by Kyle Molyneux | Thu 02 Feb 2023
UK’s first Cat Certified Machine Rebuild
One of the UK’s leading recycling and waste management companies has given Finning the green light to complete the UK’s first Certified Machine Rebuild (CMR) on a 15-year-old Cat 836 landfill compactor to give it a new lease of life ensuring that it can continue operating for another 15 years.
FCC Environment owns and operates over 200 recycling, treatment, and disposal facilities across the UK, managing more than 8.5 million tonnes of waste for their customers, which include over 72 local authorities across North Yorkshire, Suffolk and Essex. FCC’s waste processing fleet alone comprises 500 machines including landfill compactors, wheeled excavators, track type loaders and articulated dump trucks, with Cat equipment making up almost half.
One of these machines, a Cat 836 landfill compactor, was purchased from Finning in 2007 with a full repair and maintenance programme, which proved instrumental in keeping the machine operating effectively for around 15 years whilst minimising downtime. However, when the machine’s transmission failed in late 2022 FCC Group Plant Manager, Bill Stone, began discussions with the Finning team on the best solution for a replacement machine package. This included looking at buying another new machine as well as considering the option to carry out a full CMR, which is the highest-level Cat certified rebuild available.
Adam Walker, engine and drivetrain product manager at Finning is overseeing the project. He said, “Sustainability is now at the forefront of the waste industry, so we’ve seen a shift in demand towards companies requesting remanufactured or reconditioned parts for their machines, or for the entire machine to be rebuilt. This is the first machine rebuild that FCC has commissioned, but the company now plans for this approach to become an integral part of their fleet management succession plan because it enables them to demonstrate a clear commitment to improving the environmental impact of their operations and reducing emissions in the drive to net-zero.
Less energy
“Rebuilding a machine instead of buying new requires 85% less energy, uses 86% less water and generates around 61% fewer greenhouse gases,” Adam continued. “Plus, we recover and recycle over 65% of the original machine, so it’s ready to be used as a replacement part in another machine. Not only that, but customers choosing a rebuild machine option will typically save around 50-60% on the cost compared with buying a new machine. While remanufactured parts, of which there are around 8,000+ Cat certified ones available, can be up to 60% less than the cost of a brand new one.”
Bill Stone said, “We have a commitment to run our operation in an environmentally and socially responsible way, and by choosing to rebuild and give our assets a second life rather than buy new, we are helping to meet that commitment. Our mobile plant fleet is key to our operation, so it is essential these assets are managed effectively, and Finning plays a vital part in that.
“It is because of their record of strong aftermarket support and our collaborative relationship with the team at Finning that we have complete confidence in the effectiveness and efficiency of their rebuilds and they will play a crucial part in our succession planning moving forward,” Bill added.
Once complete, the Cat 836 will be ‘as new’ so will offer the same machine lifespan as a new machine. Machine rebuilds are fast becoming a recommended approach for firms’ fleet management, providing a sustainable and commercial option alongside investment in new machines. Finning has seen their number of machines rebuilds double year on year, with their specialist rebuild engineers completing hundreds over the last three years.
Got a news story? Email news@earthmoversmagazine.co.uk.
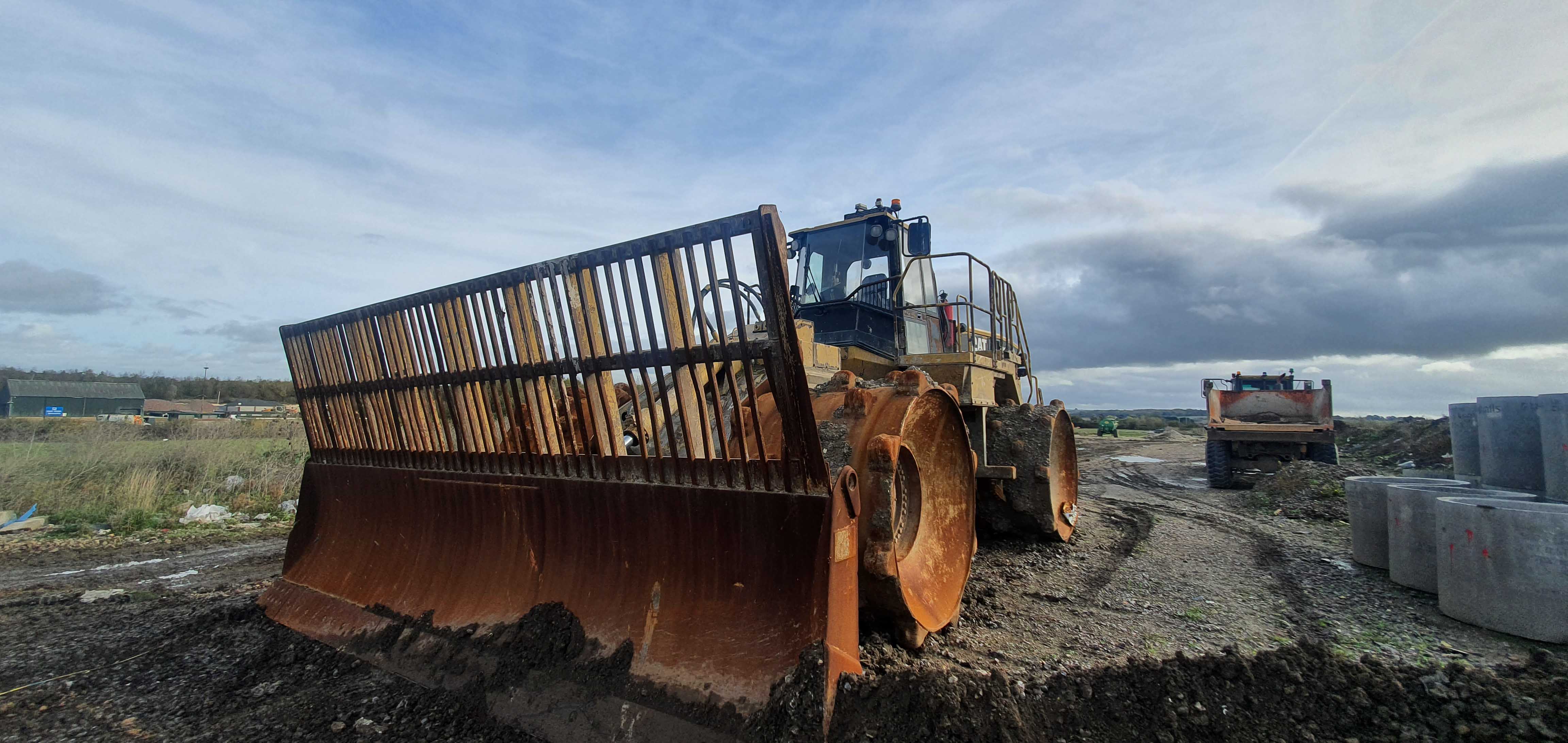