by Nick Drew | Mon 26 Jun 2023
Lundberg Production Shifts to Finland
Historically it’s quite unusual for industrial production to be moved from Sweden to Finland. But that move has recently taken place as manufacturing of Lundberg loaders has moved from Skellefteå in Sweden to Loimaa.
The Finnish manufacturer recently held a media day to show members of the press around, unfortunately I was not able to attend on this occasion, but my good friend and industry colleague Olli Päiviö did make the trip, and has kindly shared his report and photos with us here on the Digger Man Blog.
Lännen Tractors Oy, part of the LMCE Group, is now producing Lundberg compact loaders entirely in Finland. This increase in production has also increased the need for recruitment and investments in the production facilities at the Loimaa factory.
LMCE Group consists of a group of limited companies operating in Finland: Lännen MCE, Lännen Tractors and Aquamec. The subsidiary Lännen MCE AB will continue as the Swedish distributor. The assembly of Meclift forklifts is also done in Loimaa with the associated company Mecalift Oy .
Currently, the collective companies already employ 160 people and the turnover is in the 50-million-euro range, of which 75 percent of it consists of international sales.
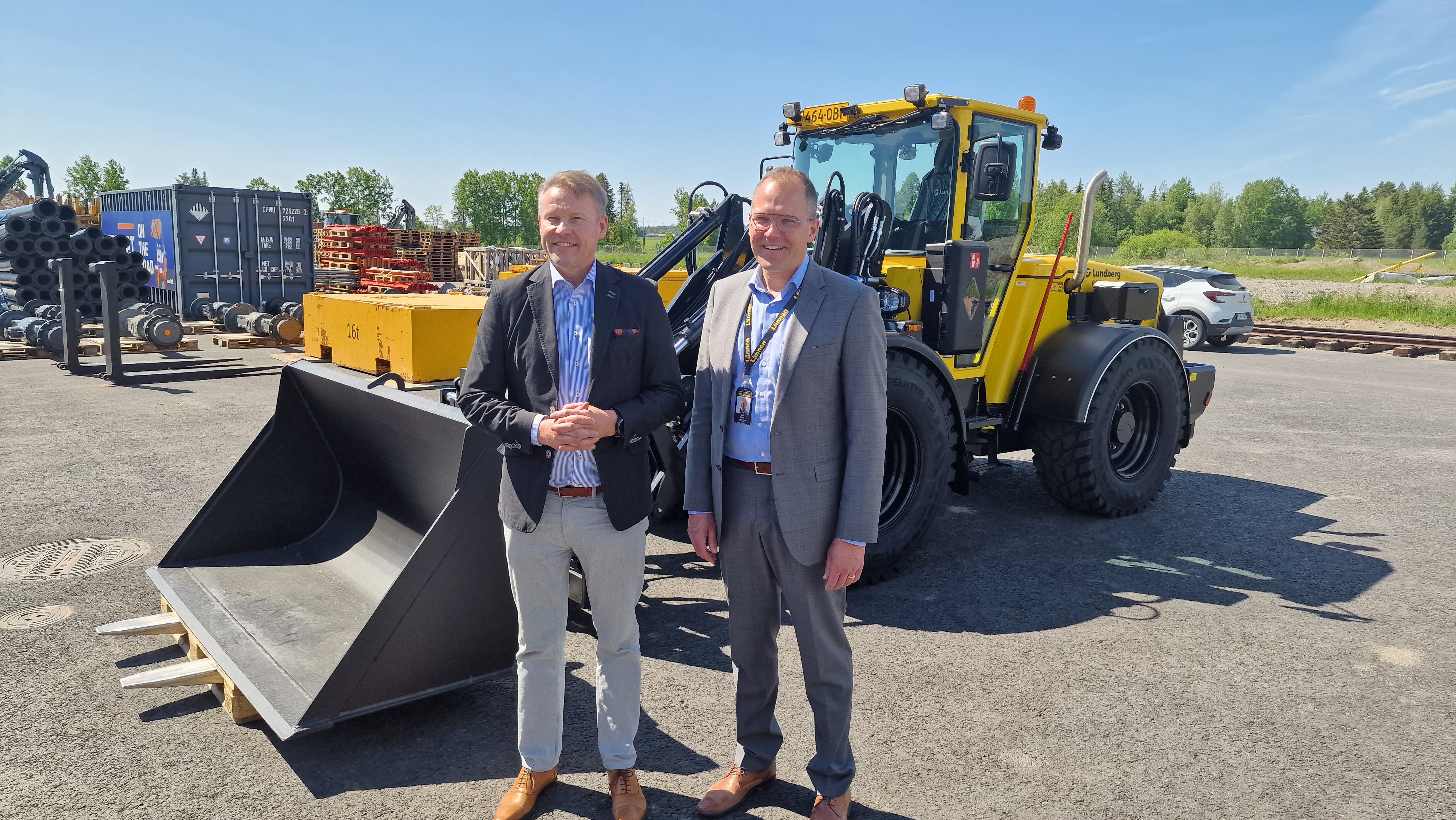
The main owner is Timo Huttunen (Left), who is the chairman of the board, and Veli Ollila, who was elected CEO of Lännen MCE Group at the beginning of June, is a minority shareholder. Together, the men steer the group forward. Huttunen has taken responsibility for the most international part of the company, i.e., the Watermaster business.
"Watermaster was born as a result of an internal idea competition held within Lännen. The actual world launch began in 2006-2007 and the concept has already been sold in more than 80 countries. More than 400 machines have now been manufactured", begins Huttunen.
The war in Ukraine stopped Russian trade, and even spare parts are no longer supplied to the country waging a war of aggression. The paralysis of Eastern trade is now making us look for replacement markets.
"We have now opened up to, for example, North America, where the first devices have already been delivered. They are assembled there locally from components supplied by us. There is a demand for dredging machines in every corner of the world, there is plenty of work in shallow water bodies," continues Huttunen.
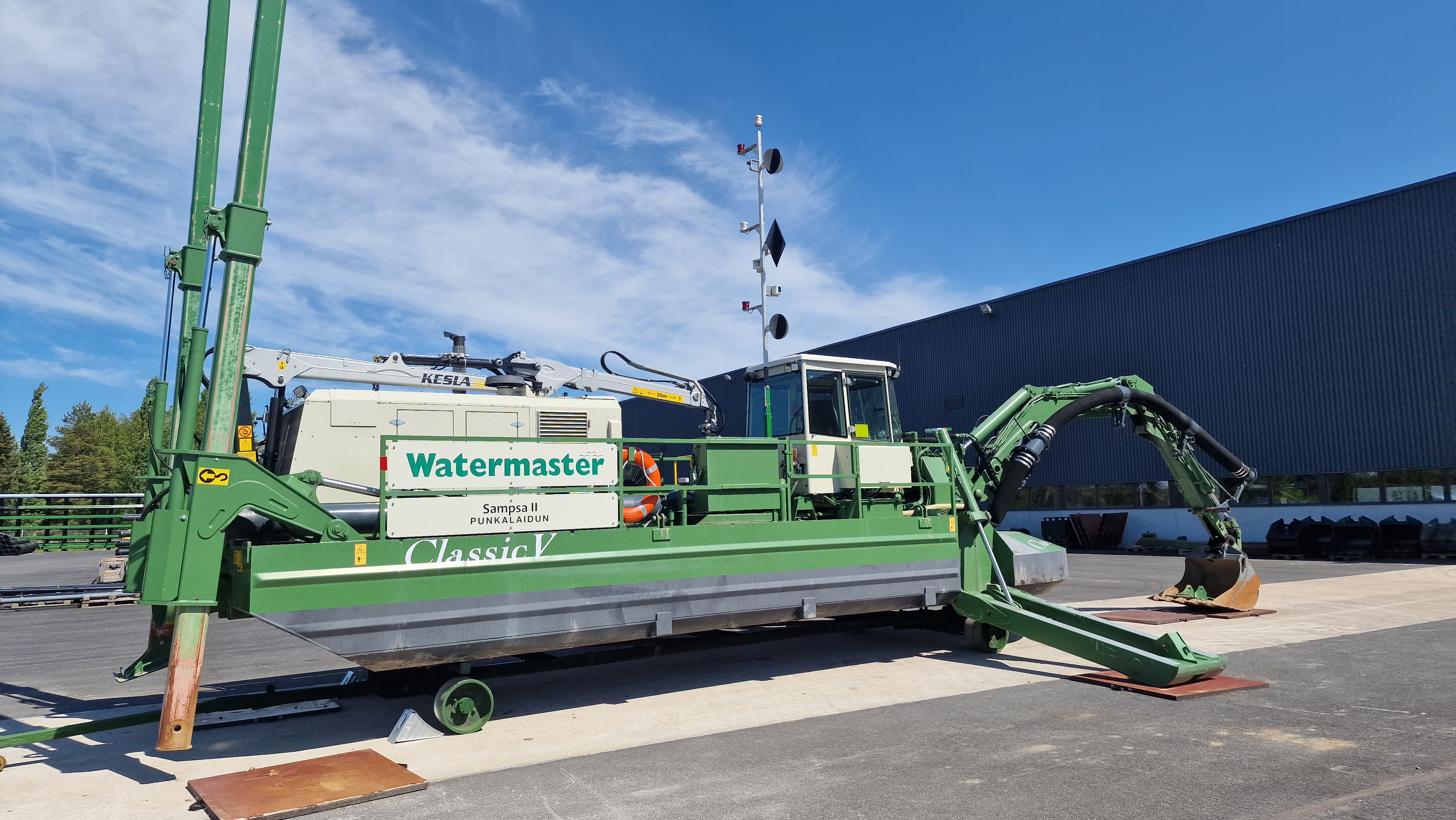
"With climate change, global population growth and urbanization, the need to clean waterways, flood control and remove harmful aquatic vegetation is growing strongly."
However, Veli Ollila, who has started as the new CEO, is not a new acquaintance at Loimaa. Ollila had already worked as the financial manager of the machine shop business of the then Lännen Tehtaat Oy on both sides of the turn of the millennium, and as a business controller at the Loima factory and in Stockholm.
The man will now move to the west from the CEO role of Jackon Finland Oy. Veli worked in that position for 10 years. In recent years, the man has also served on the boards of Lännen MCE Oy and its subsidiaries.
According to the men, about 250 machines under different brands are manufactured in Loimaa annually.
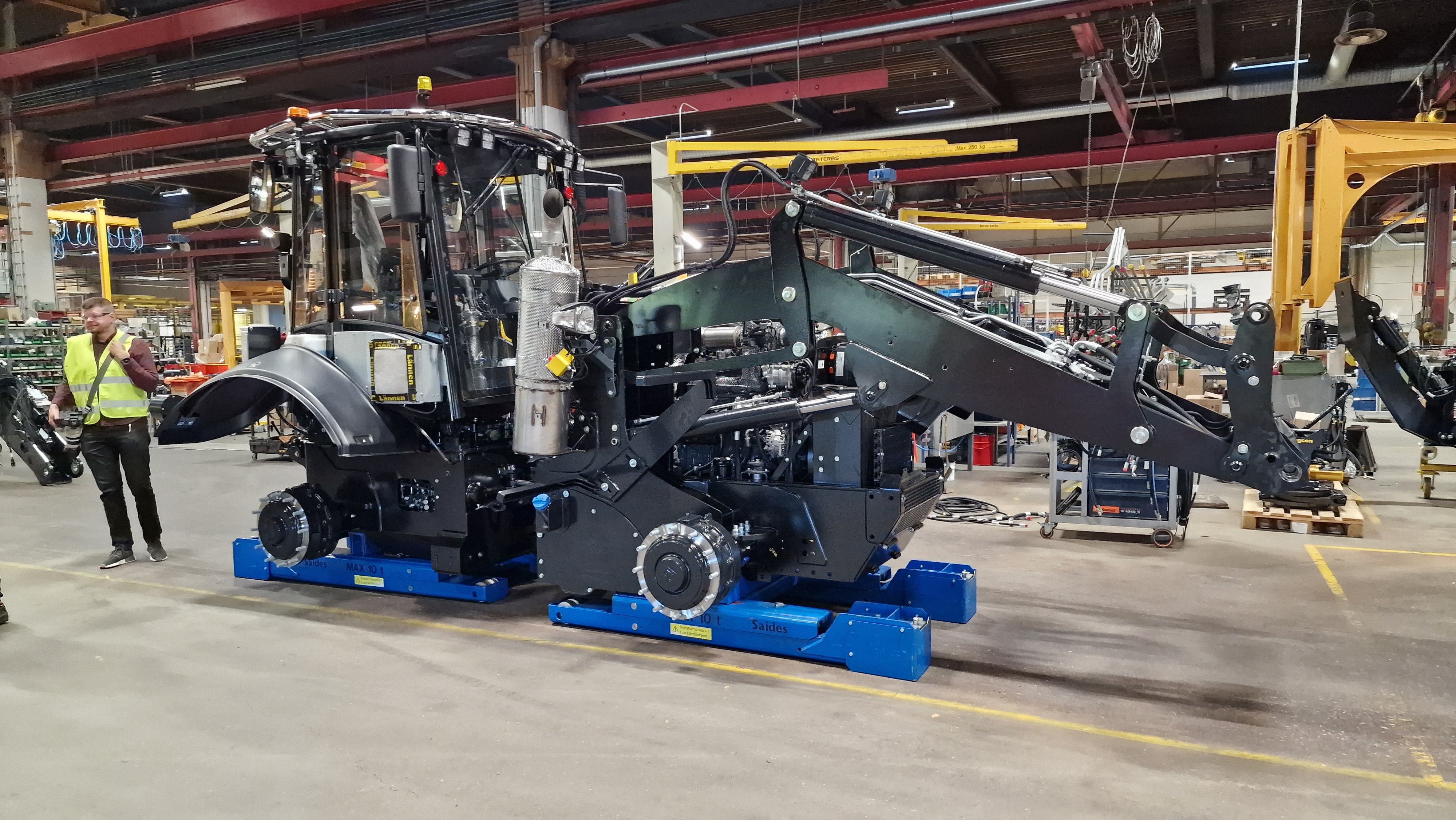
The order book for the machines is excellent and many of them have been sold a year ahead of production. The strong demand for products made the management team think of a solution to meet it.
"At the Skellefteå factory, we would not have been able to increase production sensibly. We operate there in rented premises and that also posed its own challenges. Although the Swedish krona has depreciated against the euro, it does not make the situation easier in Sweden in terms of manufacturing. The components for the machines mainly come from abroad, and as a result, more and more had to be paid for in krona. Recruiting new people in northern Sweden is also difficult, when there is a lot of other lively industrial activity in the area. Fortunately, it made it easier to find employment for the workforce that was released from us," says Huttunen.
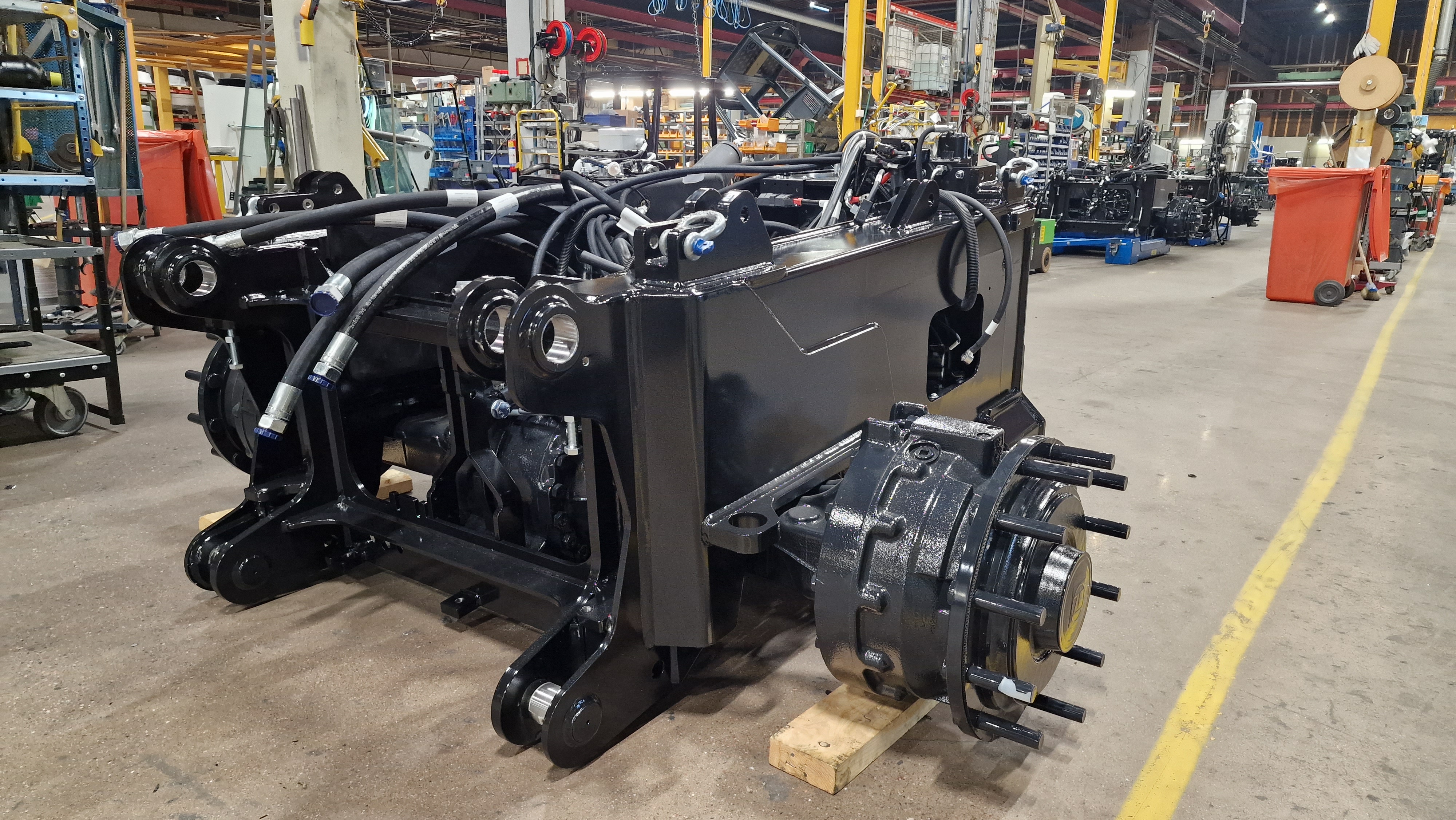
Loimaa's production before Lundberg has operated in quite spacious premises, so it was easy to find space to establish a new production line.
"The carbon footprint also decreases when the chartering of components ends. We have already made recruitments for Loimaa and we will continue them. In total, the Lundberg arrangement requires an increase of around 10–15 people. However, finding suitable skilled people is not easy", continues Huttunen.
The challenges are to raise production to meet demand. Getting to the annual production rate of around one hundred Lundberg machines requires investments in production as well.
Investments are required
The factory area in Loimaa is 20,000 square meters and the plot size is four hectares. The production facilities are spacious and bright, and it still doesn't feel too cramped, even though the product range has grown with Lundberg. Watermaster’s and multi-tasking Lännen backhoe loaders have their own assembly lines, and Meclifts are also created in their own separate department. The Lundbergs have now also got their own space. The layout will change again when production reaches its full speed.
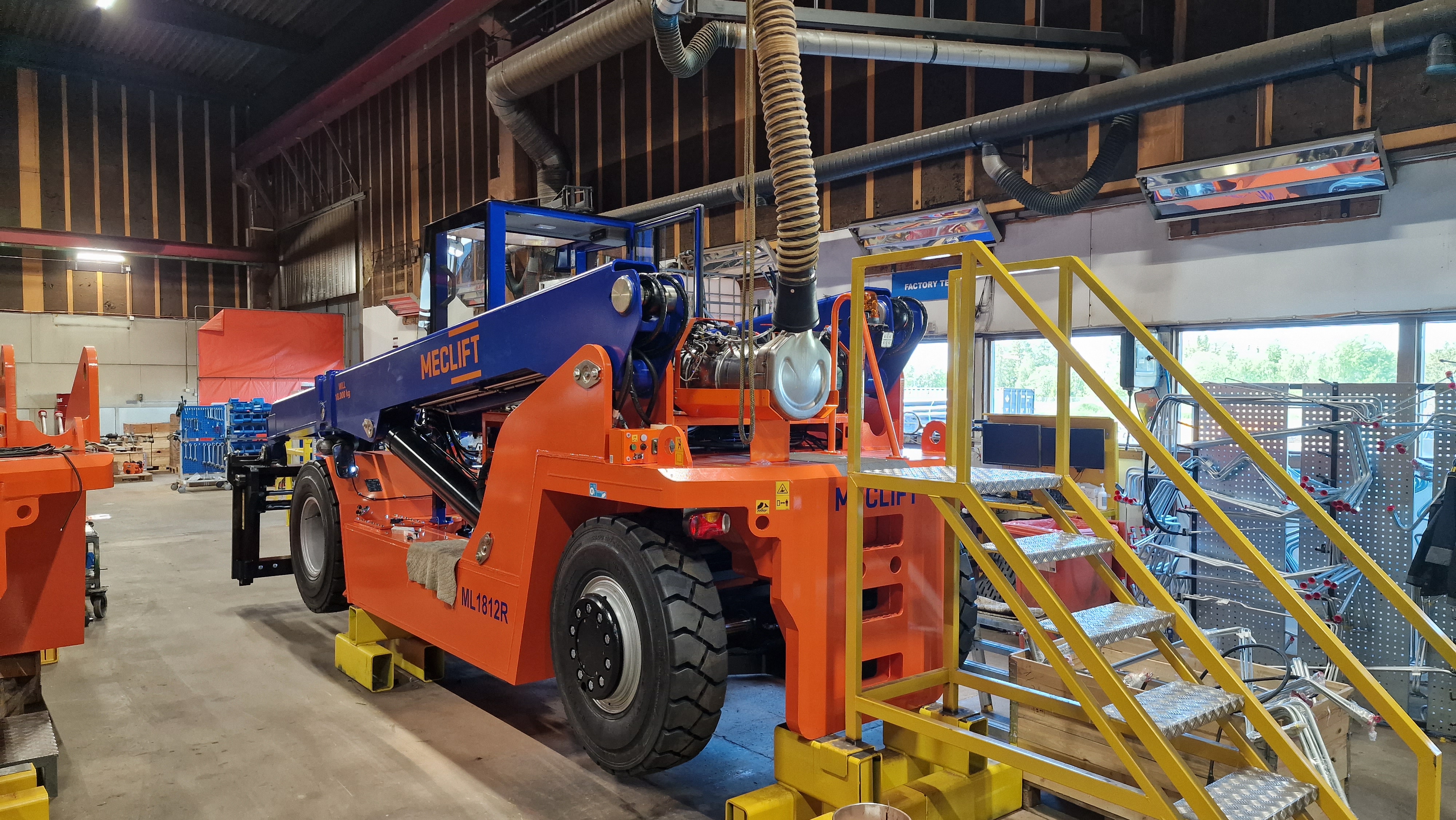
"In the past, Lundberg frames were already made here and shipped to Sweden. Parts ordered from subcontractors in Sweden can now also be manufactured here, which increases work. Production starts with pre-cut clips. Even large parts are first stapled in jigs by hand and then they move to robot welding and finally to machining. Of course, parts of small series are still welded by hand. We have invested in a new efficient machining centre and this year the paint shop will also be renewed. It brings more colour options and reduces wastage when switching from one colour to another. In total, 1.5 million euros have already been invested in production last year and this year," continues factory manager Arto Iivonen.
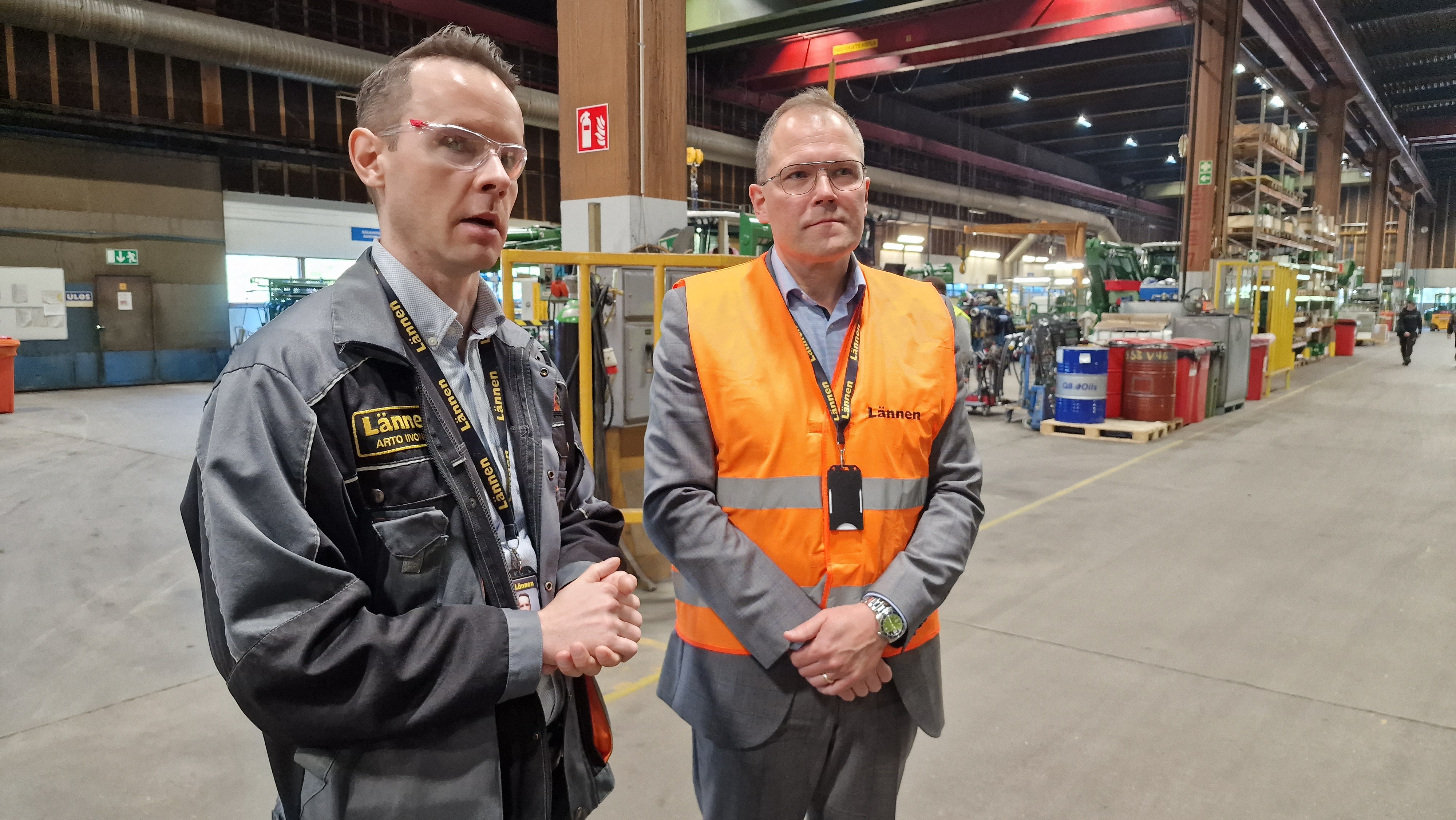
Many jobs, one machine
The word multi-function machine is used in the marketing strategy of the West. It describes the versatile usage possibilities of the entire product range.
More often than not we see Lännen backhoe loaders in special jobs, where they can be used to do the work of many different machines, from excavators and wheel loaders to personnel lifts. You see them working in infrastructure and urban construction jobs as well as in electricity and telecommunications, and railway infrastructure projects.
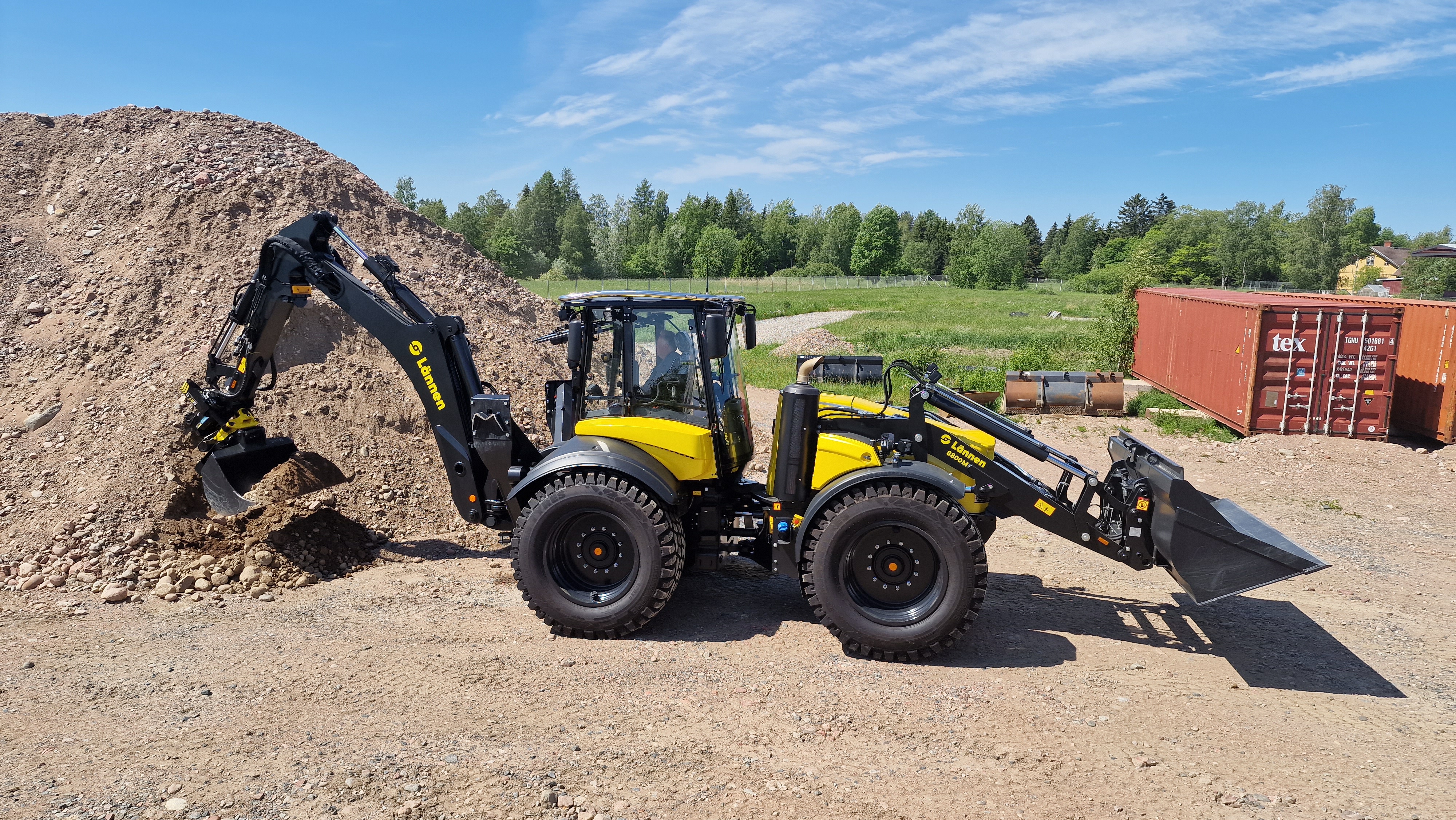
Jari Nevalainen
In the West, theoretical calculations have also been made of the carbon footprint of different machine types during their entire life cycle. The public usually only talks about carbon dioxide emissions during use, the topic has now been addressed more widely.
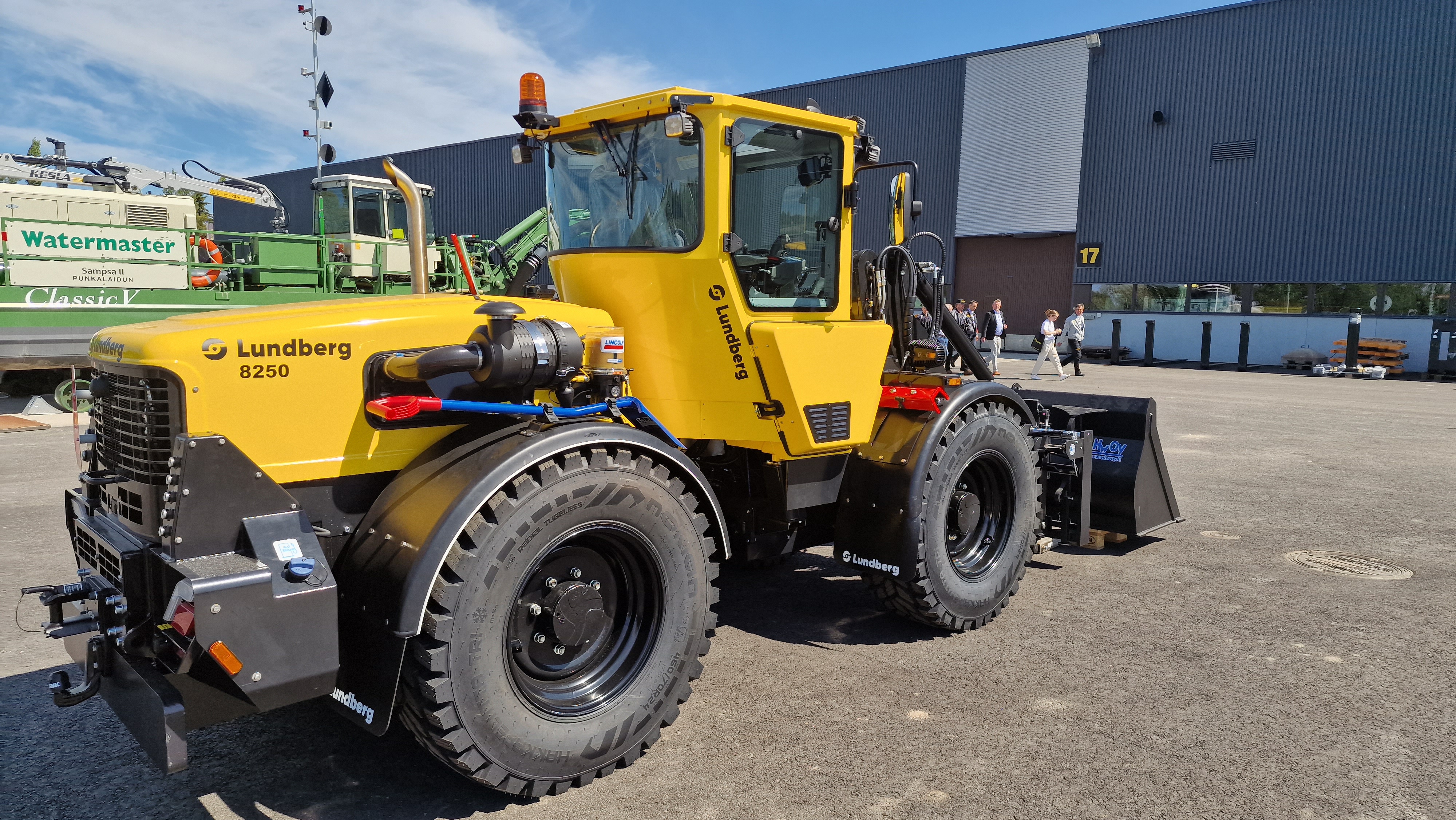
"Of course, we had to make a lot of assumptions when information about other types of machines was quite non-existent. The calculations therefore took into account the entire life cycle, starting with the production of raw materials and the manufacture of machines, all the way to distribution, use and even disposal. The biggest source of emissions in the entire chain is, of course, the use of the machines," says business director Jari Nevalainen.
According to Lännen’s calculations, up to 84 percent of the emissions of the entire life cycle are generated during what is described as the technical lifetime of the machine, i.e., 8,000 hours.
"It is remarkable that by using renewable fuel (HVO) the emissions are reduced to almost a sixth," concludes Nevalainen.
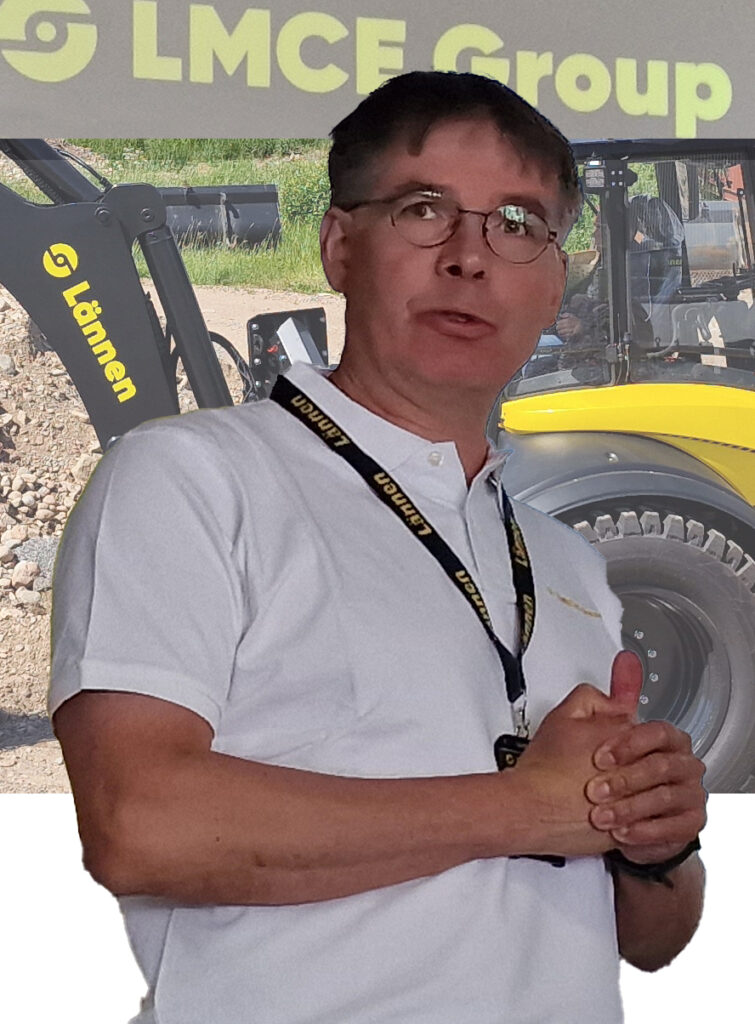
Checkout my video from one of my previous visits to the Lännen facility.
Thanks must go to Olli Päiviö and Konepörssi for sharing the material contained in this post.