by Nick Drew | Wed 13 Nov 2019
X-tracting Devon Ball Clay
Taking a look back at another of my Earthmovers articles and bringing it to life on the internet unedited and with alternative photographs.
Based in Wareham, Dorset, family run business Andrews Plant Ltd was established in 1969 by Peter Andrews. Mr Andrews has had a long history of being around JCB machines from a young age operating classic models like the Hydra Digger and the JCB 4 and 4C models
Its no coincidence then that today the Andrews Plant fleet is dominated by the British, Staffordshire built machines ranging from forward tipping dumpers up to 36 tonne hydraulic excavators. The current fleet tally is around 50 machines strong and expanding all the time.
The company have built up a fantastic working relationship with their local dealer Holt JCB over the years and so when it was time to think about trading in some of its JS220LC models, it was a pretty obvious that they would look at the new X Series machines.
Peter Andrews had already been taken up to the factory by Holt’s to look at the new production facilities and to try out the new excavators at JCB’s nearby quarry, he was very impressed with what he saw and was quick to put in an initial order for 6 of the new machines.
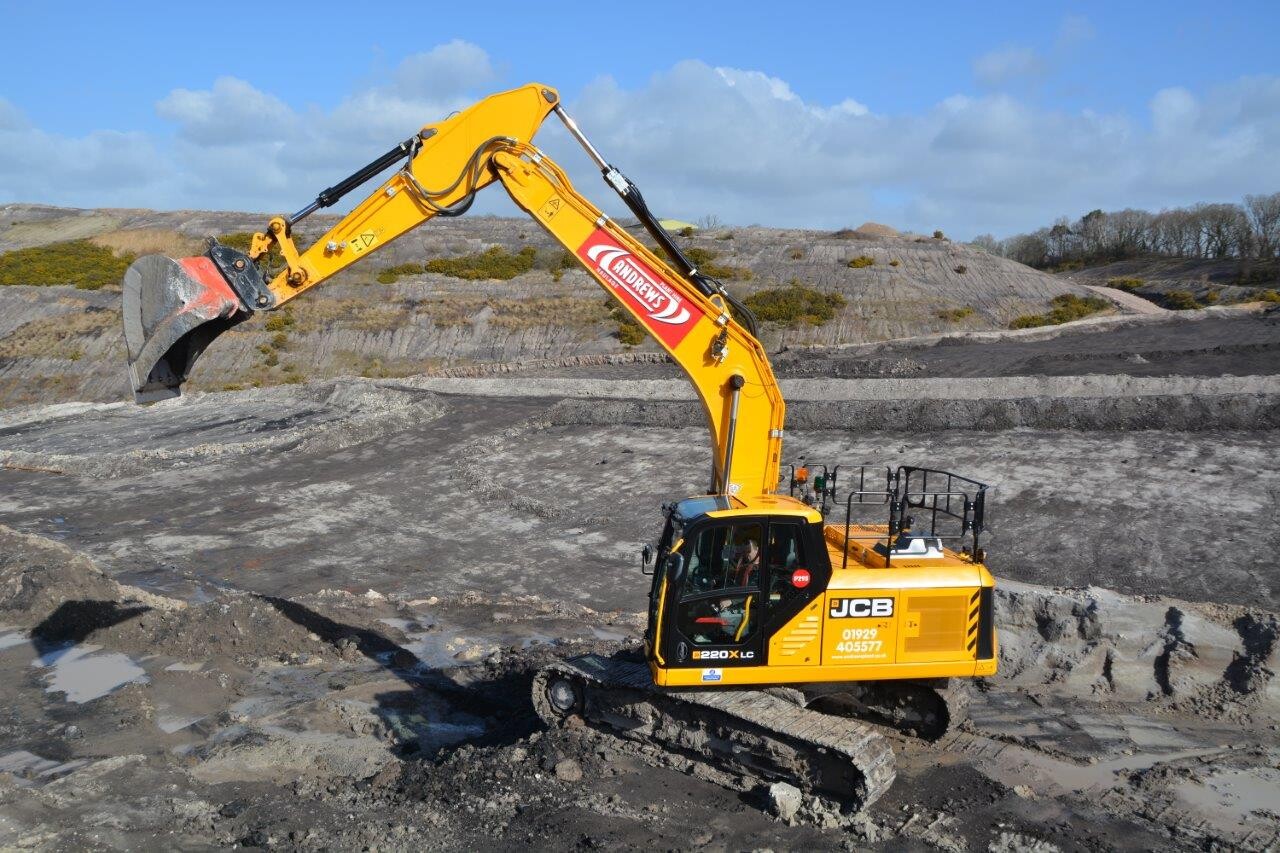
Dad liked what he saw with these new machines said Peter Andrews son, Operations Manager Chris Andrews, “The features which really appealed to us were the overall all new design of the 220XLC, the improved hydraulics which have proven to be incredibly smooth, good power in the dig and the much improved cab interior which is easily up there with the best of them, it was clear to us that a lot of thought and customer feedback had gone into the design of these new models which can only be a good thing”.
The new machines were delivered last December and 4 of them were immediately assigned to work in the ball clay pits formerly run by English China Clays (ECC) but in more recent years operated by the French owned company Imerys in Dorset and Devon, where Andrews Plant have had ongoing contracts to extract this precious material, something they have been involved in since as far back as 1979 when the original firm undertaking the bulk earthworks threw in the towel. The other two 220X LC machines have gone into the general plant hire fleet.

Chris reports that the machines have all been performing very well and apart from some early software teething problems which were quickly addressed by Holt JCB they have been extremely reliable since.
Chris Andrews estimates that the JCB’s engaged on these operations dig approximately 390,000 tons of clay per year across the 3 pits down in South Devon, this total includes both good and bad clay, obviously they have to dig out a lot of bad clay to get to the best quality material which after extraction is primarily used to produce sanitaryware.
Earthmovers caught up with two of the machines working in two separate pits in the Newton Abbot area of Devon, an area which has a long history of ball clay extraction. To make things easier and more viable Andrews Plant employ locally sourced operators for its Devon operation, these include highly experienced plant man Richard Stockley who was operating the first machine we visited.
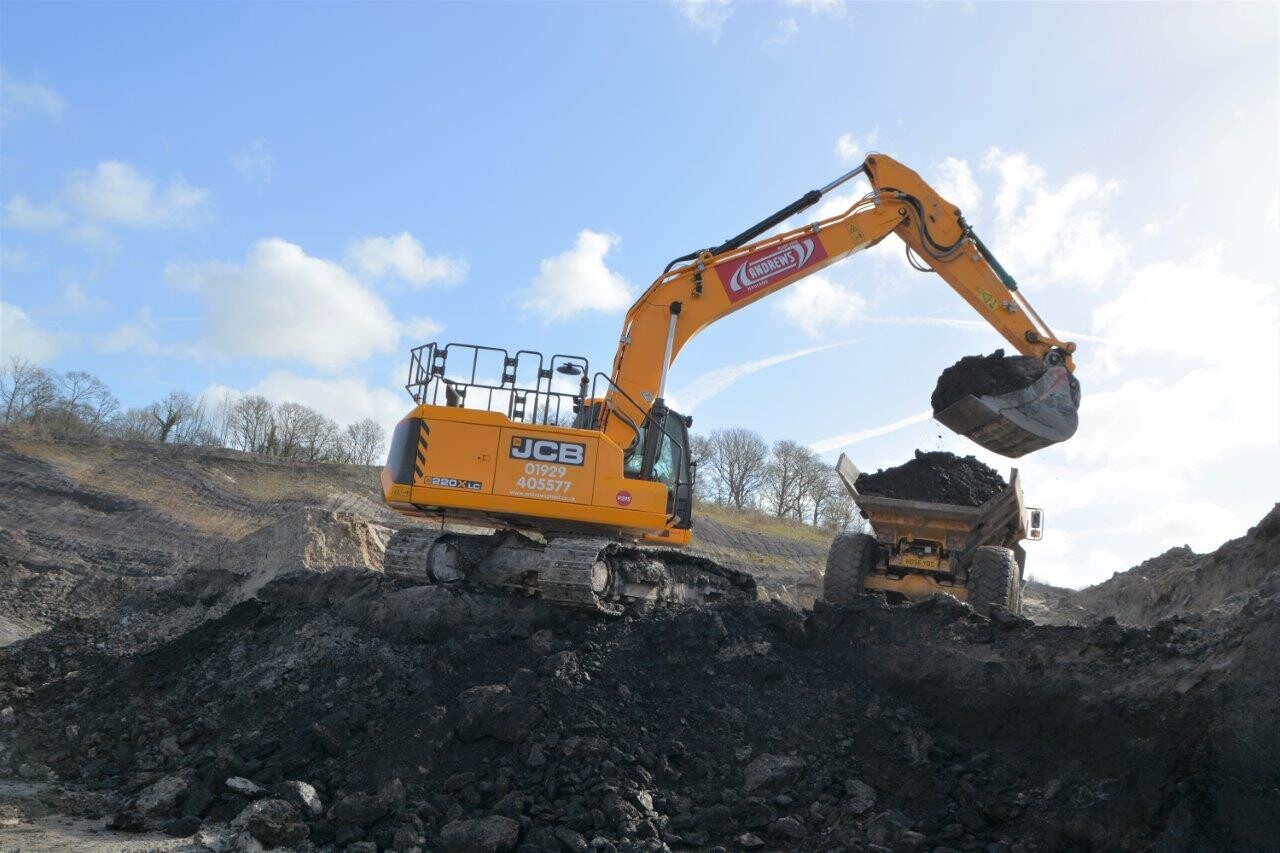
Richard has worked for Andrews Plant for some considerable time and is well known for looking after the kit he operates, he had high praise for the new X Series machines describing them as being well built, with plenty of power, smooth in operation and with a fantastic cab layout.
Richard was busy loading out the clay onto a couple of Bell dumptruck’s from the Andrews Plant fleet that, in turn, take the clay up to a large storage shed facility at the top of the pit. The clay is then re-loaded onto road going trucks and taken to the main works in Heathfield, Newton Abbot, where the raw material is processed. The refined material is then loaded onto trucks again and taken to local ports where it is loaded onto ships, while some is loaded into containers. If required some of the clay is taken by lorry to facilities in Dorset to be mixed with other materials for different markets.
Watching the 220X LC from afar it appeared to be going about its business effortlessly, the well proven 4-cylinder JCB Ecomax engine which has been tweaked for the X Series application just purrs away quite quietly while making the most of its 129kw (173hp) power output.
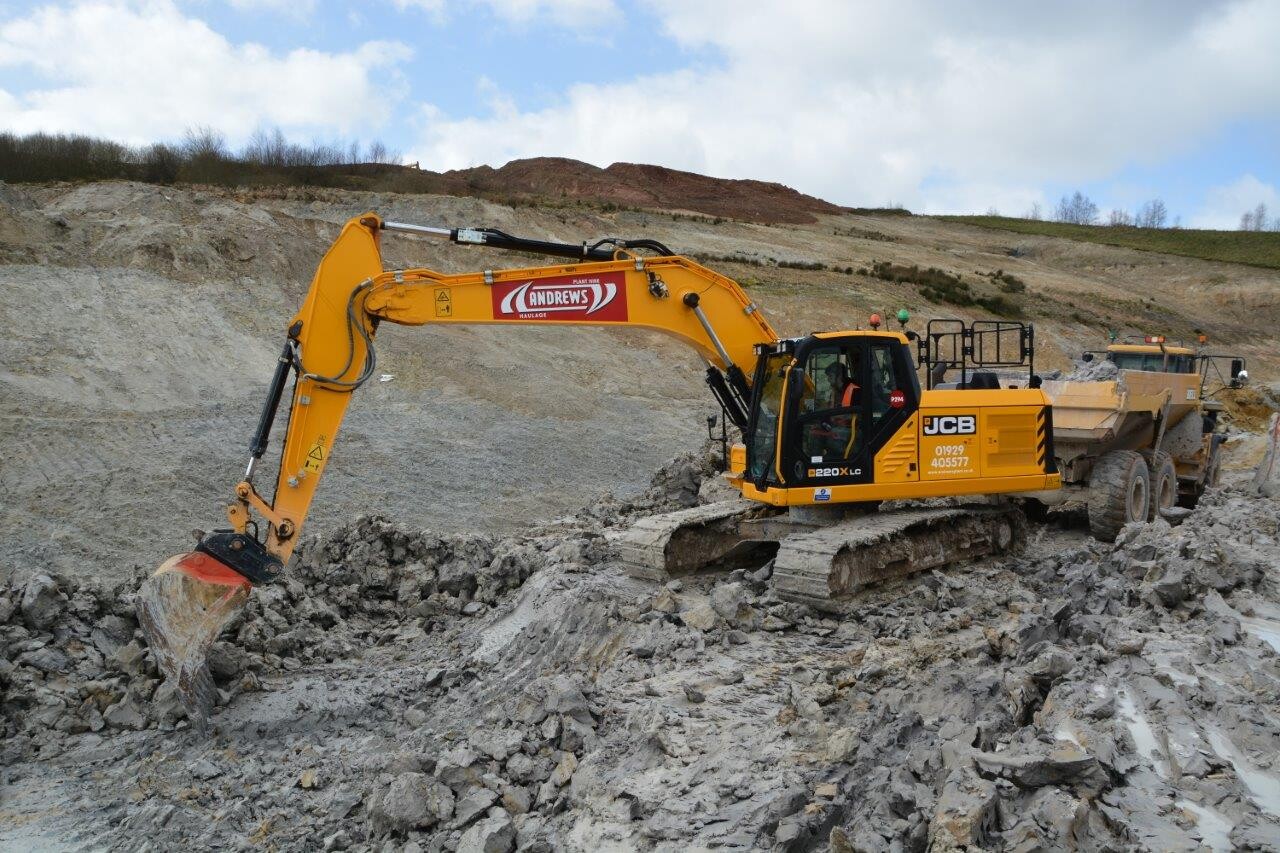
The British designed and manufactured engine drives the latest Japanese Kawasaki hydraulic pump which feeds the hydraulic circuit with a vastly improved oil flow, thanks to larger 25mm pipework, another blue-chip Japanese component in the form of the Kayaba valve block combines with the pump to offer the operator the very best in power, precision and smoothness of operation even when using multiple circuits.
At another location not far away, we caught up with the second 220X LC machine at work in the ball clay pits. This machine is operated by local man Tim Finch, Tim was also extremely positive about his latest mount describing it as being a good machine and suggesting that they will surprise a lot of people with the quality of them. Tim also spoke of one or two people he knows in the industry who were once hardened JCB “bashers” who have had to eat humble pie and agree that the new X Series is a cracking piece of kit.
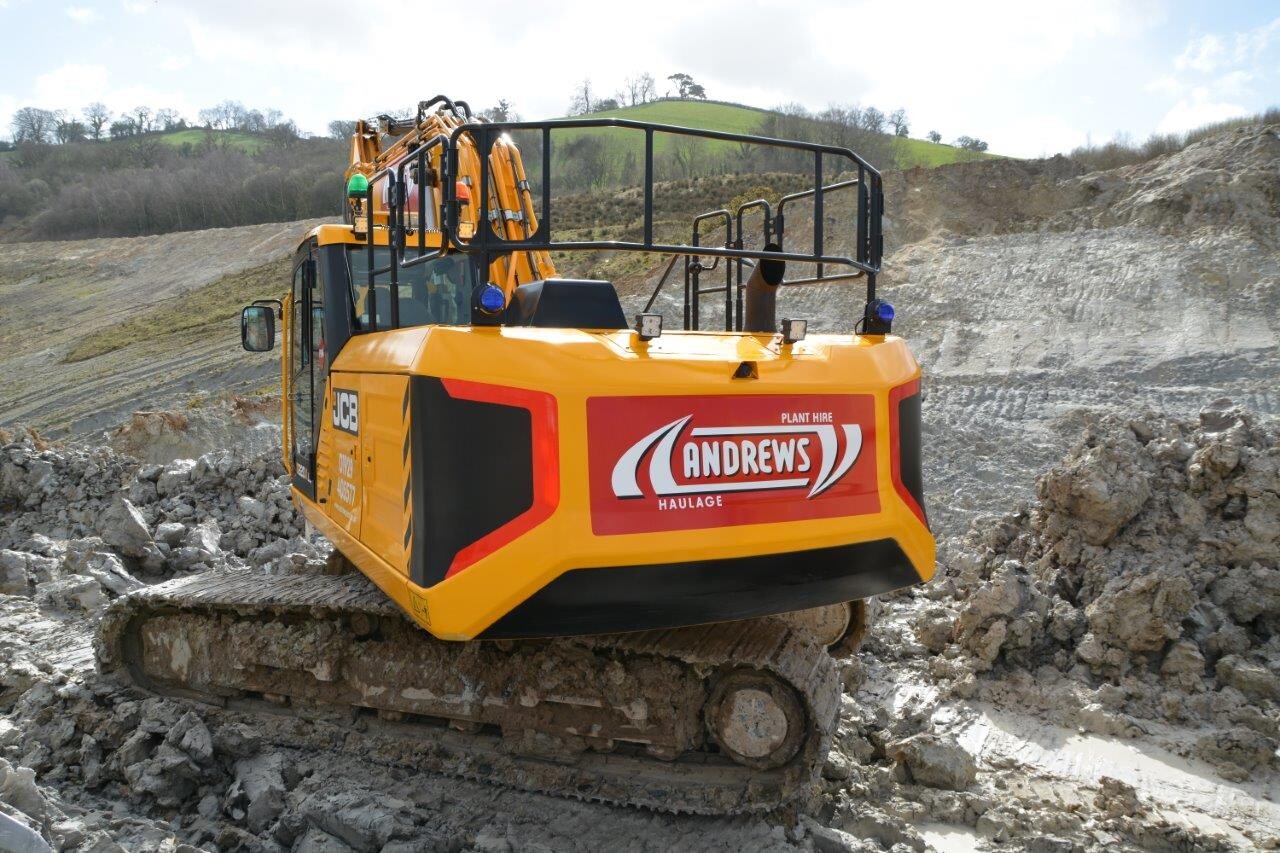
Tim was also keen to talk about the quality of the cab saying, “It’s a great cab, everything is right where you want it and well thought out, it’s a very pleasant place to spend long days in
Tim too was loading out the clay onto another pair of Bell trucks while also sorting out the bad clay from the good. Having good knowledge of the materials in these pits is a very important aspect of the job and maintaining the cleanliness of the good clay is of paramount importance.
All 6 of the new machines were supplied by Holt JCB fitted with a full LED work lighting package, all around fall from height (boxing ring) protection, green seat belt light, blue quarry spec lights on the counterweight and JCB fully automatic hydraulic quick coupler’s, the two we saw were fitted with JCB grading buckets and Miller bulk digging buckets, one with a bladed cutting edge and one with teeth.
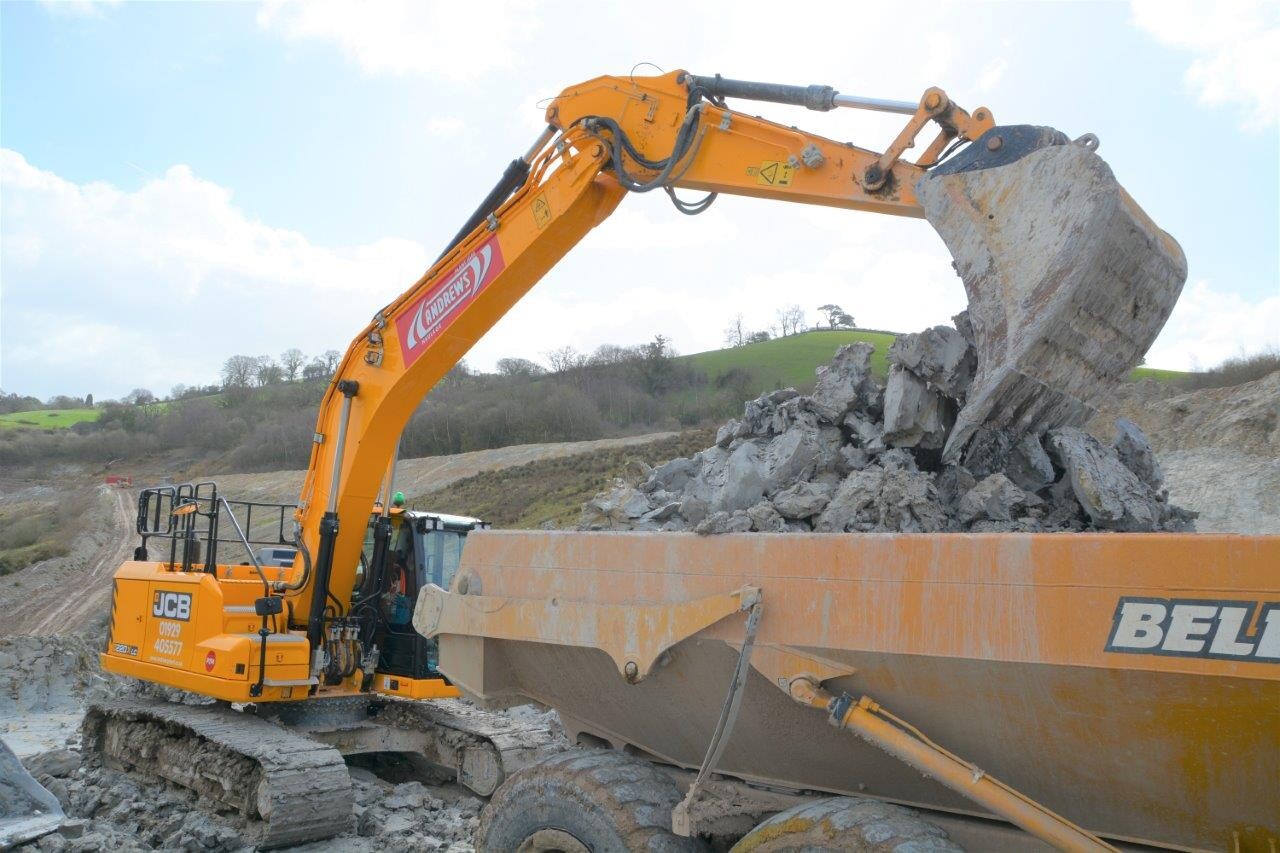
Summarizing Chris Andrews said, “So far operator and customer feedback on the new X Series machines has been very positive, not only from our own guys but from customers who have had them on a contract hire basis, its pretty clear to us that the 4 years of planning, research and development and the significant financial investment in the new product is paying dividends, I am confident that as the new size models roll out we ourselves will be investing in more of these going forward, we like to buy British historically and that’s another reason we buy JCB”.
Devon Ball Clay Mining a Pocket History
Clay extraction has been taking place in South Devon since the 1600’s when teams of men would excavate shallow trenches using various hand tools specifically designed for the job.
This was expanded to small open pits as the industry evolved. These pits grew in size as ground water pumping techniques improved in the 19th century. This was followed by so called square pits, which were a further development of small open pits, this enabled the digging of clay to be undertaken at greater depths than ever before.
In the second half of the 19th century underground or shaft mining became more popular, this technique was later developed into inclined shaft mining, which remained the preferred option until the 1960’s.
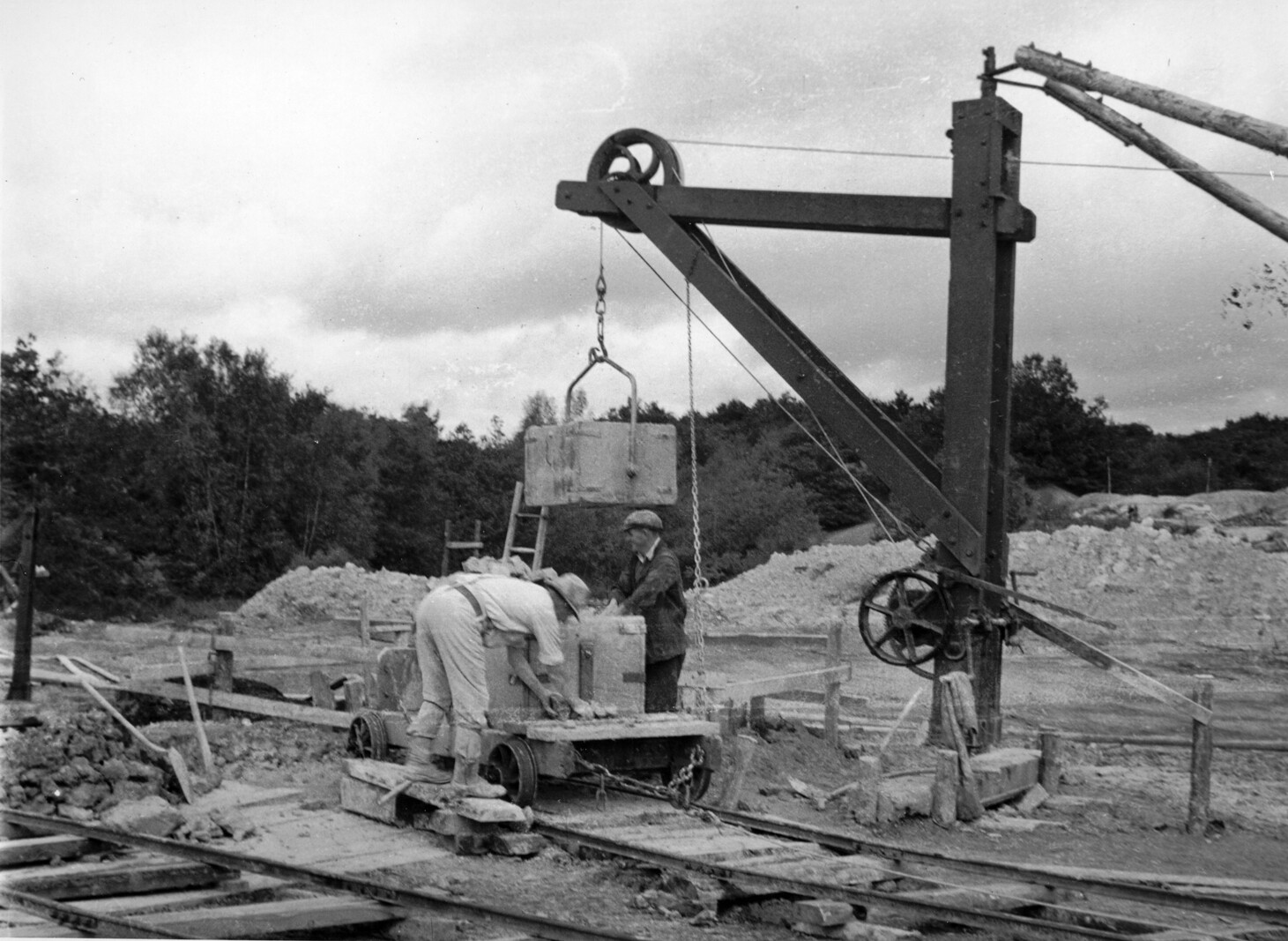
Photo: Courtesy of the Ball Clay Heritage Society.
Underground mining can be costly and dangerous and with time large scale opencast mining predominantly replaced the underground activity during the second half of the 20th century.
In the 1940’s and early 50’s diesel powered rope shovels, from the likes of Ruston Bucyrus, Priestman and Smith’s loading dumptrucks took away a lot of the hard graft that teams of men with shovels and picks had previously had to endure although some lighter pneumatic “spaders” (clay spades) hand tools were still used as an when required.
In the early 1960’s bucket wheel excavators were tried out but with powerful and more accurate hydraulic excavators being developed the bucket wheel variants were phased out in favour of the hydraulic variety which could be used with more accuracy by a skilled operator to find the rich seams of clay thus minimising waste.
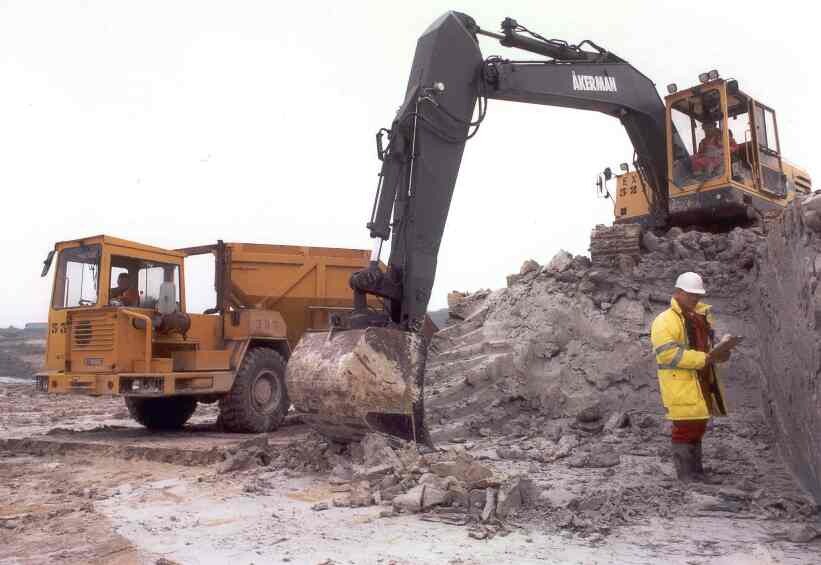
Photo: Courtesy of the Ball clay Heritage Society.
Underground mining was completely replaced by major opencast excavation in North Devon by the mid 1970’s and was steadily reduced in the South Devon facilities during the 80’s and 90’s. Today all of the production is achieved in larger and deeper open cast pits using modern hydraulic excavators in conjunction with dumptrucks.