by Nick Drew | Wed 08 Apr 2020
First Kobelco, First “Tilty”
Taking another look back at one of my articles which has previously appeared in Earthmovers Magazine and bringing it to life on the internet with alternative photos and video footage.
When Dorchester based Mark Whitely left school, he joined a bricklaying apprenticeship in the time-honoured tradition with a local company back in those days. In 1987 aged just 18 Mark set up his own business, Mark Whitely Bricklaying, eventually employing somewhere in the region of 40 people, and becoming a major bricklaying contractor in and around the Dorset area.
Expansion continued until one day he was made a proposal on site, Mark takes up the story, “About 18 years ago I turned around to the company we were working for and said, look, if that’s the best footings the groundwork company can do, then we might as well do it ourselves, to my surprise the Managing Director turned to me and said, well if you think you can do it we will give you all the work!”
It was a proposition Mark couldn’t turn down, so he went out and invested in his first excavator, a 13-tonne Hitachi and a forward tipping dumper and they have carried on offering a full groundworks and civils package to this day, in fact Mark reckons that nowadays the Mark Whitely Group is doing far more groundworks and civils than bricklaying.
As the business has grown, so too has the fleet of machinery which today includes a 13-tonne Hitachi, 6-tonne Hyundai, 2 x Kubota 3-tonners, 2 x Kubota micro excavators, 2 x Merlo telehandlers, a Herbst PTO Driven Agri-Crusher, various site dumpers from 6 to 9-tonnes and their own low loader for moving the machinery around.
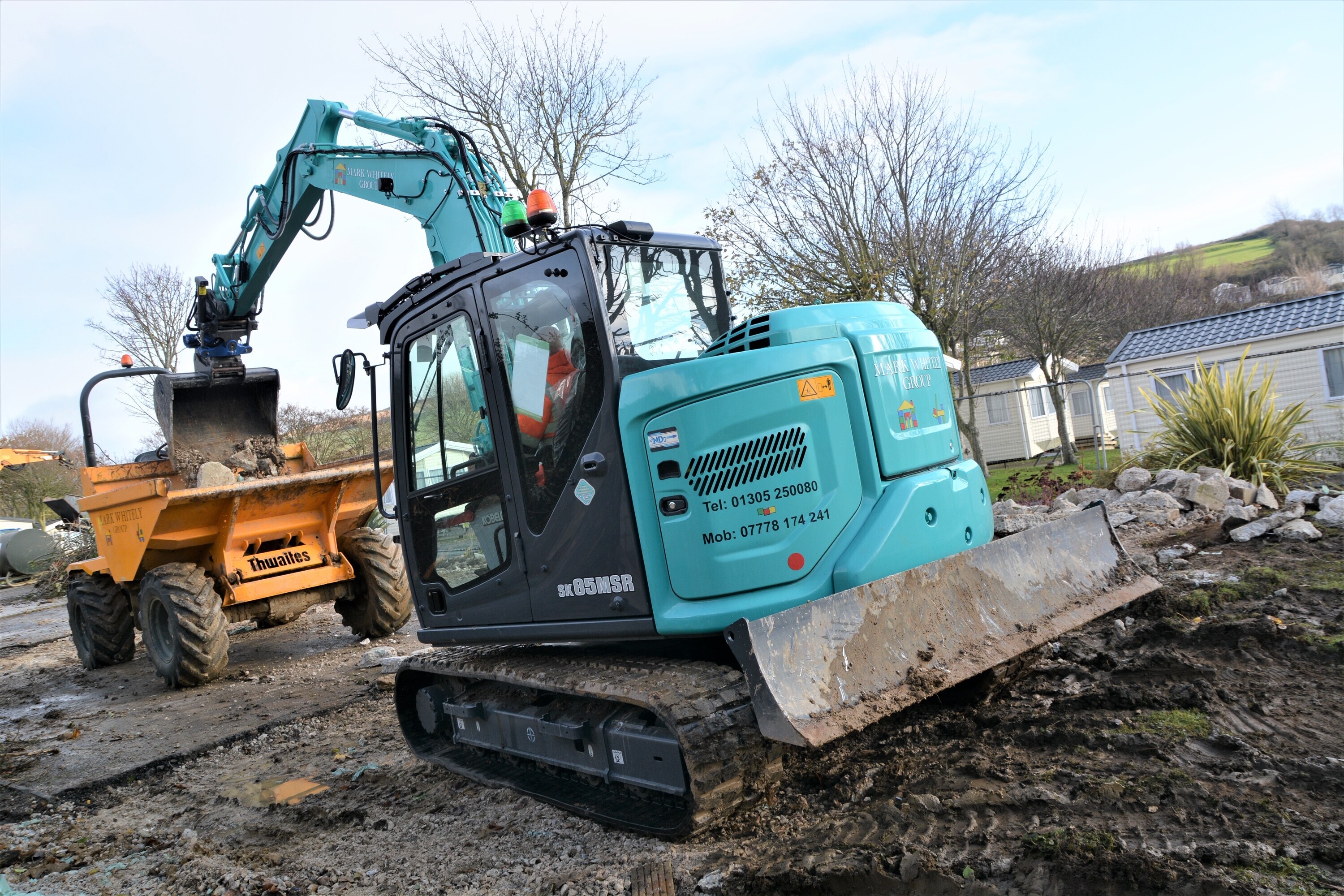
The latest piece of kit to join the fleet is a Kobelco SK85MSR-7 complete with an SMP tiltrotator which has been supplied by the Molson Group and which we caught up with on a site in the Dorset seaside town of Weymouth.
Briefing us about the job Mark said, “We’ve done a lot of work over the years here at the Waterside Holiday Park, after a couple of years away, a new management team has come in and we have been awarded this job, which involves stripping out 17 old caravan bases and replacing them with 14 luxury bases complete with hot tub facilities.
We have won the job mainly down to the fact that we have the capability to recycle most of the materials on site with minimum fuss, while ensuring that any material being removed from site is kept to the absolute bare minimum”.
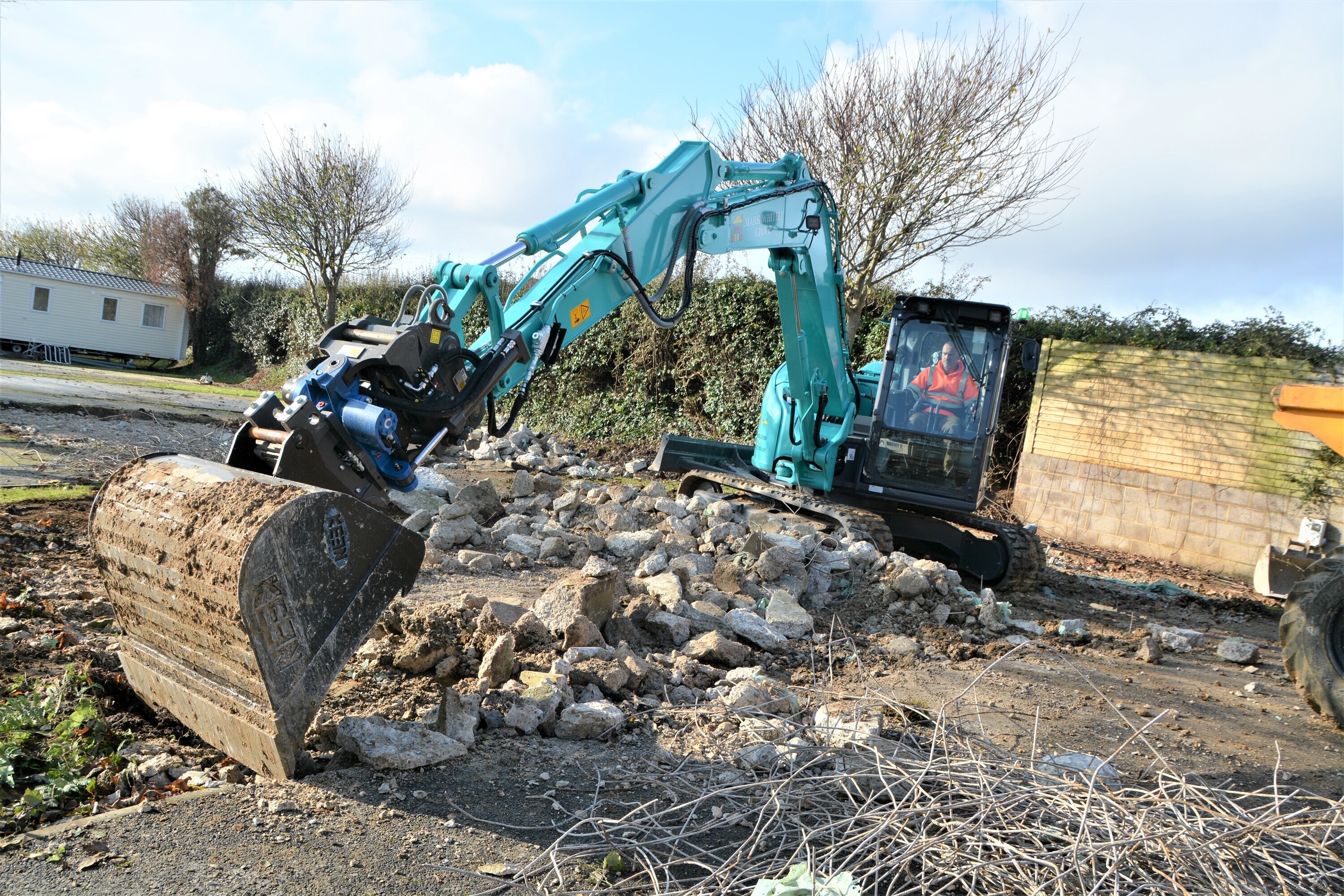
Talking about the new machine Mark said, “Its very early days, but so far we are very pleased with it, smooth to operate, very quiet and with an extremely high level of operator comfort, the two cameras provide excellent visibility to the rear and offside of the machine via the nice big monitor and the low bonnet also helps with the visibility over the back end”.
Talking about the tiltrotator Mark continued, “We’ve been looking at tiltrotators for some time now and have decided we have to keep moving with the times and all that, I’m not going to lie, it’s going to take some getting used to, but we are already seeing massive benefits to running one, less movements of the base machine, more flexibility to do the job from one spot, especially in confined quarters and its just going to save time and wear and tear in the long run, so as far as I can see, a great investment for our business!”
On the day of our visit the new machine was busy pulling up the concrete pads and loading the rubble into a site dumper, a bit later it was put to use loading the company’s Agri-Crusher to create recycled material for use as hardcore under the new concrete pads.
Walkaround
Kobelco launched the SK85MSR-7 at Bauma earlier this year replacing the outgoing SK85MSR-3 model. The old machine was a cracking piece of kit, but following consultation with existing Kobelco customers and internal research and development, they have added some great new touches and significant operational improvements on the new model. The machine tips the scales between 8,400 to 9,600kgs depending on specification, this example would be slightly heavier as its been fitted with an optional extra 350kg counterweight to compensate for the 260kgs + weight of the SMP ST10 tiltrotator and S45 H- Lock top hitch.
Power comes from the popular 4-cylinder Yanmar 4TNV98CT diesel engine which offers a power output rating of 53.7kw @2,100rpm and is Stage V EU Emissions compliant using a DPF system to achieve compliance with no requirement for AdBlue. According to Kobelco this is an increase in engine output of 27.9% compared to the previous model.
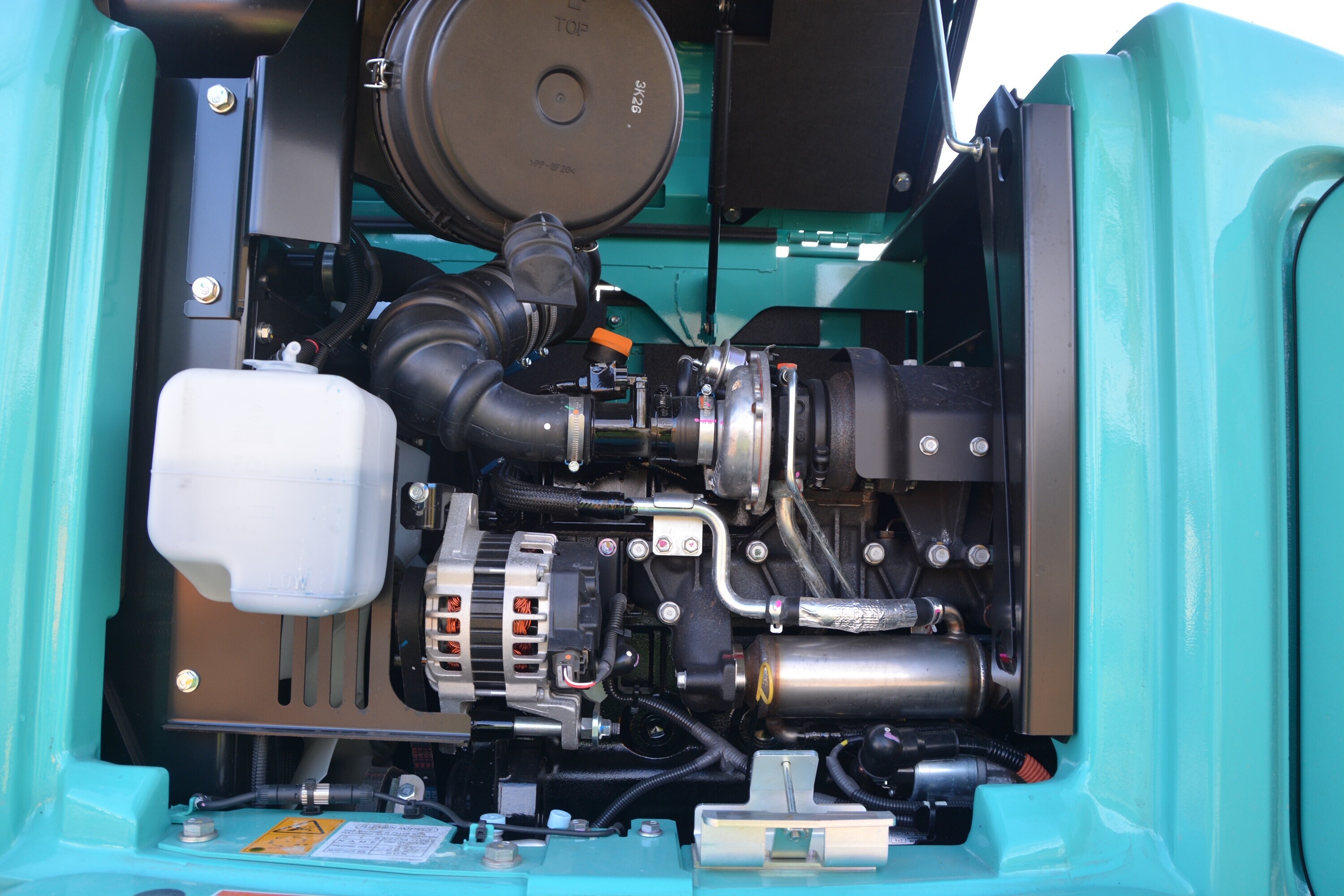
At the rear nearside behind the panel door we find the familiar Kobelco iNDr (Integrated Noise & Dust Reduction) filter system. This high-density filter mesh acts as a primary filter to prevent the cooling pack from becoming clogged with debris, its easily removable with one click of a latch, for a daily or weekly clean depending on site conditions. This compartment is also home to the batteries, the screen wash bottle and the isolation switch which on this new model now has a lockable cover over it.
To the rear the bonnet raises up for access to the aforementioned engine assisted by a gas strut and secured in place by a metal rod for safety, access to all filters is easily achieved from ground level. On the offside corner behind the panel we discover that once again it’s a Kawasaki hydraulic pump, all be it one with a Kobelco badge on it, Kobelco say that hydraulic oil flow is up on this model by 13 litres per minute. Talking of hydraulic components, the SK85MSR-7 is brimming with blue chip Japanese parts, including the main control valve, which is from KYB as are the track motors, while the slew motor is from Nabtesco.
A side panel door is home to the standard fitting electric refuelling pump and access to the hydraulic valve block. As I walked down the side of the machine checking out the 450mm standard rubber tracks, I noticed that the distance between the upper structure and undercarriage has been increased by some 20mm, this gap has been increased in order to reduce damage by rocks, something that would prove to be very beneficial on this site when moving the machine around with broken up concrete with reinforcing bar in it being a potential hazard.
The lockable fuel filler point is easily accessible from ground level, and even when refuelling using the built-in pump is always good practice to undo the cap to release any back pressure during refuelling. In the centre of the machine a lockable tool box is provide for the grease gun, cartridges and a handful of spanners.
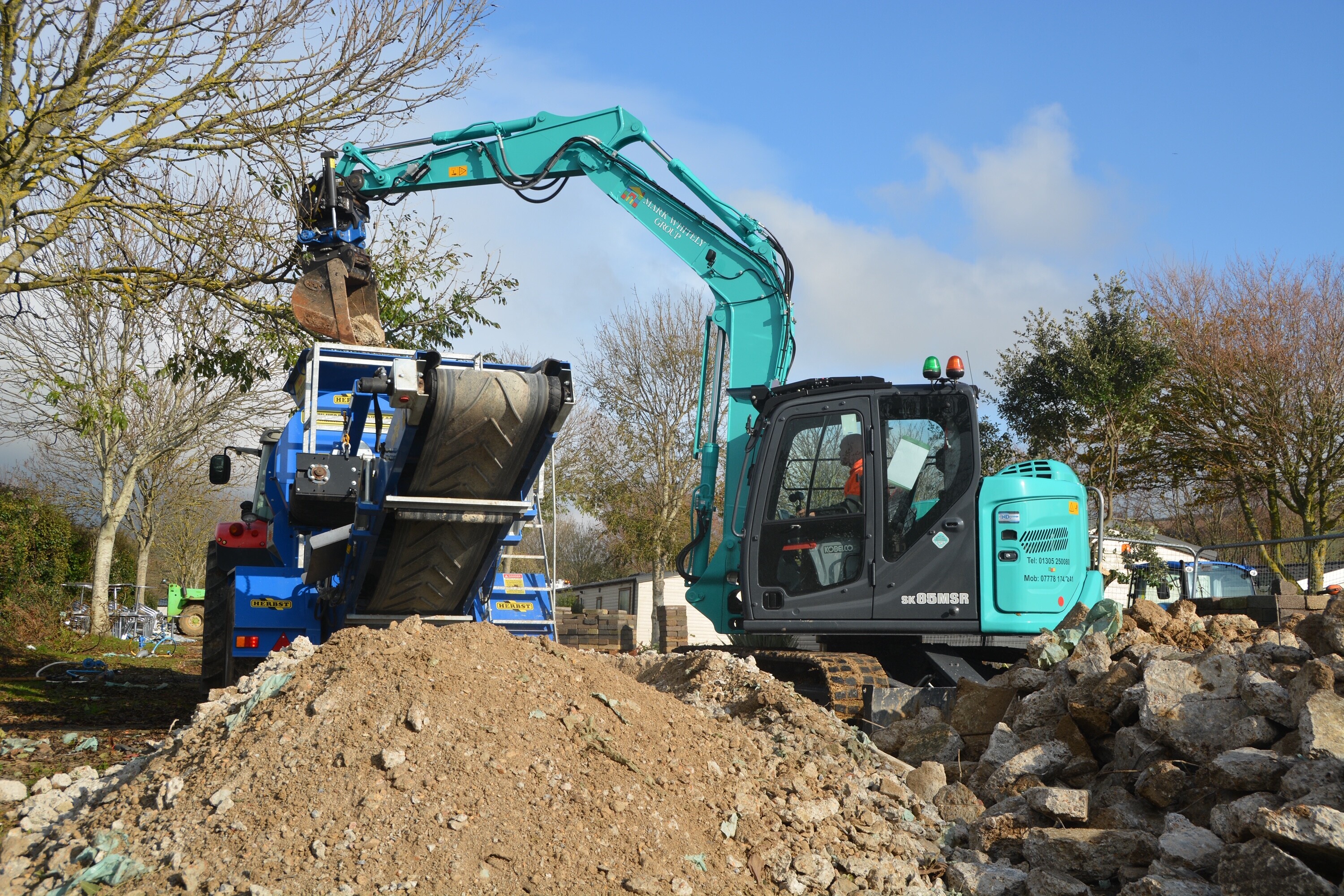
At the business end, this machine is fitted with a 3.50m boom and the longer 2.13m dipper stick which would generally offer a digging reach at ground level of 7.34m and a maximum dig depth of 4.44m, this example with the tiltrotator fitted will be capable of achieving depth and reach though, impressive for an 8/9 tonne class machine. A full set of Keen buckets were delivered with the machine at Mark’s request.
Other improvements pointed out however they measure such things, include a 15% reduction in digging cycle times, a 37% increase in arm digging speed, loaded boom lifting speed is up 38%, while bucket breakout force is up from 52.7% on the Dash-3 to 60.3 kN on the Dash-7 model.
Some of the most significant changes are within the cabin which features an all new layout. It all starts with a luxury fully adjustable Grammer heated air suspension seat, these units seem to be the go too choice, for manufacturers lately and its certainly a nice place to be spending your working day sat in.
To get yourself extra comfortable the lever angles can be independently adjusted to suit individual operator’s requirements. The arm rests are also easily adjusted for height. All the main control buttons and dials for the air conditioning are nicely located to the operators right. To the rear of the cab I note that at last in this size machine there is a shelf for a lunch bag, but its not very wide and it would need some cargo netting fitted to retain the said lunch bag, but it’s a start in my opinion!
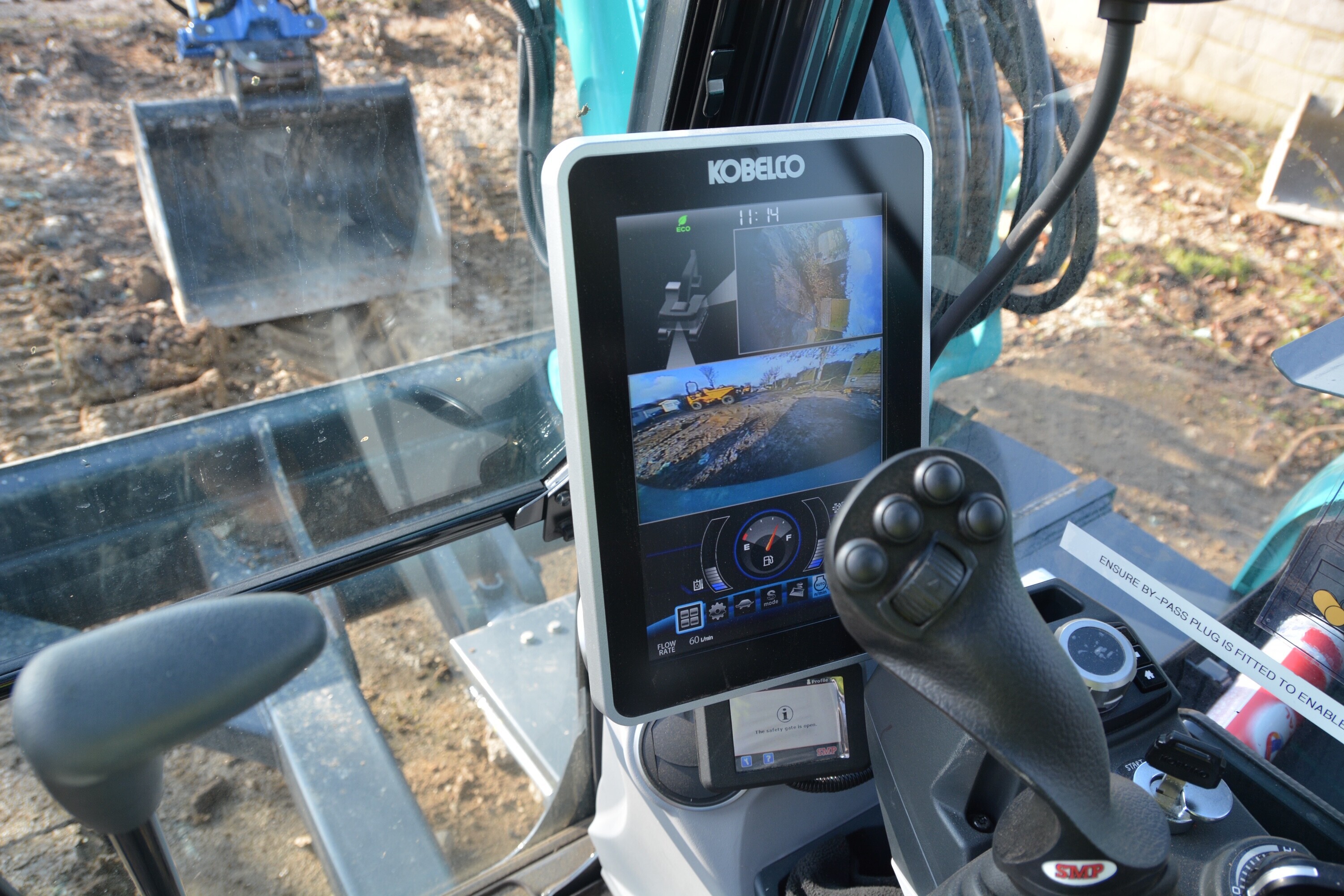
To the front of the cab is Kobelco’s 10-inch full colour monitor, it resembles an iPad and is very intuitive to use as a touch screen affair, or preferably the operator can use the jog dial control on his right-hand side to navigate through all the menus included. Although we didn’t get to use the machine on the day, I could see it is a top-quality piece of kit, and the comfort levels in the cab are second to none.
The machine has been fitted with SMP’s SVAB control system which includes its own dedicated user interface monitor which can also display the tilt angle you are working at, one would think that’s something for the boys to get their heads around at a later date once they have mastered the basics of tiltrotator life.
The operator can select from 3 working modes via the monitor, H-mode is used for heavy working, S-mode normal working and Eco-mode for prioritizing fuel efficiency over work volume.
The operator is question Bob Whitely, who was not a man of many words, but was clearly delighted with his new machine saying, “It’s a very nice machine to operate, I’m very happy with it”.
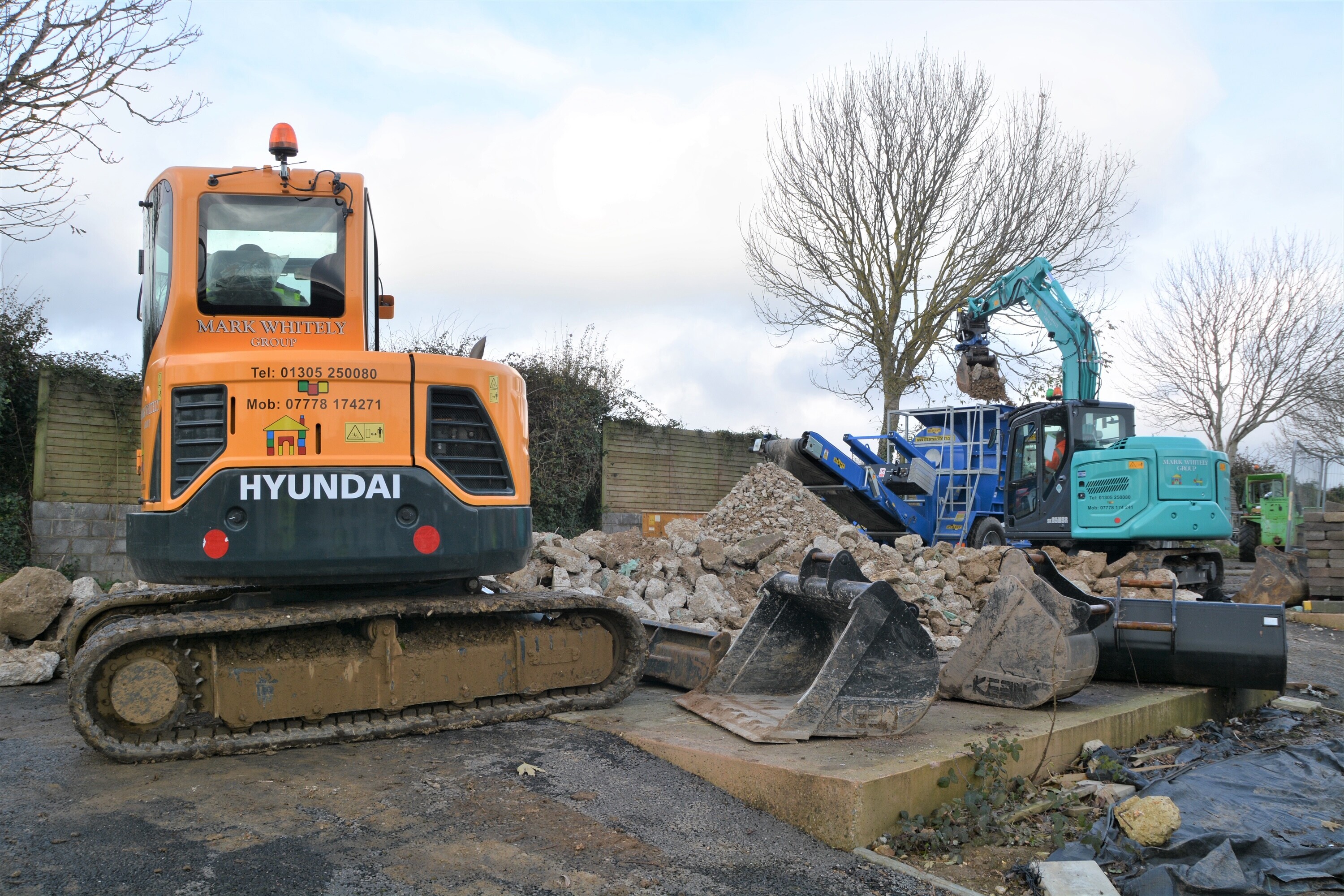
Mark Whitely was clearly very happy with the dealer service saying, “I like the way our local rep Tristan Dorey goes about things and we are now negotiating for a deal on a 14-tonne Kobelco, I also have long term plan to replace our 6-tonne class Hyundai R 60CR-9A with another Kobelco SK85MSR-7 which we will have rigged to receive the tiltrotator, which we can then float our unit between the two machines as and when we feel its needed, I’m also going to have a frame built for it, so its secured and safe when its dropped off”.

Summarizing Mark concluded, “I’ve been very pleased with my dealings with Molson, its also nice to deal with a single source for both the machine and the tiltrotator, safe in the knowledge that if there are any issues going forward its just one point of contact, that makes everyone’s life a lot easier”.