by Nick Drew | Wed 20 Jan 2021
Compact Recycling Solution
Taking a look back at one of my Earthmovers articles from last year, bringing it to life on the internet, un-edited and with alternative photos and video footage.
In a story that could possibly resonate with many individuals today during these challenging Covid-19 times, there is often hope around the corner and the chance to move on to bigger and better things.
For Ben Wyatt, Managing Director of Ringwood & Fordingbridge Skip Hire Ltd, change came about after he was made redundant from his then current job in 2007, when he saw an opportunity to purchase a second hand skip lorry to repair and then added 5 skips which he purchased from another company in Romsey. Armed with one truck and the set of skips he founded Ringwood Mini Skip Hire. Some 3 years later Ben took over the existing business of Fordingbridge Skip Hire and shortly after he merged to the two businesses into one.
In 2011 they established a waste transfer station in Fordingbridge and just kept building the business from there. Today they run around 10 trucks and in excess of 1000 skips covering Hampshire, Dorset and Wiltshire, in addition to a sister site in Calne, Wiltshire, called RF Wood & Waste Recycling.
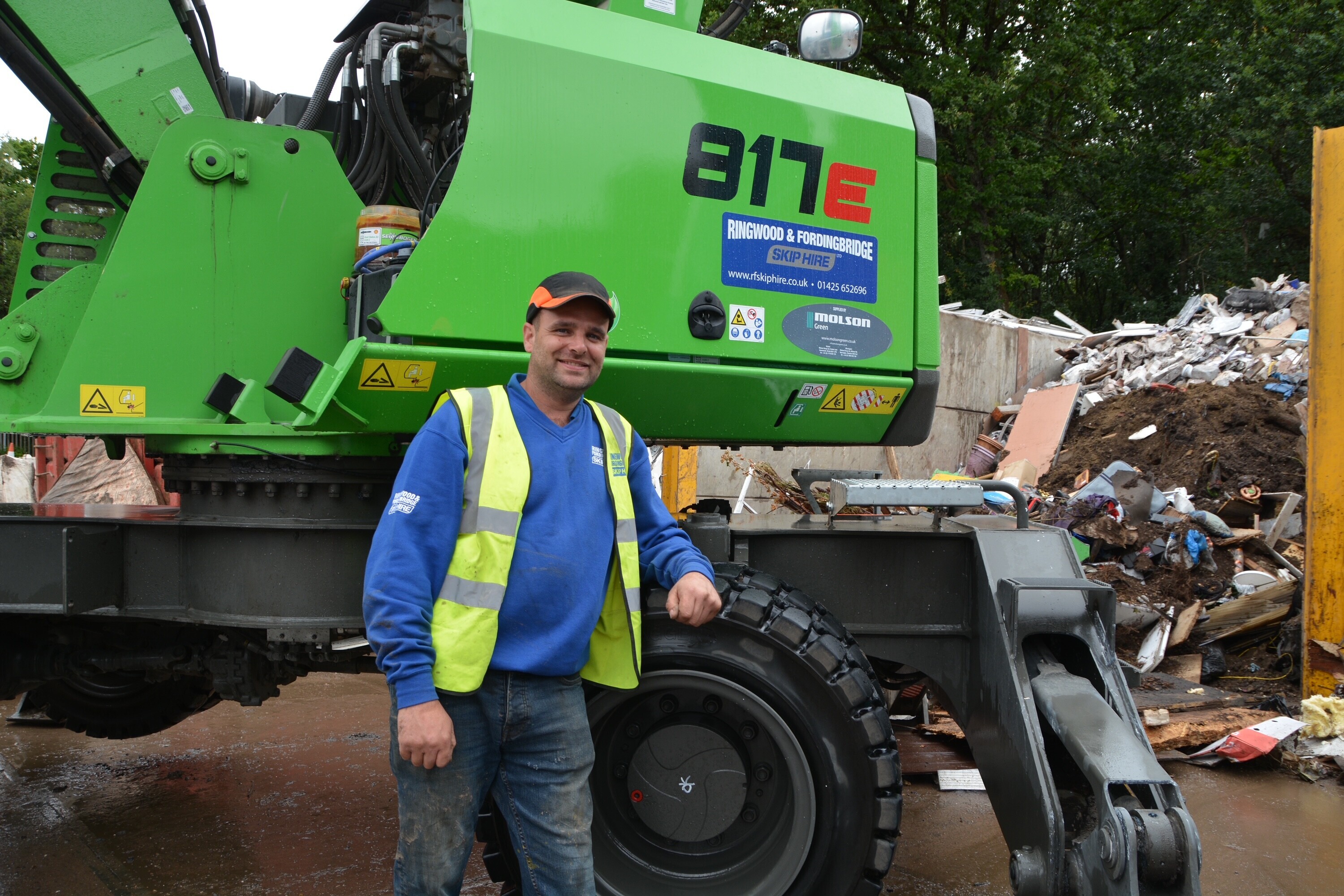
Today the business just continues to go from strength to strength and as a reflection of that, the company has just invested in more new plant and equipment which will enable them to remain on top of their game. We caught up with Ben and his Yard Manager Dan Stroud in the bustling recycling centre hidden away in the glorious New Forest on what was an incredibly damp day in Hampshire.
It is estimated that the facility processes somewhere in the region of 35,000 tonnes of waste per year but they are licenced to process anything up to 75,000 tonnes per annum.
According to Ben, customers are generally a 50/50 split between domestic and commercial, but in addition being based in the New Forest they are lucky to have so many local customers who prefer using them due to the fact they run smaller lorries that suit their small driveways.
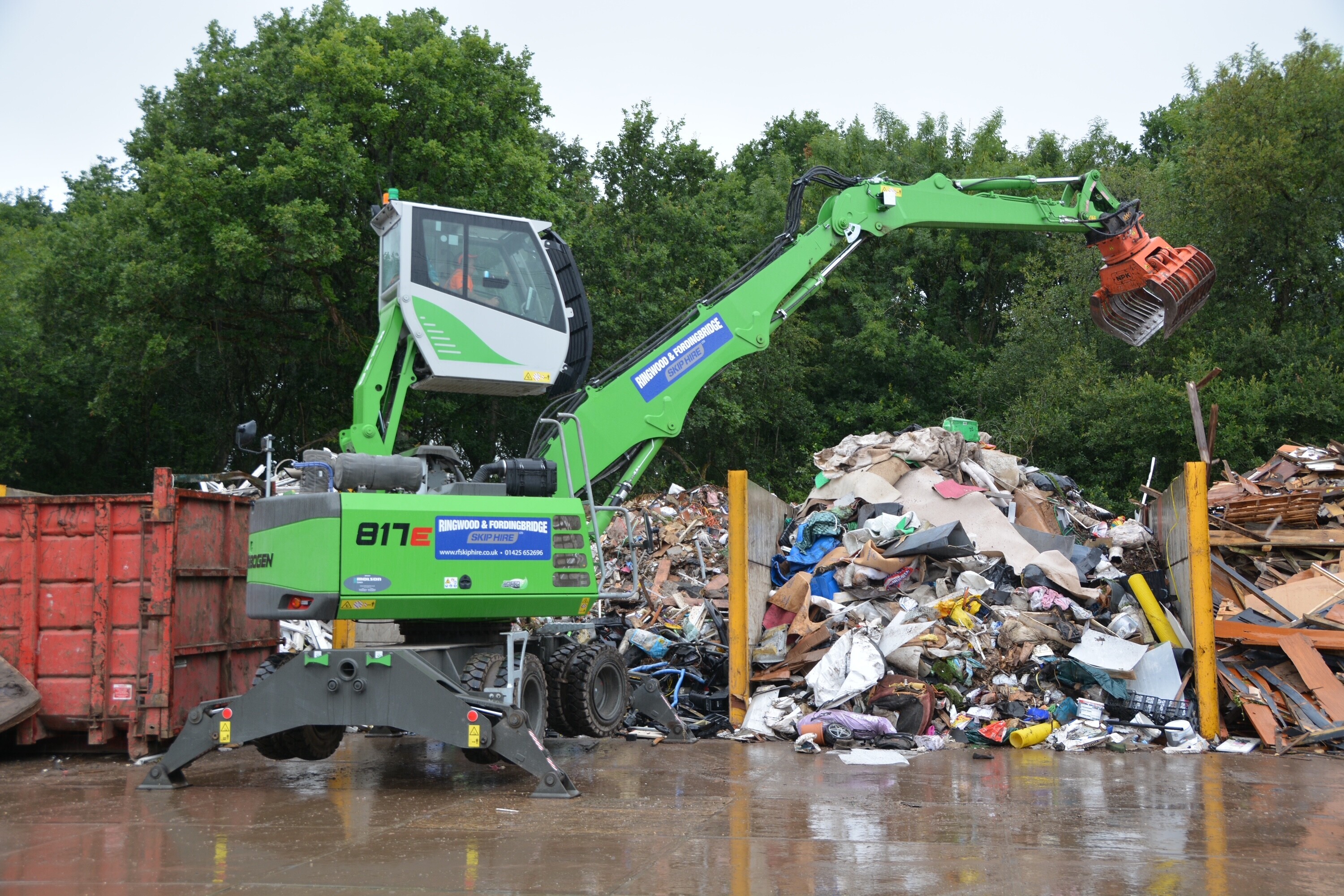
During the Covid lockdown period they saw a massive rise in domestic waste, with lots of people being off work furloughed, they noticed people had decided to do work in their gardens, which they had previously put off, then with time on their hands they had obviously started renewing fences, sheds and doing general building work. Ben said to keep up with demand they had to add another 100 skips in the two months to cover the additional work. They also had to order two more additional lorries.
The company has recently invested in two new machines, a Sennebogen 817E materials handler and a Kobelco SK75SR. They have gone for all new machines as they simply cannot afford to have breakdowns in such a busy facility. Ben said, “All we want is new reliable machines every three years, serviced and maintained that keep working, especially as we run a compact yard, if we have a machine go down, we are really stuck, as the skips just don’t stop coming in, so reliability is the key for us, we chose to go with Molson Equipment for the back-up and the service contract package they provide which really suits our needs”.

This yard really is a bustling operation and during the time of our visit trucks never stopped arriving. Undercover in the open fronted shed the company run a Baughans Majorette trommel system with a manual picking line which runs around the edge of the building. This British built system has the capacity to screen around 50 – 100 tonnes of waste per hour, so anything up to 60 skips a day.
Waste is segregated initially using a combination of the Sennebogen 817E material handler and the Kobelco SK75SR, that pick their way through the larger items of rubbish, what’s left is then pushed into a heap with the JCB telehandler, which coincidently, was another second hand purchase from Molson, this material is then loaded into the feeder by another Kobelco SK75SR, the material then progresses along the picking line, where it is manually hand-picked by a team of 5 operatives along the top belt, there are also outlets for such items as carpet, cardboard, hard and soft plastics, and all other materials in between including ferrous and non-ferrous metals.
Wood is separated to go off for biomass, plasterboard goes off for recycling, rubble goes off for crushing, the inert material goes off for screening, and the trommel fines are used for landfill cover, so apart from the trommel fines, nothing else goes to landfill, so the company claim to have a 95% recycling tally.
The wood content is transported up to the company’s sister facility in Wiltshire where it is shredded, screened, processed and dried using their own biomass boiler, to be sold on as a quality biomass product.
Machines.
Previously the company had run a mixture of CASE and JCB excavators, including a CX75C SR model and 86C-1 respectively, both fitted with grabs and a larger 13-tonne class JCB, but these machines have now been traded in for the new kit, all of which have been supplied by Molson Equipment with the exception of the small CASE 321F compact wheeled loader which is still very much a part of the team of machines in Fordingbridge.
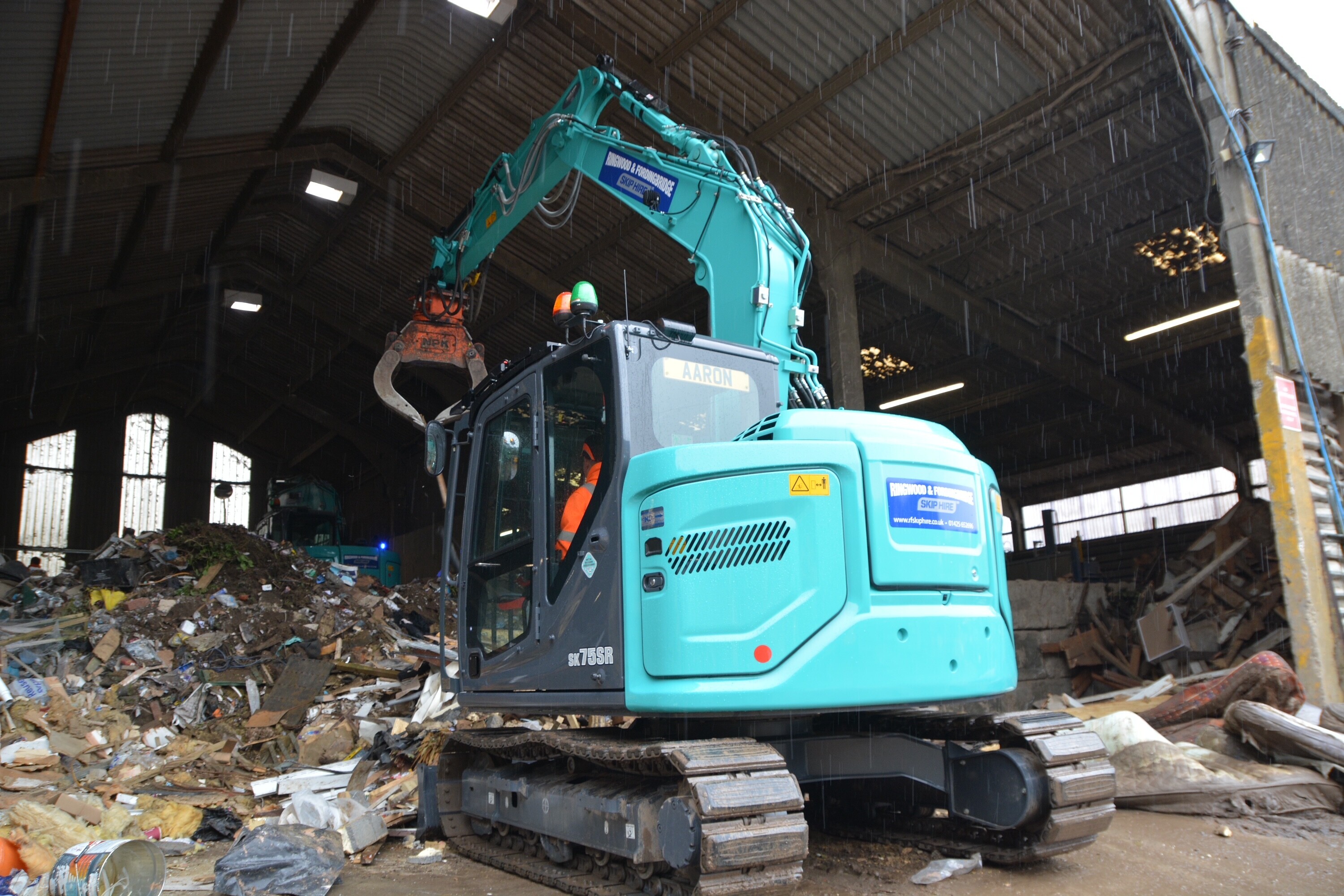
Having Molson doing a service package deal means peace of mind that they are well serviced and maintained to the highest standards ensuring that the history of each machine is well documented which means they will hold a much better residual value when its time to change.
The latest additions to the fleet are the aforementioned Sennebogen 817E and another Kobelco SK75SR talking about the German built machine Ben said, “We had a Sennebogen on demo from Molson’s for about two weeks, but we knew within the first 10 minutes of using it, that this was the machine for us, we immediately put in the order for one, but then of course we went into lockdown so delivery was delayed, but the machine eventually arrived in March during the lockdown period.
The good thing with the Sennebogen is not only does it pick skips all day, but it can load high sided trucks much more efficiently due to being able to see into the back of the wagon thanks to the elevating cab design”.
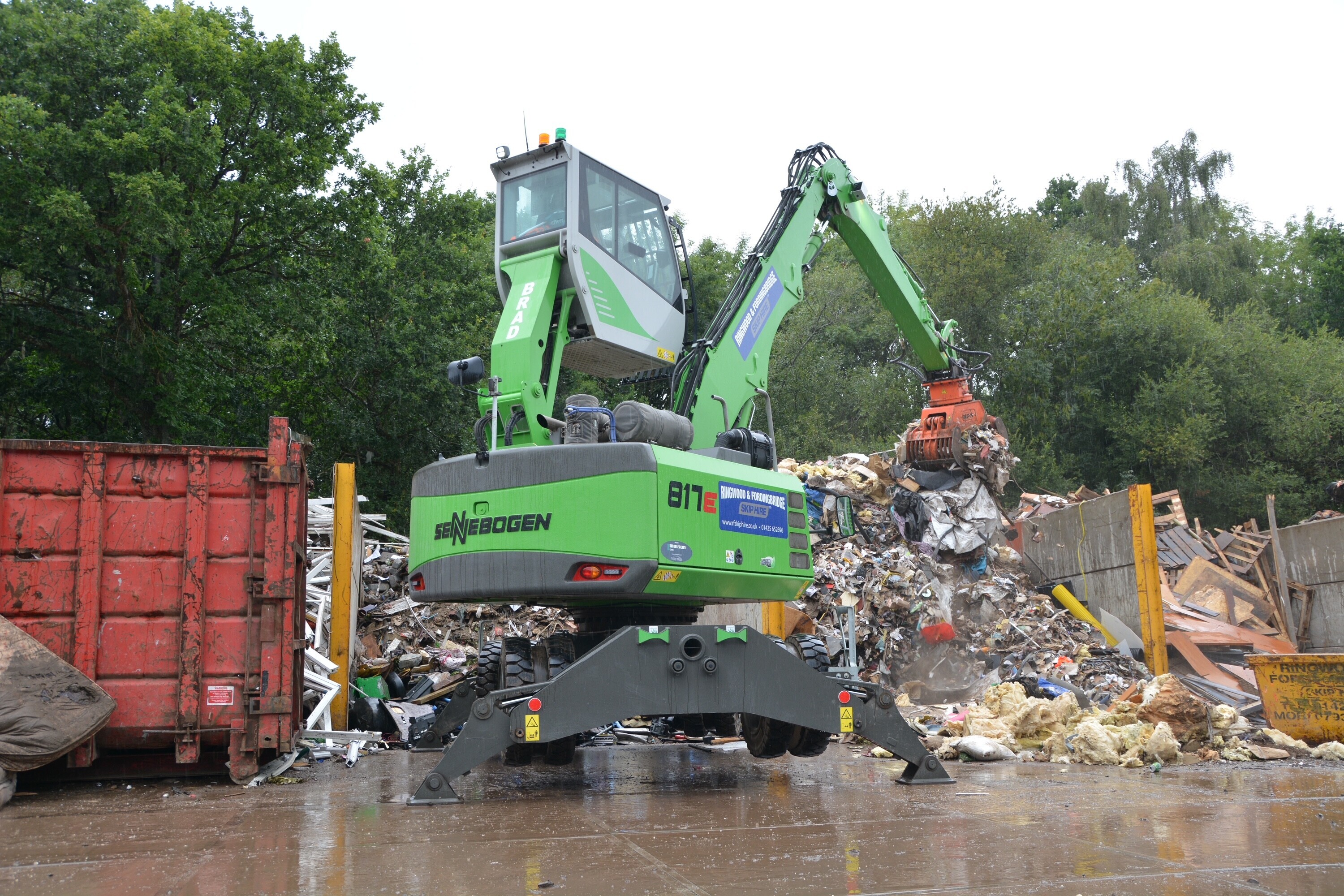
These two units have been supplied with Japanese manufactured NPK grabs which have already impressed the team with their strength and durability, with the exception of one fault with an internal clamp that came undone causing some hose damage, which has been rectified under warranty.
Ben commented, “The machines have been excellent so far and apart from a couple of tiny teething issues, we have had virtually no problems at all, and the small problems we did have were rectified in record time by Molson’s and that’s all we ask really, that if we do have a problem, that its sorted ASAP! Molson have been great for us and our local salesman Tristan Dorey is a good guy to deal with at the end of the day”.
One thing that strikes you as you walk into this particular recycling yard, is the quality of the machinery, lets face it, the waste recycling industry is a tough application for any equipment but at Ringwood and Fordingbridge they have recruited a great team of young operators who really like to take pride in the machines they are operating.
Talking about the operators Ben said, “We have young Brad Gillard (22) on the Sennebogen, he came with us straight from school, and we trained him up personally on a machine, he started on the heap in the shed loading the feeder, we later moved him down onto the Kobelco “picking” and he is now the lynch pin of the whole operation in the yard on the 817E which is really our flagship machine here now”.
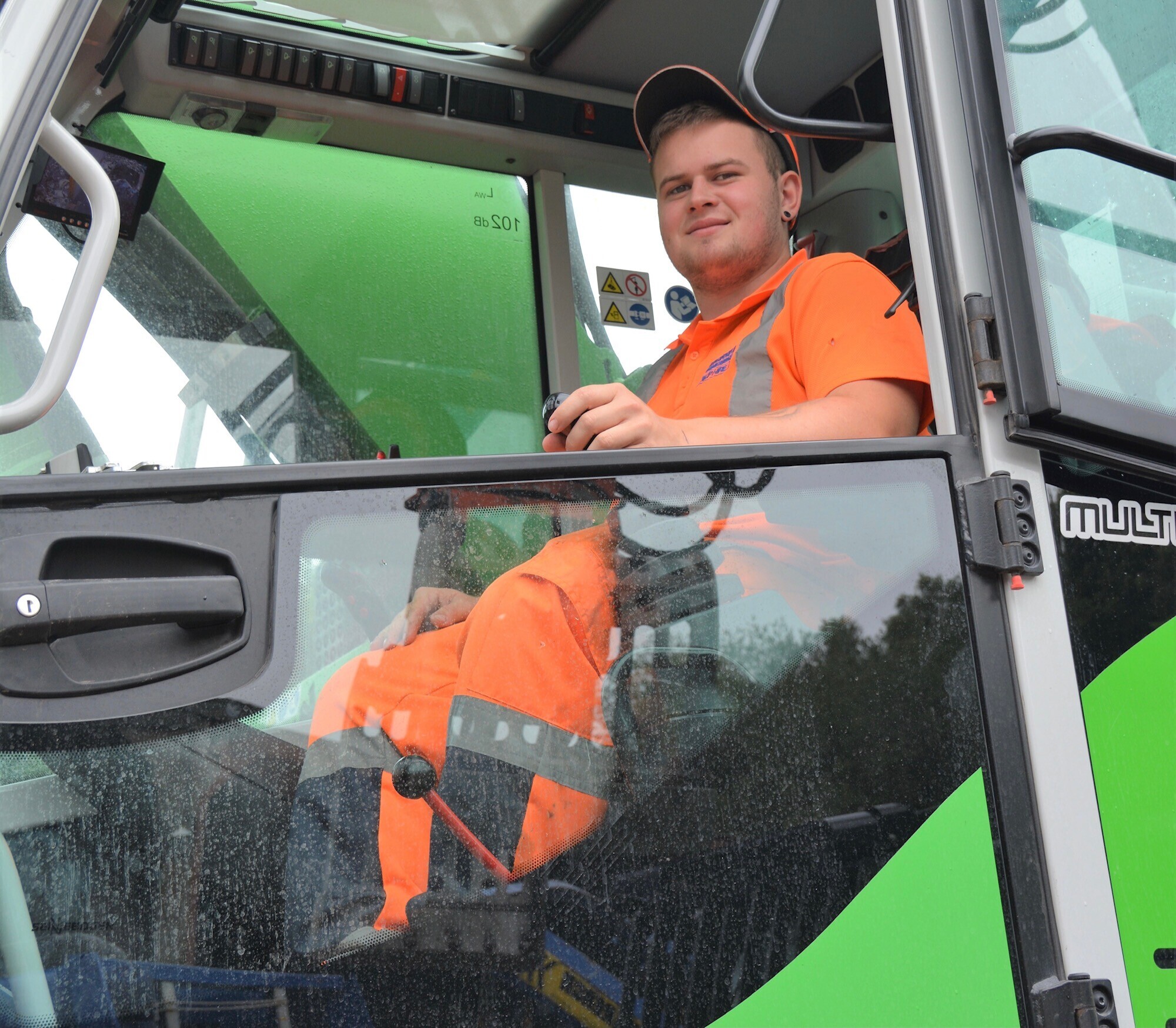
Photo: Young Gun operator on the Sennebogen Brad Gillard.
Ben continued, “Another one of our young guns is Aaron Wyatt (21) who is now on the latest Kobelco SK75SR, like Brad, he started on the ground as a picker, then progressed to become the shovel driver, before moving on to loading the feeder with the first Kobelco, before taking on the new machine in a “picking” role.
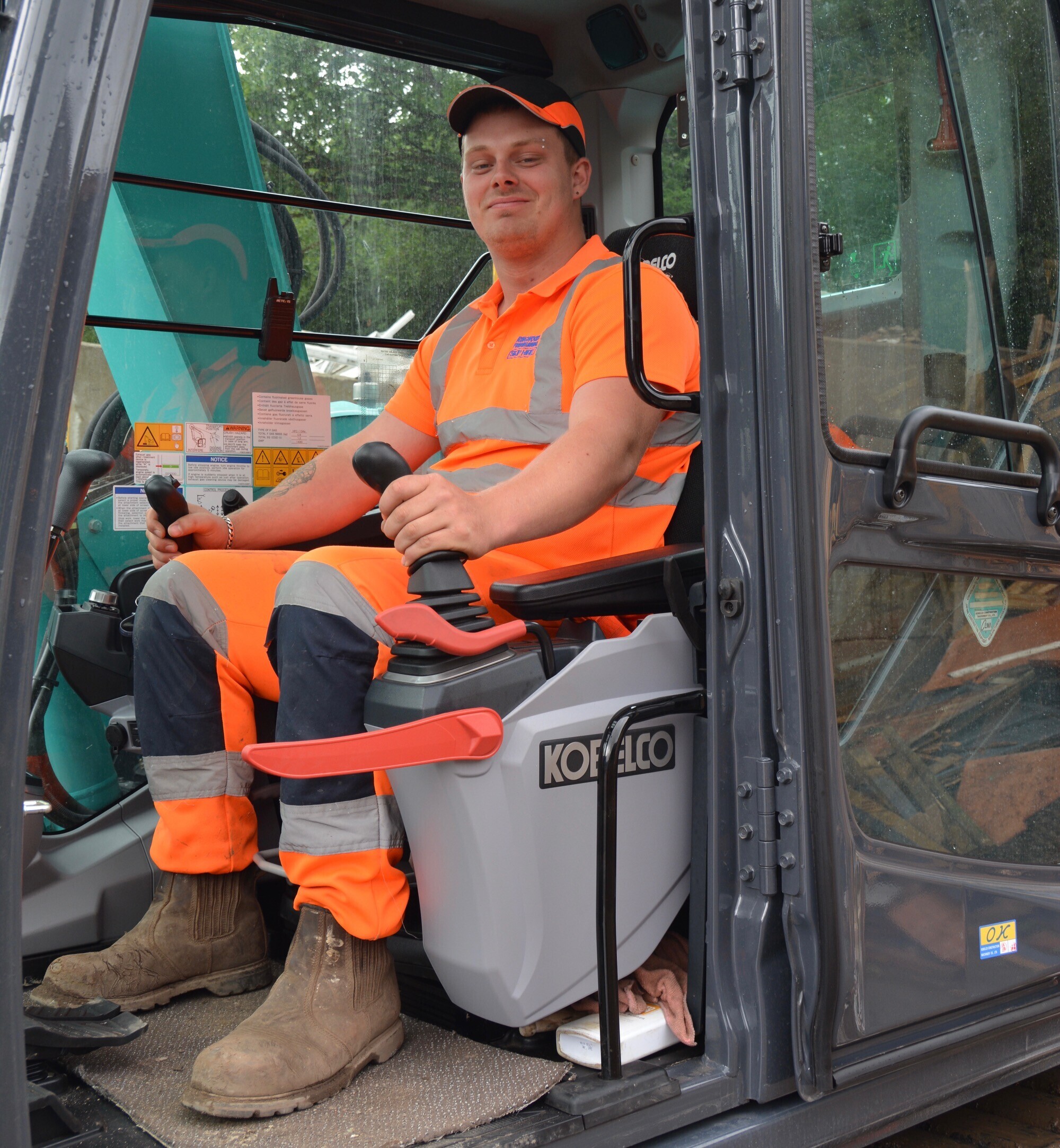
Photo: Fellow Young Operator on the Kobelco Aaron Wyatt.
We also have another newbie, who has recently done his tickets, Leon Thorne, who is now in the 18 month old Kobelco on the heap loading the feeder, he is another lad who joined us in a manual picker role, who has proven to be willing to work and adapts to whatever role we have given him so we have offered him the chance like all our other lads to improve his skills and reward him for it, at the end of the day we want all our staff to be professional, competent and safe, so we have invested in 5 young machine operators, putting them through the courses to obtain the relevant tickets”.
Both Ben and Dan are fully qualified and long term operators themselves so if the need arises they will jump on the machines if someone is out sick, Yard Manager Dan said, “At the end of the day it’s a busy site, and we have to keep the wheels turning, in addition being so compact we really have to keep on top of things, so sometimes it’s a all hands on deck approach and we all muck in!”.
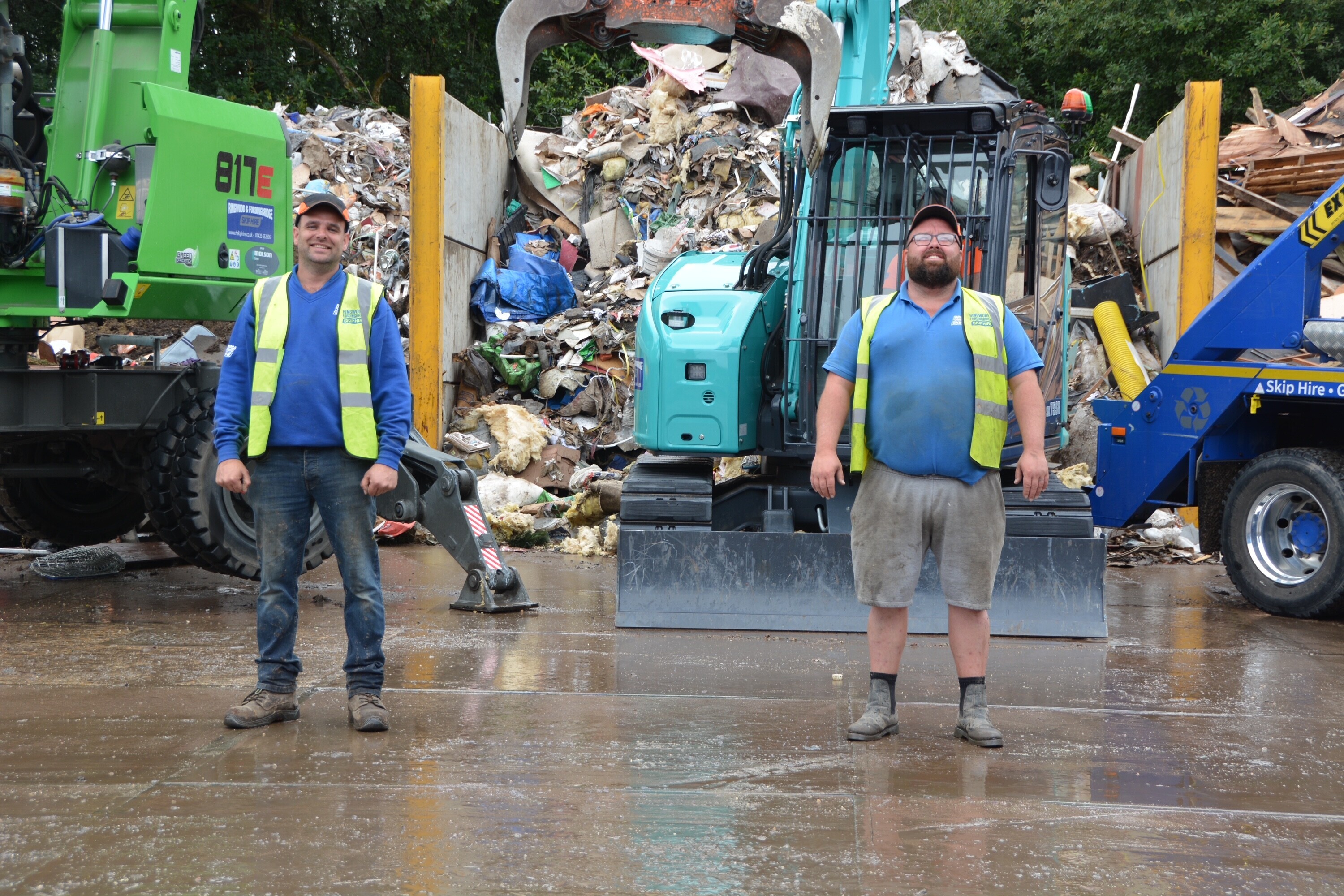
Photo: Managing Director Ben Wyatt (Left) and Yard Manager Dan Stroud.
Regarding the picking line, the guys maintain that themselves and stock many of the spare part components that might be required from time to time in the workshop, the line is approaching 10 years old now, so the guys are already drawing up plans to replace it in the future, which will possibly be next year now.
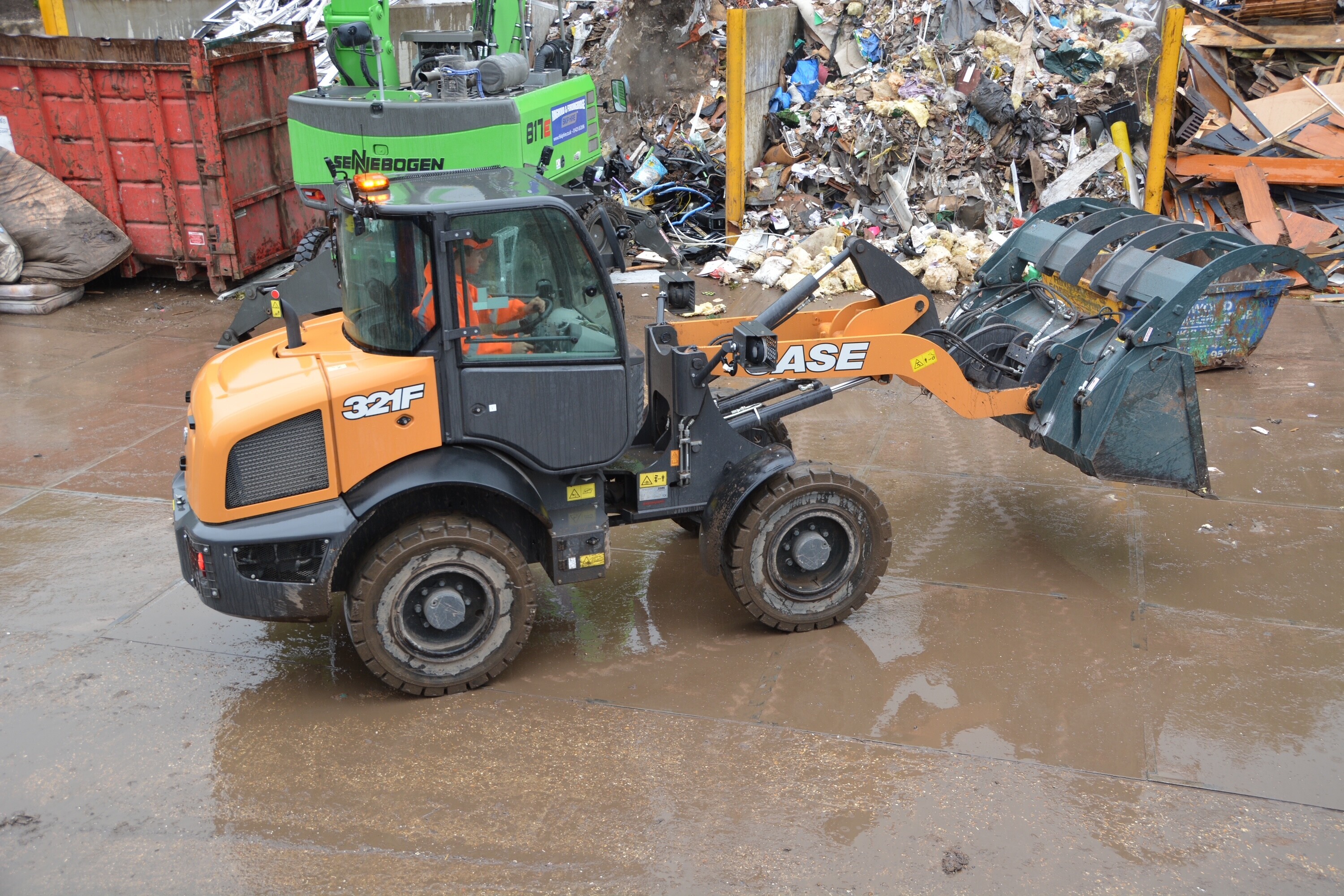
Its quite evident that the new Sennebogen is the star of the show, asked what made them go for the distinctive green machine Ben said, “Well we did initially look the Liebherr’s and the Fuchs models, but we felt that they were just that little bit too big for our small ¾ of an acre yard, whereas the Sennebogen is really compact with a very small rear radius overhang, that machine can go into one of our 5 metre bays and turn 360 degrees with no problems, it was really a bit of a no brainer!”.
Built in Sennebogen’s Bavarian factory in Straubing the 817E is the smallest example in the German manufacturers 15 model material handler line up. Weighing in at 17.2-tonnes the machine has a 9m reach and is powered by a Stage V EU emission’s compliant 3.8 litre Cummins diesel engine which offers a power output rating of 97kw @1800 rpm. As mentioned by Ben previously, Sennebogen’s MultiCab stepless elevated cab system which can be raised infinitely up to a height of 2.40m offers great all-round visibility.
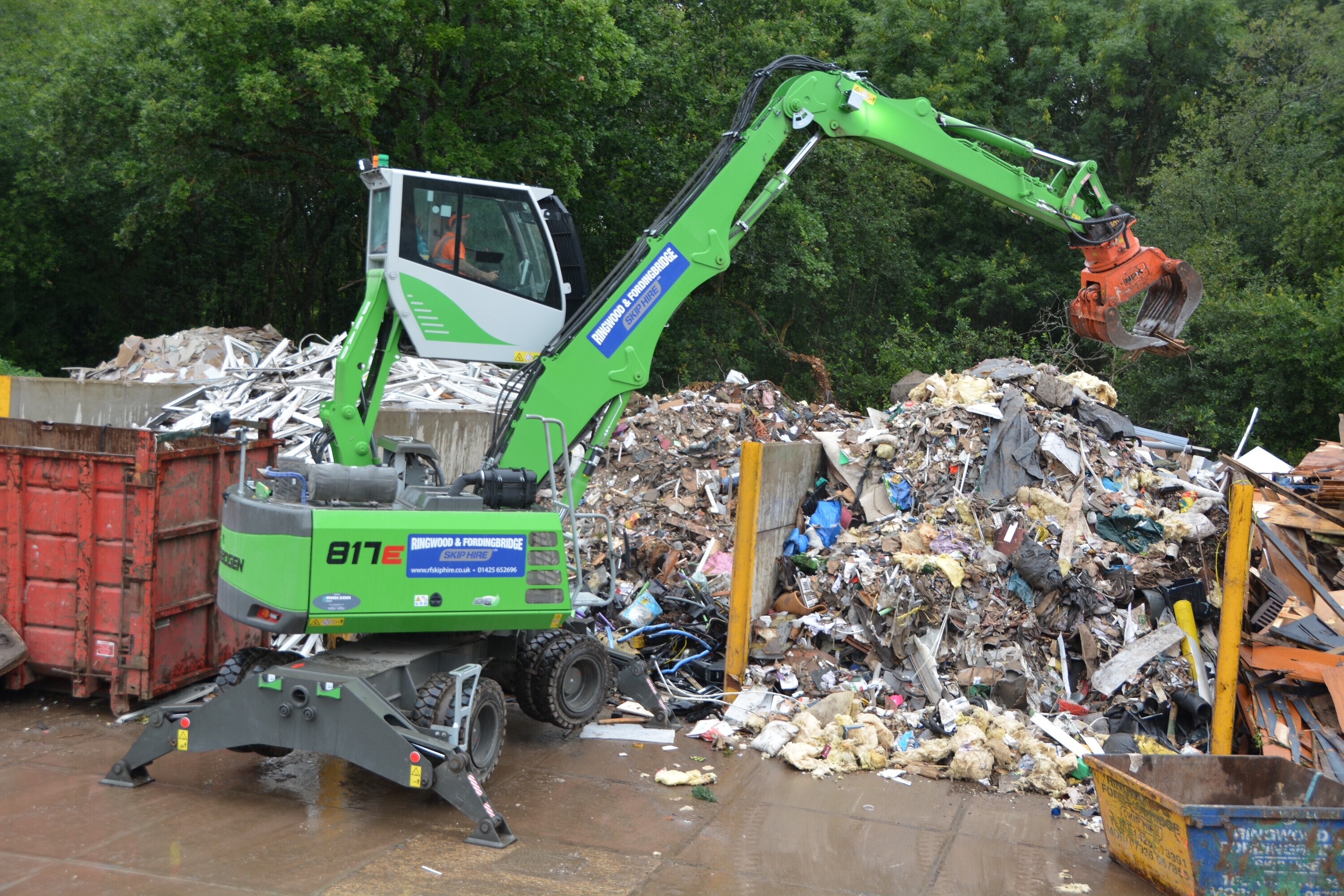
The company’s first Kobelco SK75SR has served them very well and the brand-new model which also bares the operators name in the back window is expected to be equally reliable. Power for these ultra-reliable Japanese machines comes from the ever popular 4-cylinder Yanmar 4TNV98CT diesel engine which produces a power output of 53.7kw @2,100rpm.
Another great feature on these machines which is especially appreciated in this often dusty, application is Kobelco’s iNDr (Integrated Noise & Dust Reduction) cooling system. The high-density mesh filter prevents dust getting through to the cooling packs and air filter.
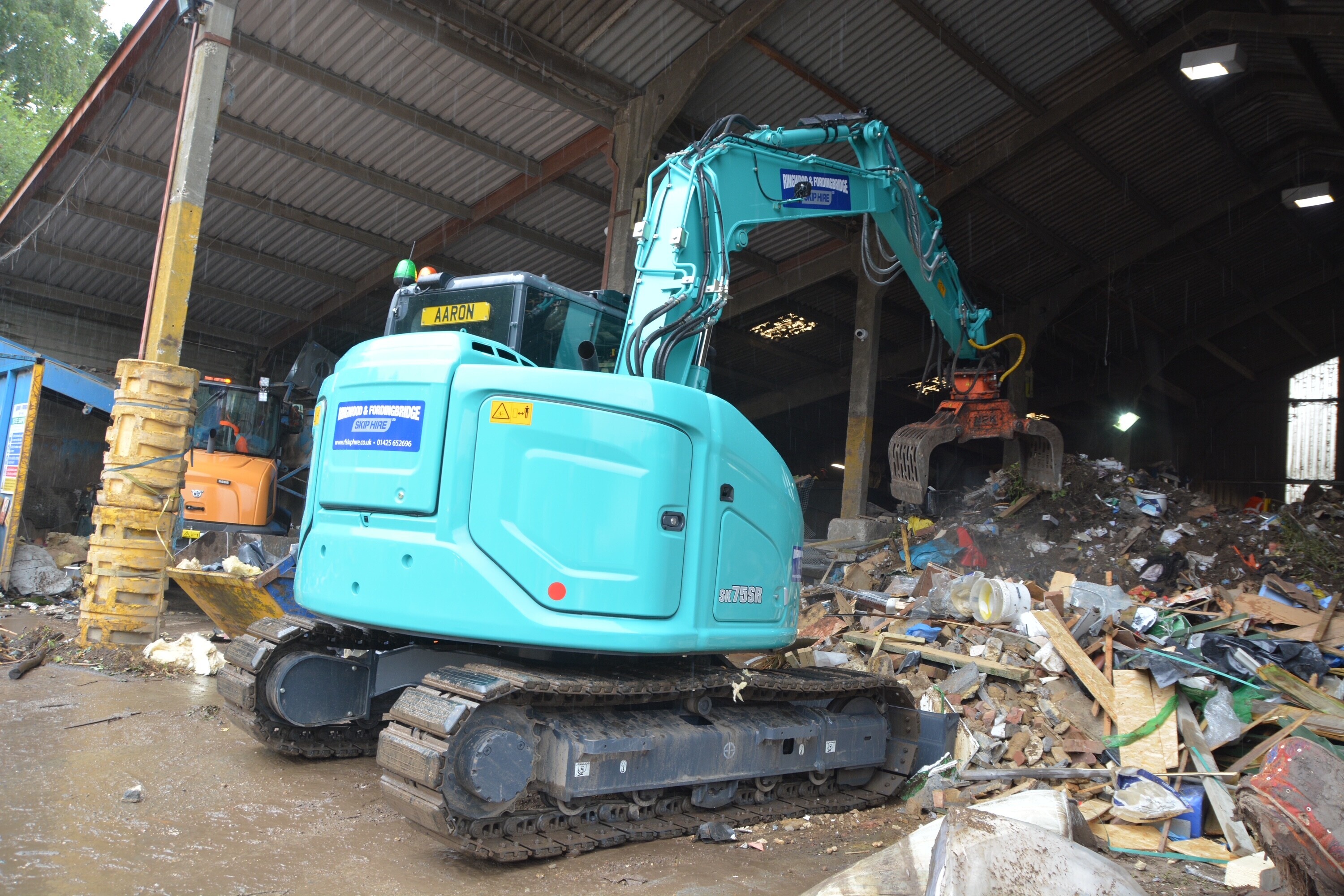
Armed with these new machines and a great team around them, the only way is up for this well-respected waste recycling firm. Summarizing Ben said, “I would just like to take this opportunity to thank our staff who all work incredibly hard to really recycle everything that arrives at out yards, we simply couldn’t do it without them”. From what we saw and heard on the day the future is definitely looking green and blue for Ringwood & Fordingbridge Skip Hire!
Checkout our video of the Sennebogen 817E in action.