by Nick Drew | Thu 15 May 2025
Takeuchi Continues to Deliver
Taking a look back at one of my articles that has previously been published in Earthmovers Magazine, un-edited and with alternative images and video.
Takeuchi’s 9-tonne midi excavator offering the TB290-2, which was first introduced to the line-up in 2019, continues to be an ever-popular machine with a wide range of customers.
The first series Takeuchi TB290 model was revealed in 2014, replacing the 8.5-tonne class TB285 which was launched in 2012 as the successor to the previous 7.5-tonne class TB175 which was well liked model both by owners and operators alike, for its smooth hydraulics, boxy no frills look, durability and reliability.
When the TB285 was first introduced it featured a much more modern rounded and compact rear end, which is not only pleasing to the eye, but more importantly less prone to damage when working in tight quarters, this has continued with the TB290 and the very popular TB290-2 which with a few tweaks along the way, is now considered to be a heavyweight product in the Takeuchi lineup. In addition, since the start of this year, all Takeuchi machines now come with a 3-year/3000 hour warranty as standard, not that you are very likely to need it, such is the legendary standard of reliability of the Japanese built excavators.
Having first seen a TB290-2 in South Wales shortly after launch in 2019, we were offered an opportunity to take another look around one, on site in Daventry, which had recently been purchased by Northamptonshire based Rowan Groundworks Ltd from their local dealers Willowbrook Plant Ltd.
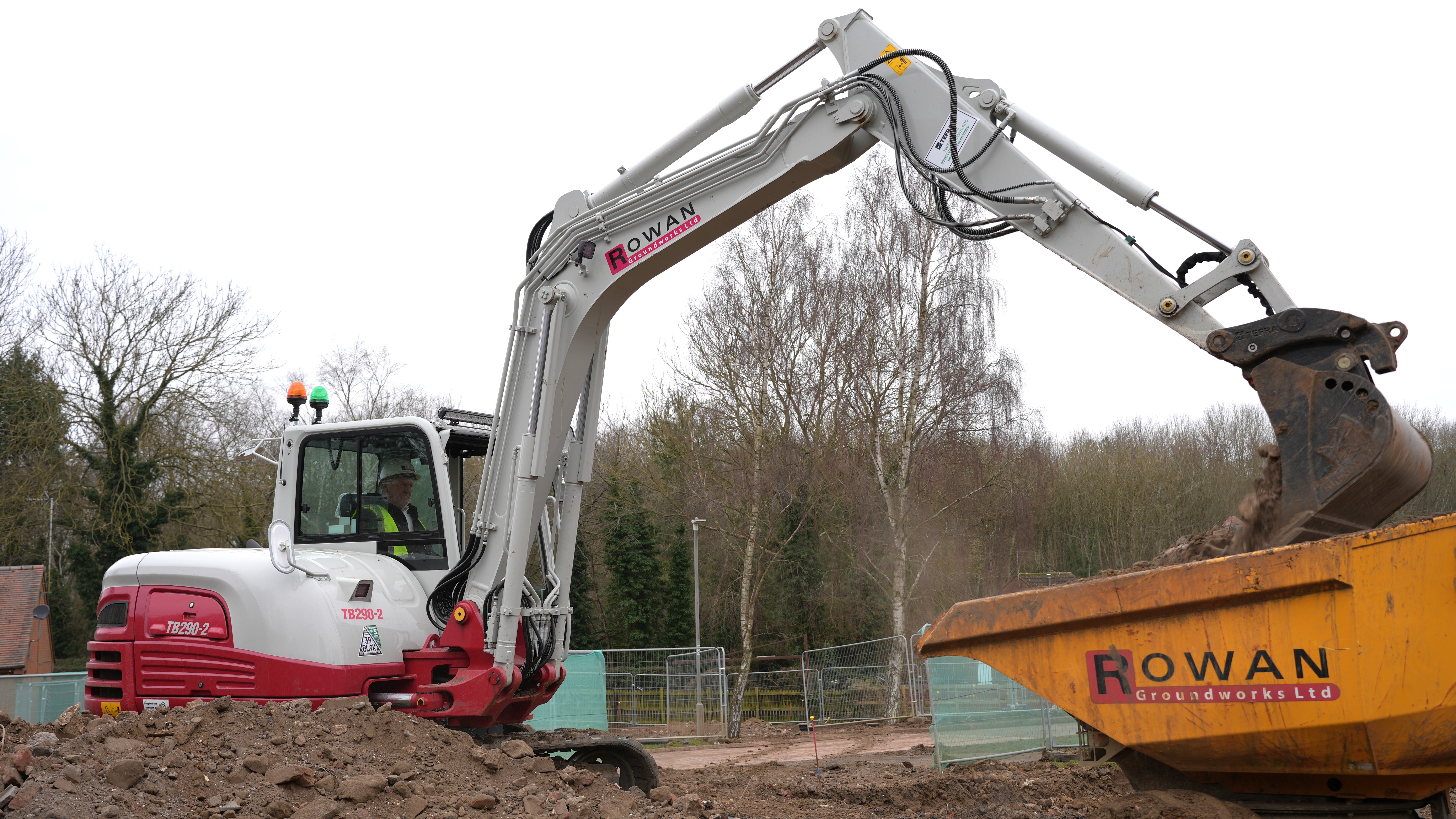
Lee Dorrington, Managing Director of Rowan Groundworks, is clearly a fan of the Takeuchi brand, as they currently run 2 x 290-2, 1 x TB216 and 1 x TB225 models.
Rowan Groundworks vastly experienced operator Norman Willmott gave us a tour around his latest Takeuchi mount.
The TB290-2 which comes with a whole raft of features as standard, is distinguished from its predecessors by the addition of red paint work which rises up along the side of the machine and drapes around the rear engine bonnet, this cosmetic alter-image look really does set it apart from the previous model which featured largely grey upper body work.
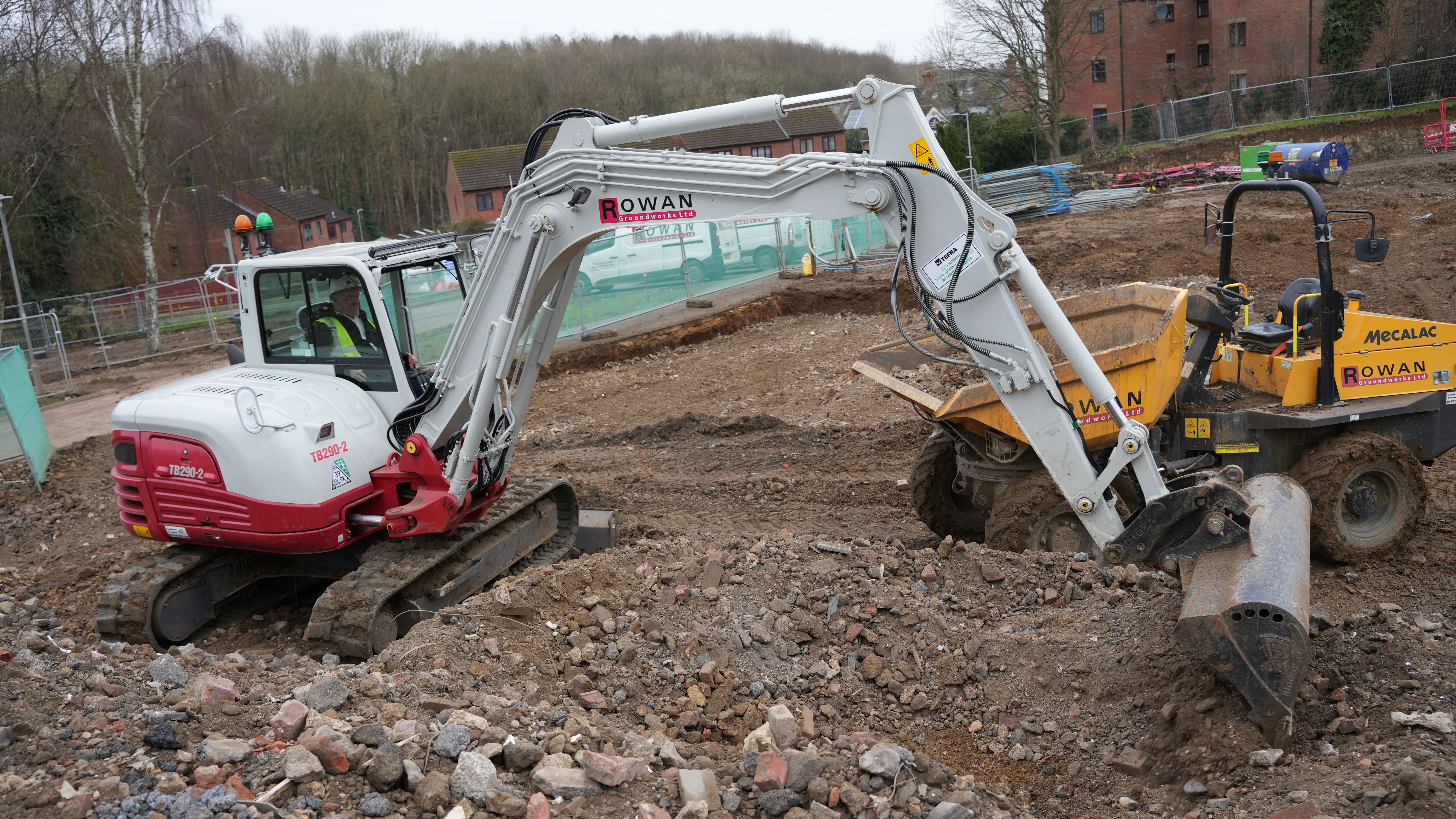
The rear bonnet raises up to reveal the heart of the TB290-2, the 4-cylinder turbocharged Yanmar 4TNV98CT-WTB diesel engine which is Stage V emissions compliant, and uses a DPF to achieve these standards. It offers a power output rating of 51.6kw @2000rpm.
This unit replaced the Isuzu power pack in the previous model which was rated at 52.0kw producing a maximum torque of just 255 N/m while the new Yanmar motor produces significantly more at 308 N/m at the same rpm.

Nestling in the engine bay is the state-of-the-art Kawasaki Variable hydraulic pump, this blue-chip component is larger than what was fitted on the previous models and offers vastly improved oil flow delivery which ensures enhanced hydraulic performance.
The engine and hydraulic components work in unison, enabling the machine to perform better and seamlessly smooth when using multiple functions during things like precision lifting, or tracking and slewing with a heavy load on the end. In this way you don’t get that feeling of one circuit slowing down another, or the jerkiness of movements you sometimes get from a machine with a less refined hydraulic system, this was one of things operator Norman commented on saying, “It really is a super smooth machine on the hydraulics, in my opinion, the best out there!”.
Same as on the earlier TB285 and TB290 models the gas strut assisted gull wing bonnet cover on the offside of the machine raises up to reveal a host of tightly packed in components inside including the main valve block, hydraulic oil tank, expansion bottle and screen wash bottle, which are located side by side and the 128-litre fuel tank. An electric refuelling pump is fitted as standard in this area and a handy sight tube, with the familiar floating red ball, is located down the side of the tank so you can easily gauge when refuelling is complete. The diesel tank filler point can also be accessed via the smaller lockable opening side panel too, which is very handy, rather than lifting the whole canopy, especially if filling up from a bowser.
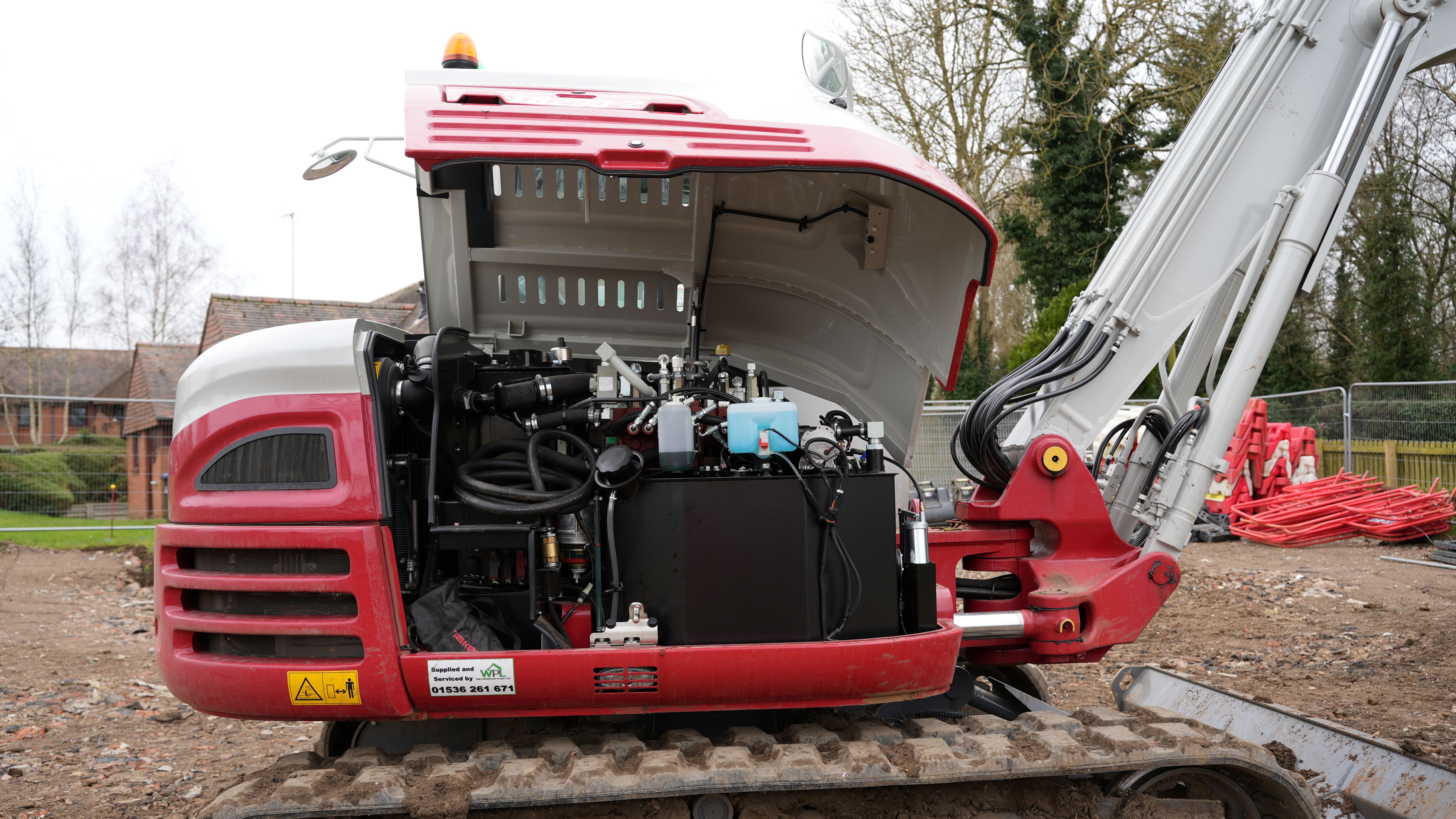
The TB290-2 now features a full LED work light package which comes as a standard fitting, this one features an impressive rooftop lightbar, 2 x boom mounted lights and 1 x forward facing on the offside canopy. Additional lights can be fitted to meet the specific customer’s needs.
This machine is fitted with the standard boom and long arm combination which offers a maximum reach at ground level of 7,290mm and a maximum dig depth of 4,580mm. Also, as standard boom and dipper check valves are factory fitted and the machine pre-piped for 3rd auxiliary lines. Boom off-set is 700 to the right and 600 to the left.
Norman has always been impressed with the twin boom lift ram set up, on this 9-tonne model, which he feels gives the boom far more stability and powerful lift performance overall. The only bit of negativity we heard from Norman was the procedure for the quick coupler, which involves using your heel on a pedal to the right-hand rear of the floor while pressing a button on the right-hand joystick, Norman said, “Sometimes it can be a bit tricky, and if you release the button on the joystick too early, you have to go back and start the whole procedure again, but it’s what it is and you do get used to it”.
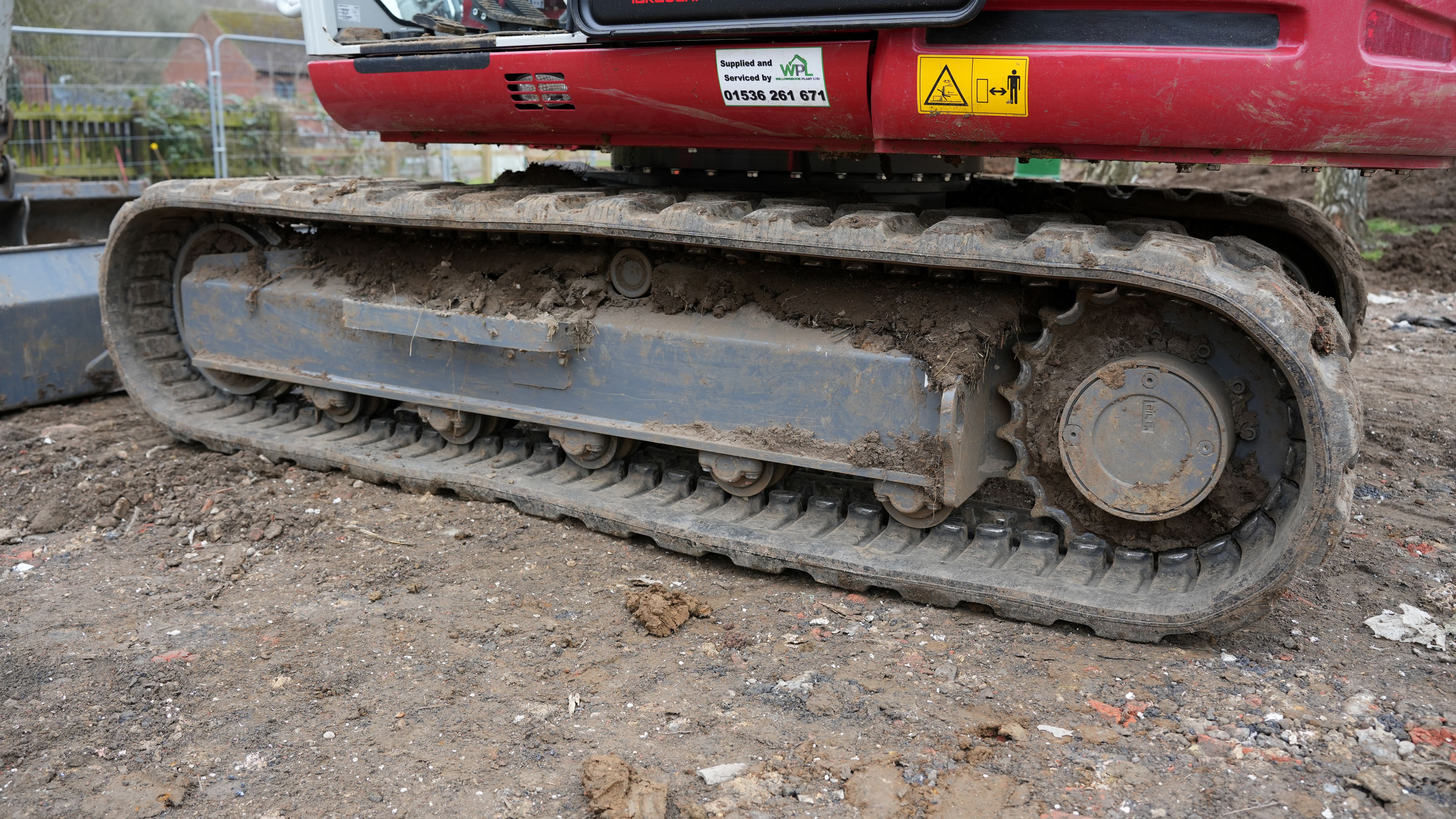
This example featured the standard fitment 450mm rubber tracks, with an overall track length of 2855mm. Other options including steel track shoes are available on request. Track guards can also be specified but this machine was not fitted with them.
At the business end of the dipper this machine was fitted with a Tefra fully automatic hydraulic quick coupler from Hill Engineering and was supplied with a full set of buckets from Rhinox, including super-sized grading/rehandling bucket
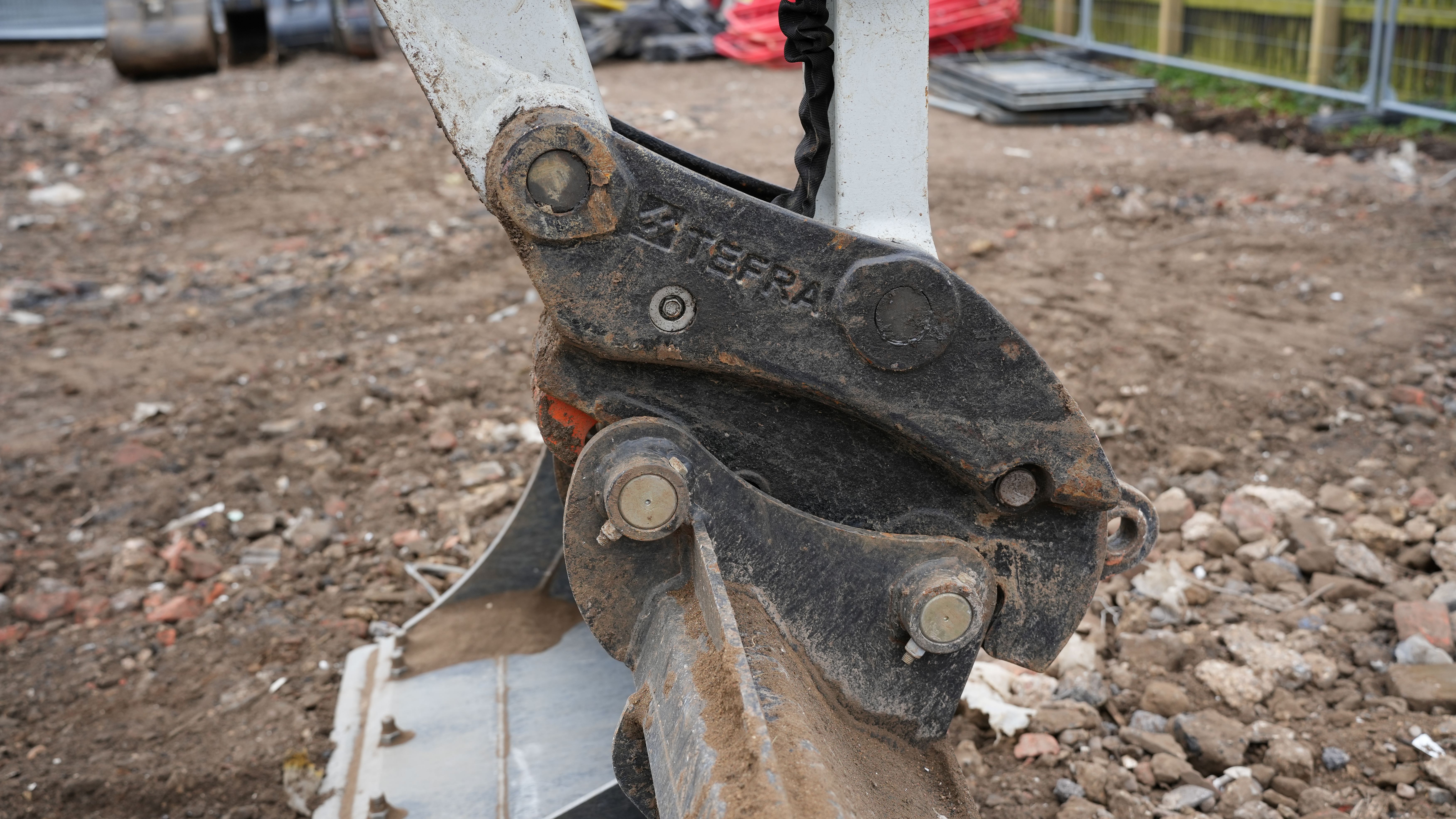
Climbing into the cab and it’s all that we have become accustomed to with the Takeuchi machines, a nice spacious interior, something that was echoed by operator Norman who said, “I’m a large sized person and I find the cab size to be very generous, I also find you don’t bang your head on the window when raising the front screen into the roof, in my opinion it’s the best in class for this size bracket”.
Everything you could possibly need is fitted in the cab, with standard fitments being, full climate control air conditioning and Bluetooth mobile phone connectivity.
For improved cab comfort, there are no less than five air vents located around the cab, to provide a good flow of hot or cold air as required to suit the climate and another nice little feature is that all important cup holder, but with quite literally a special twist. By rotating the cup holder slightly, it opens up ventilation holes in the bottom, which depending on the climate control setting, can keep your beverage hot or cold, it’s a neat feature that in all fairness, often goes unnoticed by operators until it’s pointed out to them.
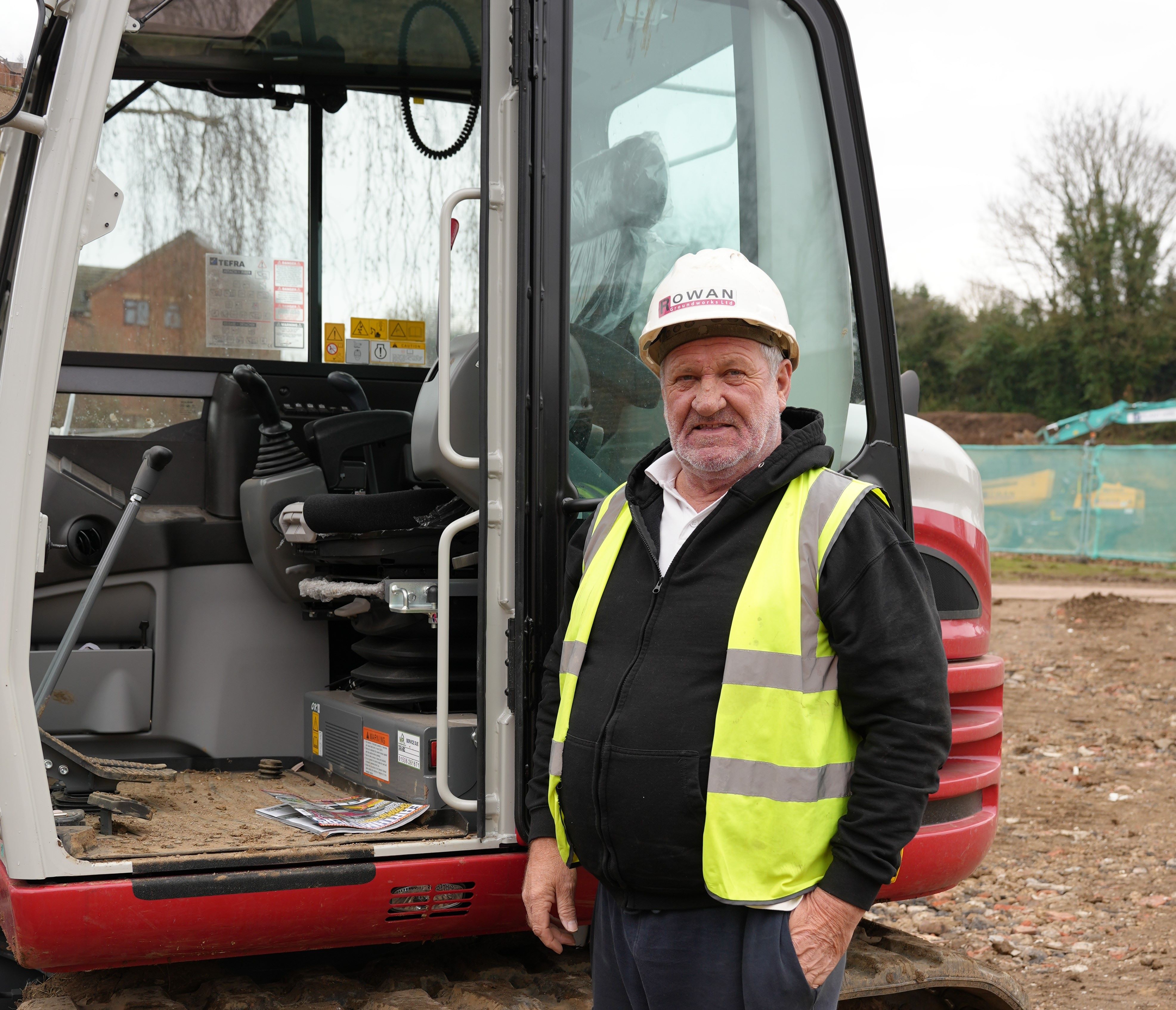
For fresh air freaks, the two offside windows can both open independently by means of sliding, and of course the top front screen can be raised up, and the bottom portion can be stored at the rear of the cabin. In addition, the main cab door can be locked in the open position as per the industry standard.
The full colour monitor offers a whole host of information back to the operator in a clear cut easy to use and read layout. The main screen reverts automatically to a rear-view camera as soon as reverse tracking is activated for improved safety not only for the operator, but for any ground crew who might have accidentally entered the working area.
Operators can also pre-set auxiliary modes on the VDU to match individual attachments flow requirements. The machine also features TFM, Takeuchi’s new Telematics system. This monitoring system keeps an eye on the overall health of the machine remotely and effectively can minimize any potential downtime.
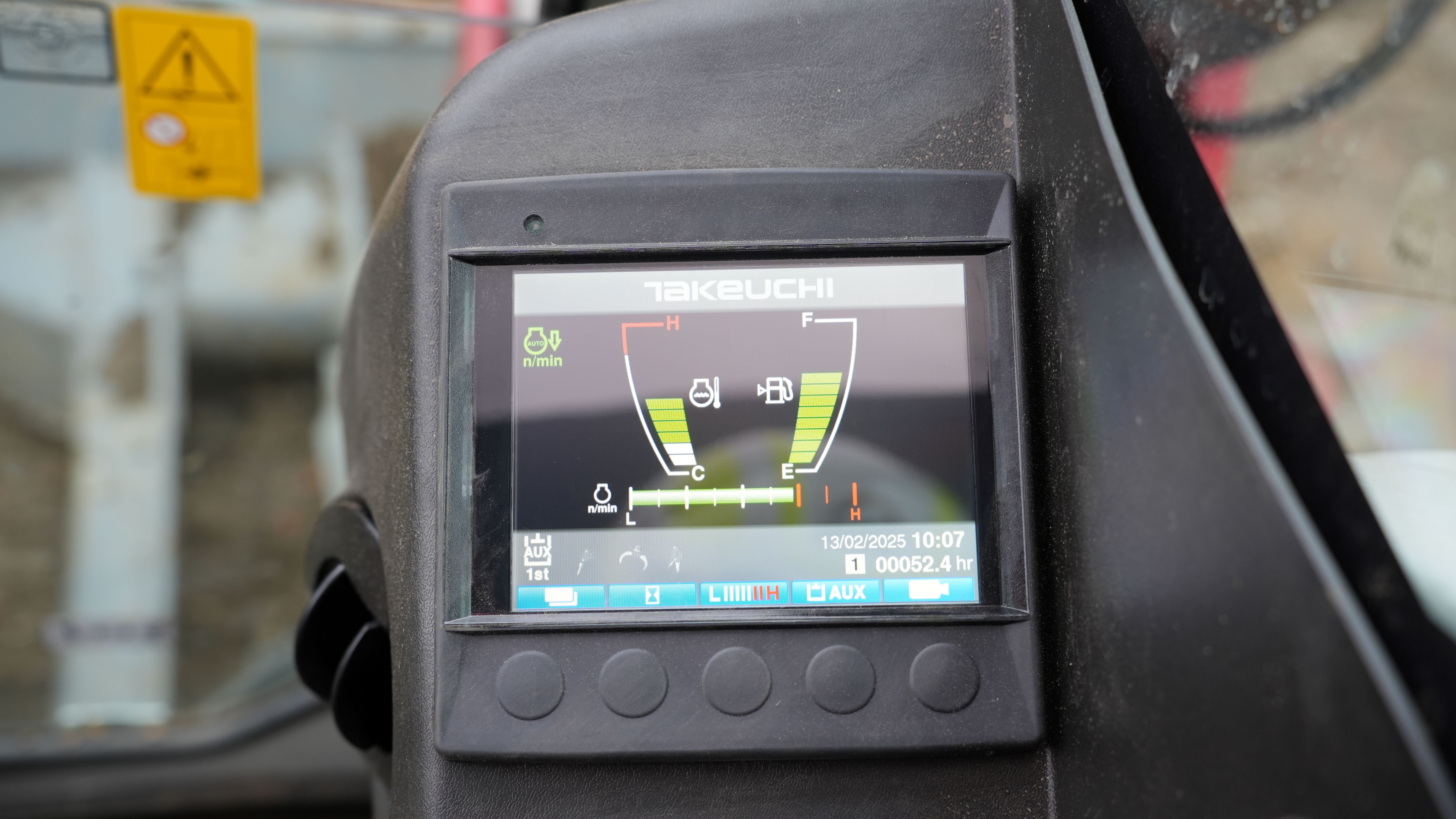
Features include remote diagnostics that reduce service trips by capturing run hours and equipment data. Utilization tracking allows the operator to make decisions based on actual equipment use, and schedules maintenance. This saves time, parts and money by avoiding unnecessary maintenance. In addition, TFM minimizes cost using the precision to identify the problem as soon as it starts.
Visibility all around is exceptionally good, there is plenty of glass, and with mirrors for and aft and of course the previously mentioned rear view camera, the operator is always assured a good view of the job site from any angle.
I was invited to take the machine for a spin, I was impressed with the three-stage hydraulic isolation lever on the left-hand joystick console, which initially raises one step, then the console goes up, then on the last stroke the lever folds up again, to allow the operator the very best entrance into the seating area. Once I sat down, I got myself comfortable in the superb Grammer heated air suspension seat, which offers multiple adjustments for that best operating position, even for guys like me with stumpy legs!
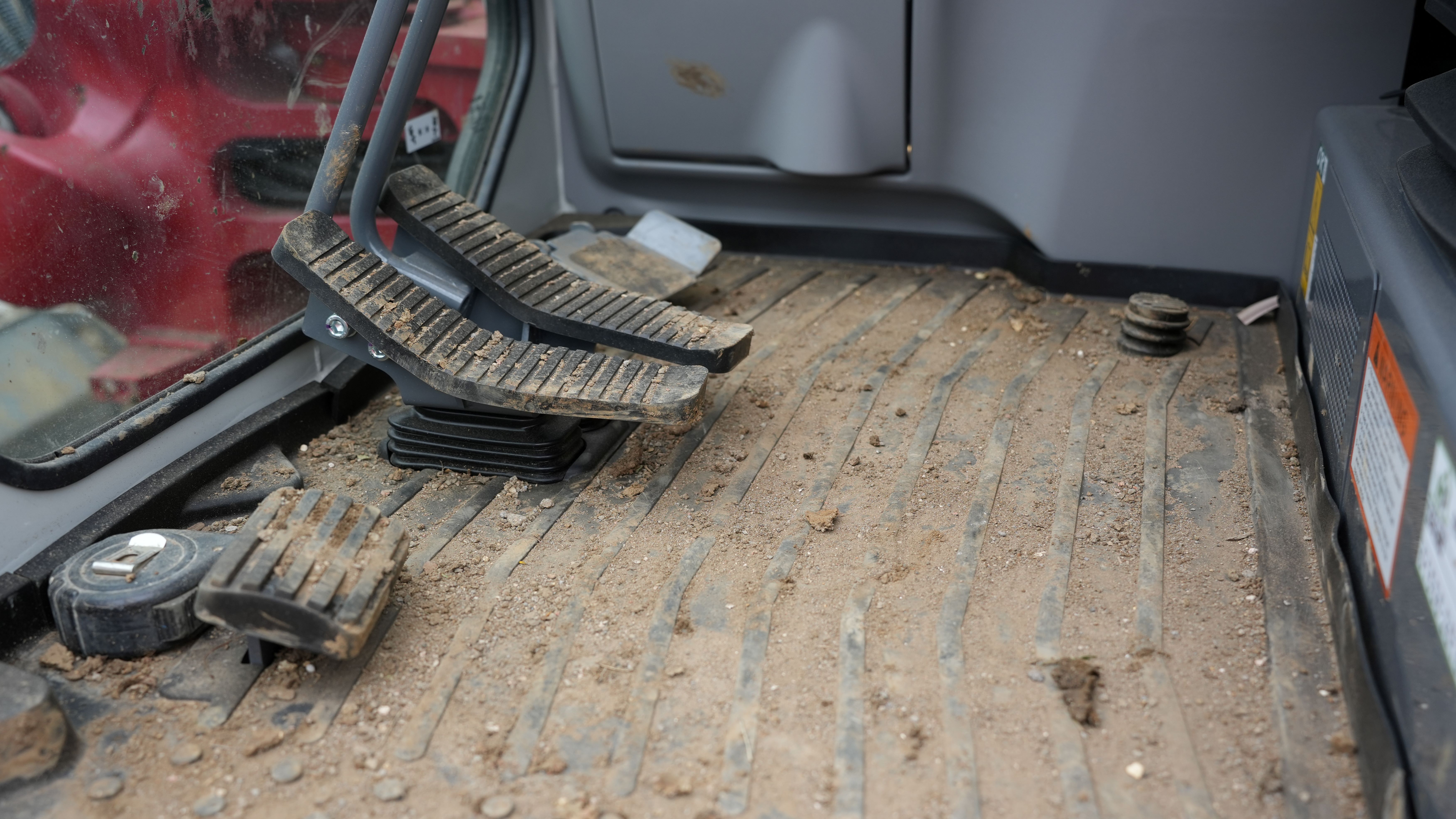
Surveying the surroundings its all the usual stuff we are used to with Takeuchi, nicely positioned control buttons, and the throttle dial located in the recess in the right-hand arm rest. Its nice to notice the decent sized track pedals more than enough for my size sevens to fit on. To the right hand-side we find the left and right off-set arm pedal, with a foot rest to the left of the track pedals.
No gimmicky push button starts on this machine, the traditional key in the ignition is great to see, having said that the key is protected by Takeuchi’s TSS (Takeuchi Security System) so you get 1 red master key and 3 black user keys, you can also programme up to 13 user keys in the system.
So, with the flick of the key the Yammar motor springs into life, after a period of warm up I gently tweaked the throttle dial to about half chat, before opening it right up, a tug on the floating blade lever and raising the boom with the right-hand joystick, I gently engaged the track pedals and headed towards a pile of recycled hardcore stored on the site.
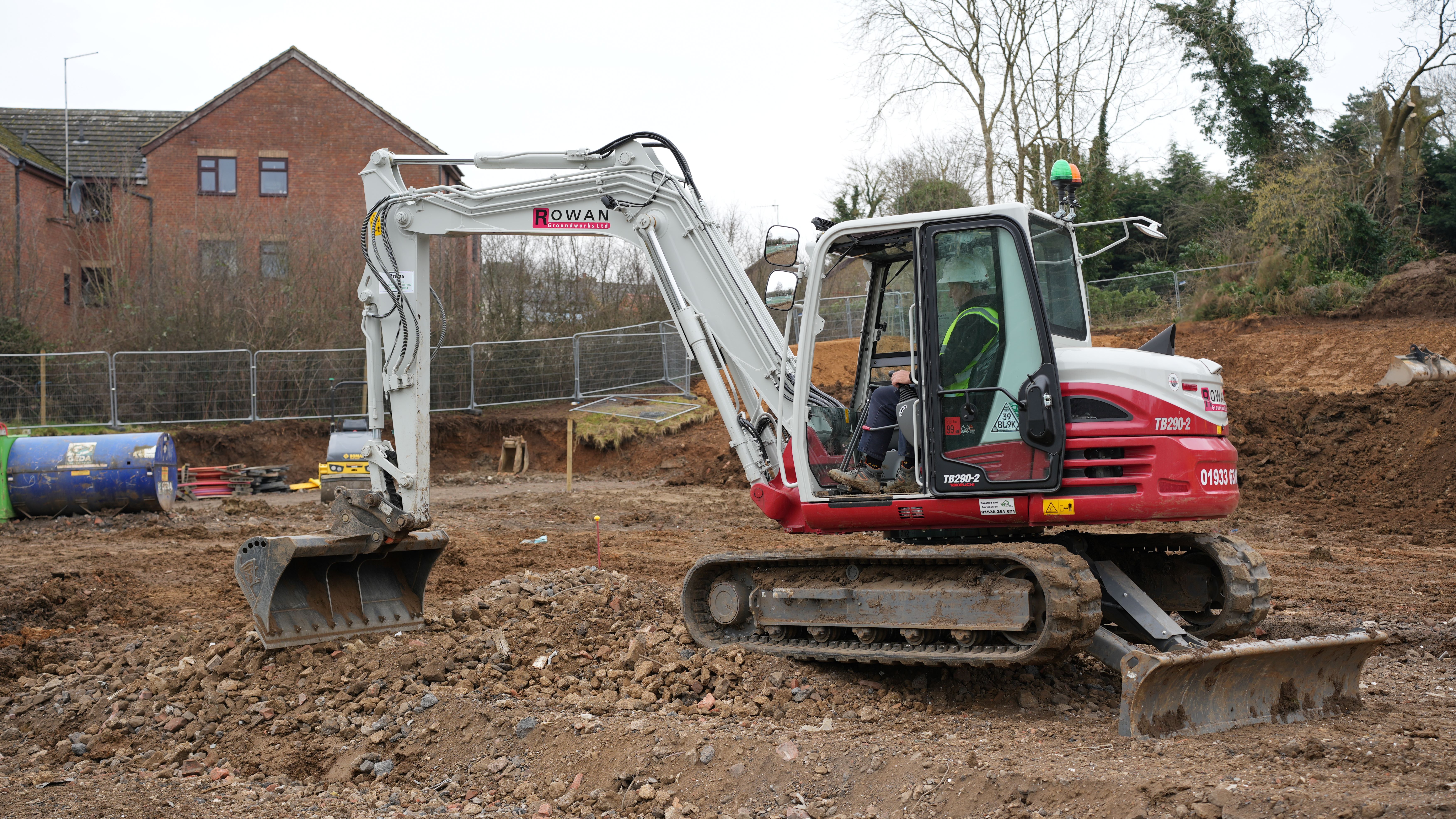
On approaching the toe of the pile, I felt I needed more power than that you get in the machines slumbering Eco mode, so I selected the Power setting and the machine entered a whole different persona, that little bit of extra poke makes the machine perform how I felt it should do. In P mode it powered up the pile reaching the plateau on top easily.
I set myself up to trim up the sides of the pile, to weather it in, as it looked ominously cloudy and full of rain on the horizon. Considering this is just a 9-tonner, its reach down the side of the heap was impressive and nothing was too much bother for the machine.
Being very familiar with the Takeuchi product, I was very quickly at home and working in unison with the machine, they just do everything you expect from a quality hydraulic excavator. Having sealed up the sides, I sat atop the heap to do something that Takeuchi machines have become so well known for, grading, the smoothness of the controls is the stuff of legends, every service works as you would expect it too, cutting through the material effortlessly, in super smooth controlled motions, it really was an absolute pleasure to be onboard.
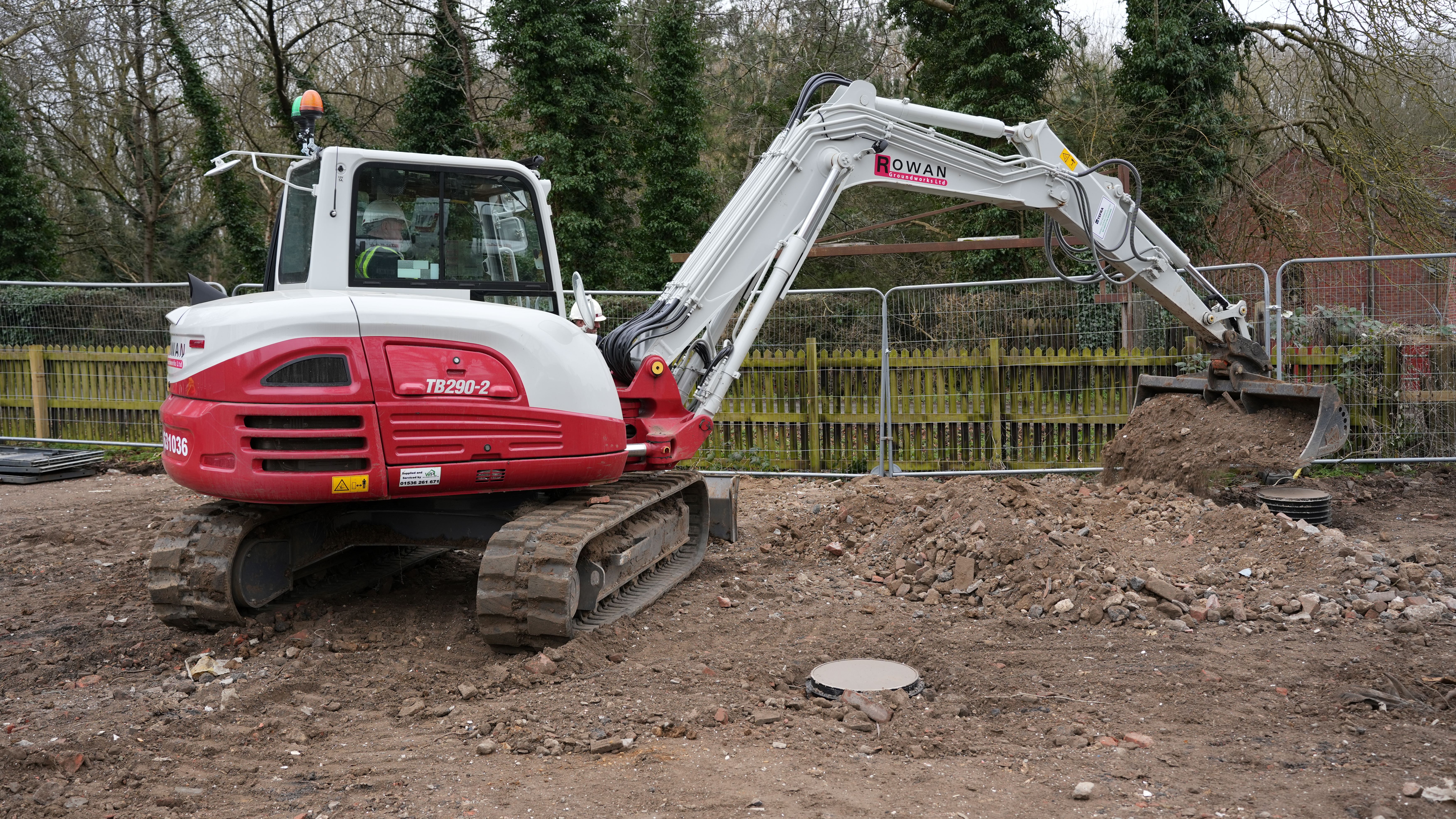
I had heard tales about the machines being a little light on the back end, but throwing material around even with the slightly oversized grading bucket, the machine never once felt unbalanced to me, despite my efforts to prompt a tip at full tilt! Slew speed remains as it was on the original TB285 a respectable 10.3 rpm with a nicely controlled take off and slow down.
This model is as good as it gets in the 9-tonne class sector, I certainly enjoyed my time in the seat!