by Kyle Molyneux | Thu 28 Nov 2019
Pioneering resurfacing work at Silverstone
Silverstone circuit in Northamptonshire has set a new standard for the finish of race tracks, thanks to pioneering resurfacing work carried out by lead contractor Tarmac, along with its road planing business, NRP, race track specialist Dromo and project partner Topcon Positioning Group.
NRP took the lead on the milling project, working with Topcon Positioning Group for its advanced SmoothRide machine control technology and to ensure that there would be, quite literally, no bumps along the road. Not only that, but the team needed to alter the entire camber of the 5,500m-long circuit to optimise water run-off.
Although the SmoothRide 3D analysis hadn’t previously been used on a race track, Tarmac, NRP and Dromo recognised the potential of the precision technology which had proven itself on highways and airport runways. It was to be the first use of the technology in the UK.
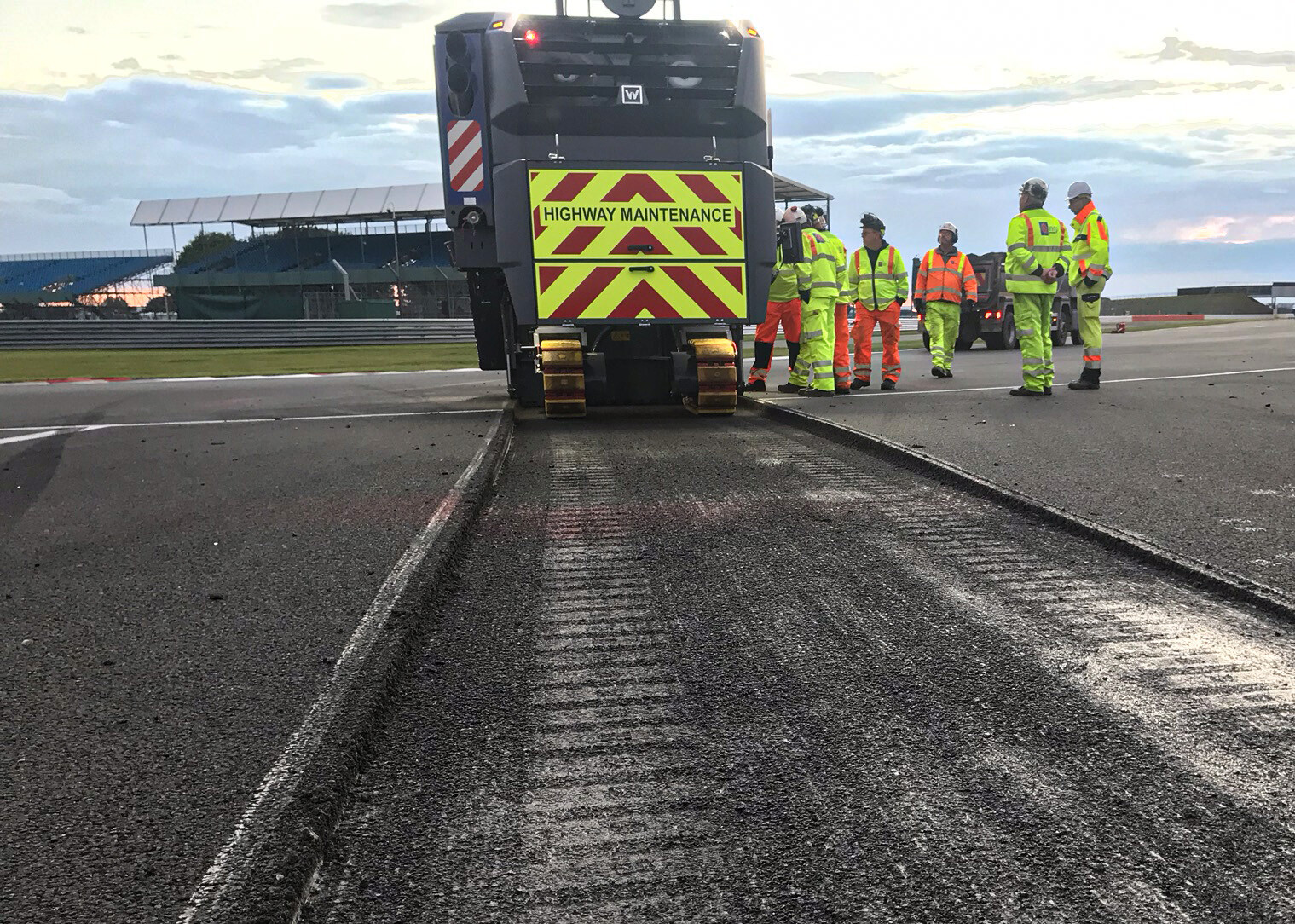
The project team first carried out a scan of the existing surface to precisely identify where any bumps were and where standing water might be likely. This scan data was then converted into a 3D digital terrain model (DTM) using Topcon’s Magnet Collage software, with the model being used to inform the new design. It was decided that milling machines would be used to shape the new track as they can make the surface extremely level, meaning the subsequent paving can be done in a constant layer thickness. This has advantages not just for the placing, rolling and compacting of the material, but also for the actual lifespan of the surface.
Normally, a surveyor would need to spend days staking out all the milling depths and the crew on the machine would then need to manually make sure those numbers are adhered to. However, this was all avoided with Topcon’s RD-MC Machine Control system. Firstly, Magnet Office and 3D Office were used to create the files needed for machine control from the design. The system was then able to use GNSS positioning to accurately calculate the difference between the existing surface and the new design at any given position, and therefore determine the desired milling depths. Sensors on the machines – in this case, two Wirtgen W210Fi machines – were used to pinpoint the current depth of the milling drum on both sides then, based on the desired depth and the actual depth, the machines were told to move the drum up or down.
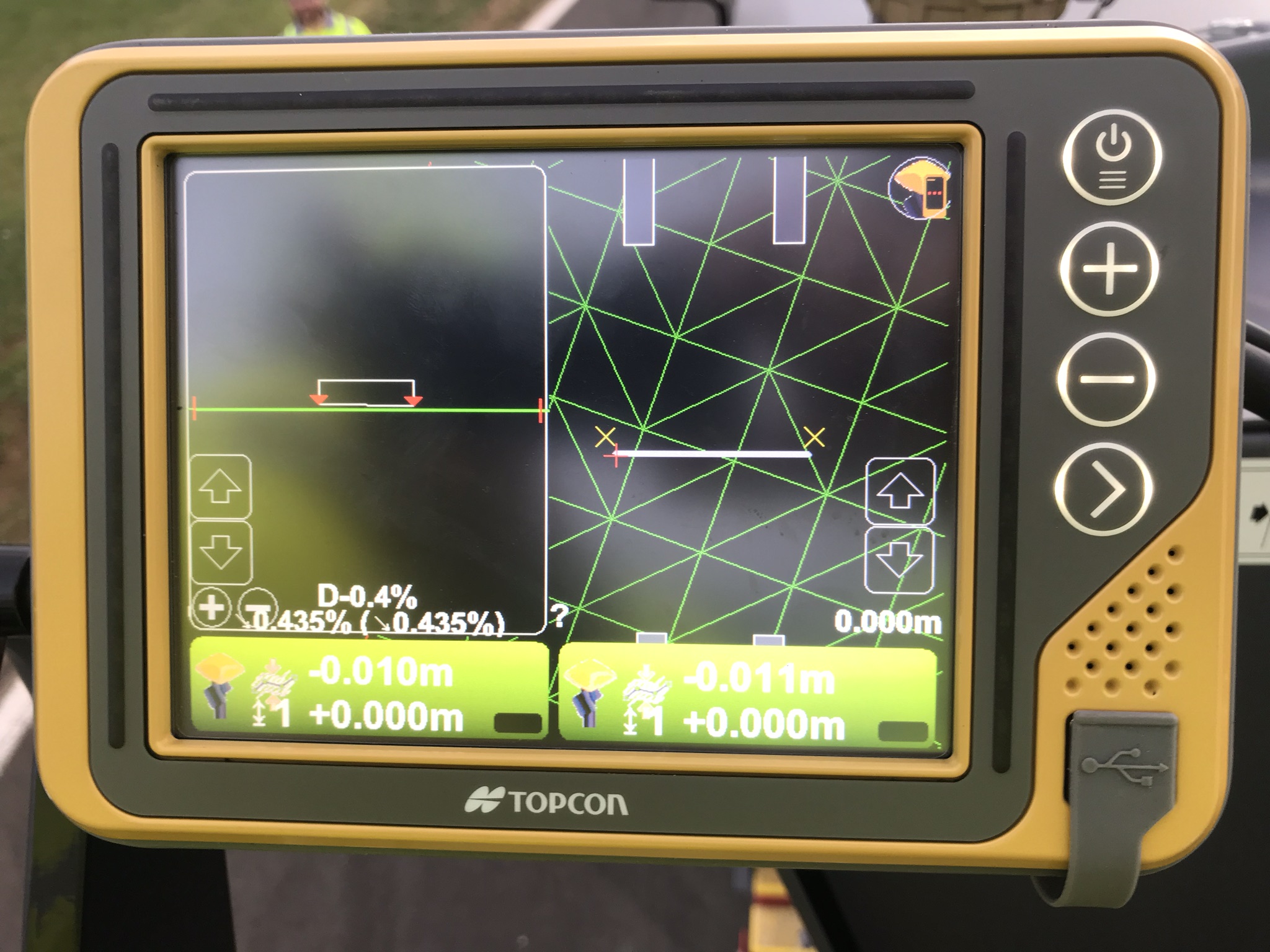
Milling of the 87,000sqm track took just three days and two nights, and left a seamless, smooth subbase that reflected the 3D design perfectly, achieving a level of quality that would be virtually impossible using traditional methods. There was also no need for surveyors to paint depth numbers on the asphalt or create stringlines to mill to, saving days of survey work. And, because the milled surface was so accurate, Tarmac was able to precisely calculate the amount of material required when it came to paving using its state-of-the-art BPO ASPHALT management system.
Got a news story? Email news@earthmoversmagazine.co.uk.