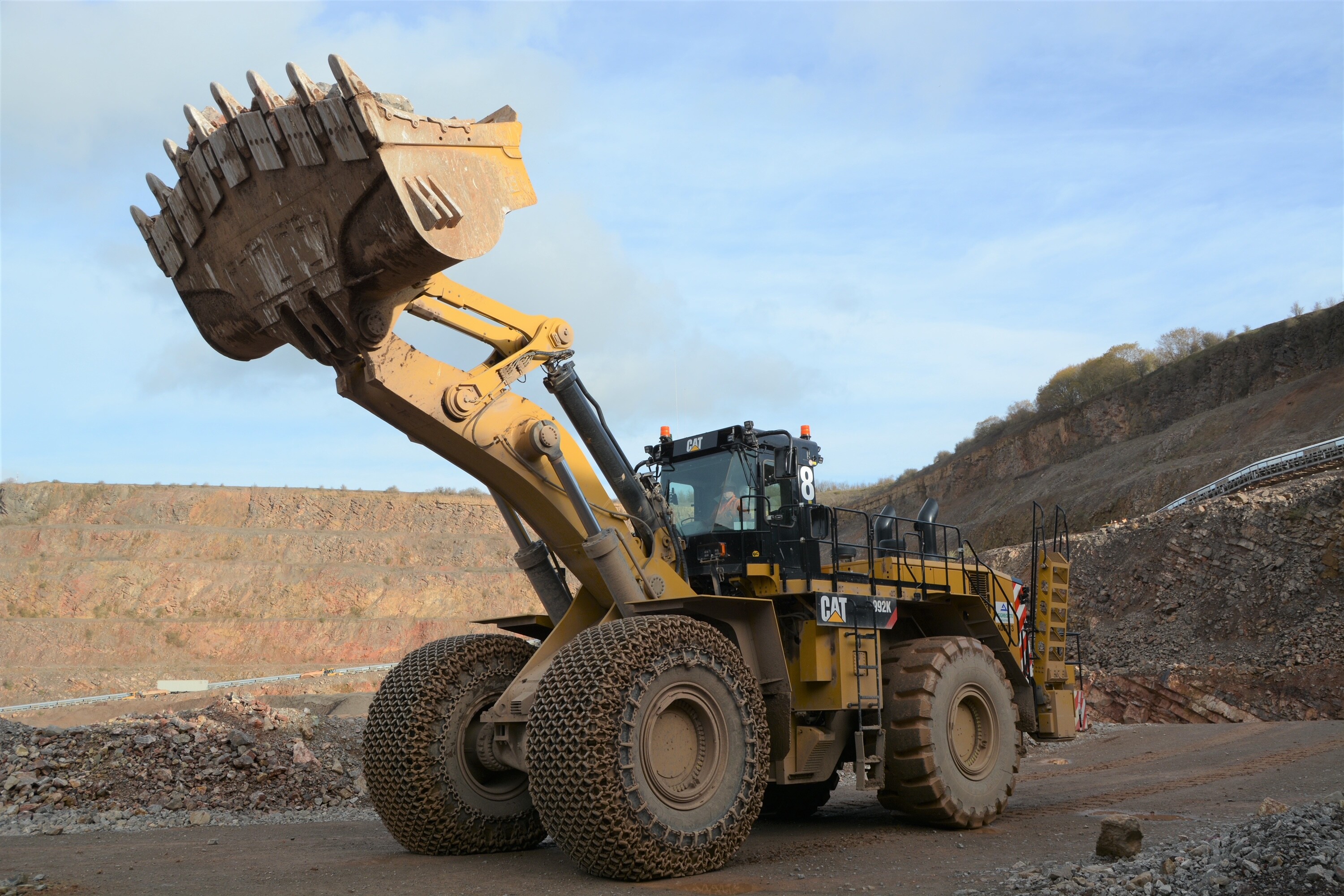
Tyre size is 45/65-R45 with the front set being fitted with heavy duty chains which are common place in this rugged environment, with these chains fitted it takes the operating weight of this giant to somewhere in the region of 100 tonnes.
Towards the rear of the machine we find the ground level fast fuel filler point, which cuts downtime when refuelling the 1,562 litre (413 gallon) diesel tank.
To the left of that point we find the electrically controlled access step ladder, the seven steps and integrated handrails guide the operator up onto the machines first platform as he makes his way to the cab via a second set of seven steps. On the lower platform I opened the engine bay side door panels to catch sight of the Tier 4 emissions compliant Cat C32 ACERT V12 diesel engine which offers a power output rating of 607kw (814hp) @1,750rpm. Serviceability is great on this machine with filters all grouped together and within easy reach for the engineers when servicing and for operator’s daily checks which can all be performed from the walking platforms.
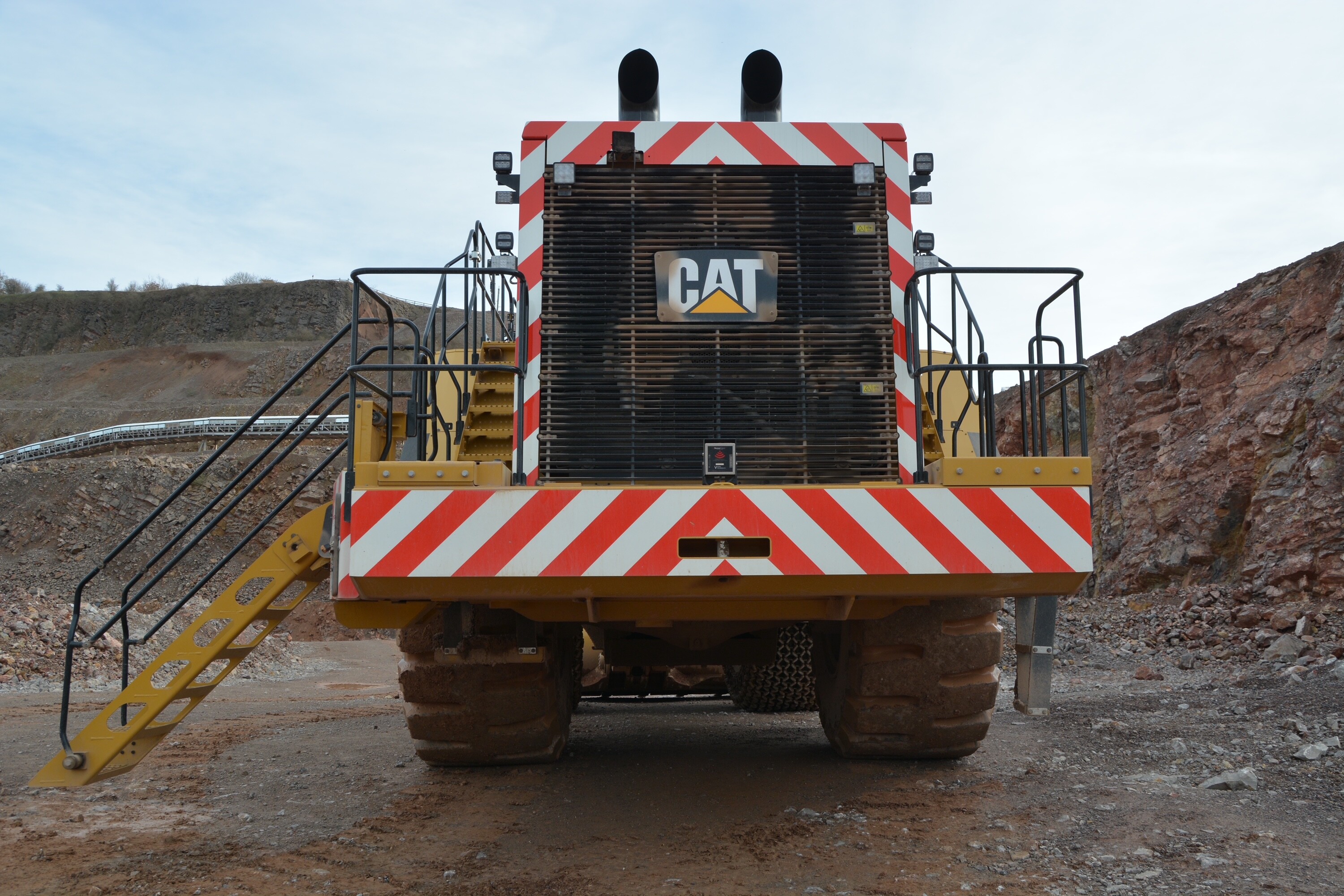
On the upper level platform, the operator finds an electrical switch which he needs to use to fold up the access steps. Unless these are raised the machine cannot be started, a great safety feature which ensures there are no incidents involving bent of broken steps.
The cab has a spacious feel to it, with a comfortable air suspension seat offering a commanding view out the front and side windows, a trainer seat is also located to the left of the operator’s seat so a passenger can be carried safely if needed.
The machine looks very operator friendly; there is no steering wheel which is becoming more and more common on machines these days, especially on those from the Caterpillar stable. All steering, direction of travel and gear changing is done via the joystick mounted on the left-hand armrest, which I must say felt incredibly intuitive. On the operators right there is whole bank of controls for various sub systems and on the right-hand armrest one finds the two bucket and loader arm control levers.
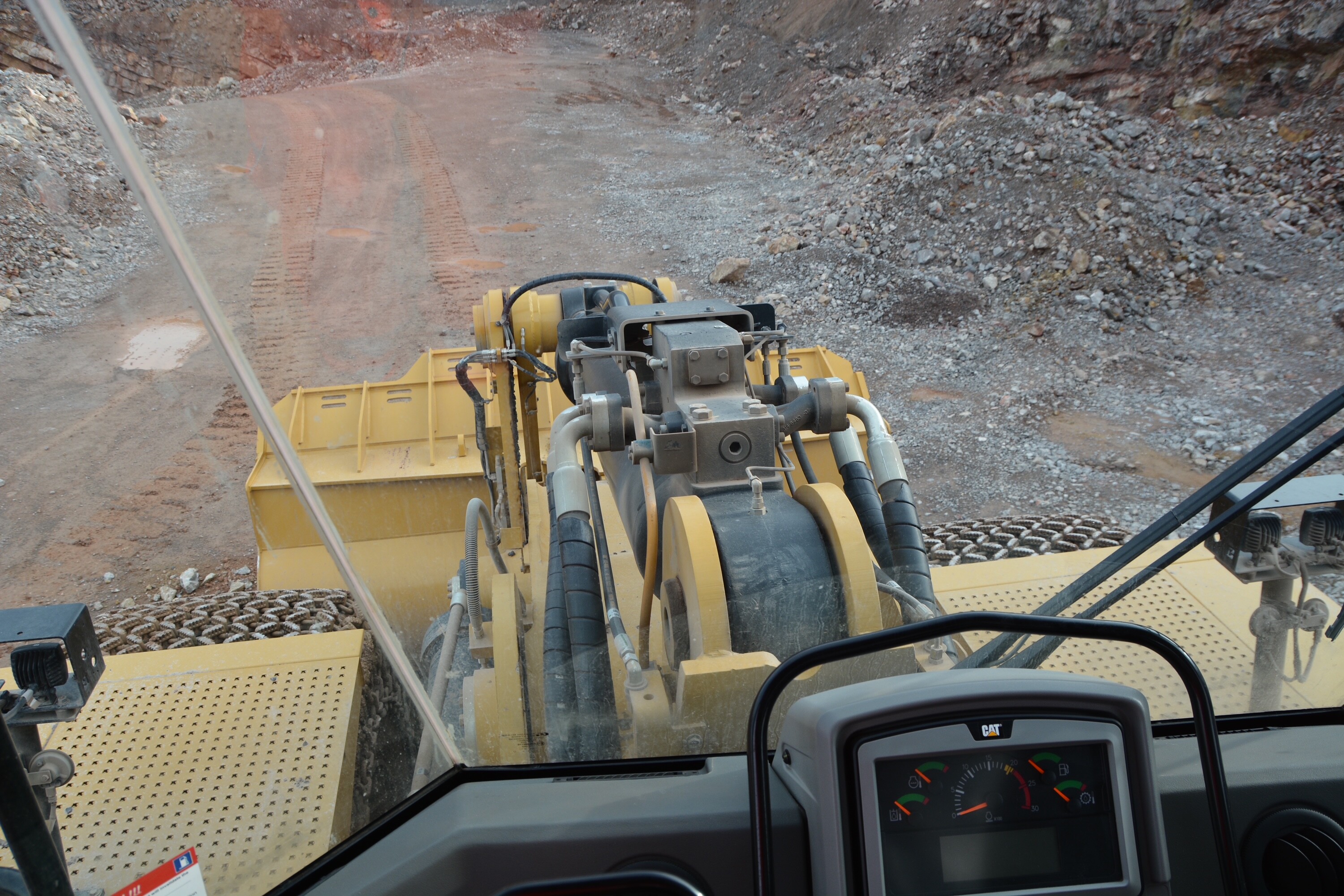
A rear-view camera monitor is mounted in the cab for use in conjunction with the substantial wing mirrors and a built-in monitor is included for the machines integrated “Payload Control” weigh-loading system. Al in all you would have to say this would be a pleasant cab to spend in this instance, long days and nights in.
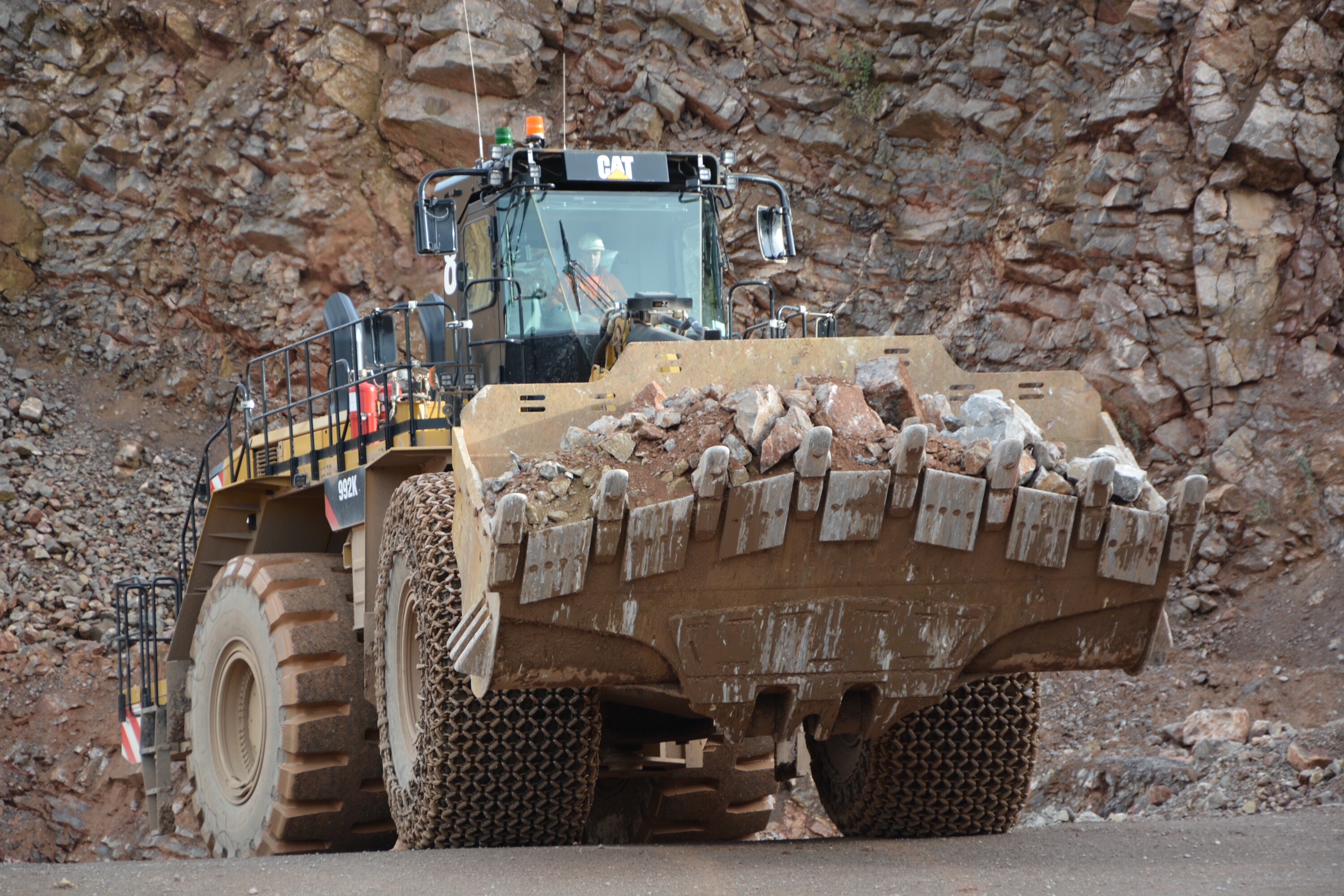
These machines make for an impressive sight as they go about their business feeding a very hungry crusher and I would imagine it’s only a matter of time before another K Series machine replaces the now ageing G Series models in this quarry. Demand for stone from the quarry looks good for the future, so it will be another busy period for Torr Works big Cat’s.